Dynamic Mechanical Analysis – Materials to Final Products
Troy Nickel | Andy Simon
March 14, 2022
From plastic for medical devices to rubber for tires, the materials we use must meet increasingly high demands. Product manufacturers and consumers expect their materials to look good, perform well, and cost less, all while being environmentally friendly. Fulfilling all these expectations requires deep understanding of material behavior from the molecular level to real world mechanical properties. Since there are many factors that affect the properties of materials, precise measurement tools and methods are required to ensure that materials fulfill the high expectations of our world. A key measurement and analysis method to evaluate the properties of materials at various stages of development and production is Dynamic Mechanical Analysis (DMA).
DMA, at its very basic, is the measurement of the viscoelastic properties of a material, which are usually quantified in the form of storage modulus, loss modulus and tan delta.1 DMA measurements are obtained by applying forces and deformations on a material and analyzing them alongside the effect of other factors such as temperature, time, and frequency.
DMA Instruments and Data
TA Instruments is the world leader in Dynamic Mechanical Analyzers with our flagship DMA 850 and RSA-G2 instruments. These instruments are capable of a wide range of tests with extremely precise measurements of the most subtle changes in properties.
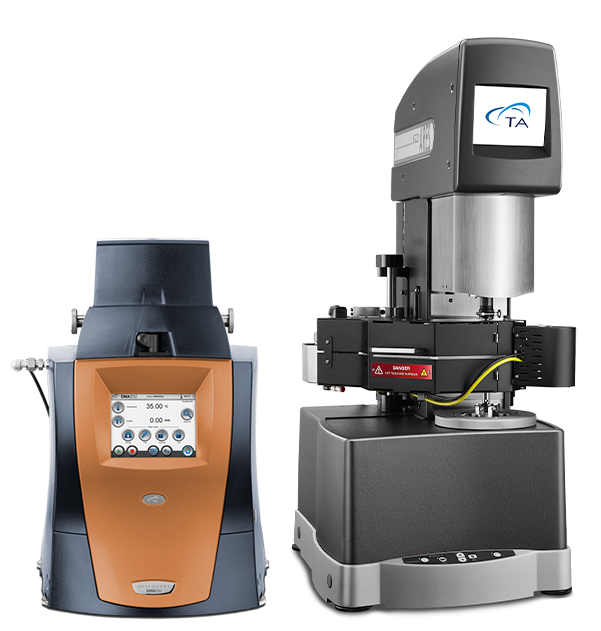
Polyethylene Terephthalate (PET) Testing on DMA 850
This figure shows a comparison among three PET samples in tension on the DMA: one with a uniform adhesive layer that performs well, one with a non-uniform layer that performs poorly, and one that is uncoated. A transition peak due to the adhesive is seen in tan δ around 40 °C in the “good” sample, whereas the “poor” sample shows a much smaller peak. Knowing the characteristics of good and poor samples enables quality control of the coating process and the finished product. Subtle transitions such as these require extremely high sensitivity and precision.

As materials and product development advance, scientists and engineers’ need additional testing capability with larger samples and higher forces. This need can come from a number of different places including:
- Materials which cannot be miniaturized (such as 3D printed or composites)
- High stiffness samples which require more force to deform
- Real world conditions which require deformations outside the Linear Viscoelastic Regime (LVR)
- Complex geometries that represent real world components
Often the data generated by these higher force tests are used directly in the design and verification of the material or product in its end use condition. As the tests and test samples begin to approximate real world conditions, the sample sizes and forces can get relatively high with applied forces of more than 10,000N and dynamic displacements of 10mm or more. High force DMA testing can look very different from traditional DMA testing in that it is often performed to learn specific information. These tests may include only the test variables which are applicable for the end use, even excluding temperature effects! For example, some customers may use high force DMA at room temperature as a quality control check for a vibration isolator or other finished components.
Since these types of DMA tests are commonly performed later in the development cycle, they are typically run in conjunction with other strength and fatigue tests. Material strength, fatigue life, and DMA properties must all be considered together as materials and designs are iterated towards the final product.
Final Product Testing on DMA 3200
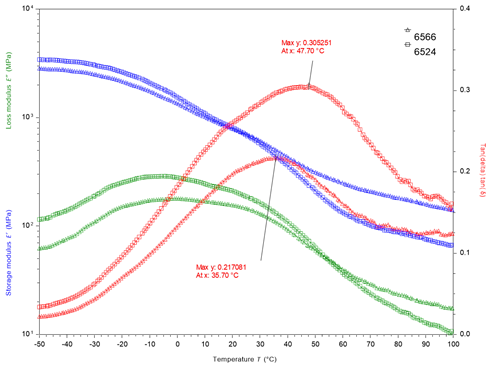

Strain Sweeps on DMA 3200
This table shows an evaluation of Payne Effect on filled rubber. The filler-filler interactions break down at higher strains resulting in lowering modulus. Understanding this effect is critical when materials are used outside the LVR.
