Keywords: direct reduction, iron ore, hydrogen, steel industry, reducing CO2 emissions, high pressure TGA
TA487
Abstract
The steel industry is replacing fossil fuels with hydrogen to reduce CO2 emissions. In a DynTHERM™ High Pressure TGA, the direct reduction of complete iron ore pellets in 100% hydrogen atmosphere can be studied under various temperature and pressure conditions to understand and optimize the process. These data can be used to dramatically reduce CO2 emissions and provide sustainable production methods for the world metal supply of the future.
Introduction
The production of metals is related to 30% of the industrial CO2 emissions and 8% of the global energy consumption [1]. While different strategies are discussed to improve the sustainability of metals, a key approach is to replace the fossil reducing agents (such as coal) with hydrogen in the production of steel from iron oxides. Therefore, a multitude of projects are underway in the steel industry to implement direct reduction of iron ores with hydrogen [1,2]. While direct reduction with hydrogen has the potential to almost eliminate CO2 emissions in steel production, the process depends on a high number of variables such as temperature, pressure, gas composition, and ore properties. So far, the prediction of process kinetics is not possible because of its complexity [3].
Generally, the direct reduction process with hydrogen follows the reaction
Fe2O3 + 3 H2 → 2 Fe + 3 H2O
but during this process, the iron oxides Fe3O4 and FeO are formed as intermediates. Commonly, Fe2O3 or hematite iron ore is used in pelletized form to produce iron and the kinetics are largely driven by defects in the pellet structure formed by the gaseous reaction with hydrogen. For a better understanding, current research is combining simulation approaches with analytical X-ray spectroscopy, X-ray diffraction, and electron microscopy technologies [3].
A promising approach is the use of High Pressure TGA to perform the hydrogen reduction reaction directly under realistic process conditions including gas atmosphere, pressure, and temperature in a TGA instrument. This way, the reduction process can be monitored continuously as well as weight change of the iron