Palabras clave: pruebas de fatiga, pruebas de tracción, fabricación aditiva, impresión 3D, nailon, polímeros sostenibles, ElectroForce
EF037-ES
Resumen
Gracias a los avances tecnológicos, la fabricación aditiva ha superado su nicho de aplicación de creación de prototipos y se utiliza cada vez más para fabricar piezas de uso final. Tiene importancia comprender las propiedades mecánicas de las piezas fabricadas aditivamente, incluyendo el comportamiento dependiente del tiempo, como la vida a fatiga, para asegurar el desempeño y la confiabilidad. En este trabajo se evalúan las propiedades mecánicas y la respuesta dependiente del tiempo a la carga de muestras de “hueso de perro” sinterizadas por láser de dos poliamidas, poliamida-11 (PA11) a base de material biológico y poliamida-12 (PA12) a base de petróleo, mediante pruebas monotónicas de tracción hasta la rotura y pruebas de fatiga cíclica. El marco de carga ElectroForce 3300 de TA Instruments™ se utilizó por su versatilidad para ejecutar pruebas tanto monotónicas como de fatiga debido a su motor electromagnético y sus tecnologías de sensores de precisión sin contacto. Los resultados identifican la superioridad de la vida mecánica y a fatiga de la PA11 en comparación con la PA12. El enfoque presentado se puede utilizar para comparar materiales cuando es importante evaluar tanto la resistencia como la durabilidad máximas bajo cargas repetidas.
Introducción
La fabricación aditiva (additive manufacturing, AM) ha surgido rápidamente como una tecnología innovadora que permite la producción de materiales con geometrías tridimensionales (3D) complejas [1]. Inicialmente se utilizó como una técnica de creación de prototipos, pero se está adoptando cada vez más para producir piezas de uso final. La sinterización por láser es una técnica de AM común que implica el uso de material en polvo para imprimir la geometría deseada. Para comprender el desempeño del producto final, así como investigar cualquier posible variabilidad causada por la AM, es necesario caracterizar mecánicamente una muestra del material sinterizada por láser. Las propiedades que dependen del tiempo y la carga, como la vida a la fatiga, son de interés para determinar la confiabilidad del material para estas piezas de AM. Estas propiedades son de particular importancia en industrias como la aeroespacial y la biomédica, donde una comprensión profunda de la vida útil del material es fundamental para evitar fallas catastróficas [2].
Dos polímeros comúnmente utilizados en el proceso de AM de sinterización láser son la poliamida-11 (PA11) y la poliamida-12 (PA12), que pertenecen a la familia de polímeros del nailon. La PA11 es a base de material biológico, y se deriva del aceite de ricino, mientras que la PA12 es a base de petróleo, y contiene un grupo metileno adicional entre los grupos amida en la estructura del polímero. Si bien es deseable la huella de carbono más pequeña de la PA11, el grupo metileno adicional de la PA12 da por resultado diferentes propiedades mecánicas de los dos materiales [3] [4]. La PA11 en general es más fuerte y más dúctil en comparación con la PA12, pero esta última tiene mejor resistencia química [5]. Al tener en cuenta esta consideración, las propiedades de desempeño de la PA11 y la PA12 se deben comprender a fondo para ponderar el impacto ambiental frente al desempeño final del material.
Las diferencias de las propiedades mecánicas de estos dos polímeros se han explorado, pero la vida a fatiga se ha estudiado poco [4] [6]. A menudo, las pruebas mecánicas y de fatiga se realizan con instrumentos separados, lo que requiere mayor inversión y un espacio más grande. En esta nota de aplicación se examinan las respuestas cuasiestática y cíclica de muestras de “hueso de perro” de PA11 y PA12 sinterizadas por láser al utilizar el marco de carga ElectroForce 3300. También se explora la posible variabilidad inducida por el proceso de sinterización por láser.
Experimental
Se utilizó un proceso de AM con sinterización por láser para fabricar muestras de “hueso de perro” tipo V con muestras de PA11 y PA12 obtenidas en el comercio [7]. En la Figura 1a se presentan las muestras de “hueso de perro” de PA12 (izquierda) y PA11 (derecha) antes y después de la prueba hasta la falla.
