Keywords: High Pressure TGA, catalytic reactions, catalyst weight, nickel catalyst, methanation, steam reforming, catalyst deactivation, coking, Evolved Gas Analysis, EGA, mass spectrometry
TA435
Introduction
TGA is a well-established method to characterize catalysts and determine parameters such as thermal stability or content of volatile compounds. High Pressure TGA allows to investigate the thermal stability at the relevant high operating pressure and apply reactive gases and steam and therefore to use the HP TGA instrument as a catalytic reactor while monitoring the catalyst weight.
This experimental setup allows to exactly identify conditions that induce catalytic reactions and changes in the catalyst material such as activation, oxidation, coking or any other deactivation process that is related to catalyst weight change. At the same time, the reaction yield can be monitored by Evolved Gas Analysis (EGA) using techniques such as online Mass Spectrometry, Gas Chromatography or FTIR. While the reaction atmosphere can consist of most commonly used reactive gases such as hydrogen, methane, ethane, carbon dioxide or carbon monoxide and also steam, the experimental conditions can cover temperatures up to 1100 °C and pressures up to 80 bar.
To demonstrate the versatility of the HP TGA method for catalyst reaction optimization, two examples are shown here: the influence of reaction pressure and temperature on the reaction yield of a methanation reaction and the reversible deactivation by coking of a catalyst in a steam reforming reaction as the result of various steam to methane ratios in the reaction atmosphere.
Experimental
The methanation reaction was investigated in a Discovery HP TGA 75, while a HP TGA 7500 instrument was used for the steam reforming reaction. Both High Pressure TGA instruments are based on a patented magnetic levitation system1,2 that allows the weight measurement of the sample in the reaction atmosphere. All sensitive electronics parts of the balance are located outside of the reaction chamber and are temperature controlled for best weight signal stability. While the HP-TGA 75 has one single mass flow controller for reaction gases and three gas connections that allow switching the reaction gas during the experiment, the HP TGA 7500 shown in figure 1 is equipped with three independent mass flow controllers for reaction gases and an integrated steam generator for the flexible generation of varying gas, gas mixture or gas/steam atmospheres. For both reactions, a Pfeiffer Thermostar GSD 300 online mass spectrometer was used for EGA analysis.

Methanation of Carbon Dioxide is a process to generate methane by reduction with hydrogen following the reaction equation CO2 + 4 H2 ↔ CH4 + 2 H20. This reaction has a high commercial relevance as a key process in the power-to-gas (P2G) concept3. In this study, 21 mg of a catalyst precursor consisting of nickel oxide nanoparticles on alumina carrier material was used as sample in the HP-TGA 75 instrument4. Alumina supported nickel catalysts are today the most commonly used catalysts in methanation reactions5,6. The activation of this catalyst precursor material was achieved by drying at 500 °C in inert argon atmosphere followed by switching to hydrogen for reduction while the conditions of 500 °C, 1.5 bar and 20 ml/min gas flow rate remained unchanged. This in situ activation procedure was then followed by a series of catalytic experiments with a gas mixture of 2% CO2, 8% H2 and 90% argon obtained from a premixed gas cylinder by Linde Gas. With this setup, the reaction yield was monitored at various temperatures between 275 and 350 °C and at 1.5, 15 and 30 bar using the online MS.
Steam Reforming of natural gas is the process that produces most of the world’s hydrogen following the reaction CH4 + 2 H20 ↔ CO2 + 4 H2. An HP TGA 7500 instrument was used for steam reforming experiments with a commercial nickel catalyst obtained from Süd-Chemie (Munich, Germany). This catalyst material was activated in a similar way as described above using conditions of 500 °C, 5 bar and a gas flowrate of 50 ml/min of a reducing gas mixture containing 8% hydrogen in argon. Following this activation, various steam reforming experiments were performed with this catalyst at 700 °C and 10 bar pressure by applying various flowrates of methane and steam. The intention was to change the water/methane ratio to identify the conditions that lead to coking of the catalyst.
Results and Discussion
The main benefit of performing catalytic gas phase reactions on solid catalysts in a TGA instrument is to measure the catalyst weight permanently during the experiment in order to continuously and quantitatively detect catalyst activation or deactivation processes as they occur.
Methanation Reaction
In the methanation example, the pre-catalyst was dried and then activated at 500 °C and 1.5 bar in hydrogen. After switching to hydrogen, about 180 minutes were required to reach a stable weight signal that indicated the complete activation (see figure 2). Prior to these experiments, the NiO content was determined by ICP-MS as 9% (wt) in the dried material. From the 1.76% activation weight loss due to reduction with hydrogen found in the TGA measurement, a 97% conversion rate of the NiO to the active metallic Nickel could be calculated.
