Palabras clave: análisis termomecánico, CTE, materiales dieléctricos, placas de circuito impreso (PWB)
TA356-ES
Se ha desarrollado un protocolo de ensayo de TMA (análisis termomecánico) que produce datos prácticos para la comparación de diferentes materiales dieléctricos y sus efectos en el desempeño, tomando como base pruebas estándar de la industria. Este método es una combinación de protocolos térmicos estándar que PWB Inc. ha desarrollado para determinar la Tg, CTE, ciclos de tensión térmica y tiempo hasta la delaminación, tras una simulación de montaje y repetición de trabajo. Esto se consigue utilizando diversos ciclos térmicos, velocidades de rampa y tiempos de mantenimiento. El protocolo tiene tres partes o zonas diferenciadas. En la zona 1, el ensayo emula el perfil térmico de IPC TM650 – 2.4.24.5 (temperatura de transición vítrea y expansión térmica de materiales utilizados en interconexiones de alta densidad (HDI) y microvías). La zona 2 simula la excursión térmica asociada al montaje sin plomo y al trabajo repetido. La zona 3 es similar al protocolo T260 establecido en IPC 2.4.24.1 Tiempo hasta la delaminación (método TMA) utilizando la velocidad de rampa más rápida de 100 °C/min. Las tres zonas se ilustran en la Figura 1.
Preparación de la muestra: aunque se puede utilizar un elemento dieléctrico de fase «c» revestido y sin revestir, este ensayo se realiza normalmente en muestras de placas de circuito impreso (PWB) fabricadas, con los planos de tierra de cobre extendidos por toda la muestra. La muestra se corta a aproximadamente 6 mm por 6 mm. La muestra se prepara de forma que se preserve la integridad del material dieléctrico. La muestra se coloca en la platina, orientada para medir la expansión en el eje z (fuera del plano con fibras de vidrio internas) de la placa.
Zona 1: esta sección inicial tiene varias funciones; los objetivos principales son desestresar la muestra y eliminar el historial térmico antes de la primera transición vítrea (Tg) y la medición del coeficiente de expansión térmica (CTE). La muestra se somete a tres ciclos desde temperatura ambiente hasta 200 °C a una velocidad de calentamiento de 10 °C/min y de enfriamiento de 20 °C/min. Se utiliza una sonda de superficie con la presión establecida en 0.05 N. Se anota la forma de la expansión térmica a lo largo del tiempo para el ciclo 1. El CTE y la Tg se miden en los ciclos 2 y 3. En los datos del TMA, la Tg se detecta como un cambio en la pendiente del cambio de dimensión. La temperatura de inicio extrapolada de este cambio se mide como la Tg. El CTE se mide como la pendiente de los datos antes y después de la Tg en cada caso. El delta de la Tg se determina como los cambios en la Tg entre los ciclos 2 y 3. En la Figura 2 se incluyen datos representativos de esta zona.
El CTE de la muestra es un reflejo de la tensión que experimenta la placa en el entorno de uso final. El CTE es una combinación de los distintos componentes, incluidos el cobre, el vidrio y el epoxi. Con un mayor número de capas de cobre, se espera que el CTE se reduzca. En construcciones de alto contenido en resina, el CTE aumenta. La Tg del material es independiente de la construcción del PWB. Un delta de la Tg negativo puede reflejar que el material se degrada durante el ciclo térmico. Un delta de la Tg positivo puede indicar que el material se está curando durante el ciclo térmico. Un delta de la Tg superior a ±5 °C se considera significativo.
