The DMA 3200 combines decades of cutting-edge fatigue and world-leading Dynamic Mechanical Analysis technologies into a unique and highly versatile testing platform. The patented, frictionless Electroforce® motor technology, superior mechanical design, efficient environmental control, and wide variety of clamping systems deliver superior data accuracy for the broadest range of applications.
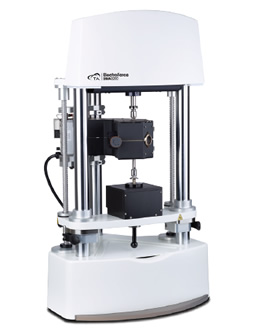
Product Features
The DMA 3200 features patented ElectroForce linear motor technology enabling a single instrument to deliver unequalled performance and data accuracy. This unique motor technology combines powerful rare-earth magnets with a frictionless flexural suspension for the most precise force and displacement control over a wide range of frequencies and amplitudes. The DMA 3200 motor delivers a force output of up to 500 N and controlled displacements ranging from 1 micron to 13 mm. Testing can be conducted in both static and dynamic modes.
In addition, the frictionless, moving-magnet design eliminates failure points that exist in other motor designs, such as moving wires and bearing degradation. This ensures the most durable and reliable performance; proven over billions of cycles through decades of maintenance-free use in ElectroForce fatigue test instruments. It is the only motor in the industry backed by a ten-year warranty.
This efficient, quiet, and lubrication-free motor technology allows the DMA 3200 to be used virtually anywhere; from lab to production floor, or from the cleanroom to office space.
Key Features
- Patented, linear motor and high-resolution displacement sensor provides unmatched control over the widest ranges of force, displacement, and frequency, for superior data accuracy
- Ultra-durable, frictionless motor, backed by industry’s only ten-year warranty, provides maintenance- and worry-free operation
- High force of 500 N enables testing of larger samples or final parts under real-world conditions, by achieving higher loading levels in both DMA and fatigue analysis
- Forced Convection Oven (FCO) provides superior control and responsiveness over a temperature range of -150°C to 600°C for the highest degree of accuracy and flexibility in experiment thermal profiles
- Large Sample Oven (LSO), with a temperature range of -150°C to 315°C, offers spacious interior dimensions to accommodate testing of large samples or components
- Air Chiller Systems (ACS) offer unique gas flow cooling for sub-ambient testing without the use of liquid nitrogen, eliminating potential laboratory hazards while providing an incredible return on investment
- Broad range of fixtures accommodate a wide range of sample sizes and geometries adding to testing versatility
- Extremely rigid test frame and air bearings ensure the most accurate results on samples of very high stiffness
- Multi-color status lights provide clear and visible indication of instrument and test status
- WinTest® and TRIOS Software packages provide powerful and easy-to-use instrument control and data analysis for the ultimate flexibility in experimental design
Instrument Specifications
Instruments Specifications | DMA | Fatigue & Quasi-Static |
Maximum Force | 500 N | 450 N |
Minimum Force 500 N Sensor Optional 22 N Sensor |
0.2 N 0.025 N |
5.0 N 0.22 N |
Force Resolution 500 N Sensor Optional 22 N Sensor |
0.006 N 0.00026 N |
0.015N 0.00067 N |
Dynamic Displacement Range | ±0.0005 to ± 6.5 mm | ±0.002 to ± 6.5 mm |
Displacement Resolution | 1 Nanometer | 1 Nanometer |
Maximum Acceleration | 80 G | 80 G |
Maximum Displacement at 50 Hz | ± 6.5 mm | ± 6.5 mm |
Maximum Displacement at 100 Hz | ± 1.0 mm | ± 1.0 mm |
Modulus Range | 103 to 3×1012 Pa | NA |
Modulus Precision | ± 1% | NA |
Tan δ Sensitivity | 0.0001 | NA |
Tan δ Resolution | 0.000015 | NA |
Frequency Range | 0.01 to 100 Hz | 0.00001 to 300 Hz |
Oven Specifications
Oven Specifications | FCO | LSO |
Maximum Temperature | 600°C * | 315°C |
Heating Rate | 0.1 to 60°C/min | 0.5 to 10°C/min |
Cooling Rate | 0.1 to 60°C/min | 0.5 to 10°C/min |
Isothermal Stability | ± 0.1°C | ± 2°C |
Interior Dimensions | 70 mm High x 60 mm Dia | 191 x 200 x 200 mm |
* Note: Standard sample clamps are for use to a maximum temperature of 500°C. Optional sample clamps are required for testing to 600°C.