Subsequently, this activated catalyst was used for the methanation reaction applying a reaction gas mixture with 8% hydrogen and 2% carbon dioxide in argon at various temperatures in the range of 275–350 °C. Gas flowrate was 20 ml/min at 1.5 bar. The online MS was applied to monitor the carbon dioxide, water and methane concentrations. CO2 and water could be detected easily by their molecular ions of m/z 44 and 18 while the ion trace of 15 m/z was used to monitor the generation of methane, since the molecular ion of methane m/z 16 is also present in the CO2 mass spectrum. The results of this measurement are shown in figure 3: as expected, the decrease of the CO2 concentration goes along with the increase of the reaction products methane and water and the overall conversion rate of the reaction is directly related to the reaction temperature. As the temperature is changing in 25 °C steps up or down, concentrations of reactand and products correlate exactly. During this process, the catalyst weight remains stable and unchanged as it is required in a catalytic reaction. Catalyst weight change would indicate a deactivation process, for example by oxidation or other undesired side reaction and would most likely go along with a loss of catalytic activity.
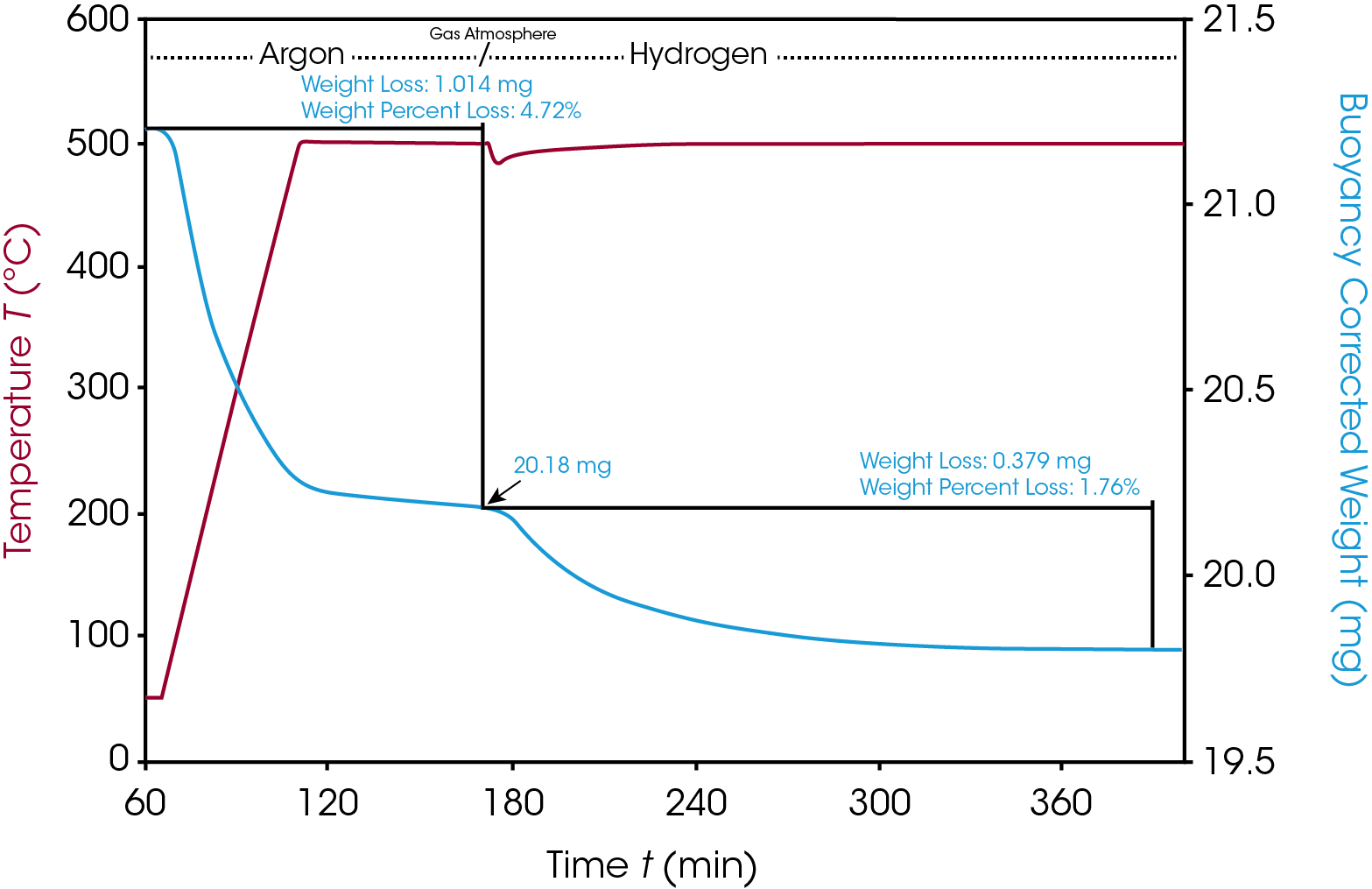
In the next series of experiments, the influence of pressure was investigated by repeating the measurement at 15 bar and 30 bar with a gas flowrate of 100 ml/min. By comparing the MS data, it can be shown that in general, increasing the pressure is leading to a higher reaction yield and that the influence of temperature is similar, but more pronounced at 15 and 30 bar compared with the measurement at 1.5 bar. Figure 4 is showing the comparison between all three pressures using only the mass trace m/z 15 that indicates the methane concentration which is the important product of the methanation reaction. No catalyst weight change was detected at any pressure which is indicating that no deactivation or side reaction occured.


