Keywords: Fuel cell membrane, mechanical property, modulus, coefficient of hygroscopic expansion, humidity control
RH112
Abstract
Fuel cells use thin polymer films as the solid electrolyte. The polymers used in this application must have desired properties such as high proton conductivity, high chemical and thermal stability, and low gas permeability. It is important to have a good understanding of the physical properties of electrolyte membranes, especially under different operating temperature and humidity conditions.
An enhanced relative humidity accessory on TA Instruments Discovery Hybrid Rheometer is introduced for the analysis of fuel cell membrane. The measurement results provide quantitative evaluation to the mechanical properties (modulus, tan delta) of the membrane as a function of both temperature and humidity. In the meantime, the rheometer is also capable of measuring the coefficient of hygroscopic expansion (CHE) of the membrane.
Introduction
PFSA membranes are based on the Short Side Chain (SSC) perfluorosulfonic acid (PFSA) ionomer and have excellent lifetime for fuel cells, electrolyzers, and various electrochemical technologies. PFSA membranes show good proton conductivity, high gap barrier, and are capable of maintaining physical properties within a wide range of operation temperature and humidity. Water management is crucial in fuel cell applications. The PFSA copolymer is reported to have strong water retention within the membrane and performs well in low-humidity electrochemical device operation.
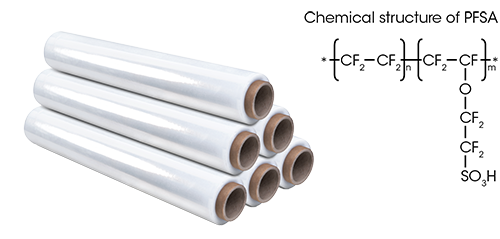