Se realizaron pruebas monotónicas y de fatiga en el ElectroForce 3300 de TA Instruments. Se seleccionó el ElectroForce 3300 para este trabajo debido a su versatilidad y capacidad para ejecutar las pruebas lentas necesarias para medir el alargamiento y la resistencia a la tracción, así como pruebas cíclicas rápidas para estudiar la fatiga. En la Figura 1b se muestra el instrumento con una configuración de prueba de tracción. La geometría de la muestra y las condiciones de prueba siguieron los requisitos de la Sociedad Estadounidense para Pruebas y Materiales (American Society for Testing and Materials, ASTM) D638-22 [7]. Se realizaron pruebas de tracción monotónicas a una velocidad de 1.2 mm/min (velocidad de deformación de 0.0018 s-1) hasta la falla para todas las muestras. Se probaron tres muestras tanto de PA11 como de PA12 para examinar la variabilidad de las propiedades mecánicas.
Las pruebas de fatiga se realizaron a tensión máxima de 25, 30, 32.5, 35 y 40 MPa con una frecuencia de 25 Hz. El nivel de tensión de 40 MPa fue aproximadamente el 80 % de la resistencia máxima de la muestra de PA11 más fuerte, según se determinó a partir de las pruebas monotónicas de tracción hasta la falla. Se usó una relación R de 0.1 para mantener la tensión en la muestra. Se eligió la tensión máxima más baja para estudiar sistemáticamente cómo aumenta la vida útil del material con la tensión decreciente. Se ejecutaron tres muestras para cada nivel de tensión a fin de examinar la variabilidad entre las partes de PA11 y PA12. La deformación se vigiló con un extensómetro óptico Epsilon ONE, modelo One250CE/280. En la Figura 1c se presenta una muestra representativa de “hueso de perro” dentro de las empuñaduras.

Resultados y discusión
Pruebas monotónicas
Las propiedades mecánicas de PA11 y PA12 se evaluaron mediante pruebas de tracción monotónicas. En la Figura 2 se muestran las curvas de tensión en comparación con la deformación resultantes cuando las muestras se deformaron a una velocidad de 0.0018 s-1. La muestra de PA11 tiene una mayor resistencia máxima a la tracción (ultimate tensile strength, UTS) y un porcentaje de alargamiento mayor en el momento de la falla para todas las muestras.
En las Tablas 1 y 2 se muestran los valores de UTS y el porcentaje de alargamiento hasta la falla, junto con los valores promedio de las tres curvas y la desviación estándar.
La resistencia más alta y el mayor alargamiento de la PA11 se han observado antes cuando se utiliza un proceso de fusión en lecho de polvo para producir piezas de PA11 y PA12 [3]. Los resultados de las pruebas monotónicas muestran que la PA11 tiene mayor capacidad para alargarse sin perder resistencia en comparación con la PA12. Esto hace que la PA11 sea una mejor opción para piezas de uso final y para aplicaciones donde se requiere un material más resistente y dúctil.
Probar las muestras por triplicado brinda la oportunidad de observar la variabilidad potencial en el proceso de sinterización por láser en sí. La sinterización por láser es un proceso de AM por fusión en lecho de polvo, y ha recibido críticas desde el punto de vista de la reproducibilidad [8]. En la sinterización por láser, la variabilidad tiende a provenir de las propiedades del lecho de polvo, las características del láser y los parámetros del proceso. En la Tabla 1 se muestra que el porcentaje de alargamiento hasta la falla tiene la mayor variabilidad, mientras que la UTS permanece consistente para ambos materiales. Las muestras de PA11 y PA12 tienen, cada una, una curva en la Figura 2 que se alarga notablemente más en comparación con las otras dos réplicas, y esto imparte una desviación estándar más alta, como se observa en la Tabla 1. Las inconsistencias por el proceso de AM pueden manifestarse como variaciones de las propiedades mecánicas, lo cual es indeseable para un producto de uso final.