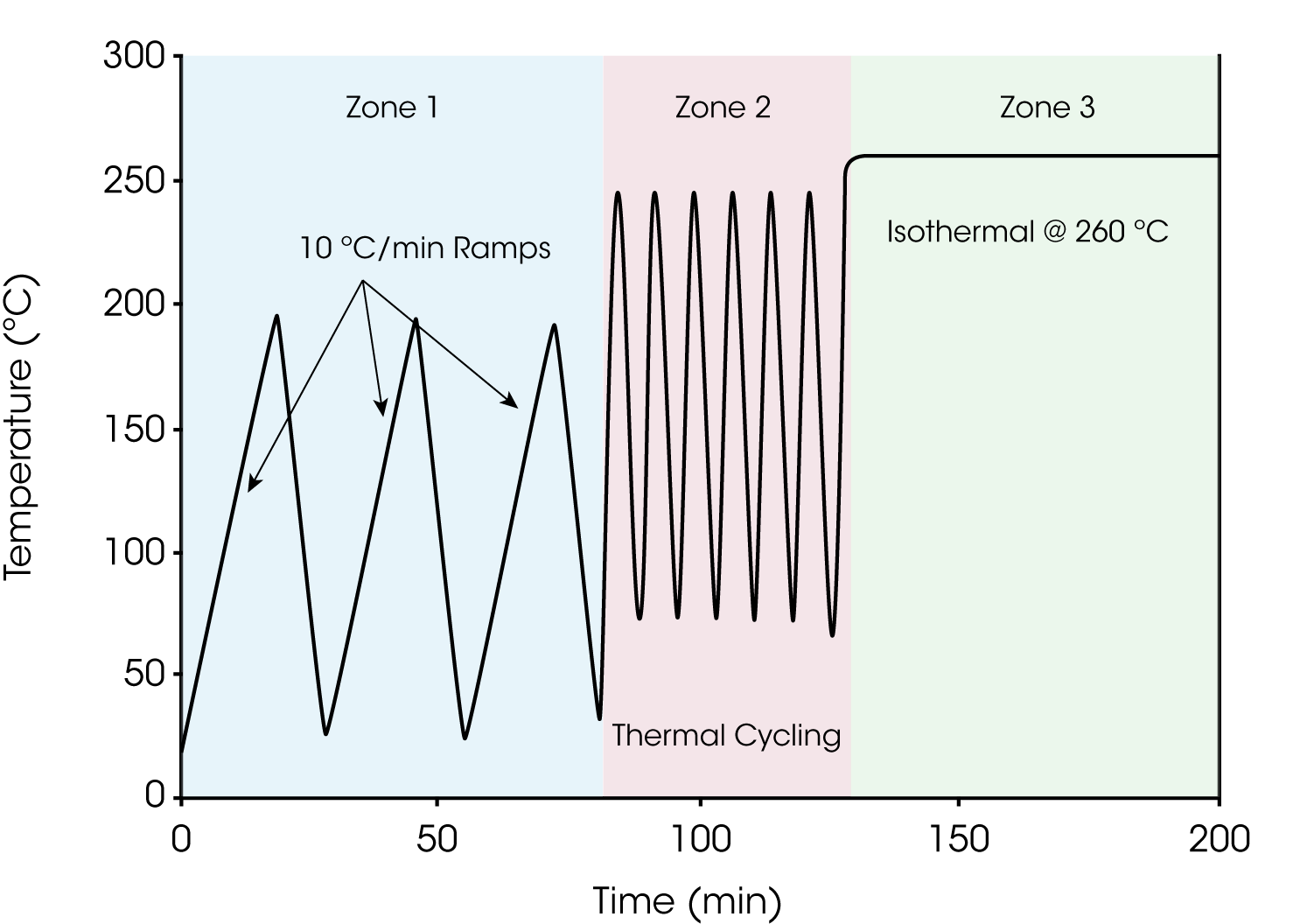
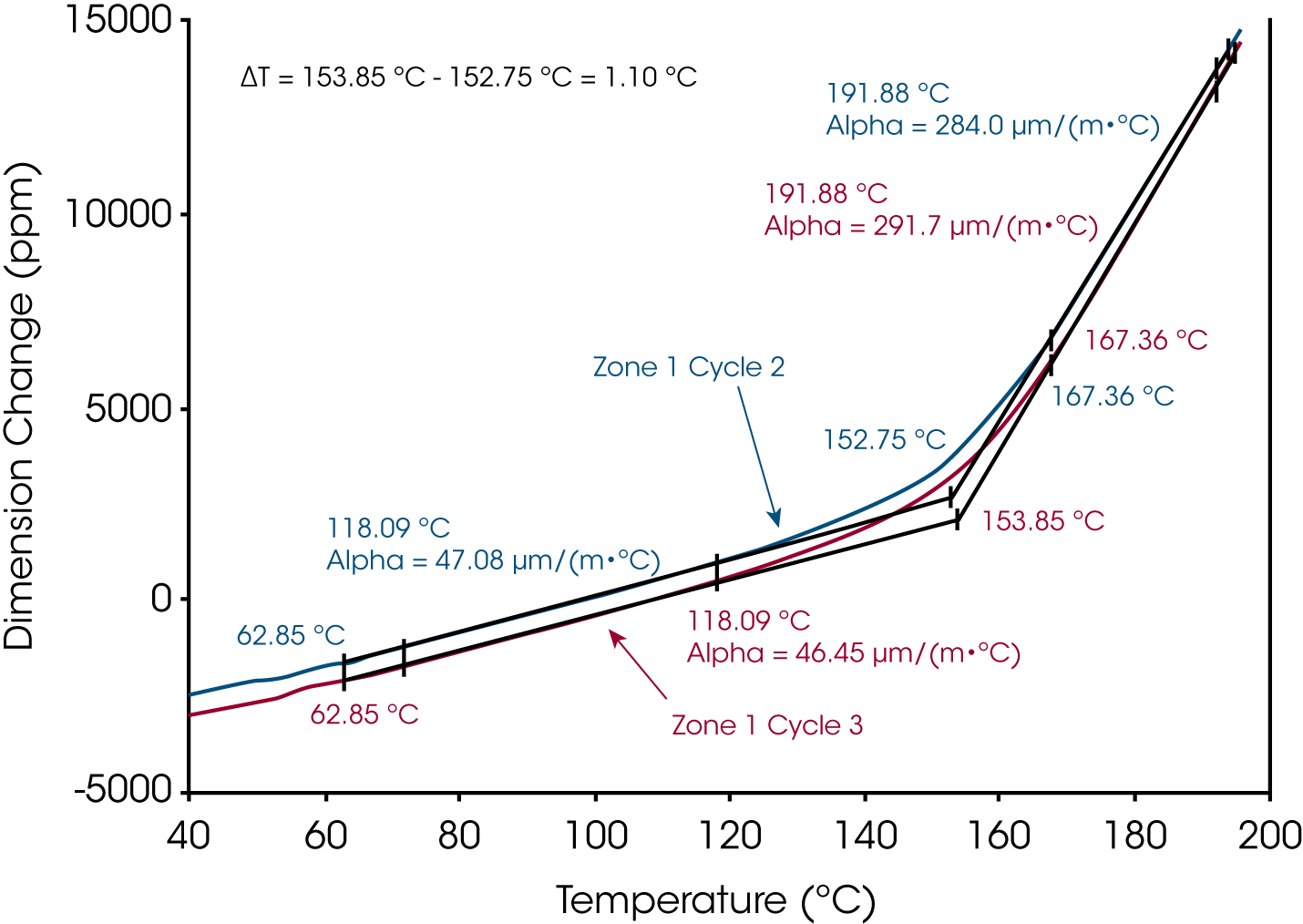
Zona 2: esta zona funciona como una evaluación «mecánica», ya que los materiales se someten a temperaturas de montaje/repetición de trabajo tradicionales o sin plomo. Se espera que los cupones que tengan una adhesión física deficiente entre las capas de dieléctrico o entre el elemento dieléctrico y el cobre puedan fallar durante esta parte del ensayo. La desgasificación, debida a los elementos volátiles o al agua atrapada, debería estar completa al final de esta zona. Seis ciclos térmicos emulan las velocidades de rampa no lineales que se utilizan en el montaje a la elevada temperatura de 260 °C. Las excursiones térmicas de las zonas 1 y 2 pueden tener un efecto de envejecimiento o, en algunos casos, de curado del sistema epóxico, dependiendo de cómo se hayan almacenado los materiales y de cómo haya procesado el fabricante el PWB. Los seis pasos del perfil térmico en esta zona se describen en la Tabla 1, y el método térmico programado se indica a continuación.