ore pellet. In this study, complete hematite iron ore pellets were analyzed in pure hydrogen atmosphere in a DynTHERM HP TGA instrument at temperatures of 700 and 900 °C and pressures up to 50 bar.
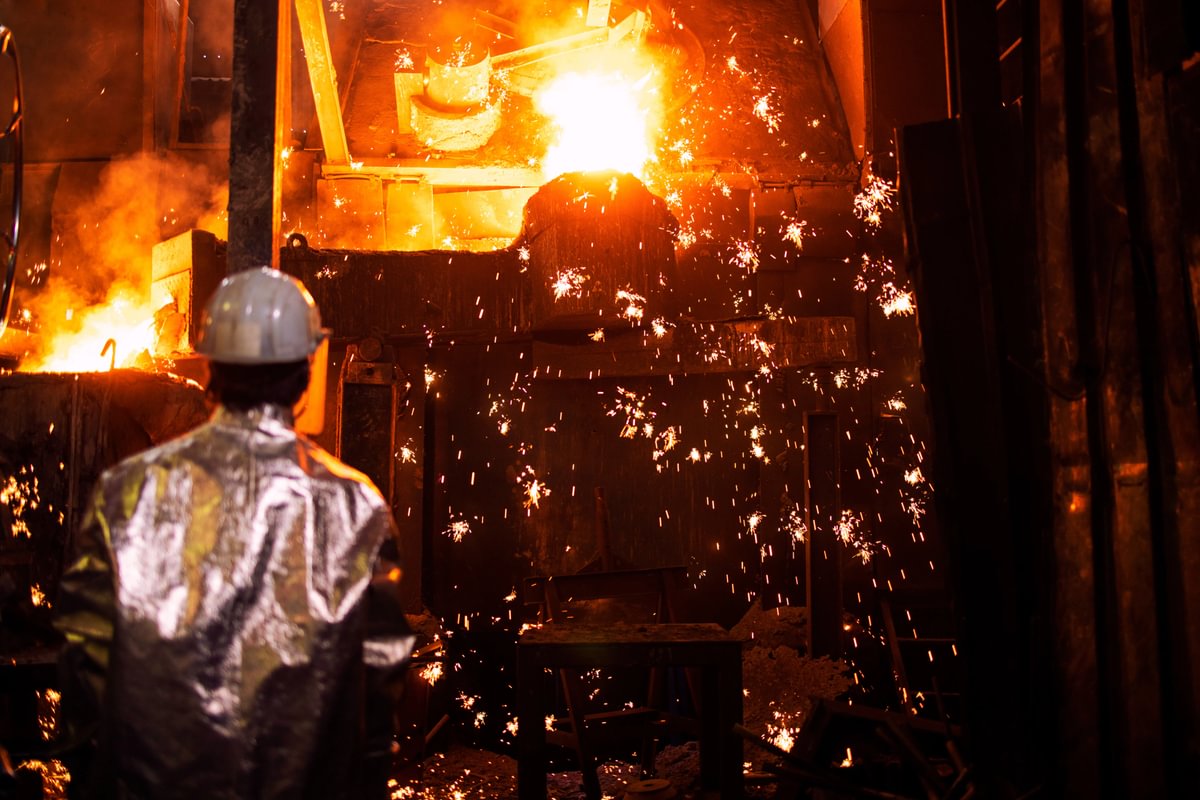
Experimental
A DynTHERM 1500-50 HP-G+V instrument with two standard reaction gas lines and steam option was used for these experiments. To obtain a direct exposure of the sample pellets to the reaction gas atmosphere, a custom pellet holder was produced from platinum wire material as shown in Figure 2.
In this setup, iron ore pellets of 2–3.5 g weight could be reduced. The experimental conditions were 200 ml/min argon gas flowrate and a heating rate of 10 °C/min to 700 ° or 900 °C. At these reaction temperatures, the gas supply was switched to 200 ml/min hydrogen for an isothermal step of 120 minutes. For cooling down the furnace, the gas supply was switched to argon again.
In experiments at elevated pressure, the gas flow rates were increased to 500 ml/min NTP to partly compensate for the loss of linear velocity that is a result of pressure increase. Performing TGA