Technology
ElectroForce® Linear Motor
ElectroForce® Linear Motor
The DMA 3200 features patented ElectroForce linear motor technology enabling a single instrument to deliver unequalled performance and data accuracy. This unique motor
technology combines powerful rare-earth magnets with a frictionless flexural suspension for the most precise force and displacement control over a wide range of frequencies and
amplitudes. The DMA 3200 motor delivers a force output of up to 500 N and controlled displacements ranging from 1 micron to 13 mm. Testing can be conducted in both static
and dynamic modes.
In addition, the frictionless, moving-magnet design eliminates failure points that exist in other motor designs, such as moving wires and bearing degradation. This ensures the most durable and reliable performance that has been proven over billions of cycles through decades of maintenance-free use in ElectroForce fatigue test instruments. It is the only motor in the industry backed by a ten-year warranty.
This efficient, quiet, and lubrication-free motor technology allows the DMA 3200 to be used virtually anywhere; from lab to production floor, or from the cleanroom to office space.
High Resolution Optical Displacement Sensor
High Resolution Optical Displacement Sensor
The DMA 3200 features a High Accuracy Displacement Sensor (HADS), for the purest control and measurement of the small and large deformations necessary for DMA and fatigue testing. HADS is an ultra-performance optical device capable of friction-free, low-noise measurements with nanometer resolution at high-speeds. The sensor is placed close to the sample and loading axis to further minimize errors in compliance or thermal expansion.
Interchangeable Force Sensors
Interchangeable Force Sensors
High-stiffness and high-bandwidth force sensors are mounted on the base of the rigid frame and are interchangeable to optimize for different sample stiffnesses. The instrument comes standard with a 500 N sensor and an optional 22 N sensor can be added to improve low-force data for soft-sample tests..
High Mechanical Stiffness Design
High Mechanical Stiffness Design
In mechanical testing, an instrument design with highly stiff components, such as the frame, connecting components and sample clamps, are critical for measurement accuracy. Minimizing instrument component deformations, or compliance, reduces displacement measurements that can otherwise appear to be sample deformation. The ultra-stiff design of the 3200 ensures superior data accuracy. It starts with a rigid, three-column frame design which maximizes axial and off-axis stiffness, which are further enhanced through the use of air bearings above and below the test specimen. Unlike traditional rolling or plain bearings that introduce noise and friction into the measurement, air bearings have the added benefit of preserving the high performance attributes of the friction-free ElectroForce® linear motor.
Forced Convection Oven, FCO
Forced Convection Oven, FCO
The FCO is the premier temperature device for materials testing and is designed to optimize temperature response time, uniformity and stability. This powerful oven can heat at rates up to 60°C/min. Superior temperature stability is achieved through the use of twin element resistive gun heaters, which provide counter-rotating air flow into a uniquely shaped oven chamber which optimizes gas mixing for uniformity and stability over the temperature range of -150°C to 600°C*. The FCO comes standard with a convenient long-life internal LED light and viewing port. An optional liquid nitrogen cooling system is available for temperatures control to -150°C. Alternatively the FCO can be cooled to as low as -100°C using LN2 free Air Chilling Systems.
* Testing above 500˚C requires high temperature sample clamps
Large Sample Oven, LSO
Large Sample Oven, LSO
The LSO offers spacious interior dimensions to accommodate larger sample sizes or components. In this design, air is passed over two resistive elements and into the cavity, optimizing uniformity over large volume for temperature control from -150°C to 315°C. The LSO comes standard with a large 140 mm x 190 mm viewing window and removable door for convenience. The larger volume of the LSO is ideal for configuring the DMA 3200 with customized clamping solutions for unique applications.
Air Chiller Systems, ACS
Air Chiller Systems
Air Chiller Systems (ACS) offer unique gas flow cooling that provides for sub-ambient testing without the use of liquid nitrogen. Available in two models, the ACS-2 and ACS-3, the chillers feature a multi-stage cascading compressor design that is capable of utilizing compressed air (7 bar, 200 l/min) as the cooling medium. The ACS-2 and ACS-3 models permit operation of the FCO at temperatures as low as -55°C and -100°C, respectively. For the LSO, the ACS-2 and ACS-3 models permit operation to -15°C and -50°C, respectively. The chiller systems can help eliminate or reduce liquid nitrogen usage and associated hazards from any laboratory and offer an incredible return on investment.
