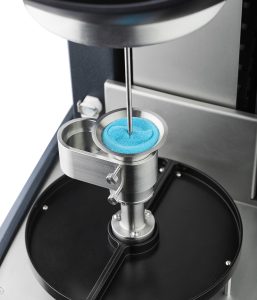
The Powder Rheology Accessory expands the DHR’s capabilities to powders, enabling characterization of behaviors during storage, dispensing, processing and end use. Product development and process optimization are accelerated with quantitative measurements of dynamic flowability and shear properties of consolidated powder, under ambient conditions or controlled temperature. Screening incoming raw materials or new formulations detects unexpected behavior to avoid large-scale production issues and provide granular-level insights into powder morphology variations to enable solutions to challenging processing problems.
Features & Benefits:
- Flexibility to switch from liquid or solid samples to powders in less than 10 seconds, keeping pace with rapidly changing testing needs
- Measurements of powder behavior during processing, dispensing, storage and end- use with interchangeable tools for dynamic flowability, shear properties and more
- Repeatable results enabled by fast, easy intuitive sample loading and automated conditioning protocols
- Walk-up usability for every operator – TRIOS Powder test forms streamline routine test methods while enabling complete customizability
- Simplified data interpretation with optional Powder Analysis software, reporting quantitative key performance indicators in one click
- Available temperature control: -10 °C to 150 °C
Repeatable Sample Loading
Accurate results depend on repeatable powder sample preparation. The accessory’s unique loading tools and automated conditioning procedures reduce sample-to-sample variability to as low as 0.2%.
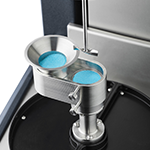
Temperature Control
The DHR offers complete powder rheology testing with controlled temperature to predict powder behaviors under a wide range of environmental conditions. The SmartSwap™ Peltier Concentric Cylinder Jacket offers a versatile, convenient, and safe solution for every powder testing method: Shear, Flowability, Wall Friction, and Compressibility.
Powder temperature is controlled through direct conductive heating and cooling. Sample temperature uniformity is achieved through an upper heat shield and composite heat-break geometries preventing thermal gradients. Peltier technology enables sample heating up to 150 °C and cooling down to -10 °C without the need for liquid nitrogen or mechanical chillers.
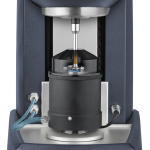
Flow Cell
An impeller rotor is moved helically through the powder, measuring torque and force to report unconfined and confined Total Flowability Energy.
Flow Sample Volume: 21.2 mL
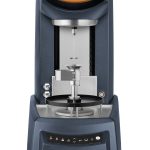
Shear Cell
Powder is consolidated in a serrated cup and plate and slowly sheared until yield under varying normal stress, reporting cohesion, yield strength, flow function and more.
Shear Sample Volume: 13.1 mL
ASTM D7891
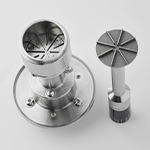
Wall Friction
Consolidated powder interactions with a solid surface are directly measured, reporting Wall Friction Angle. Interchangeable smooth and rough steel plates are included, with options for different materials.
Wall Friction Sample Volume: 13.1 mL
ASTM D7891
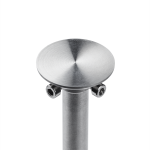
Compressibility
Pre-conditioned powder is subjected to incrementally increasing normal stresses, monitoring the decrease in sample volume as powder is compressed and reporting % Compressibility under specified normal stress.
Compressibility Sample Volume: 21.2 mL
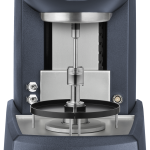
Powder materials present unique challenges at all stages, from new formulation development to final product performance. The Powder Rheology Accessory provides insights into real-world behavior to accelerate solutions to processing problems.
Formulation
In development, formulators are often seeking insight into bulk powder behavior. Unexpected processing issues may occur during scale-up, requiring re-formulation and delaying product commercialization.
Powder Rheology Insights
Powder rheology measurements on small lab-scale samples (< 25 mL) demonstrate impacts of formulation changes on processability and performance, avoiding future large-scale problems.