experiments at higher pressures requires data correction to eliminate buoyancy effects; this was achieved by blank run subtraction with data obtained by performing measurements under identical conditions without sample.
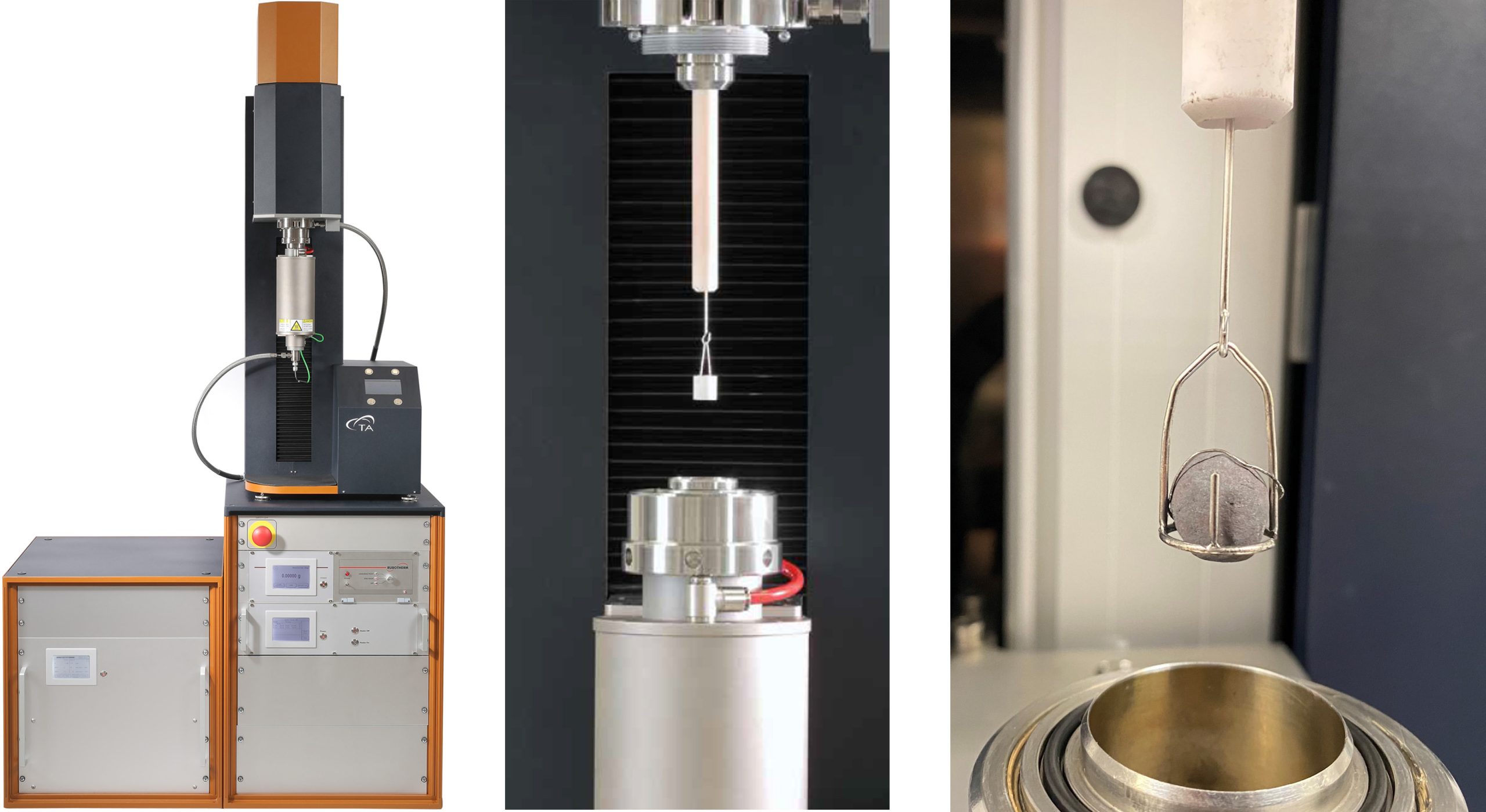
Results and Discussion
At 700 °C and ambient pressure, almost 120 minutes are required to achieve complete reduction to iron. Figure 3 shows that increasing the temperature to 900 °C or raising the pressure from ambient pressure to 10 bar dramatically increase the kinetics so that complete conversion can be achieved faster.
The theoretical weight loss of the reduction of iron (III) oxide to iron is 30.1%. In all three experiments, the final weight loss was 28.5 – 28.9%, indicating that complete reduction of the Fe2O3 material to iron was achieved. As seen in Figure 4, the DynTHERM instrument allows you to study the influence of pressure up to 50 bar.
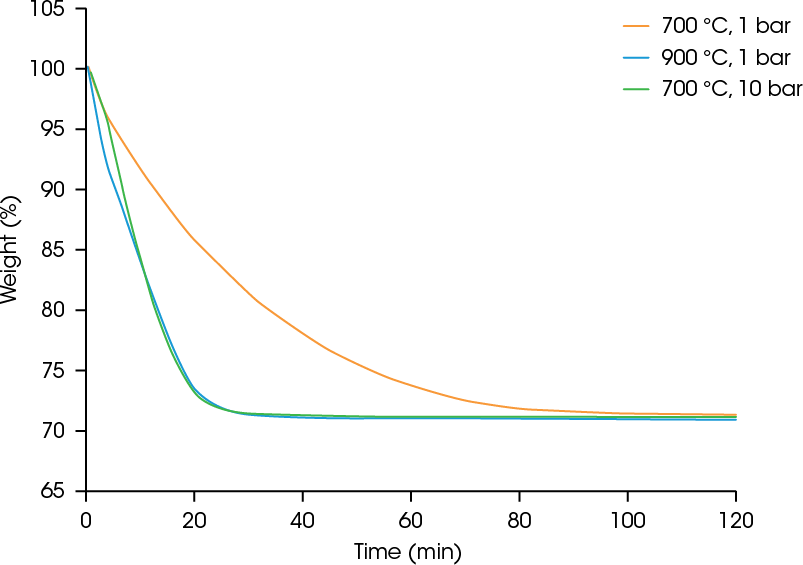
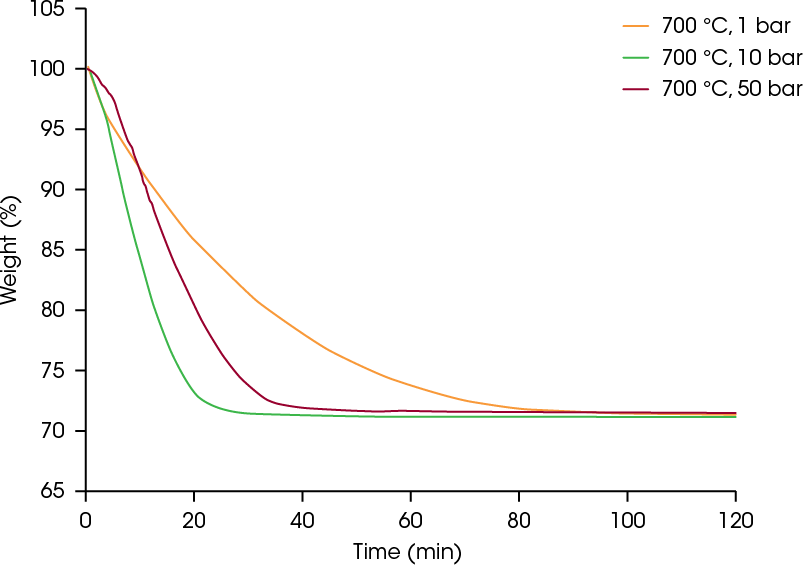
