Thermoplastic processing converts resins supplied in the form of compounds and masterbatches into films, sheets, and other rigid form factors through techniques like injection molding, extrusion, blow molding, and thermoforming. At this step of the polymer value chain, analytical techniques assist with optimizing process conditions and troubleshooting, studying product performance under end-use environmental conditions, and identifying root causes of product failure in the field.

Instruments and Test Parameters
Mechanical properties of materials
- Storage modulus, loss modulus, tan delta
- Glass transition (Tg)
Characterization of blend compatibility
- Storage modulus, loss modulus, tan delta
Effect of heat and humidity on mechanical properties
- Storage modulus, loss modulus, tan delta
- Glass transition (Tg)
Differential Scanning Calorimetry
Thermal stability
- Oxidative Induction Time (OIT)
- Oxidative Onset Time (OOT)
Batch-to-batch repeatability
- Crystallinity
Polymer Workflow Automation
Thermal stability
- Decomposition temperature
Composition determination
- Filler content (residue)
- Decomposition products
Polymer Workflow Automation
Processability
- Viscosity flow curve
- Zero shear viscosity
- Viscoelastic properties (Storage modulus, loss modulus)
- Crossover modulus and frequency
Melt strength
- Extensional viscosity
Polymer Workflow Automation
Application Examples
How stable is this resin during processing and end-use?
Stabilizers and other additives are often added to resins to prevent degradation from environmental effects encountered during processing and end-use conditions. These additives include antioxidants, oxygen scavengers, heat and UV light stabilizers, or flame retardants, to ensure the polymer’s intended properties are maintained during processing and the product’s lifetime. Stabilizers are inherently sacrificial and are gradually consumed when exposed to high temperature or UV light; once the stabilizer is completely exhausted, the polymer properties start to degrade rapidly.
The performance of stabilizers can be evaluated through Oxidative Induction Time (OIT) analysis on the DSC. In this isothermal test, the purge gas in the DSC is switched from Nitrogen to Oxygen, providing an environment where the stabilizer is consumed. At the onset of polymer degradation, the heat flow signal starts to increase and the time is noted as OIT.
Temperature ramps on the DSC can also be used to measure the Oxidative Onset Time (OOT), a related measure of polymer stability. Both OIT and OOT tests can also be performed using a high-pressure DSC, which reduces test time by accelerating stabilizer consumption.
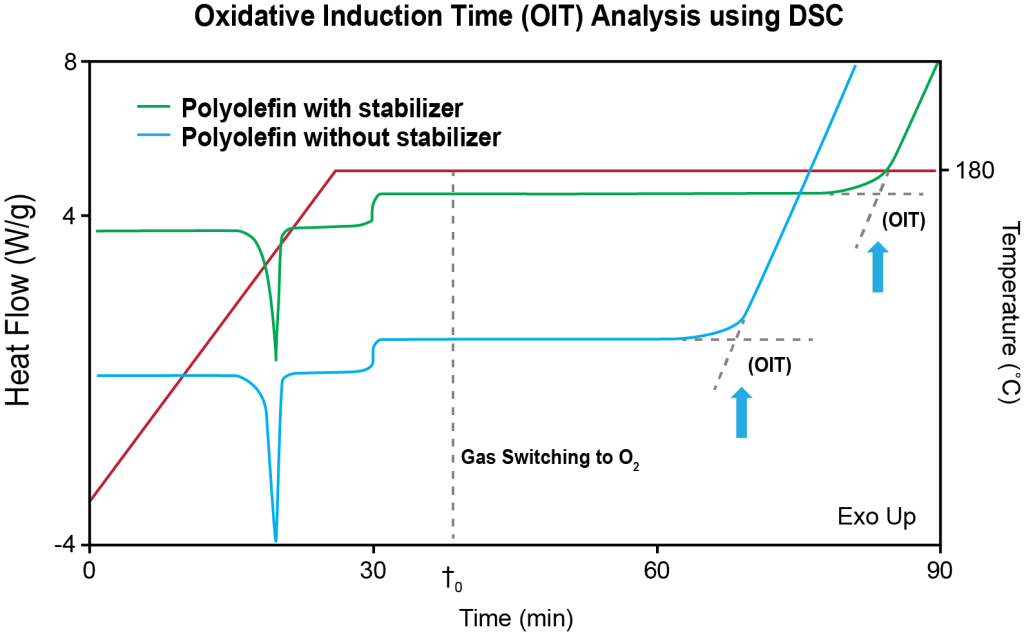
Answer the following questions with OIT & OOT results from your DSC:
- Feedstock evaluation: Can this resin be processed as-is? Are antioxidants needed for additional stability?