Clamping Systems
The DMA 3200 features a variety of sample clamping systems that provide multiple modes of deformation to accommodate a wide range of sample stiffness. Standard clamping systems available for use with the FCO include tension, compression, three-point bending, clamped bending, and shear sandwich. Standard FCO clamps, constructed of 17-4 stainless steel, are for use to a maximum temperature of 500°C, with optional clamps available for extended use to 600°C. LSO clamping systems, constructed of titanium, can accommodate larger samples and are available in tension, compression and three-point bending modes. All FCO clamps can be used with the LSO.
Three-Point Bending
Three-Point Bending
In this mode, the sample is deformed around three-point contacts at both ends and its middle. It is considered a “pure” mode of deformation as the sample is freely supported by fulcrums eliminating clamping effects. It is ideal for testing solid bars of stiff materials, such
as composites, ceramics, glassy and semi-crystalline polymers, and metals.
Tension
Tension
In this mode, the sample is clamped at the top and bottom and placed in tension. The tension clamp is for tensile testing of thin films, strips, bars and individual fibers and fiber bundles.
Compression
Compression
In this mode, the sample is placed between upper and lower round plates and deformed under various conditions of compression. Compression can be used for testing of many low to moderate modulus materials including foams, elastomers, gels, and other soft solids.
Dual and Single Cantilever
Dual and Single Cantilever
Cantilever modes are also known as “clamped” or “supported” bending modes because the support and deformation points are mechanically fixed to the sample. In dual cantilever the sample is clamped at both ends and at the center. The same clamp is used for single
cantilever and the sample is clamped between one end and the central clamp. Single cantilever allows for testing of shorter sample lengths. Cantilever is ideal for eneralpurpose
testing of thermoplastics and elastomers and other highly damped materials, as well as measuring transitions of coatings on substrates.
Shear Sandwich
Shear Sandwich
In Shear Sandwich, two equal-size pieces of a material are “sandwiched” between two ends and a central plate. The applied deformation is parallel to the sample thickness and the resultant deformation is simple shear. This mode is sometimes refered to as double-lap shear. Typical samples tested include polymer melts, foams, elastomers, gels, pastes, and other soft solids or high viscosity liquids.
Specifications
Specifications
Clamp Specifications | FCO* Clamp Sample Dimensions | LSO Clamp Sample Dimension |
Tension | Up to 35 mm long, 12.5 mm wide and 1.5 mm thick |
Up to 100 mm long, 12.7 mm wide, and 8 mm thick |
Compression | 8, 15, and 25 mm diameter plates provided; maximum sample thickness is 15 mm | Up to 50mm diameter, and 100 mm thickness (height) |
Three-Point Bend | Spans of 10, 25, and 40 mm. Up to 12.8 mm wide and 5 mm thick |
Adjustable Span of 10 to 100 mm. |
Cantilever Bend | Up to 38 mm long, 12.5 mm wide, and 1.5 mm thick | N/A |
Shear Sandwich | Sample thicknesses of 0.5, 1.0 and 1.5 mm; shearing surface is 15 mm square. |
N/A |
* Note: All FCO fixtures are compatible with the DMA 3200 LSO Environmental System. Adapters are included.
Control and Analysis Software
The DMA 3200 is powered by two of the industry’s most powerful software packages: WinTest® and TRIOS. These two packages provide advanced algorithms, sophisticated data visualization, and powerful analysis tools for fast and flexible execution and presentation of experiments.
WinTest Advanced Control Software
WinTest Advanced Control Software
WinTest is powerful instrument control and data acquisition software for the DMA 3200. It offers an intuitive environment that provides flexibility in fatigue and DMA experimental design. DMA experimental methods include temperature ramps, temperature sweeps, strain sweeps, and frequency sweeps. Fatigue and ramp-to-failure tests are easily programmed with a variety of available waveforms including sine, triangle, square, or ramp. In addition, waveforms can be combined, or real-to-life waveforms can be imported. Unique TuneIQ and Controlled Stop help users harness the acceleration and power of ElectroForce motors by simplifying tuning tasks.
