Keywords: Polymers, TGA, thermogravimetric analyzers, thermogravimetric analysis, flame retardency
TA135
Summary
With the rapid penetration of polymeric materials into the building industry, flame retardancy of those materials has become very important. Products containing flame retardant additives must exhibit adequate flame resistance properties without sacrificing appearance or physical properties. Thermogravimetric Analysis (TGA), which provides information about the thermal stability and decomposition rate of materials, is an excellent technique for rapidly comparing the behavior of materials tested with different flame retardants.
Introduction
Flame retardation can be achieved by affecting any or all of three general phases of polymer burning (1-3). These phases and the associated general mechanisms for retardancy provided by the additive component are:
Temperature Rising
Catalysis of the thermal decomposition of the polymer, resulting in a rapid physical separation of the molten polymer mass adjacent to the flame front.
Decomposition
Alteration of the pyrolytic reaction occurring adjacent to the flame front, resulting in either fueling the flame front with a less-flammable gas mixture (thus a lower heat feedback) or producing an inflammable carbonaceous coating.
Ignition
Evolution of gaseous products (e.g., hydrogen halides) which inhibit the combustion process. There are many screening tests used in the United States to determine burning characteristics or burning rate. The most common ones are ASTM methods:
D568-61: Flammability of Plastic Films and Sheets.
D635-63: Flammability of Rigid Plastics.
D757-49: Flammability Test for Self-Extinguishing Plastics.
D1692-57T: Test for Flammability of Plastic Foams and Sheeting.
D1360-58: Test for Fire Retardancy of Paints.
Thermogravimetric Analysis (TGA), which measures weight changes in materials as a function of temperature or time, provides a simple, fast alternative to these ASTM methods. By monitoring the weight loss under different heating conditions, the burning characteristics of different material formulations can be compared.
Experimental
Experimental conditions will vary slightly for different polymers, based upon the thermal stability of the materials. In most cases, the change will be only in the temperature range of the experiment. Before actual sample runs, the TGA should be temperature calibrated. Typical test conditions are:
Sample Size: 25-30 mg.
Program Rate: 10, 5, 2.5 and 1.2 ºC/min.
Initial Temperature: Ambient
Final Temperature: 700 ºC
Atmosphere: Air at 40 mL/min.
Data Sampling Interval: 2 sec/data set (Longer intervals can be used at heating rates less than 10 ºC/min.
Since a variation in moisture content among samples will affect results, test specimens should be dry and handled only with gloves or tweezers. In addition, sample size and surface area should be kept relatively constant. The sample is loaded into a clean, tared, platinum sample pan in the TGA module. It is then heated at the selected heating rates, which should cover an order of magnitude (1 to 10, 2 to 20, etc.) in range. Four runs are required. Rates greater than 20 ºC/min usually should not be used because of the possible lag in sample temperature.
After all heating rate experiments are completed, the stored data files are then analyzed using TGA Kinetics Software (PN 996379-911). The materials evaluated here were polycarbonates with and without flame retardant.
Results
Although polycarbonates are inherently self-extinguishing (4) (a characteristic of their high aromaticity), stringent flame retardance standards still require the use of additives.
The TGA profiles for standard and flame-retarded polycarbonate at 10 ºC/minute are compared in Figure 1. The standard material decomposes at a temperature about 20- 25 ºC higher than the flame-retarded material. This is true regardless of heating rate (1.2 to 10 ºC/min). In other words, the flame-retarded material loses a greater percentage of weight than the standard material (e.g., 48% vs 28%) at a given temperature (e.g., 460 ºC) during the decomposition step. This indicates that the flame-retardant additives in the polycarbonate accelerate the decomposition.
The derivative curves for the two materials (Figure 2) also show characteristic differences. The standard material exhibits two decomposition reactions (A and B) occurring between 350 and 450 ºC. The slower the heating rate, the more distinguishable are the two reactions. Reaction A becomes more prevalent as the heating rate increases. With the flame-retarded material, however, decomposition reaction A proceeds at a much faster rate than reaction B. This is true at all heating rates.
The second stage of weight loss, seen in Figure 1, is oxidation of the carbon skeleton which remains after the initial decomposition. Figure 2 shows that for the flameretarded material the rate of oxidation is consistently about half the rate of decomposition (first stage of weight loss). In the standard material, however, the rate of oxidation is dependent on the heating rate. It is postulated that at slow heating rates (2.5 ºC/min or slower) a more porous carbon skeleton is formed, allowing oxidation to proceed at a higher rate. Faster heating rates apparently produce lessporous carbon skeletons, resulting in slower oxidation.