An advantage of the method is that after reaction, the iron pellet samples can be recovered for further analysis. A simple visual comparison of the pellet before and after reduction as shown in Figure 5 of the 1 bar reaction shows that reduction process changed the structure of the pellet, causing visible cracks in the surface.
As it is known that the kinetics of the hydrogen reduction process are driven by defects in the microstructure of the feedstock, the next step is to analyze the reacted pellets with various analytical techniques. Consequently, Figure 6 shows two SEM (scanning electron microscope) images of iron ore pellets reduced in hydrogen atmosphere in the DynTHERM instrument at 1 and 50 bar with quite different microstructure [4].
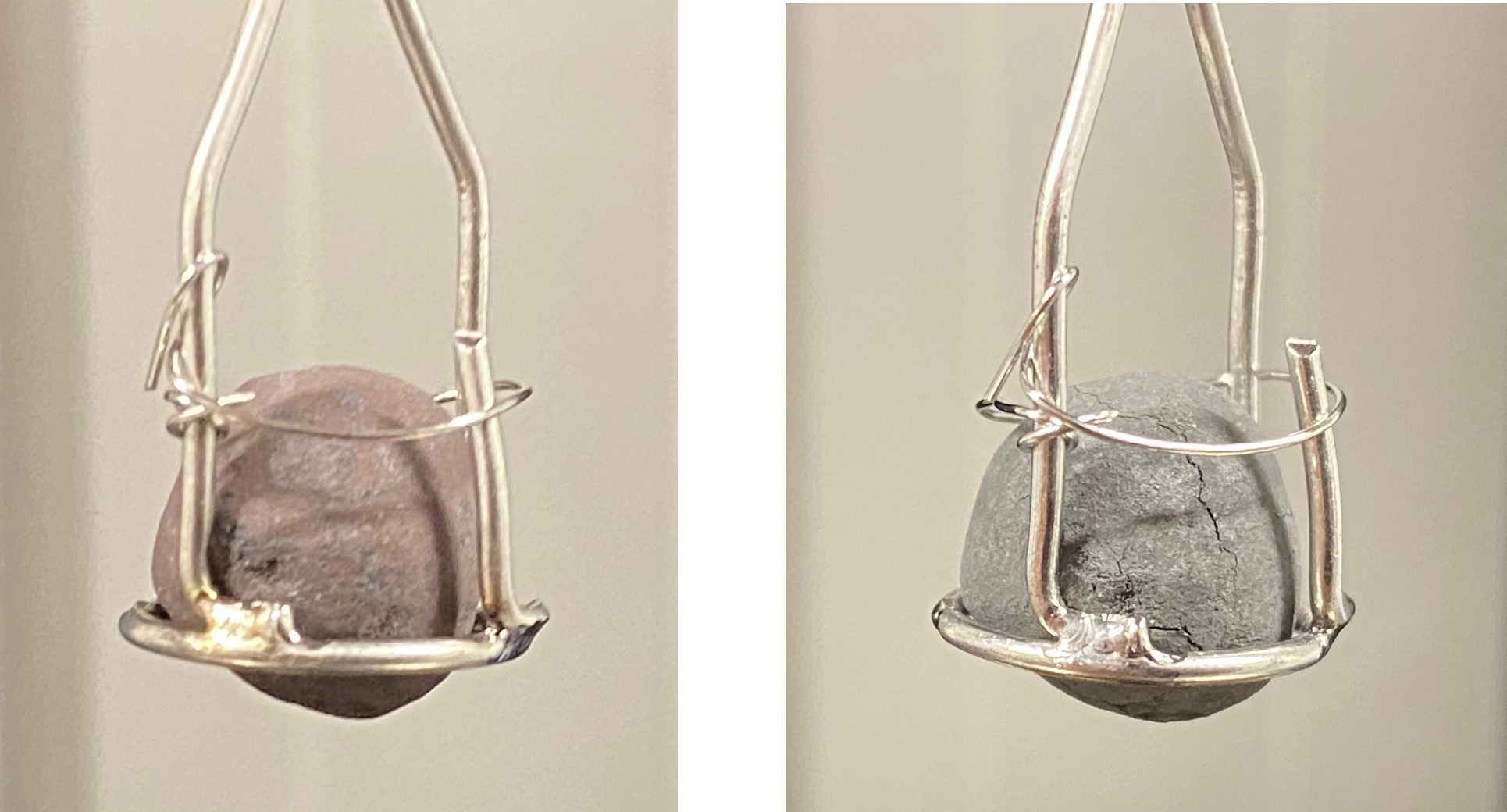
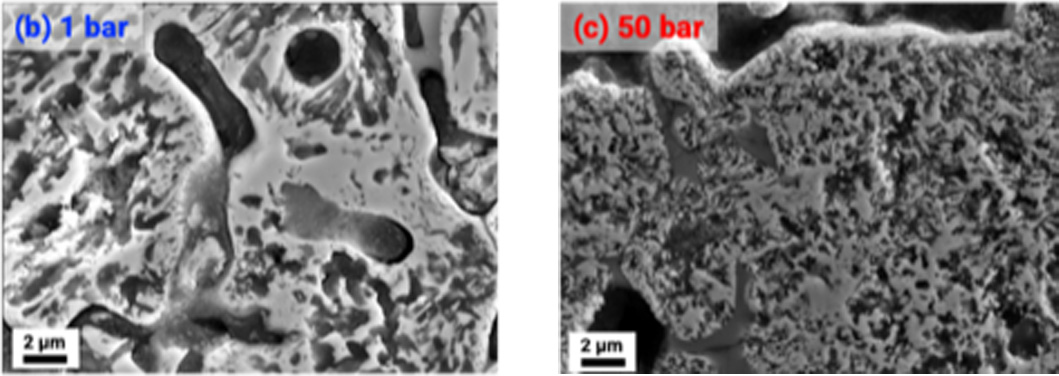
Of course, it is also possible to reduce Fe2O3 powder using a ceramic crucible; in this case, 500 °C are sufficient to achieve complete conversion. The TGA diagram obtained at 1 bar is shown in Figure 7 and data analysis reveals a weight loss of 4.2% of volatile content during the temperature ramp before the reaction atmosphere was switched to Gas 2 / hydrogen at 500 °C to start the reduction.