Characterizing effects of additives on powder shear properties
Successful formulations must incorporate the required components while achieving optimal rheological behavior. Adding a new ingredient, even at very low levels, can change bulk properties.
The Powder Shear Cell is sensitive to these changes, demonstrated by measuring sand before and after blending with 5% silicone oil. This small addition dramatically changes behavior under low normal stress, increasing Cohesion and Yield Strength by a factor 10. Major Principal Stress, a measure of the maximum stress under consolidation, is unaffected.
The familiar effect of wetting sand to build a sandcastle is quantified by Powder Shear testing, and broadly applicable to optimizing all powder formulations to meet performance requirements.
Storage
Hoppers and silos must be optimized for powder characteristics to ensure consistent, controlled dispensing and avoid blockages, rat-holing or avalanching.
Powder Rheology Insights
Shear measurements of consolidated powder report parameters used in hopper design: Cohesion, Unconfined Yield Strength, Major Principal Stress, Flow Function and Angle of Internal Friction.
Consolidation of Graphite Anode Powder
The graphite used in battery anode slurries is stored in large hoppers and dispensed as needed. The compressive load on the powder varies with the position inside the hopper, which results in changes in powder properties. Powder shear measurements of graphite under increasing consolidation stress show an increased yield strength, preventing the powder from dispensing from the hopper, and increased cohesion, requiring longer mixing time to distribute uniformly into a slurry.
Stability
Powder morphology is susceptible to changes during mixing, processing or long-term storage. Instabilities alter processing performance and compromise the quality of a final product.
Powder Rheology Insights
Flowability tests detect changes from agglomeration or caking, or segregation of blends which leads to inaccurate dosing in pharmaceuticals, or inconsistent behavior in industrial materials.
SLS Printing Powder Stability
Selective Laser Sintering (SLS) is an additive manufacturing process fusing powdered raw material to form a solid part, leaving the majority of powder unused. Ideal SLS powders can be reclaimed from the printer bed and reused, without compromising performance. Unconfined flowability of a PA-11 SLS powder was measured at elevated temperatures, reaching above glass transition and below melt temperature as required for printing. Upon repeating the measurement, the powder’s Total Flowability Energy shows only a 4% increase, indicating its behavior has not significantly changed and may be reused successfully.
Processing
In production, powder undergoes multiple processes such as feeding, mixing, granulation and milling. Successful processing requires continuous flow at all stages to keep up production.
Powder Rheology Insights
Flow energy measurements predict processability at critical stages of production, in both confined and unconfined conditions across varying flow speeds.
Impact of Lactose Morphology on Flowability During Processing
The choice of excipients used in pharmaceutical powders for solid dose tableting impacts critical process parameters (CPP). Lactose is widely used in pharmaceuticals, but rheological behavior is highly dependent on particle morphology.
Milled lactose exhibits greater resistance to flow due to interlocking of its jagged, irregular particles, unlike the smooth, spherical particles of spray-dried lactose. The Powder Flow Cell was used to measure both materials over a range of speeds, revealing milled lactose’s total flow energy increases at slower rates, predicting insufficient flow rates during dispensing or mold filling. Pre-screening CPPs such as flowability helps to prevent costly manufacturing issues and ensure product quality.
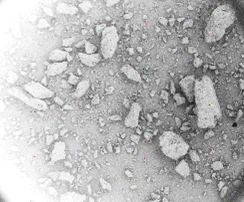
Milled
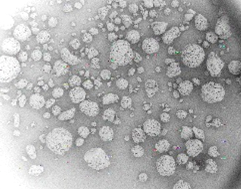
Spray-Dried
End Use
Food, personal care and consumer products must meet consumers’ expected behavior. Powder caking or agglomeration impacts dispensing, compromising consumer acceptance.
Powder Rheology Insights
Powder rheology directly measures dispensing behavior and evaluates impacts of storage conditions such as consolidate or environmental changes.