- Failure Analysis: Did this part antioxidant at sufficient levels suitable for the end-use conditions?
- End-of-Life recycling: How much antioxidant is needed to stabilize and process this batch of PCR?
Related Application Notes:
Does this resin possess sufficient melt strength for blow molding?
Manufacturing processes such as blow molding, film blowing, thermoforming and fiber spinning involve the application of an extensional deformation to polymer melts; the deformation process is comparable to a balloon or bubble gum being blown into a sphere. Successful products depend on the ability of the polymer melt to sustain large deformation without breaking or collapsing and can be quantitatively described by the extensional viscosity.
Compared to shear viscosity, extensional viscosity measurements are extremely sensitive to the molecular structure. Polymers with high degree of Long-Chain Branching (LCB) display a strain-hardening effect during elongational deformation, especially at increasing speeds. This behavior indicates a higher melt strength during extensional processes, which helps to stabilize a bubble and prevent collapsing, or avoid thin fibers breaking. Conversely, polymers with a linear morphology (no branching) often fail to process successfully.
This critical performance differentiation is not adequately detected by traditional flow measurements. Extensional viscosity measurements can be easily made on rotational rheometers using the Extensional Viscosity Accessory (EVA).
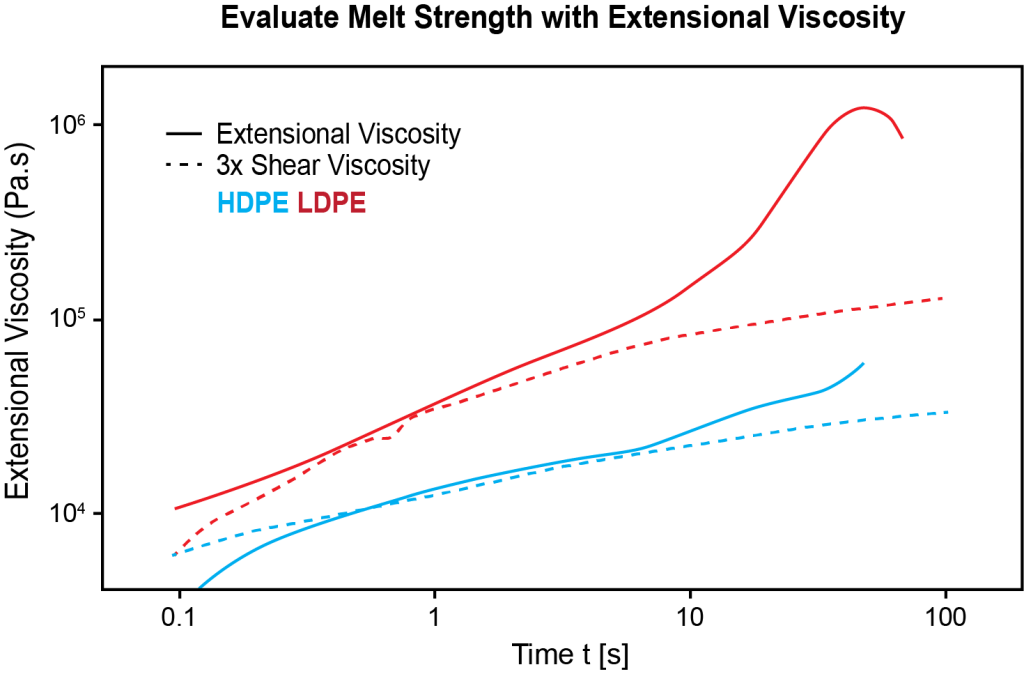
Answer the following questions with extensional viscosity measurements:
- Processability: What is the melt strength of this resin? How much stretching can the bubble withstand before it breaks?