TRIOS for Data Analysis Software
TRIOS for Data Analysis Software
TRIOS for Data Analysis Software
TA Instruments TRIOS software seamlessly transfers DMA data from WinTest, providing experimentalists with the industry’s leading tool for analyzing and presenting DMA data. This intuitive software includes a wide variety of plotting tools, some of which include multi-axis plotting, smart default and user-customizable graph settings, drag-and-drop overlay, and user-defined variables. A complete range of DMA analysis models and functions includes Time-Temperature Superposition, peak analysis, onset point analysis, peak integration, and continuous and discrete relaxation spectrum. The software can be installed offline on any computer for easy sharing of data with colleagues.
Applications
High Force Dynamic Mechanical Analysis, DMA
Dynamic Mechanical Analysis, DMA
DMA is a technique that applies a sinusoidal deformation, stress or strain, to a sample and measures the viscoelastic response. The frequency and magnitude of the deformation can be held constant or varied (swept) during an experiment. The material response to the deformation can be monitored as a function of temperature, frequency, or time. DMA is used to determine variety of mechanical properties, i.e., complex modulus, E*, storage and loss moduli (E’, & E”) and damping (tan δ) of viscoelastic materials, detect molecular motions, and develop structure-property relationships.
High Force Dynamic Mechanical Analysis, DMA
The high-force capability of the DMA 3200 extends experimental loading regimes and enables testing of larger samples or actual components. Examples of high force DMA capabilities are shown in the figures to the right.
The top figure shows a temperature ramp on a bar of Polycarbonate at a heating rate of 3°C/min and strain of 0.4%. The dimensions of the sample are 1.6 mm thick, 12.8 mm wide, and 19 mm long. These results demonstrate the capabilities of the DMA 3200 design in several ways. First, the high-force, high-stiffness design of the DMA 3200 enables such a thick sample to be tested in the glassy region, or below the Tg, of the polymer in tension mode. A more traditional lower force DMA instrument design would be both force and stiffness limited. Such results would have to be obtained in a bending configuration vs. tension. Second, the friction-free design which provides excellent low force sensitivity enables characterizing the glass transition through over three decades of change in modulus.
The bottom figure shows strain sweeps on two cylindrical rubber samples, tested using compression clamps, at a temperature of 30°C and frequency of 10 Hz. The sample dimensions were a diameter of 10 mm and thickness of 20 mm. These two rubber samples have different amounts of filler content, specifically 40 phr and 60 phr, where phr is a batch unit standing for parts per hundred of rubber. It can be seen that higher filler content results in a higher modulus as well as a more strain-dependent modulus. During this test, forces required to apply 20% strain, which is equivalent to 5 mm, are approaching 60 N. These results highlight both the high force and exceptional displacement control of the DMA 3200.
Fatigue and Quasi-static Testing
Fatigue and Quasi-static Testing
Most materials, components, and devices are exposed to repeated loading conditions during their use and this loading causes fatigue of the material. This fatigue can lead to dramatic changes in material behavior, which can impact overall performance, or it can result in complete and catastrophic failure. Mechanical fatigue testing provides insights on how and when materials, components, or devices fail when subjected to oscillating forces, or stresses. These insights into material behavior are used to ensure reliable product performance and prove out lifetime claims.
Monotonic testing, also known as tensile testing, is also useful for evaluating strength and deformation response. In this case, properties are measured during a single load-to-failure test.
Various material, component or device characteristics can be measured with the DMA 3200, supporting many types of dynamic or static strength studies.
Enabling Fatigue and Quasi-static Testing
The flexibility, power, and durability of the DMA 3200 enables a variety of tests in addition to DMA. Its wide range of speed and force make it useful for both fatigue and quasi-static testing. Examples of these capabilities are shown in the figures to the right.
The top figure shows a single pull-to-failure test, aka tensile test, on a small bar of solder. The displacement ramp was controlled at 1 micron per minute and temperature was constant at 25°C. The dimensions of the sample are 0.5 mm diameter and 2 mm long. This test requires slow and precise control of displacement over a very long time, in this case 14 hours. The sample demonstrates the classic linear region in the beginning of the test in the left of the plot and a very long ductile failure over the middle and right of the plot. This test demonstrates flexibility of the ElectroForce linear motor. Even though it has very high dynamic capabilities it can also be used for precise and slow testing as well.
The bottom figure shows the results of a fatigue study on thermoplastic elastomers. This curve is often called an “S-N Curve” for Strength versus Number of cycles. It is a common plot to illustrate and characterize the cyclic-loading lifetime of materials or components as a function of the loading level. It can be seen that as the stress is decreased the sample required more cycles to failure. This test demonstrates how the DMA 3200 can be used for a high cycle test, leveraging it’s high acceleration and durability attributes.
