3 Essential Types of Mechanical Testing for Polymer Development
Andy Simon | Morgan Ulrich
June 10, 2024
High-performance polymers are a critical material for manufacturers due to their combination of mechanical, thermal, and chemical properties, but especially their cost. Without adequate testing, manufacturers could run into a slew of issues, from immediate product failure to poor performance or failure after some time in usage. In this post, we review the three most important types of mechanical testing to better predict and ensure performance, safety and reliability.
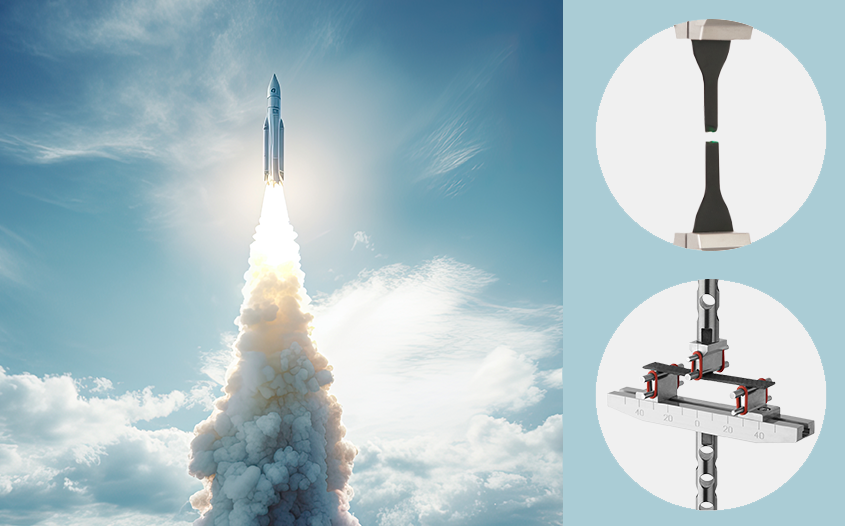
As high-performance and technical industries innovate, so do the materials they use to build their products. A car company might have to design a specialized part to handle increased torque from an EV. An engineer might need to develop a novel storage solution for critical scientific cargo in a rocket headed to the International Space Station. No matter the goal, each component must perform safely, reliably, and predictably. Success requires a multi-faceted testing approach in the development stage, because the stakes could not be higher when a product reaches the real world (or leaves it).
Whether a new supplier is necessary because of lingering supply chain complexities after the COVID-19 pandemic, weight and cost reduction are required to innovate, or sustainability is mission critical, more and more industries around the globe–from aerospace to automotive to life sciences and beyond–have shifted toward one common materials solution: High-performance, synthetic polymers.
What Are High-Performance Polymers?
High-performance polymers are a category of chemically-produced substances such as polyamides, polyethylene, Teflon, and synthetic rubber. They offer numerous benefits, including reduced production costs and lower weight than historical engineering materials like steel and aluminum.
However, implementing any new material into your production process takes extensive lab time to answer two key questions: How does this material change over time? And how does this material respond to specific types of stress? Proactively answering these questions before launching your product isn’t just essential to your P&L. It’s also crucial to establish parameters for safe and reliable use.
Polymer Mechanical Testing Basics: Fatigue, Tensile and DMA
Here are three types of mechanical testing that measure polymer behavior–whether that polymer is headed through the grocery store parking lot or into low earth orbit.
Fatigue Testing
Polymers usually fail in one of two ways:
- Over time from repeated use.
- All at once under extreme stress.
Manufacturers almost always test number two, yet they frequently overlook number one. But plastics are actually more sensitive to failure over time. Which is why fatigue testing is critical in any high-performance product–it reproduces the conditions in which a material behaves tomorrow, next week, or in 10 years.
Fatigue testing ensures you know precisely how many “pulls” it takes to break a product or material. Specialized equipment, like Load Frame Instruments, replicates real-world conditions, using predetermined levels of force over and over until a failure occurs. This information can predict product endurance, optimize structural design, inform safety limits, or help determine durability.
Observing a material after its first or even 10th use might be relatively simple. But what about its 40,000th? Fatigue testing is the most accurate and timely way to answer that question before your product leaves R&D into the real world.
Tensile (Monotonic) Testing
What happens to a polymer under a single, powerful blow? How much force is required to break it? Tensile–or monotonic–testing gets the answer.
Data like this is necessary in its own right, but tensile testing provides even more valuable insight when combined with fatigue testing. An initial tensile test provides thresholds that can then repeat over thousands of cycles. An instrument like the ElectroForce 3200 can perform both by applying precise levels of force and then duplicating those levels – thousands or even millions of times.
That testing rigor provides a fuller understanding of a material’s weakness – from catastrophic failure to normal wear and tear. This means you will gain the insight needed to save both money and time during the pre- and post-production cycles. More importantly, you’ll also get information that can save lives.
Dynamic Mechanical Analysis (DMA)
Time and force are crucial variables in polymer research. But so is temperature. Dynamic Mechanical Analysis combines all three to measure three fundamental material properties:
- Storage modulus: The stored energy (stiffness) of a material, and how that energy returns when it’s stretched and returns back into shape.
- Loss modulus: The energy lost to heat from the materials’ viscous properties, also known as damping.
- Glass transition: The temperature range in which a material changes from its rigid “glassy” state into a more rubbery, viscous state.
From testing the modulus difference between multiple samples of one polymer, understanding how a modulus changes across a temperature range, or finding the precise temperature ranges where a material loses its structural rigidity, DMA provides robust data with a wide range of applications. Quality control, product development, and product performance just to name a few.
Conclusion: Why You Need All Three
A complete understanding of a polymer’s behavior is not possible through any single form of mechanical testing. You might know how much force it takes to break a single sample. But what about when 50% of that force is applied 10,000 times? Or if that force is applied next to a running engine at midday?
Any one mechanical test–be it fatigue, tensile, or DMA–provides an incomplete picture. As more and more industries need to navigate the polymer development journey, only combining all three ensures they’re fully equipped to ensure they do it successfully. But with the proper tools and a rigorous testing process, polymers will continue to fuel innovation in industries worldwide.
Other Resources
- eBook – Essential Polymer Material Analysis Techniques for Scientists, Researchers, and Engineers
- Blog – How Sustainable Polymer Development is Supported by Dynamic Mechanical Analysis
- Application Note – Flexural Fatigue Behavior of Woven Fiberglass Composites at Elevated Temperature
- Application Note – Tensile and Fatigue Properties of Additively Manufactured Polyamides
- Application Note – Evaluation Of The Loss Of Polymer Strength And Durability Due To Fatigue Loading And Manufacturing Artifacts