Tabla 1. Resistencia máxima a la tracción (ultimate tensile strength, UTS) y % de alargamiento en el momento de la falla para la PA11 con el promedio de ejecución por triplicado y la desviación estándar (σ).
PA11 | UTS (MPa) | Alargamiento (%) |
---|---|---|
1 | 49.24 | 44.76 |
2 | 49.40 | 54.24 |
3 | 49.87 | 41.87 |
Promedio | 49.50 | 46.96 |
σ | 0.33 | 6.47 |
Tabla 2. Resistencia máxima a la tracción (UTS) y % de alargamiento en el momento de la falla para la PA12 con el promedio de ejecución por triplicado y la desviación estándar (σ).
PA12 | UTS (MPa) | Alargamiento (%) |
---|---|---|
1 | 39.91 | 23.35 |
2 | 40.35 | 23.40 |
3 | 40.51 | 26.56 |
Promedio | 40.25 | 24.44 |
σ | 0.31 | 1.84 |
Pruebas de fatiga
Las pruebas monotónicas se han utilizado extensamente para caracterizar las propiedades mecánicas de las piezas de AM. A medida que las técnicas de AM se utilizan cada vez más, tiene importancia comprender la confiabilidad de la pieza resultante y el desempeño esperado durante su vida útil. Esto exige una caracterización más allá de las pruebas de tracción monotónicas simples y rápidas, y que el producto se evalúe a lo largo del tiempo bajo las cargas y deformaciones que encontrará en la aplicación prevista.
Se realizaron pruebas de fatiga en las muestras de PA11 y PA12 para evaluar la robustez de los materiales bajo carga cíclica constante. Para ilustrar esta prueba, en la Figura 3 se muestra el desplazamiento total en comparación con el tiempo para una de las muestras de PA11 durante la carga cíclica hasta la falla a una tensión de 30 MPa. Durante todo el tiempo experimental, de 0 a ~2800 s (7×104 ciclos), la longitud de la muestra aumenta gradualmente a lo largo de la prueba, como se observa por un desplazamiento cada vez mayor desde su posición original. Hacia el final de la prueba, justo antes de los 2400 s (6×104 ciclos), el desplazamiento comienza a aumentar a un ritmo más rápido. Esto continúa hasta que el material falla, lo que se indica por un aumento repentino y brusco del desplazamiento debido a la rotura del material.
En el recuadro de la Figura 3 se muestra un intervalo de 1 s durante la prueba para ver lo que le está sucediendo al material en una escala de tiempo más corta. Todas las pruebas se realizaron a 25 Hz. En este intervalo de un segundo, el material está expuesto a 25 ciclos sinusoidales con una amplitud bien definida que está imponiendo tensión cíclica sobre el material hasta el nivel de 30 MPa. Ver esta prueba desde estas dos escalas de tiempo diferentes muestra cómo las deformaciones continuas en escalas de tiempo cortas conducen a un aumento masivo de la longitud de la muestra, y esto da pie a la falla final del material.