Example Measurements:
- Modulus of Elasticity (E)
- Stiffness (K)
- Yield Strength
- Tensile Strength
- Elongation at Break
- Fatigue Strength
Example Strength Studies:
- Accelerated Life Testing
- SN Curve Determination
- Mechanical Aging
- Creep and Recovery
- Stress Relaxation
- Tensile testing
- Description
-
Product Features
The DMA 3200 features patented ElectroForce linear motor technology enabling a single instrument to deliver unequalled performance and data accuracy. This unique motor technology combines powerful rare-earth magnets with a frictionless flexural suspension for the most precise force and displacement control over a wide range of frequencies and amplitudes. The DMA 3200 motor delivers a force output of up to 500 N and controlled displacements ranging from 1 micron to 13 mm. Testing can be conducted in both static and dynamic modes.
In addition, the frictionless, moving-magnet design eliminates failure points that exist in other motor designs, such as moving wires and bearing degradation. This ensures the most durable and reliable performance; proven over billions of cycles through decades of maintenance-free use in ElectroForce fatigue test instruments. It is the only motor in the industry backed by a ten-year warranty.
This efficient, quiet, and lubrication-free motor technology allows the DMA 3200 to be used virtually anywhere; from lab to production floor, or from the cleanroom to office space.
Key Features
- Patented, linear motor and high-resolution displacement sensor provides unmatched control over the widest ranges of force, displacement, and frequency, for superior data accuracy
- Ultra-durable, frictionless motor, backed by industry’s only ten-year warranty, provides maintenance- and worry-free operation
- High force of 500 N enables testing of larger samples or final parts under real-world conditions, by achieving higher loading levels in both DMA and fatigue analysis
- Forced Convection Oven (FCO) provides superior control and responsiveness over a temperature range of -150°C to 600°C for the highest degree of accuracy and flexibility in experiment thermal profiles
- Large Sample Oven (LSO), with a temperature range of -150°C to 315°C, offers spacious interior dimensions to accommodate testing of large samples or components
- Air Chiller Systems (ACS) offer unique gas flow cooling for sub-ambient testing without the use of liquid nitrogen, eliminating potential laboratory hazards while providing an incredible return on investment
- Broad range of fixtures accommodate a wide range of sample sizes and geometries adding to testing versatility
- Extremely rigid test frame and air bearings ensure the most accurate results on samples of very high stiffness
- Multi-color status lights provide clear and visible indication of instrument and test status
- WinTest® and TRIOS Software packages provide powerful and easy-to-use instrument control and data analysis for the ultimate flexibility in experimental design
- Specs
-
Instrument Specifications
Instruments Specifications DMA Fatigue & Quasi-Static Maximum Force 500 N 450 N Minimum Force
500 N Sensor
Optional 22 N Sensor0.2 N
0.025 N5.0 N
0.22 NForce Resolution
500 N Sensor
Optional 22 N Sensor0.006 N
0.00026 N0.015N
0.00067 NDynamic Displacement Range ±0.0005 to ± 6.5 mm ±0.002 to ± 6.5 mm Displacement Resolution 1 Nanometer 1 Nanometer Maximum Acceleration 80 G 80 G Maximum Displacement at 50 Hz ± 6.5 mm ± 6.5 mm Maximum Displacement at 100 Hz ± 1.0 mm ± 1.0 mm Modulus Range 103 to 3×1012 Pa NA Modulus Precision ± 1% NA Tan δ Sensitivity 0.0001 NA Tan δ Resolution 0.000015 NA Frequency Range 0.01 to 100 Hz 0.00001 to 300 Hz Oven Specifications
Oven Specifications FCO LSO Maximum Temperature 600°C * 315°C Heating Rate 0.1 to 60°C/min 0.5 to 10°C/min Cooling Rate 0.1 to 60°C/min 0.5 to 10°C/min Isothermal Stability ± 0.1°C ± 2°C Interior Dimensions 70 mm High x 60 mm Dia 191 x 200 x 200 mm * Note: Standard sample clamps are for use to a maximum temperature of 500°C. Optional sample clamps are required for testing to 600°C.