- End-of-life: Do the processing parameters need to change for this batch with recycled resins? What additives are needed to process this batch of recycled resins into a film? (e.g., chain extenders)
How does the product perform?
Understanding the product performance under final end-use application conditions helps guide product formulation, process optimization, and plays an important role in troubleshooting and failure analysis. For plastic products, the mechanical properties are closely tied to the end-use product performance and can be evaluated through a combination of different mechanical testing techniques that provide information on the material’s modulus. Depending on the type of deformation, additional information and insights can also be obtained.
- Monotonic testing: Unidirectional deformation to failure under an applied load – test materials under conditions of increasing load (e.g., Stress-strain curves)
- Fatigue testing: Understand damage and failure from repeated loading – test materials and finished products under conditions of increasing cycling (e.g., S/N curves)
- Dynamic Mechanical Analysis (DMA): Study solid viscoelastic properties as a function of temperature and deformation frequency (e.g., Glass transition temperature (Tg), Time-Temperature Superposition (TTS))
DMA testing investigates the temperature dependance of a solid specimen’s mechanical properties under bending, compression, or tensile deformation. It provides quantitative information about the material’s viscoelastic properties through the Storage Modulus (E’), Loss Modulus (E”) and tan(δ) (damping factor). When polymeric specimens are heated, they undergo transitions that are reflected in these mechanical parameters. DMA is one of the most sensitive techniques available to measure glass transition and beta transition temperatures, since it picks up on subtle changes in local polymer mobility brought about by the increased temperature.
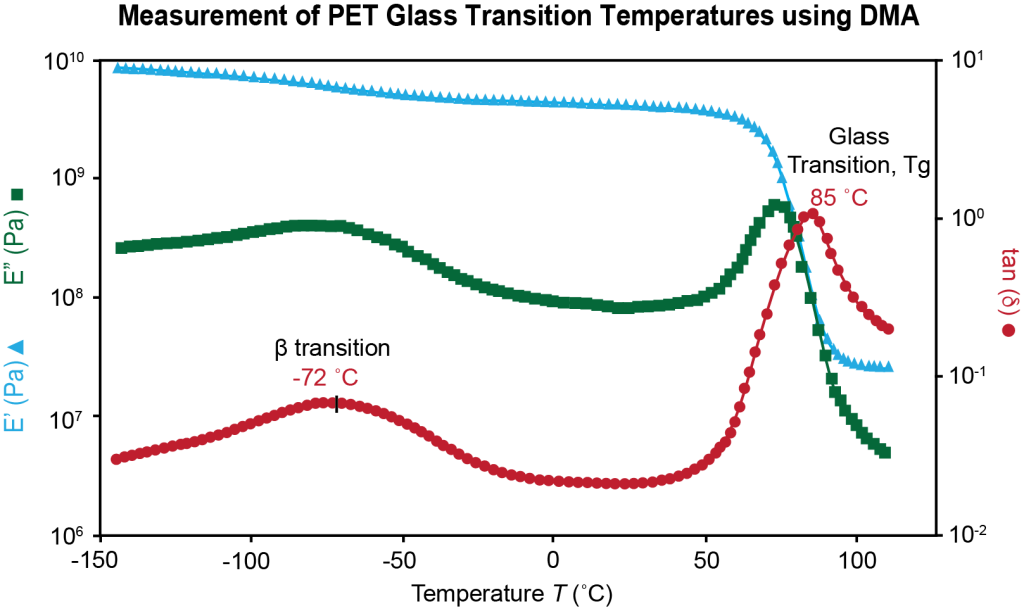
Answer the following questions with results from your DMA:
- Processing: Was this batch of resins blended uniformly to achieve miscibility?
- Product performance: Does this product have the right mechanical strength/ stiffness for the intended end-use environmental conditions (temperature, relative humidity)?
- End-of-life: Do products produced with recycle resin match the mechanical properties of those made with virgin resins?