Steam Reforming Reaction
To study a steam reforming reaction, a commercial nickel catalyst by Süd-Chemie was used. The pelletized material was dried and activated at 500 °C with a reaction gas mixture of 8% hydrogen in argon at a pressure of 5 bar and a flowrate of 50 ml/min. Under these conditions, 240 minutes were required to complete the activation of the catalyst and to reach a stable weight signal. The conversion rate to the active metal catalyst could not be calculated this time because the NiO content of the catalyst was not known.
After activation, the steam reforming reaction was performed at 700 °C and 10 bar. The reaction atmosphere consisted of 45 ml/min argon, 5 ml/min methane and 20 ml/min of steam so that the resulting steam to methane ratio was 4:1. Under these conditions, hydrogen generation was detected by online MS while the catalyst weight remained constant. To investigate the influence of the water to methane ratio on the catalyst weight, the ratio was changed to 1:1 and later to 1:2 by adjusting methane and steam flowrates. As can be seen in figure 5, a 1:1 ratio leaves the catalyst weight at the constant value of 26.2 mg, but when the ratio is changed to 1:2, the excess of methane immediately leads to a linear weight increase of 0.1 mg/min (~0.3 %(wt)/min). This weight increase is caused by the formation of coke (elemental carbon) on the catalyst. This coking process can be reversed and the catalyst regenerated by switching off the methane flow: steam reacts with the coke and this is documented by a fast weight loss rate of – 0.28 mg/min (~0.9 %(wt)/min): in only 15 minutes, more than 4 mg of coke are removed from the catalyst surface.
While these data clearly show the suitability of the HP TGA method to study activation and deactivation process of solid catalysts, care should be taken to avoid too extreme conditions. Figure 6 shows that coking can lead to impressive amounts of carbon formed that have the potential to contaminate the instrument. However, contamination with carbon is not a severe problem for the HP TGA instrument, it is possible to remove carbon easily, either mechanically or by oxidation with air.


Conclusion
In the data shown here, it could be demonstrated that High Pressure TGA is a suitable method to study catalyst performance and to optimize catalytic reaction conditions. Gas phase reactions such as methanation, steam reforming and many other technically and commercially important reactions can be performed in a HP-TGA instrument at technically relevant pressure, temperature and gas or vapor composition conditions. The reaction turnover can be monitored by EGA analysis with mass spectrometry, FTIR or other suitable methods and the catalyst weight signal provides valuable online data on activation and deactivation processes.
In these experiments, the weight change data of the catalyst in the activation process by reduction with hydrogen could be used to measure the conversion rate of the catalytic active metal content (in this case Nickel) to the active state. In the methanation experiment, online MS data clearly documented the influence of temperature and pressure on the reaction yield. The steam reforming experiment then proved the potential to use the catalyst weight signal for the detection of catalyst deactivation by coking caused by inappropriate reaction conditions. Since most deactivation processes including oxidation, decomposition or coking are related to a weight change, the HP-TGA method can be used effectively to monitor catalytic reactions and to optimize reaction conditions.
References
- TA Instruments, Brochure High Pressure Thermogravimetric Analyzers, 2021
- European Patent: 1958323, US Patent: 2009/0 160.279 A1
- K. F. Kalz, R. Kraehnert, M. Dvoyashkin, R. Dittmeyer, R. Gläser, U. Krewer, K. Reuter, J.-D. Grunwaldt, Future challenges in heterogenous catalysis: understanding catalysis under dynamic reaction conditions, ChemCatChem 2017, 9, 17-29.
- T. Paschke, L. Schwensow, W. Kleist, 54. Jahrestreffen Deutscher Katalytiker 2021, Application of High Pressure Thermogravimetry as a perfect tool to study catalyst performance
- J.M. Thomas, W.J. Thomas, Principles and practice of heterogenous catalysis, p. 540ff, VCH Weinheim 2008
- B. Mutz, M. Belimov, W. Wang, P. Sprenger, M.-A. Serrer, P. Pfeifer, W. Kleist, J.-D. Grunwaldt, Potential of an alumina-supported Ni3Fe catalyst in the methanation of CO2: impact of alloy formation on activity and stability. ACS Catal. 2017, 7, 6802–6814
Acknowledgement
This work was performed by Thomas Paschke at the TA Instruments Application Lab in Bochum, Germany and was supported by Leif Schwensow and Wolfgang Kleist of the Laboratory of Industrial Chemistry at the RUB (Ruhr Universität Bochum) and by Volker Hagen of Rubokat GmbH Bochum.
Click here to download the printable version of this application note.