- Technology
-
Technology
ElectroForce® Linear Motor
ElectroForce® Linear Motor
The DMA 3200 features patented ElectroForce linear motor technology enabling a single instrument to deliver unequalled performance and data accuracy. This unique motor
technology combines powerful rare-earth magnets with a frictionless flexural suspension for the most precise force and displacement control over a wide range of frequencies and
amplitudes. The DMA 3200 motor delivers a force output of up to 500 N and controlled displacements ranging from 1 micron to 13 mm. Testing can be conducted in both static
and dynamic modes.In addition, the frictionless, moving-magnet design eliminates failure points that exist in other motor designs, such as moving wires and bearing degradation. This ensures the most durable and reliable performance that has been proven over billions of cycles through decades of maintenance-free use in ElectroForce fatigue test instruments. It is the only motor in the industry backed by a ten-year warranty.
This efficient, quiet, and lubrication-free motor technology allows the DMA 3200 to be used virtually anywhere; from lab to production floor, or from the cleanroom to office space.
High Resolution Optical Displacement Sensor
High Resolution Optical Displacement Sensor
The DMA 3200 features a High Accuracy Displacement Sensor (HADS), for the purest control and measurement of the small and large deformations necessary for DMA and fatigue testing. HADS is an ultra-performance optical device capable of friction-free, low-noise measurements with nanometer resolution at high-speeds. The sensor is placed close to the sample and loading axis to further minimize errors in compliance or thermal expansion.
Interchangeable Force Sensors
Interchangeable Force Sensors
High-stiffness and high-bandwidth force sensors are mounted on the base of the rigid frame and are interchangeable to optimize for different sample stiffnesses. The instrument comes standard with a 500 N sensor and an optional 22 N sensor can be added to improve low-force data for soft-sample tests..
High Mechanical Stiffness Design
High Mechanical Stiffness Design
In mechanical testing, an instrument design with highly stiff components, such as the frame, connecting components and sample clamps, are critical for measurement accuracy. Minimizing instrument component deformations, or compliance, reduces displacement measurements that can otherwise appear to be sample deformation. The ultra-stiff design of the 3200 ensures superior data accuracy. It starts with a rigid, three-column frame design which maximizes axial and off-axis stiffness, which are further enhanced through the use of air bearings above and below the test specimen. Unlike traditional rolling or plain bearings that introduce noise and friction into the measurement, air bearings have the added benefit of preserving the high performance attributes of the friction-free ElectroForce® linear motor.
Forced Convection Oven, FCO
Forced Convection Oven, FCO
The FCO is the premier temperature device for materials testing and is designed to optimize temperature response time, uniformity and stability. This powerful oven can heat at rates up to 60°C/min. Superior temperature stability is achieved through the use of twin element resistive gun heaters, which provide counter-rotating air flow into a uniquely shaped oven chamber which optimizes gas mixing for uniformity and stability over the temperature range of -150°C to 600°C*. The FCO comes standard with a convenient long-life internal LED light and viewing port. An optional liquid nitrogen cooling system is available for temperatures control to -150°C. Alternatively the FCO can be cooled to as low as -100°C using LN2 free Air Chilling Systems.
* Testing above 500˚C requires high temperature sample clamps
Large Sample Oven, LSO
Large Sample Oven, LSO
The LSO offers spacious interior dimensions to accommodate larger sample sizes or components. In this design, air is passed over two resistive elements and into the cavity, optimizing uniformity over large volume for temperature control from -150°C to 315°C. The LSO comes standard with a large 140 mm x 190 mm viewing window and removable door for convenience. The larger volume of the LSO is ideal for configuring the DMA 3200 with customized clamping solutions for unique applications.
Air Chiller Systems, ACS
Air Chiller Systems
Air Chiller Systems (ACS) offer unique gas flow cooling that provides for sub-ambient testing without the use of liquid nitrogen. Available in two models, the ACS-2 and ACS-3, the chillers feature a multi-stage cascading compressor design that is capable of utilizing compressed air (7 bar, 200 l/min) as the cooling medium. The ACS-2 and ACS-3 models permit operation of the FCO at temperatures as low as -55°C and -100°C, respectively. For the LSO, the ACS-2 and ACS-3 models permit operation to -15°C and -50°C, respectively. The chiller systems can help eliminate or reduce liquid nitrogen usage and associated hazards from any laboratory and offer an incredible return on investment.
- Clamping Systems
-
Clamping Systems
The DMA 3200 features a variety of sample clamping systems that provide multiple modes of deformation to accommodate a wide range of sample stiffness. Standard clamping systems available for use with the FCO include tension, compression, three-point bending, clamped bending, and shear sandwich. Standard FCO clamps, constructed of 17-4 stainless steel, are for use to a maximum temperature of 500°C, with optional clamps available for extended use to 600°C. LSO clamping systems, constructed of titanium, can accommodate larger samples and are available in tension, compression and three-point bending modes. All FCO clamps can be used with the LSO.