Repeatability of TGA decomposition studies is excellent, as indicated by the curves in Figure 3, showing the results of three successive runs at a heating rate of 10 ºC/min.
TGA kinetics software is used routinely to estimate the activation energy, pre-exponential factor, and lifetime for materials which decompose upon heating. The kinetic parameters and constants of the two polycarbonates are summarized in Table 1. The results confirm that the retarded polycarbonate decomposes at a lower temperature and a faster rate.
Table 1. Kinetics Results* for Thermal Decomposition of Polycarbonates in Air
Parameter and Constant | Standard | Flame-Retarded |
---|---|---|
Activation Energy | 90.0 KJ/mole | 97.7 KJ/mole |
Log (pre-exp) Factor | 4.62 1/min | 5.35 1/min |
60-min Half-life Temperature | 443.5 ºC | 427.6 ºC |
Lifetime at 300 ºC | 105 min | 100 min |



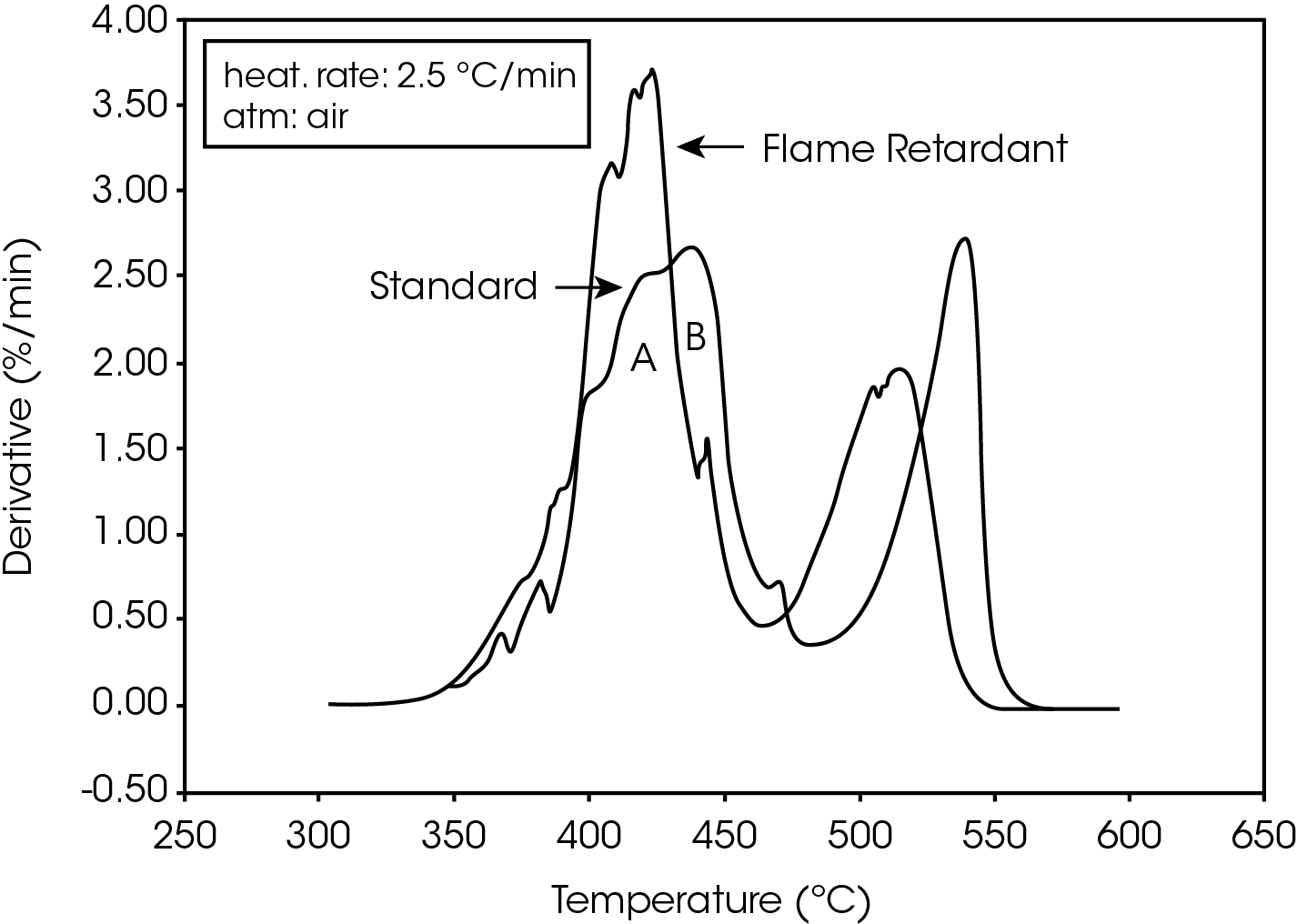
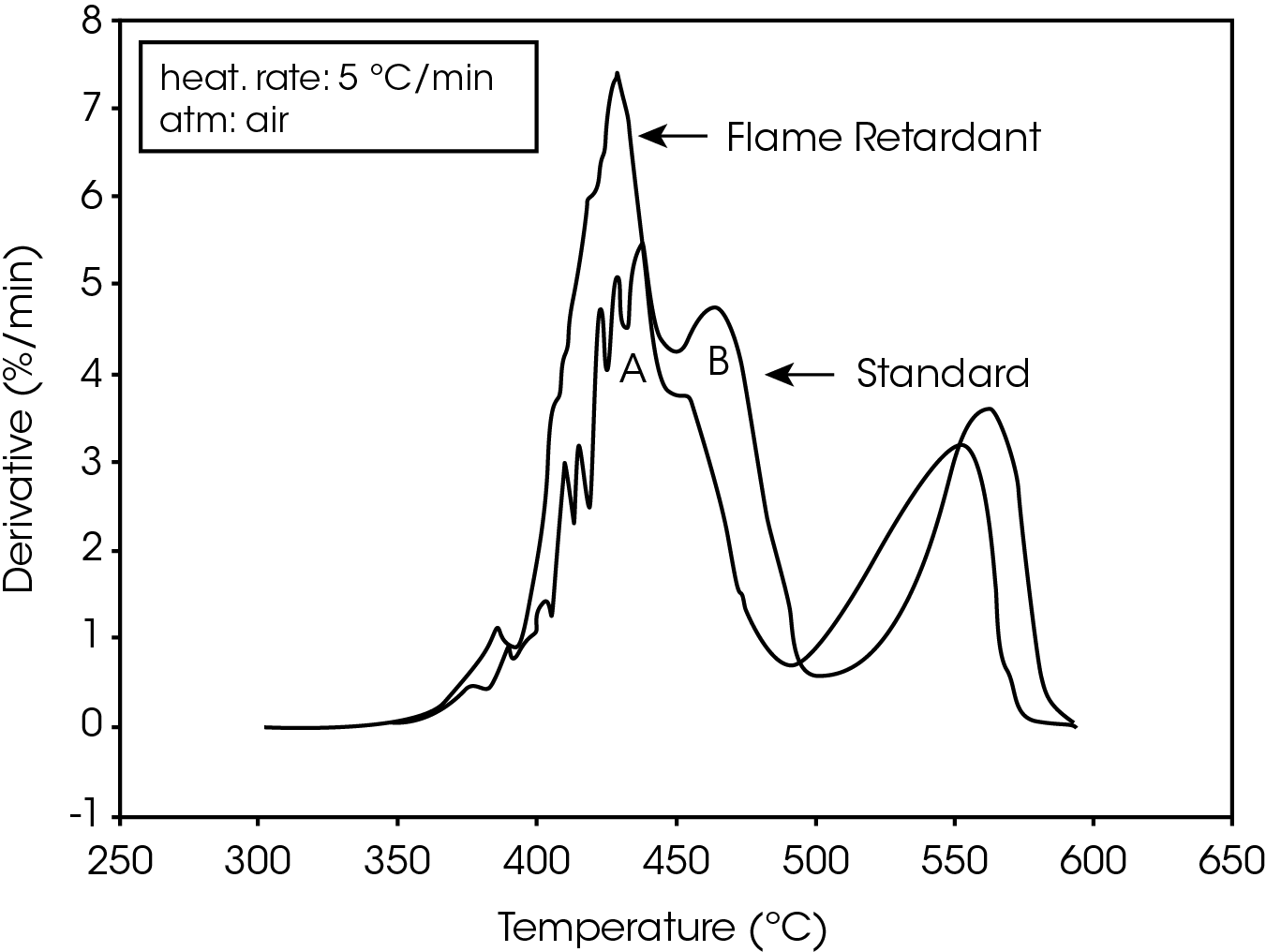

References
- Encyclopedia of Polymer Science & Technology, Vol. 7, 1967, Interscience.
- C.J. Hilado, Flammability Handbook of Plastics, 3rd Ed., 1982, Technomic Publications.
- C.J. Hilado, Fire Prevention and Suppression, Part 2, Vol. 18, 1981, Technomic Publication.
- P. Thiery, Fireproofing, Eng. Ed., 1970, Elsevier Publications.
Click here to download the printable version of this application note.