Material Analysis for Bioplastics Quality Assurance and Degradation
Bharath Rajaram | Michael Onepe | Morgan Ulrich
May 23, 2022
What are bioplastics, and how can manufacturers use thermal analysis, rheology, and mechanical analysis to successfully incorporate bioplastics into products?
What are bioplastics? How can plastic manufacturers use them to improve the environmental impact of their products? With so many emerging green technologies, producers and consumers need to differentiate between greenwashing1 and genuine advancements. Furthermore, if a new development is deemed environmentally beneficial, all stages of the plastics supply chain, especially converters, must then learn how to incorporate the new technology without undermining their process or products.
The terms “bioplastics” or “bio-polymers” can actually refer to two kinds of materials: Bio-based plastics are produced from renewable raw materials, such as sugarcane or corn. Biodegradable plastics can be completely broken down through microbial or enzymatic decomposition processes resulting in environmentally benign natural byproducts, such as gases (CO2, N2), water, biomass, and inorganic salts. Biodegradation can also be applied to certain types of fossil-fuel based plastics such as Polybutylene adipate terephthalate (PBAT) and Polycaprolactone (PCL). It is important to note that not all bio-based plastics are biodegradable, and vice versa.
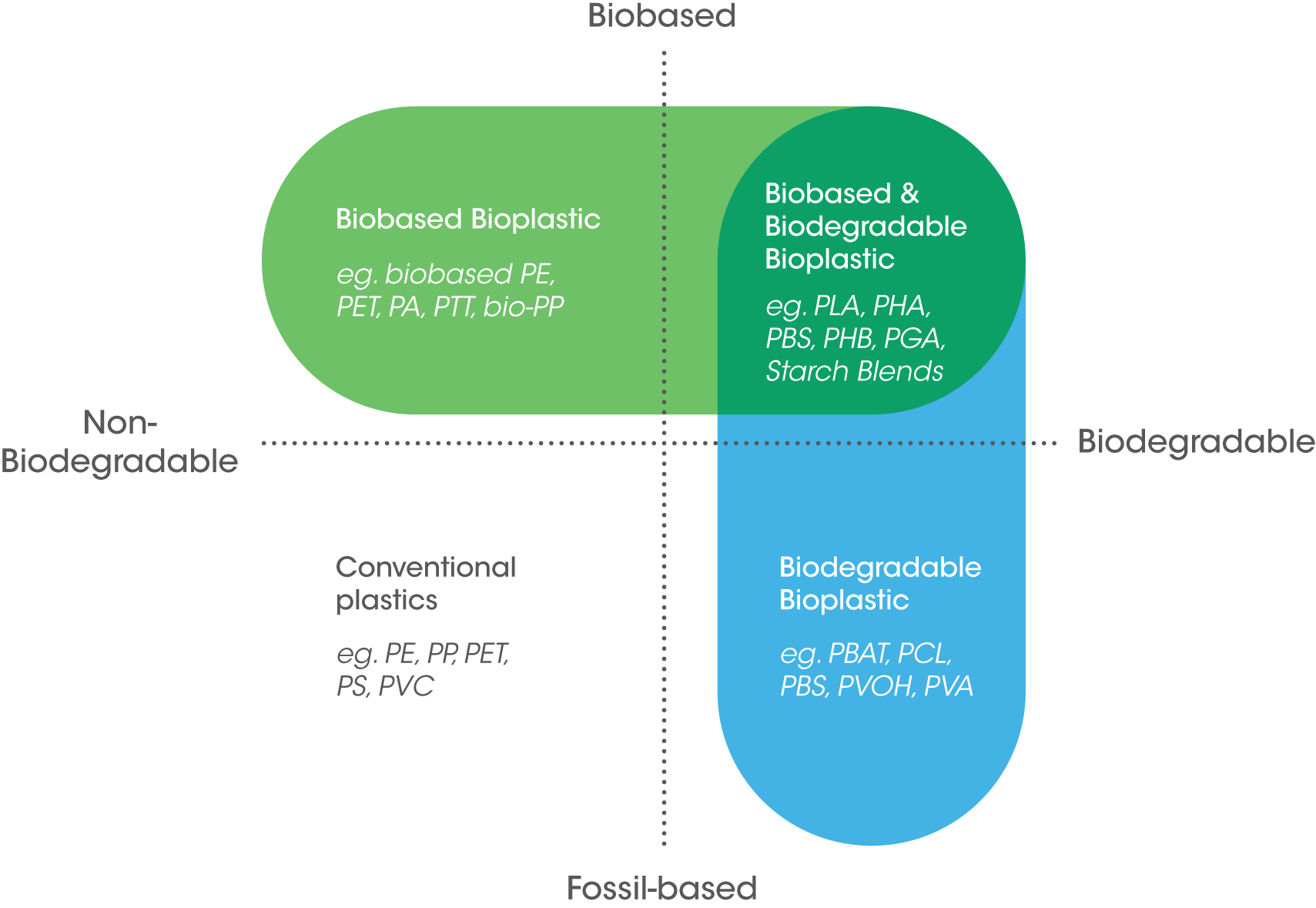
Plastic sustainability must be addressed at each stage of the material life cycle, from creation to degradation. Both bio-based and biodegradable plastics are potentially more sustainable than conventional plastics, but they need the right materials and conditions to achieve the most sustainable solution. Maximum sustainability is achieved with bioplastics that are both bio-based and biodegradable, offering a truly sustainable path from production to end-of-life waste management. Classes of plastics that meet this criteria include PLA, PHA, PHB, and starch blends.
Manufacturing with Bio-Based Plastics
Bio-based plastics are appealing since they can have identical chemical structures and properties to conventional plastics.2 As a result, they are commonly used for products requiring high durability and strength. Replacing fossil-fuel plastic materials with bio-based plastics reduces our consumption of nonrenewable resources and is more sustainable long-term. However, bio-based plastics could potentially pose the same set of sustainable disposal challenges that are encountered with conventional fossil-fuel plastics. Another challenge is life cycle sustainability analysis and minimizing the water and fuel usage during farming for bio-based ingredients.