Three-Point Bending
Three-Point Bending
In this mode, the sample is deformed around three-point contacts at both ends and its middle. It is considered a “pure” mode of deformation as the sample is freely supported by fulcrums eliminating clamping effects. It is ideal for testing solid bars of stiff materials, such
as composites, ceramics, glassy and semi-crystalline polymers, and metals.
Tension
Tension
In this mode, the sample is clamped at the top and bottom and placed in tension. The tension clamp is for tensile testing of thin films, strips, bars and individual fibers and fiber bundles.
Compression
Compression
In this mode, the sample is placed between upper and lower round plates and deformed under various conditions of compression. Compression can be used for testing of many low to moderate modulus materials including foams, elastomers, gels, and other soft solids.
Dual and Single Cantilever
Dual and Single Cantilever
Cantilever modes are also known as “clamped” or “supported” bending modes because the support and deformation points are mechanically fixed to the sample. In dual cantilever the sample is clamped at both ends and at the center. The same clamp is used for single
cantilever and the sample is clamped between one end and the central clamp. Single cantilever allows for testing of shorter sample lengths. Cantilever is ideal for eneralpurpose
testing of thermoplastics and elastomers and other highly damped materials, as well as measuring transitions of coatings on substrates.
Shear Sandwich
Shear Sandwich
In Shear Sandwich, two equal-size pieces of a material are “sandwiched” between two ends and a central plate. The applied deformation is parallel to the sample thickness and the resultant deformation is simple shear. This mode is sometimes refered to as double-lap shear. Typical samples tested include polymer melts, foams, elastomers, gels, pastes, and other soft solids or high viscosity liquids.
Specifications
Specifications
Clamp Specifications FCO* Clamp Sample Dimensions LSO Clamp Sample Dimension Tension Up to 35 mm long, 12.5 mm wide
and 1.5 mm thickUp to 100 mm long, 12.7 mm wide, and 8 mm thick Compression 8, 15, and 25 mm diameter plates provided; maximum sample thickness is 15 mm Up to 50mm diameter, and 100 mm thickness (height) Three-Point Bend Spans of 10, 25, and 40 mm.
Up to 12.8 mm wide and 5 mm thickAdjustable Span of 10 to 100 mm. Cantilever Bend Up to 38 mm long, 12.5 mm wide, and 1.5 mm thick N/A Shear Sandwich Sample thicknesses of 0.5,
1.0 and 1.5 mm; shearing surface is 15 mm square.N/A * Note: All FCO fixtures are compatible with the DMA 3200 LSO Environmental System. Adapters are included.
- Software
-
Control and Analysis Software
The DMA 3200 is powered by two of the industry’s most powerful software packages: WinTest® and TRIOS. These two packages provide advanced algorithms, sophisticated data visualization, and powerful analysis tools for fast and flexible execution and presentation of experiments.
WinTest Advanced Control Software
WinTest Advanced Control Software
WinTest is powerful instrument control and data acquisition software for the DMA 3200. It offers an intuitive environment that provides flexibility in fatigue and DMA experimental design. DMA experimental methods include temperature ramps, temperature sweeps, strain sweeps, and frequency sweeps. Fatigue and ramp-to-failure tests are easily programmed with a variety of available waveforms including sine, triangle, square, or ramp. In addition, waveforms can be combined, or real-to-life waveforms can be imported. Unique TuneIQ and Controlled Stop help users harness the acceleration and power of ElectroForce motors by simplifying tuning tasks.
TRIOS for Data Analysis Software
TRIOS for Data Analysis Software
TRIOS for Data Analysis Software
TA Instruments TRIOS software seamlessly transfers DMA data from WinTest, providing experimentalists with the industry’s leading tool for analyzing and presenting DMA data. This intuitive software includes a wide variety of plotting tools, some of which include multi-axis plotting, smart default and user-customizable graph settings, drag-and-drop overlay, and user-defined variables. A complete range of DMA analysis models and functions includes Time-Temperature Superposition, peak analysis, onset point analysis, peak integration, and continuous and discrete relaxation spectrum. The software can be installed offline on any computer for easy sharing of data with colleagues.