A dynamic mechanical analyzer (DMA) with humidity control capability is an ideal instrument for quantitative evaluation of the physical properties of fuel cell membranes. Figure 1 shows TA Instruments DMA850 with the humidity control accessory attached. This humidity chamber is capable of controlling the relativity humidity from 5 to 95% with a wide range of operating temperatures from 5 °C to 120 °C.
In addition to using a traditional DMA instrument, TA Instruments rotational rheometers (i.e., the Discovery series Hybrid Rheometers) can also perform dynamic mechanical analysis on solid films. In this application note, the TA Discovery Hybrid Rheometer with a Relative Humidity (RH) accessory (shown in figure 2) is used for the mechanical property measurements of a PFSA membrane. This rheometer uses the same humidity generator as that is used on the DMA 850. Its operational specifications are listed in figure 3. The modulus and dampening factor of the PFSA membrane are measured under both temperature and humidity control.
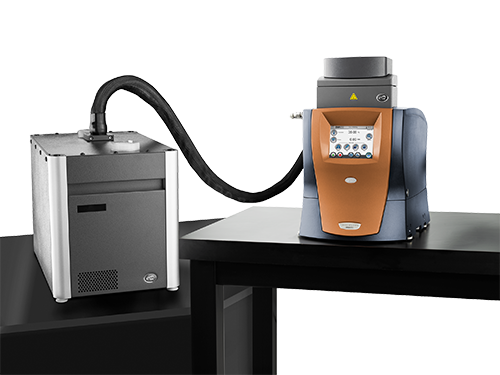
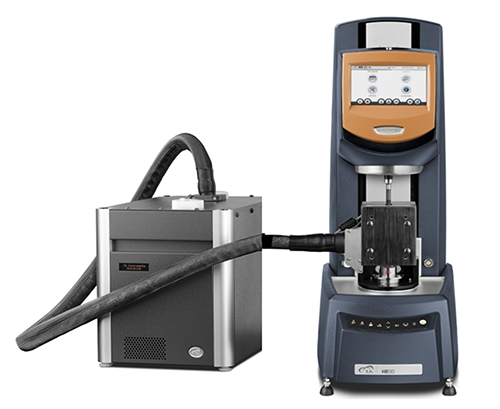
Temperature Range | 5 °C – 120 °C |
Temperature Accuracy | ± 0.5 °C |
Heating/Cooling Rate | Maximum ±1 °C/min over entire range |
Humidity Range | 5% to 95% RH (see chart below) |
Humidity Accuracy | 5 – 90% RH: ±3% RH
90% RH: ±5% RH |
Humidity Ramp Rate | ±2% RH/min (fixed) both increasing and decreasing |
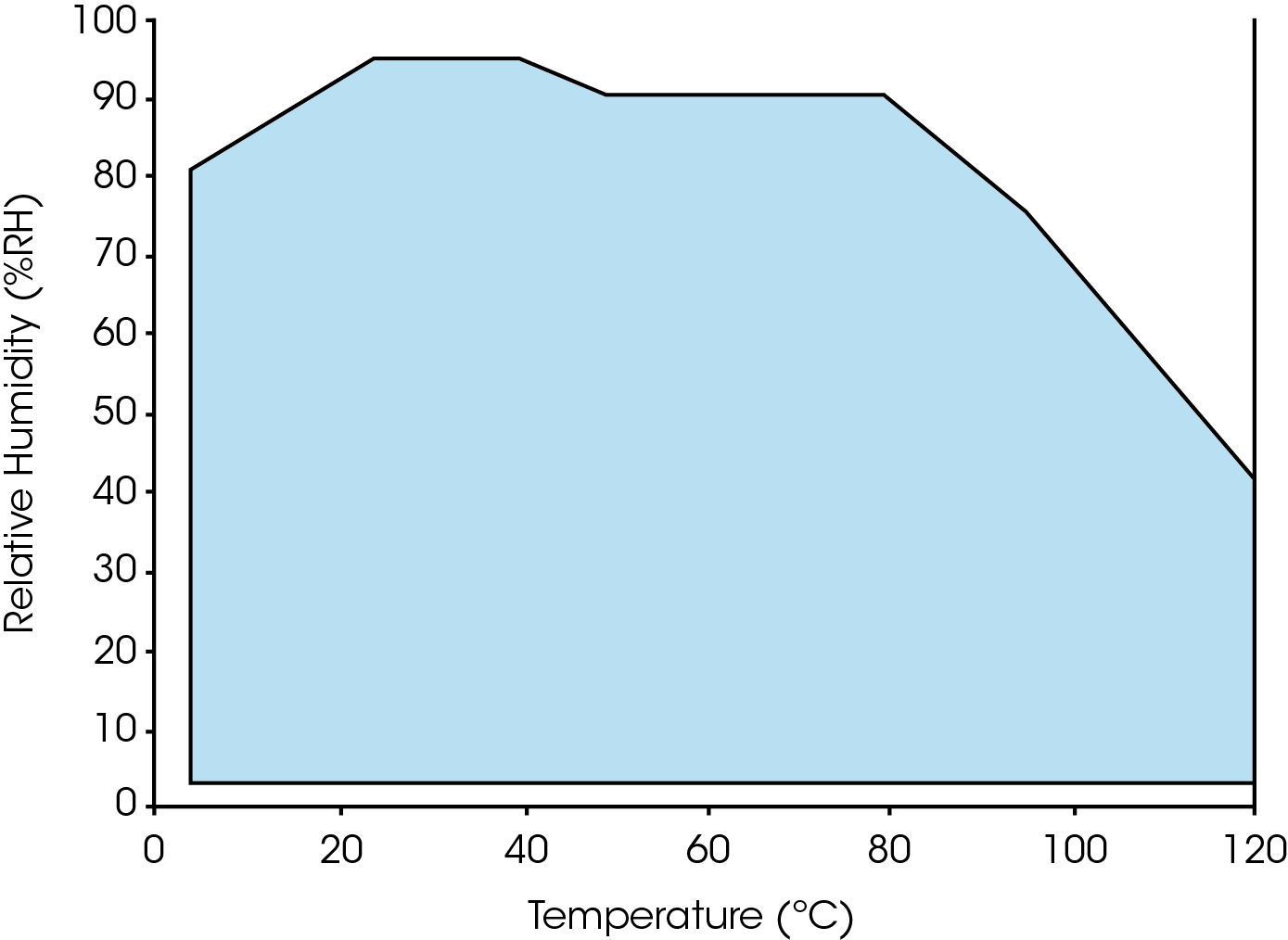
Experimental
Commercial PFSA film was used in this research. The film is transparent with thickness of about 50µm. A TA Instruments Discovery Hybrid Rheometer (HR-30) equipped with the relative humidity chamber was used for the measurements. The PFSA film sample was loaded onto a film tension test geometry as shown in figure 4.