Researchers working on novel bio-plastics must balance these sustainability demands while maintaining efficient production and high-quality products. When new bio-based plastic formulations are developed, manufacturers need to perform rigorous tests to ensure their end product meets customer’s performance and processability expectations at a cost comparable to fossil-fuel sourced plastics. To this end, parameters like material strength, durability, viscosity, thermal stability, phase transitions, and other qualities must be quantified.
Manufacturing Biodegradable Plastics
Biodegradable plastics offer the potential to result in less plastic waste after use, but the term itself applies to a broad spectrum of biodegradability. Most of today’s biodegradable plastics need to be composted under specific temperature and humidity conditions, presenting an opportunity for new polymers that widen the potential for degradation anywhere and sooner after use.3
Biodegradable plastics can come from bio-based or fossil derived materials (or a blend of both), which require the pre-product testing described above but with the added challenge of designing for decomposition. Plastic manufacturers need to ensure processability, product performance, and finally effective biodegradability when designing new blends.
Plastic processors are tasked with designing products that withstand regular use yet degrade easily after disposal. Material testing helps them balance the necessary properties and find formulations that meet all requirements throughout the polymer life cycle. Thermal analysis helps developers optimize plastics for decomposition in compost facilities or landfills. These measurements can inform consumer instructions to ensure the proper disposal of products for decomposition. Mechanical analysis can also measure plastics’ strength and durability for processing, use, and decomposition.
Material Analysis of Bioplastics
In any plastic feedstock, material analysis is crucial for optimizing processing conditions and end-use performance. New bioplastic formulations require even more rigorous testing to ensure that they meet user standards while maximizing sustainability. The following material analysis techniques are already common in plastic development but are even more crucial for successful bioplastic innovation.
Thermal analysis measures how changes in temperature affect a material’s properties. Thermal analysis instruments typically measure heat flow, weight loss, dimension change, or mechanical properties as a function of temperature. Characterizing thermal properties is crucial for bioplastic material selection and optimization, answering questions such as:
- How will this material behave when heated up for processing, including molding or extrusion?