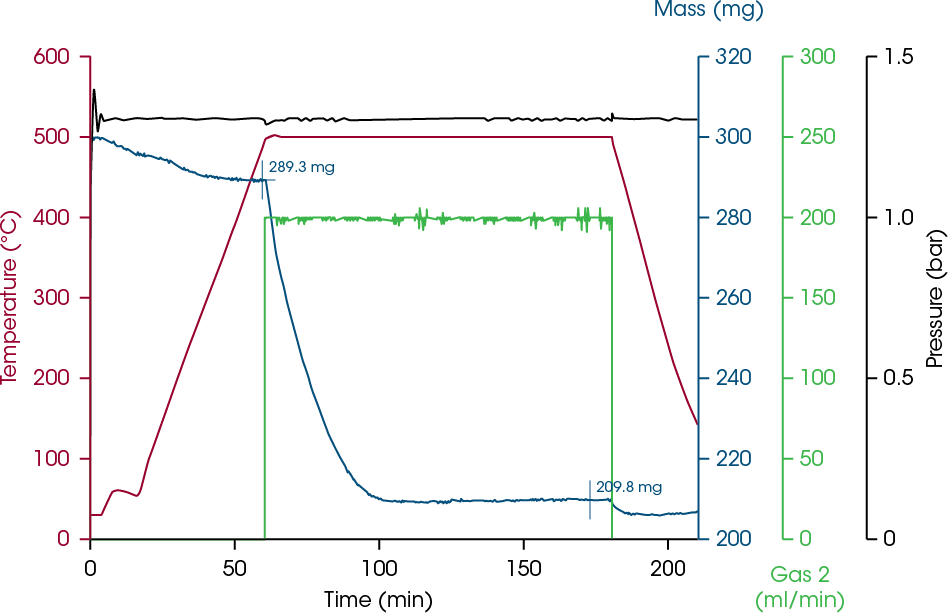
Conclusions
It could be shown that the DynTHERM High Pressure TGA instrument is a very valuable tool to study the direct reduction of iron ore in hydrogen. Complete pellets can be analyzed to improve the understanding of the reaction parameters that drive the kinetics of the process.
Besides the reduction reactions in pure hydrogen atmosphere shown here, the DynTHERM instrument can use complex gas mixtures including nitrogen, other reactive gases such as methane, carbon dioxide, or carbon monoxide, and even steam.
The evolving gas atmosphere can be analyzed, as well, to gain further insights; online mass spectrometry or FTIR would be the most common analytical techniques for this task.
References
- Raabe D, Tasan C.C. and Olivetti E.A. “Strategies for improving the sustainability of structured metals”, Nature 2019, 575: 64-74.
- Pattison F. and Mirgaux O. “Hydrogen Ironmaking: How It works”, Metals 2020, 10, 922
- Ma Y., Souza Filho I.R., Bai Y. Schenk J., Patisson F., Beck A., van Bokhoven J.A., Willinger M.G., Li K., Xie D., Ponge D., Zaefferer S., Gault B., Mianroodi J.R. and Raabe D. “Hierarchical nature of hydrogen-based direct reduction of iron oxides”, Scripta Materialia 2022, 213, 114571
- Özgün Ö., Dirba I., Gutfleisch O.,Ma Y. and Raabe D. “Green Ironmaking at Higher H2 Pressure: Reduction Kinetics and Microstructure Formation During Hydrogen‑Based Direct Reduction of Hematite Pellets”, Journal of Sustainable Metallurgy 2024, https://doi.org/10.1007/s40831-024-00877-4
Acknowledgments
This paper was written by Dr. Thomas Paschke.
Iron ore pellets, SEM images, and scientific advice were kindly provided by Dr. Yan Ma, Max Planck Institut für Eisenforschung in Düsseldorf, Germany.
DynTHERM is a trademark of Waters Technologies Corporation.
For more information or to request a product quote, please visit www.tainstruments.com to locate your local sales office information.
Click here to download the printable version of this application note.