Dynamic mechanical tests were performed in 2 different scenarios with both temperature and humidity control. In the first set of tests, relative humidity was held constant at 30%. The temperature was increased stepwise from 10 °C up to 90 °C. The modulus and dimension change of PFSA film with increasing temperature were monitored as a function of temperature. In the second set of tests, temperature was held constant at 30 °C, 50 °C and at 90 °C. The relative humidity was increased stepwise from 5% up to 90%. In both scenarios, dynamic oscillatory tests were conducted at a frequency of 1 rad/s and with a strain amplitude that is within the linear viscoelastic region of the sample.
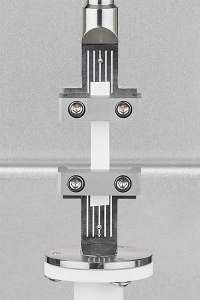
Results and Discussions
Figure 5 shows the results of an iso-hume temperature step test. The relative humidity was held constant at 30%. Dynamic mechanical measurement was performed at a frequency of 1 rad/s with an oscillation amplitude of 0.1%, which is within the linear viscoelastic region of the sample. The measurement results show that sample modulus (E’) is decreasing with increasing temperature. In the meantime, it is observed that the length (i.e. gap) of the film is increasing with temperature due to thermal expansion.
The mechanical properties of PFSA film can also be measured at an isothermal temperature but with a change in relative humidity (shown in figure 6). In this measurement, the test temperature was held constant at 30 °C, and the relativity humidity was increased stepwise from 10% up to 90%. Dynamic testing was conducted at 1 