- Will the plastic maintain its stability if it’s heated or cooled during transport or use?
- How will the material decompose? Can we optimize the materials for biodegradable plastics?
The most common thermal analysis instrument for bioplastics is a Differential Scanning Calorimeter (DSC) which measures thermal stability and phase transitions to analyze a plastic’s behavior under different conditions. Bioplastic developers use Thermogravimetric Analysis (TGA) for exact composition determination, including volatile or solvent content and filler content (residue). TGA also measures decomposition temperature as well as resulting products, which are crucial for designing sustainable biodegradable plastics.
Mechanical Analysis includes a variety of techniques to characterize a material’s mechanical properties or determine a structure’s response to force. Bioplastic manufacturers use Dynamic Mechanical Analysis (DMA) to measure storage modulus, loss modulus, tan delta, and glass transition (Tg); these measurements help predict a plastic material’s response to forces and deformations at set temperatures. Material strength (measured with Young’s modulus, yield strength, ultimate strength, elongation at break, fatigue and durability) is crucial for predicting the final product’s behavior and can be efficiently measured on mechanical test load frames.
Rheology is the study of the flow and deformation of materials. Rheometers measure bioplastics’ viscosity, which is crucial which is crucial for optimizing processability especially through extrusion and blow molding. Rheology also supports analysis of plastic’s uniformity and durability while developing a new blend.
These material measurements facilitate every step of bioplastic manufacturing, from evaluating the quality of a given feedstock to testing the properties of a final product. As new bioplastic formulations are developed, manufacturers will need systematic approaches to incorporate new blends while maintaining efficiency, meeting customer expectations, and maximizing sustainability.
The Best Material Measurements for Bioplastics
Bio-based and biodegradable plastics pose new challenges, yet manufacturers are already rising to the occasion with cutting-edge material analysis. Accurate measurements of composition and material behavior at every stage of manufacture facilitate the design and production of new green plastic products. Leading bioplastic developers around the world are turning to TA Instruments, the world leader in thermal analysis, rheology, microcalorimetry, and mechanical test instruments. TA Instruments set the industry-accepted standard for measuring material properties and are therefore the brand of choice for top polymer labs.
While adopting a new material test regimen can seem daunting, TA Instruments are designed with the user in mind. Many of our instruments are equipped with TRIOS one-touch functionality to run pre-programmed tests with just the click of a button. We also offer industry-leading customer support to help our users from instrument selection and installation through to successful testing.
Whether you are looking to expand your existing testing capabilities or pivot to meet new sustainability challenges, TA Instruments offers the instrumentation and guidance you need. Contact our experts today for personalized support and answers to any questions. And visit our polymers page to learn more about our unique offerings for the plastics industry.
References:
- The troubling evolution of corporate greenwashing. (2016). Bruce Watson. The Guardian. Accessed May 2022. https://www.theguardian.com/sustainable-business/2016/aug/20/greenwashing-environmentalism-lies-companies
- Bio-based? Recyclable? Biodegradable? Your guide to sustainable plastics. (2020). Sandrine Ceurstemont. Neste. Accessed May 2022. https://journeytozerostories.neste.com/plastics/bio-based-recyclable-biodegradable-your-guide-sustainable-plastics#6ce5bead
- Are bioplastics better for the environment than conventional plastics? (2019). Anja Krieger. Ensia. Accessed May 2022. https://ensia.com/features/bioplastics-bio-based-biodegradable-environment/
Other Resources
- Quantifying Polymer Crosslinking Density Using Rheology and DMA
- Characterization of Shape-Memory Polymers by DMA
- Determination of the Linear Viscoelastic Region of A Polymer Using a Strain Sweep on the DMA 2980
- Characterization of an Acrylic/Melamine Copolymer Blend by DSC and DMA
- Characterization of a Polymer Resin/Catalyst System by TGA, DSC, DMA
- Dynamic Mechanical Analyzers
- DMA 850