Tabla 1. Resumen del protocolo del TMA cíclico
Zona | Pre | Zona 1 | Zona 2 | Zona 3 | ||||||||
---|---|---|---|---|---|---|---|---|---|---|---|---|
Ciclos | 1 | 3 | 6 | 1 | ||||||||
Velocidad de rampa | 10 | 10 | 20 | 181 | 98 | 73 | 49 | 38 | 100 | 100 | 5 | 20 |
Temperatura | 22 | 200 | 22 | 100 | 160 | 200 | 230 | 260 | 22 | 255 | 260 | 22 |
Tiempo isotérmico (min) | 1 | 0 | 1 | 0 | 0 | 0 | 0 | 0 | 2 | 0 | 90 | End |
TMA Método térmico TA Advantage Software
- Fuerza 0.05 N
- Almacenamiento de datos desactivadof
- Equilibrar a 22.00 °C
- Isotérmico durante 1.00 min
- Almacenamiento de datos activado
- Rampa 10.00 °C/min hasta 200.00 °C
- Marcar fin de ciclo
- Rampa 20.00 °C/min hasta 22.00 °C
- Marcar fin de ciclo
- Repetir el segmento 6 dos veces
- Rampa 181.00 °C/min hasta 100.00 °C
- Rampa 98.00 °C/min hasta 160.00 °C
- Rampa 73.00 °C/min hasta 200.00 °C
- Rampa 49.00 °C/min hasta 230.00 °C
- Rampa 38.00 °C/min hasta 260.00 °C
- Marcar fin de ciclo
- Rampa 100.00 °C/min hasta 22.00 °C
- Marcar fin de ciclo
- Isotérmico durante 2.00 min
- Repetir el segmento 11 cinco veces
- Rampa 100.00 °C/min hasta 255.00 °C
- Rampa 5.00 °C/min hasta 260.00 °C
- Isotérmico durante 90.00 min
- Marcar fin de ciclo
- Almacenamiento de datos desactivado
- Rampa 20.00 °C/min hasta 22.00 °C
La zona 2 es la simulación de montaje y repetición de trabajo. Como hay muchos perfiles térmicos diferentes utilizados en el montaje, el perfil dado es una réplica exacta del perfil térmico logrado cuando los cupones se preacondicionan utilizando los métodos descritos en IPC TM 650 (IPC 2.6.26 Ensayo de ciclo térmico inducido por corriente) con la excepción de alcanzar 260 °C en lugar de 150 °C. El uso de este perfil de excursión térmica asegura que este protocolo está directamente relacionado con los resultados de las pruebas de confiabilidad. La falla en esta zona se ha atribuido a un error mecánico similar a la delaminación adhesiva. Los elementos volátiles atrapados, la desgasificación o una adhesión deficiente entre las capas laminadas (cobre o material dieléctrico) pueden provocar la delaminación en esta zona.
Zona 3: la zona 3 es análoga al ensayo T260 existente especificado en IPC – 650 – 2.4.24, Tiempo hasta la delaminación (método TMA) con una velocidad de rampa de 100 °C/minuto y un tiempo de mantenimiento máximo de 90 minutos. Si se mantiene a 260 °C, el componente epóxico de la PWB tiende a oscurecerse y puede carbonizarse si se deja durante un período prolongado. Se cree que la descomposición química es el modo de falla dominante en esta zona y que la delaminación a estas temperaturas se debe a la degradación química más que a la mecánica. La rápida velocidad de calentamiento (100 °C/min) garantiza que la muestra no se degrade durante la rampa térmica hasta 260 °C. Como el tamaño de la muestra es pequeño y suele haber cobre presente, los gradientes térmicos se reducen al mínimo. (Se ha observado que los tiempos de T260 hasta la delaminación con la rampa de temperatura más lenta de 20 °C/minuto son más cortos que los tiempos de T260 hasta la delaminación obtenidos con la rampa más rápida de 100 °C/minuto).
La Figura 3 contiene una comparación de los datos de la zona 3 para dos muestras diferentes. El cambio dimensional de la muestra A es estable durante la duración isotérmica de 260 °C, lo que indica estabilidad química y física. Sin embargo, la delaminación de la muestra B se evidencia por la rápida expansión que comienza aproximadamente a los 27 min.