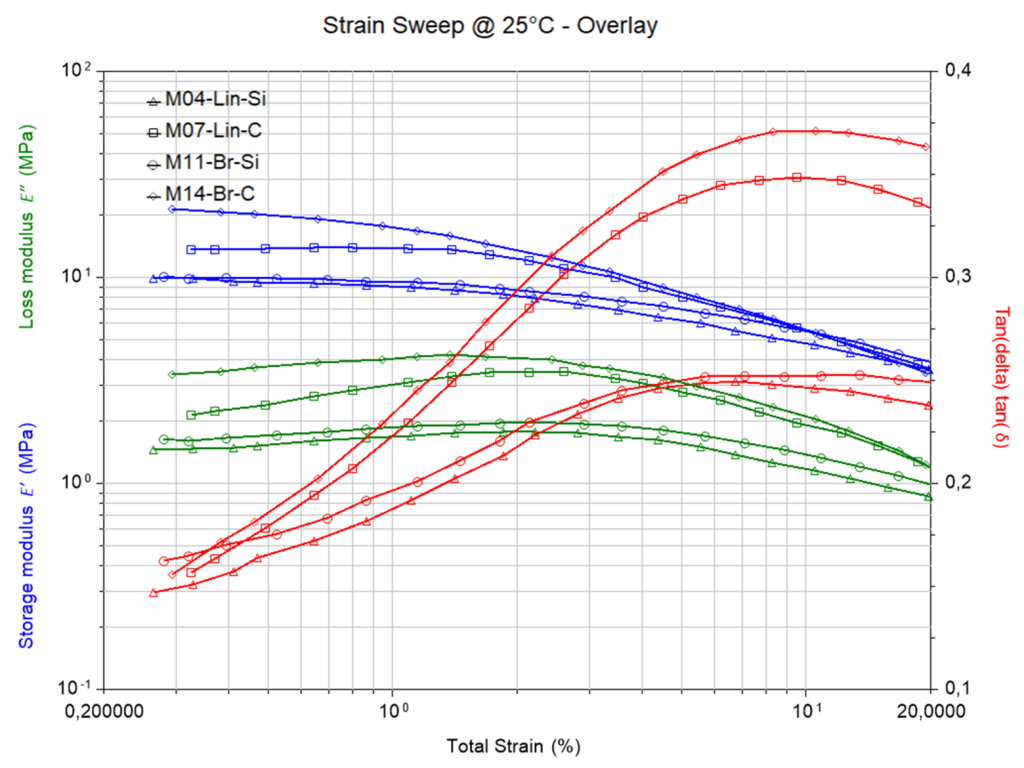
TA Instruments family of Mechanical Testing products provide a wide range of high performing material strength, fatigue, and DMA capability within one instrument. The DMA 3200 is a specially configured 3200 instrument for the highest DMA performance but maintains all of its material strength and fatigue testing capability. The entire load frame line, from the ElectroForce 3200 (capacity: up to 500 N) to the Electroforce 3550 (capacity: up to 15kN), can be configured for DMA testing while maintaining the premier materials strength and fatigue capability that ElectroForce is known for. This provides users with a versatile tool to design, test, and refine their products in an accurate and time-effective way. The specialized software for DMA and fatigue testing provide the user with world class capability for a wide variety of test types to offer versatility without compromise.
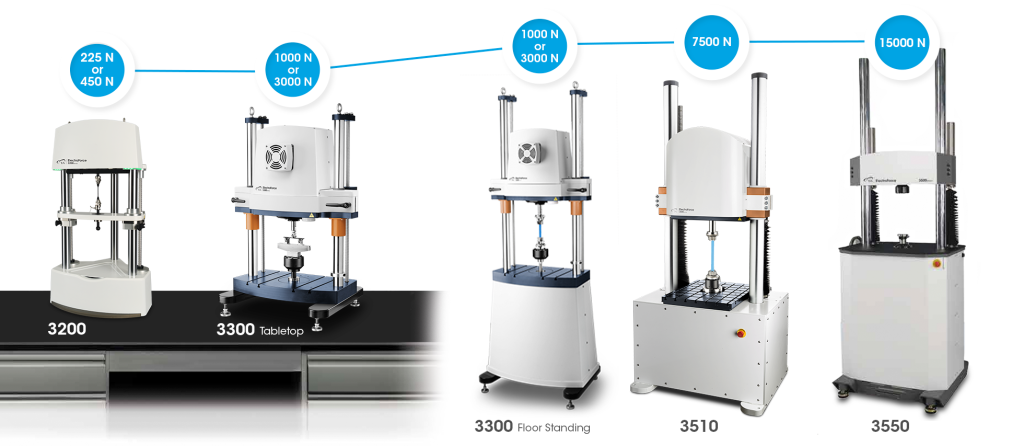
TA offers instruments for the widest range instruments capable of DMA, strength, and fatigue testing on the market. This broad range of products allows customers to fulfill their testing needs from material development to final product testing and verification with a common partner and commonly with a single instrument.
References:
- Groenewoud, W. M. (Ed.). (2001). Characterisation of Polymers by Thermal Analysis. Elsevier Science B.V. https://doi.org/10.1016/B978-044450604-7/50005-4