Product Video
Tech Tip
- App Note: Powder Rheology of Lactose: Impacts of powder morphology on performance of pharmaceutical excipients
- App Note: Powder Rheology of Graphite: Characterization of Natural and Synthetic Graphite for Battery Anode Slurries
- App Note: Epoxy Powder Rheology: Impact of Temperature on Flow and Shear Properties
- App Note: Effect of Moisture and Substrate Material on Wall Friction Angle of Carboxymethyl Cellulose Powder
- App Note: Effect of Moisture on Cohesion Strength of Carboxymethyl Cellulose Powder
- Blog: Powder Rheology for Pharmaceutical Development
- DHR Accessories Brochure
- Explore Discovery Hybrid Rheometers
- Request a Quote
- Description
-
The Powder Rheology Accessory expands the DHR’s capabilities to powders, enabling characterization of behaviors during storage, dispensing, processing and end use. Product development and process optimization are accelerated with quantitative measurements of dynamic flowability and shear properties of consolidated powder, under ambient conditions or controlled temperature. Screening incoming raw materials or new formulations detects unexpected behavior to avoid large-scale production issues and provide granular-level insights into powder morphology variations to enable solutions to challenging processing problems.
- Features & Benefits
-
Features & Benefits:
- Flexibility to switch from liquid or solid samples to powders in less than 10 seconds, keeping pace with rapidly changing testing needs
- Measurements of powder behavior during processing, dispensing, storage and end- use with interchangeable tools for dynamic flowability, shear properties and more
- Repeatable results enabled by fast, easy intuitive sample loading and automated conditioning protocols
- Walk-up usability for every operator – TRIOS Powder test forms streamline routine test methods while enabling complete customizability
- Simplified data interpretation with optional Powder Analysis software, reporting quantitative key performance indicators in one click
- Available temperature control: -10 °C to 150 °C
- Technology
-
Repeatable Sample Loading
Accurate results depend on repeatable powder sample preparation. The accessory’s unique loading tools and automated conditioning procedures reduce sample-to-sample variability to as low as 0.2%.
Temperature Control
The DHR offers complete powder rheology testing with controlled temperature to predict powder behaviors under a wide range of environmental conditions. The SmartSwap™ Peltier Concentric Cylinder Jacket offers a versatile, convenient, and safe solution for every powder testing method: Shear, Flowability, Wall Friction, and Compressibility.
Powder temperature is controlled through direct conductive heating and cooling. Sample temperature uniformity is achieved through an upper heat shield and composite heat-break geometries preventing thermal gradients. Peltier technology enables sample heating up to 150 °C and cooling down to -10 °C without the need for liquid nitrogen or mechanical chillers.
Flow Cell
An impeller rotor is moved helically through the powder, measuring torque and force to report unconfined and confined Total Flowability Energy.
Flow Sample Volume: 21.2 mL
Shear Cell
Powder is consolidated in a serrated cup and plate and slowly sheared until yield under varying normal stress, reporting cohesion, yield strength, flow function and more.
Shear Sample Volume: 13.1 mL
ASTM D7891
Wall Friction
Consolidated powder interactions with a solid surface are directly measured, reporting Wall Friction Angle. Interchangeable smooth and rough steel plates are included, with options for different materials.
Wall Friction Sample Volume: 13.1 mL
ASTM D7891
Compressibility
Pre-conditioned powder is subjected to incrementally increasing normal stresses, monitoring the decrease in sample volume as powder is compressed and reporting % Compressibility under specified normal stress.
Compressibility Sample Volume: 21.2 mL
- Applications
-
Powder materials present unique challenges at all stages, from new formulation development to final product performance. The Powder Rheology Accessory provides insights into real-world behavior to accelerate solutions to processing problems.
Formulation
In development, formulators are often seeking insight into bulk powder behavior. Unexpected processing issues may occur during scale-up, requiring re-formulation and delaying product commercialization.
Powder Rheology Insights
Powder rheology measurements on small lab-scale samples (< 25 mL) demonstrate impacts of formulation changes on processability and performance, avoiding future large-scale problems.
Characterizing effects of additives on powder shear properties
Successful formulations must incorporate the required components while achieving optimal rheological behavior. Adding a new ingredient, even at very low levels, can change bulk properties.