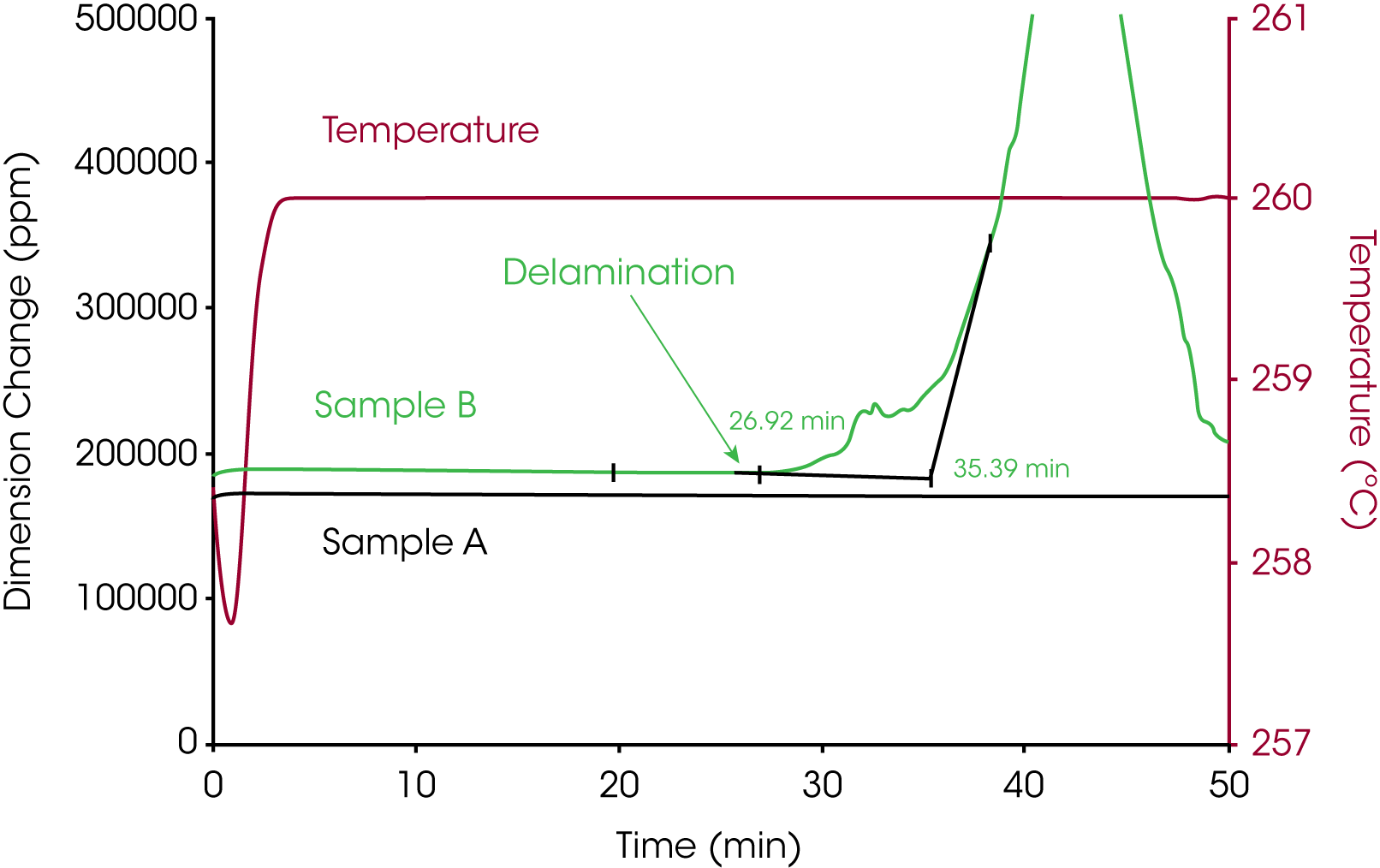
No se han establecido normas sobre el tiempo que un material debe resistir la delaminación después de alcanzar la isotermia en la zona 3. Se ha observado que un material que falla antes de 10 minutos a 260 °C tiende a desempeñarse mal cuando se somete a ensayos de confiabilidad (IPC 2.6.26 Ensayo de ciclo térmico inducido por corriente). Además, debe tenerse en cuenta que el modo de falla de confiabilidad puede ser la delaminación, pero las grietas de barril de aparición temprana también aparecen en los orificios de montaje enchapados (PTH). Las fallas en esta zona con frecuencia parecen estar relacionadas con la degradación del material del sistema epóxico y parecen ser menos fallas de origen mecánico. El envejecimiento del material es evidente; los enlaces transversales se rompen en el epoxi y se observa delaminación cohesiva. Esta delaminación no se limita a las interfaces entre las capas laminadas. Las grietas pueden atravesar los límites de las etapas «C» y «B».
medición eficaz de las tensiones térmicas (tanto físicas como químicas) a las que se somete el material dieléctrico durante el procesamiento y, al mismo tiempo que complementa los ensayos y métodos estándar de la industria, proporciona información adicional que no puede obtenerse mediante protocolos alternativos.
Reconocimiento
Paul Reid, coordinador de programa de PWB Interconnect Solutions, Inc. Nepean, Ontario Canadá, K2H 9C1 paul.reid@pwbcorp.com
Haga clic aquí para descargar la versión imprimible de esta nota de aplicación.