- Applications
-
Applications
High Force Dynamic Mechanical Analysis, DMA
Dynamic Mechanical Analysis, DMA
DMA is a technique that applies a sinusoidal deformation, stress or strain, to a sample and measures the viscoelastic response. The frequency and magnitude of the deformation can be held constant or varied (swept) during an experiment. The material response to the deformation can be monitored as a function of temperature, frequency, or time. DMA is used to determine variety of mechanical properties, i.e., complex modulus, E*, storage and loss moduli (E’, & E”) and damping (tan δ) of viscoelastic materials, detect molecular motions, and develop structure-property relationships.
High Force Dynamic Mechanical Analysis, DMA
The high-force capability of the DMA 3200 extends experimental loading regimes and enables testing of larger samples or actual components. Examples of high force DMA capabilities are shown in the figures to the right.
The top figure shows a temperature ramp on a bar of Polycarbonate at a heating rate of 3°C/min and strain of 0.4%. The dimensions of the sample are 1.6 mm thick, 12.8 mm wide, and 19 mm long. These results demonstrate the capabilities of the DMA 3200 design in several ways. First, the high-force, high-stiffness design of the DMA 3200 enables such a thick sample to be tested in the glassy region, or below the Tg, of the polymer in tension mode. A more traditional lower force DMA instrument design would be both force and stiffness limited. Such results would have to be obtained in a bending configuration vs. tension. Second, the friction-free design which provides excellent low force sensitivity enables characterizing the glass transition through over three decades of change in modulus.
The bottom figure shows strain sweeps on two cylindrical rubber samples, tested using compression clamps, at a temperature of 30°C and frequency of 10 Hz. The sample dimensions were a diameter of 10 mm and thickness of 20 mm. These two rubber samples have different amounts of filler content, specifically 40 phr and 60 phr, where phr is a batch unit standing for parts per hundred of rubber. It can be seen that higher filler content results in a higher modulus as well as a more strain-dependent modulus. During this test, forces required to apply 20% strain, which is equivalent to 5 mm, are approaching 60 N. These results highlight both the high force and exceptional displacement control of the DMA 3200.
Fatigue and Quasi-static Testing
Fatigue and Quasi-static Testing
Most materials, components, and devices are exposed to repeated loading conditions during their use and this loading causes fatigue of the material. This fatigue can lead to dramatic changes in material behavior, which can impact overall performance, or it can result in complete and catastrophic failure. Mechanical fatigue testing provides insights on how and when materials, components, or devices fail when subjected to oscillating forces, or stresses. These insights into material behavior are used to ensure reliable product performance and prove out lifetime claims.
Monotonic testing, also known as tensile testing, is also useful for evaluating strength and deformation response. In this case, properties are measured during a single load-to-failure test.
Various material, component or device characteristics can be measured with the DMA 3200, supporting many types of dynamic or static strength studies.
Enabling Fatigue and Quasi-static Testing
The flexibility, power, and durability of the DMA 3200 enables a variety of tests in addition to DMA. Its wide range of speed and force make it useful for both fatigue and quasi-static testing. Examples of these capabilities are shown in the figures to the right.
The top figure shows a single pull-to-failure test, aka tensile test, on a small bar of solder. The displacement ramp was controlled at 1 micron per minute and temperature was constant at 25°C. The dimensions of the sample are 0.5 mm diameter and 2 mm long. This test requires slow and precise control of displacement over a very long time, in this case 14 hours. The sample demonstrates the classic linear region in the beginning of the test in the left of the plot and a very long ductile failure over the middle and right of the plot. This test demonstrates flexibility of the ElectroForce linear motor. Even though it has very high dynamic capabilities it can also be used for precise and slow testing as well.
The bottom figure shows the results of a fatigue study on thermoplastic elastomers. This curve is often called an “S-N Curve” for Strength versus Number of cycles. It is a common plot to illustrate and characterize the cyclic-loading lifetime of materials or components as a function of the loading level. It can be seen that as the stress is decreased the sample required more cycles to failure. This test demonstrates how the DMA 3200 can be used for a high cycle test, leveraging it’s high acceleration and durability attributes.
Example Measurements:
- Modulus of Elasticity (E)
- Stiffness (K)
- Yield Strength
- Tensile Strength
- Elongation at Break
- Fatigue Strength
Example Strength Studies:
- Accelerated Life Testing
- SN Curve Determination
- Mechanical Aging
- Creep and Recovery
- Stress Relaxation
- Tensile testing
- Video
-