The Powder Shear Cell is sensitive to these changes, demonstrated by measuring sand before and after blending with 5% silicone oil. This small addition dramatically changes behavior under low normal stress, increasing Cohesion and Yield Strength by a factor 10. Major Principal Stress, a measure of the maximum stress under consolidation, is unaffected.
The familiar effect of wetting sand to build a sandcastle is quantified by Powder Shear testing, and broadly applicable to optimizing all powder formulations to meet performance requirements.
Storage
Hoppers and silos must be optimized for powder characteristics to ensure consistent, controlled dispensing and avoid blockages, rat-holing or avalanching.
Powder Rheology Insights
Shear measurements of consolidated powder report parameters used in hopper design: Cohesion, Unconfined Yield Strength, Major Principal Stress, Flow Function and Angle of Internal Friction.
Consolidation of Graphite Anode Powder
The graphite used in battery anode slurries is stored in large hoppers and dispensed as needed. The compressive load on the powder varies with the position inside the hopper, which results in changes in powder properties. Powder shear measurements of graphite under increasing consolidation stress show an increased yield strength, preventing the powder from dispensing from the hopper, and increased cohesion, requiring longer mixing time to distribute uniformly into a slurry.
Stability
Powder morphology is susceptible to changes during mixing, processing or long-term storage. Instabilities alter processing performance and compromise the quality of a final product.
Powder Rheology Insights
Flowability tests detect changes from agglomeration or caking, or segregation of blends which leads to inaccurate dosing in pharmaceuticals, or inconsistent behavior in industrial materials.
SLS Printing Powder Stability
Selective Laser Sintering (SLS) is an additive manufacturing process fusing powdered raw material to form a solid part, leaving the majority of powder unused. Ideal SLS powders can be reclaimed from the printer bed and reused, without compromising performance. Unconfined flowability of a PA-11 SLS powder was measured at elevated temperatures, reaching above glass transition and below melt temperature as required for printing. Upon repeating the measurement, the powder’s Total Flowability Energy shows only a 4% increase, indicating its behavior has not significantly changed and may be reused successfully.
Processing
In production, powder undergoes multiple processes such as feeding, mixing, granulation and milling. Successful processing requires continuous flow at all stages to keep up production.
Powder Rheology Insights
Flow energy measurements predict processability at critical stages of production, in both confined and unconfined conditions across varying flow speeds.
Impact of Lactose Morphology on Flowability During Processing
The choice of excipients used in pharmaceutical powders for solid dose tableting impacts critical process parameters (CPP). Lactose is widely used in pharmaceuticals, but rheological behavior is highly dependent on particle morphology.
Milled lactose exhibits greater resistance to flow due to interlocking of its jagged, irregular particles, unlike the smooth, spherical particles of spray-dried lactose. The Powder Flow Cell was used to measure both materials over a range of speeds, revealing milled lactose’s total flow energy increases at slower rates, predicting insufficient flow rates during dispensing or mold filling. Pre-screening CPPs such as flowability helps to prevent costly manufacturing issues and ensure product quality.
Milled
Spray-Dried
End Use
Food, personal care and consumer products must meet consumers’ expected behavior. Powder caking or agglomeration impacts dispensing, compromising consumer acceptance.
Powder Rheology Insights
Powder rheology directly measures dispensing behavior and evaluates impacts of storage conditions such as consolidate or environmental changes.
- Videos
-
Product Video
Tech Tip
- Resources
-
- App Note: Powder Rheology of Lactose: Impacts of powder morphology on performance of pharmaceutical excipients
- App Note: Powder Rheology of Graphite: Characterization of Natural and Synthetic Graphite for Battery Anode Slurries
- App Note: Epoxy Powder Rheology: Impact of Temperature on Flow and Shear Properties
- App Note: Effect of Moisture and Substrate Material on Wall Friction Angle of Carboxymethyl Cellulose Powder
- App Note: Effect of Moisture on Cohesion Strength of Carboxymethyl Cellulose Powder
- Blog: Powder Rheology for Pharmaceutical Development
- DHR Accessories Brochure
- Explore Discovery Hybrid Rheometers
- Request a Quote