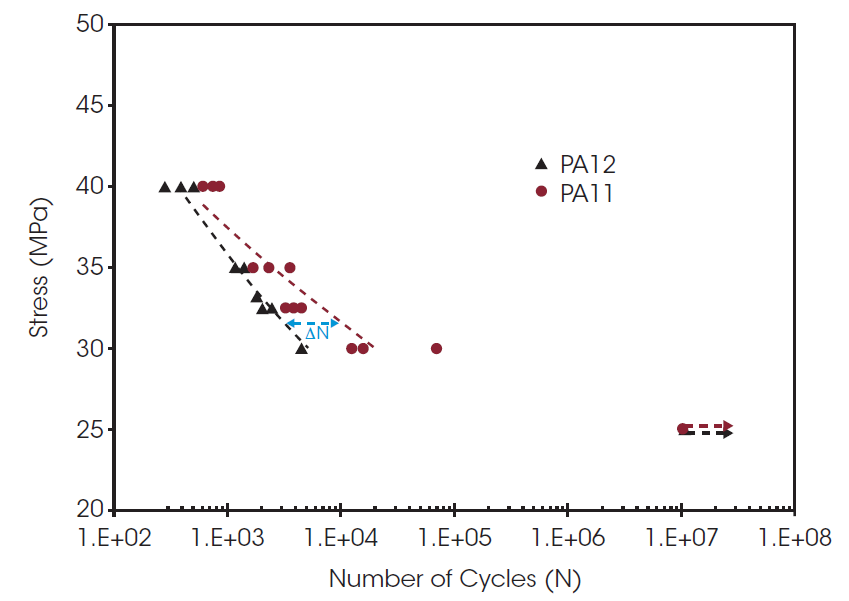
En la Figura 4 se muestran las curvas S/N resultantes, también llamadas curvas de Woehler, con tensión que varía de 40 a 25 MPa. La curva S/N grafica la amplitud de la tensión (stress, S) cíclica en comparación con el número de ciclos hasta la falla (N), lo que la hace útil para visualizar la fatiga. A 25 MPa, todas las muestras alcanzaron 107 ciclos, que se estableció como el límite del ciclo de falla para este estudio. Cuando un nivel de tensión da por resultado falla de muestras, se considera que ese nivel de tensión está por debajo del límite de resistencia.
Para ambas muestras, el número de ciclos hasta la falla disminuye a medida que la tensión aumenta. A niveles de tensión de 30 a 40 MPa, la PA12 alcanza la falla a un número de ciclos más bajo en comparación con la PA11. Se crearon líneas de tendencia de mejor ajuste para las curvas con datos de 40 a 30 MPa; las muestras de nivel de 25 MPa se omitieron debido a la ausencia de falla. A tensión alta, el número de ciclos hasta la falla es del mismo orden de magnitud, a unos pocos cientos de ciclos. A partir de las líneas de tendencia se observa que la diferencia en los ciclos hasta la falla (ΔN=NPA11-NPA12, línea azul en la Figura 4) aumenta a medida que disminuye la tensión. Este resultado es coherente con los datos monotónicos, porque se espera que la PA11 más fuerte y dúctil sea más robusta bajo carga cíclica.
Las pruebas por triplicado en cada nivel de tensión permiten analizar la reproducibilidad del proceso de AM de una manera similar a las pruebas monotónicas. La curva PA12 S/N tiene poca dispersión en los datos en cada nivel de tensión. Sin embargo, la PA11 tiene una dispersión notable de los datos para niveles de tensión de 35 y 30 MPa. A partir de los datos monotónicos también se observó que las desviaciones estándar en la UTS y el % de alargamiento en el momento de la falla fueron mayores para la PA11 en comparación con la PA12. Esto identifica que los problemas de reproducibilidad pueden ser contraproducentes para la PA11 en el proceso de AM de sinterización por láser, y esto se manifiesta como variabilidad de las propiedades mecánicas y de fatiga del material.
La variabilidad observada en este trabajo muestra que se debe llevar a cabo una evaluación exhaustiva de las piezas de PA11 sinterizadas por láser antes de su uso en la aplicación. Esto implicará probar una mayor cantidad de muestras en los niveles de tensión de aplicación dados y, por consiguiente, establecer de manera más rigurosa los niveles de confianza de los límites de fatiga subsiguientes. También se deben realizar pruebas de fatiga sistemáticas entre 25 y 30 MPa a fin de establecer un límite de resistencia preciso que se base en los resultados en los que el nivel de tensión de 25 MPa causó falla de todas las muestras. Además, esta prueba debe acompañarse de una caracterización adicional del material mediante métodos directos e indirectos, como microscopia electrónica, difracción de rayos X y análisis térmico, para identificar los orígenes microestructurales de esta variación.