rad/s frequency with an oscillation amplitude set at 0.1%. The measurement results show that the modulus of PFSA film is decreasing with increasing environmental humidity. When water molecules diffuse into the film, it acts as a plasticizer to reduce its stiffness. Therefore, higher humidity results in a lower storage modulus (E’). Also, the length of the film is observed to increase with increasing humidity.
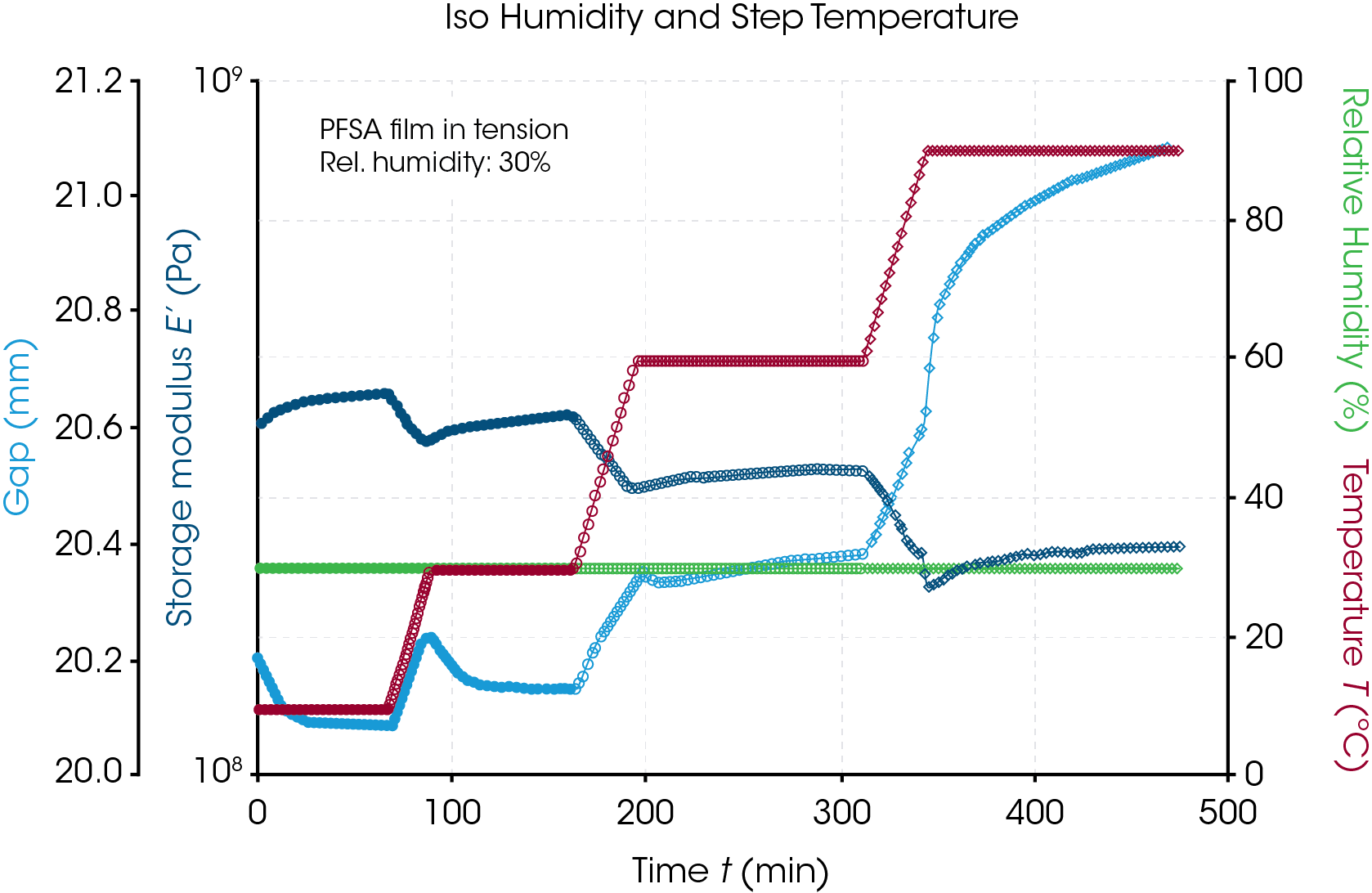
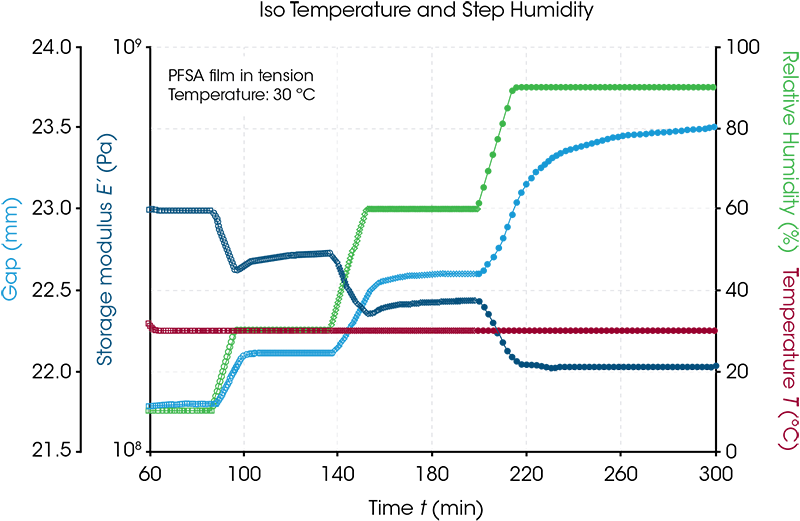
From both the isothermal and iso-hume test results, one can see that this film takes a certain amount of time (usually longer than 1 hour) to reach equilibration at each temperature and humidity step. Figure 7 shows the summary of sample equilibration modulus (E’) change as a function of humidity. The results show that under both test temperatures of 50 °C and 90 °C, E’ decreases with increasing environmental humidity. Also, higher temperature results in lower E’ at the same humidity level.
During the dynamic measurements, the changes of sample dimension (i.e. length) can also be monitored along with the measurement of modulus. Figure 8 shows the measurement results of sample length change (i.e. delta L) as a function of changing humidity at 50 °C and 90 °C. This provides the capability of quantifying the coefficient of hygroscopic expansion (CHE). In general, CHE is described as the change of length per meter per %RH, which correlates to the slop of the delta L over %RH. The results shown in figure 8 indicate that PFSA film has a different CHE at different measurement temperatures.