Conclusiones
A medida que las piezas de AM se utilizan más ampliamente en aplicaciones de uso final, es necesario comprender el desempeño mecánico y la confiabilidad de las piezas, así como la posible variabilidad causada por el proceso de fabricación. En esta nota se examinaron la PA11 y PA12 en relación con sus propiedades mecánicas y de vida a fatiga al utilizar el ElectroForce 3300. El ElectroForce 3300 resultó ser idóneo para estas mediciones, al utilizar un solo equipo para pruebas tanto mecánicas como de fatiga bajo una amplia gama de métodos de prueba:
- La prueba de tracción monotónica identificó que la PA11 tiene propiedades superiores de resistencia mecánica y ductilidad con una mayor UTS y un mayor % de alargamiento en el momento de la falla en comparación con la PA12.
- En las pruebas de vida a fatiga se identificó que la PA11 tuvo un ciclo de vida a fatiga más prolongado en comparación con la PA12 en cada nivel de tensión probado. La diferencia entre el aumento del ciclo de vida de la PA11 sobre la PA12 creció a medida que disminuyó la tensión.
- La realización de múltiples iteraciones para cada muestra permitió evaluar la repetibilidad del diseño de la pieza en el proceso de AM.
La variación de las propiedades mecánicas, especialmente en PA11, identificó que aún es necesario trabajar para superar la variabilidad entre piezas que ha afectado a los procesos de AM. Con base en el análisis mecánico y de fatiga, la PA11 es el mejor polímero para un producto de uso final, porque se espera que siga siendo robusta y tenga una vida útil más prolongada en comparación con la PA12. Junto con estas consideraciones de propiedades mecánicas, la baja huella de carbono de la producción de PA11 a partir de fuentes de origen biológico en comparación con la PA12 a base de petróleo hacen de ella una clara elección de material también desde el punto de vista de la sostenibilidad.
Referencias
- G. N. Mhetre, V. S. Jadhav, S. P. Deshmukh and C. M. Thakar, “A Review on Additive Manufacturing Technology,” ECS Trans., vol. 107, p. 15355, 2022.
- S. S. Alghamdi, S. John, N. R. Choudhury and N. K. Dutta, “Additive Manufacturing of Polymer Materials: Progress, Promise, and Challenges,” Polymers, vol. 13, p. doi. org/10.3390/polym13050753, 2021.
- A. Salazar, A. Rico, J. Rodriguez, J. S. Escudero and F. M. de la Escalera Cutillas, “Monotonic loading and fatigue response of a bio-based polyamide PA11 and a pertol-based polyamide PA-12 manufactured by selective laser sintering,” European Polymer Journal, vol. 59, pp. 36-45, 2014.
- N. Lammens, M. Kersemans, I. De Baere and W. Van Paepegem, “On the visco-elasto-plastic response of additively manufactured polyamide-12 (PA-12) through selective laser sintering,” Polymer Testing, vol. 57, pp. 149-155, 2017.
- S. C. Lao, W. Yong, K. Nguyen, T. J. Moon, J. H. Koo, L. Pilato and G. Wissler, “Flame-retardant Polyamide 11 and 12 Nanocomposites: Processing, Morphology, and Mechanical Properties,” Journal of Composite Materials, vol. 44, pp. 2933-2951, 2010.
- B. Van Hooreweder, D. Moens, R. Boonen, J. P. Kruth and P. Sas, “On the difference in materials structure and fatigue properties of nylon specimens produced by injection molding and selective laser sintering,” Polymer Testing, vol. 32, pp. 972-981, 2013.
- A. D638-22, “Standard Test Method for Tensile Properties of Plastics,” ASTM International, 2022.
- L. Dowling, J. Kennedy, S. O’Shaughnessy and D. Trimble, “A review of critical repeatability and reproducibility issues in powder bed fusion,” Materials and Design, vol. 186, p. 108346, 2020.
- V. Malmgren, “PA11 vs PA12-one atom different,” wematter, 01 2022. [En línea]. Disponible en: https://wematter3d.com/pa11-vs-pa12-one-atom-different. [Consultado el 5 de mayo de 2023].
Reconocimiento
La redacción de este documento estuvo a cargo del Dr. Mark Staub en TA Instruments.
Haga clic aquí para descargar la versión imprimible de esta nota de aplicación.