Another method for CHE measurement is the iso-force humidity step. In this iso-force humidity step test method, a constant low static force (e.g. 0.1 N) is applied to the sample while equilibrating or changing humidity. The benefit of using this iso-force method is that the sample is under a much lower tension force compared to dynamic testing. This minimizes the potential of the sample creeping due to the additional applied oscillation force, so the sample length change can be measured more precisely.
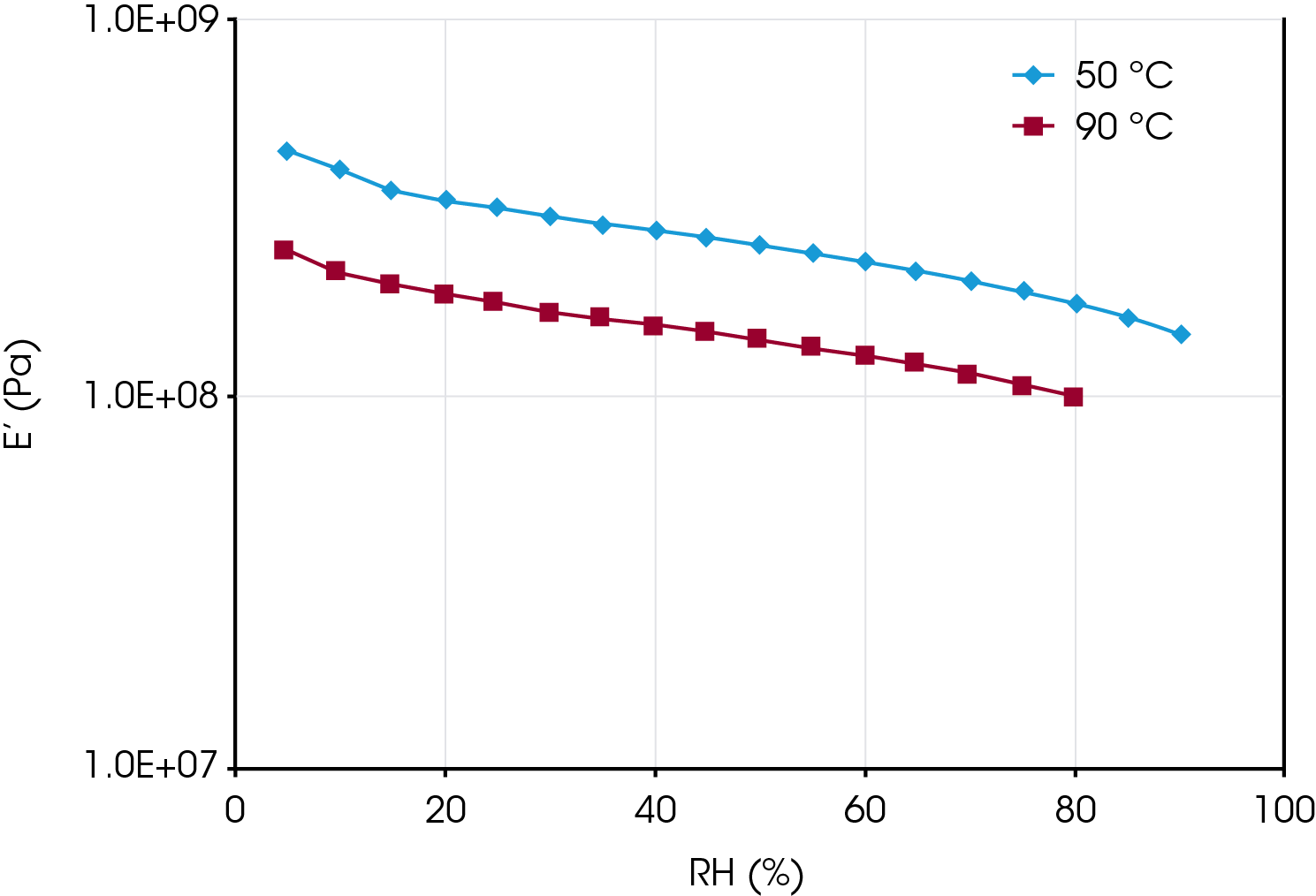
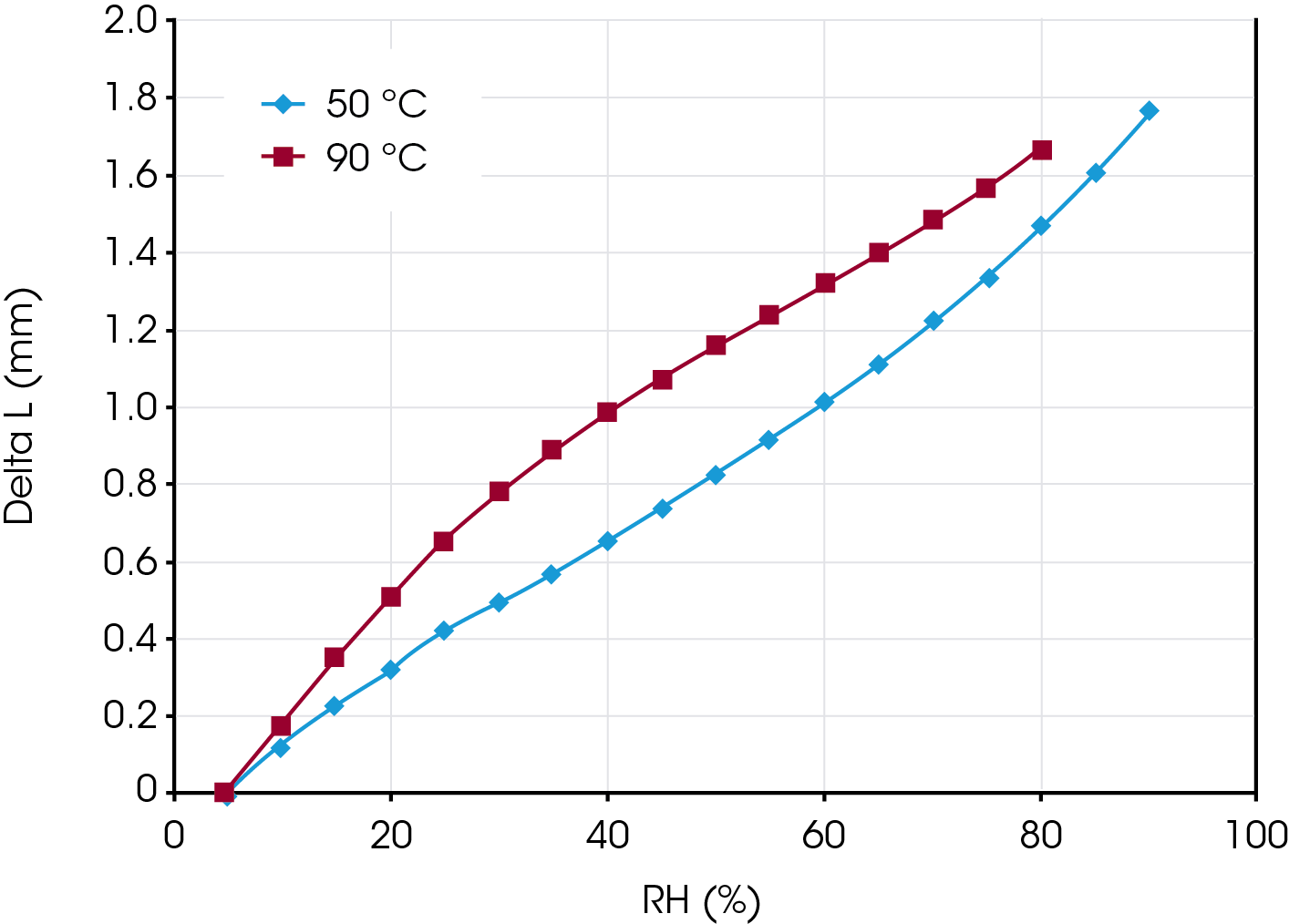
References
- A Baroutaji; JG Carton; M Sajjia; AG Olabi. “Materials in PEM Fuel Cells”. 2016 Elsevier Inc. DOI: 10.1016/B978-0-12-803581-8.04006-6
Acknowledgement
This paper was written by Dr. Tianhong (Terri) Chen, Principal Applications Support Scientist at TA Instruments.
Click here to download the printable version of this application note.