Keywords: DSC, TMA, TGA, DMA, thermal analysis, battery, battery separator, lithium-ion battery, polyolefins
TA462
Abstract
Battery separators are critical to the performance and safety of lithium-ion batteries, allowing ion exchange while acting as a physical barrier between electrodes. Coatings can be applied to the porous polymer films to improve properties and performance. This application note utilizes thermal analysis techniques to characterize uncoated and coated separators. Thermogravimetric analysis (TGA) is used to determine stability, decomposition, and polymer content of the separators. The melting temperature and crystallinity are found using differential scanning calorimetry (DSC). Thermomechanical analysis (TMA) is used to determine shrinkage and rupture temperatures by measuring dimensional change as a function of temperature. Finally, viscoelastic experiments are performed using dynamic mechanical analysis (DMA) to measure the temperature dependent mechanical response.
Introduction
Separators are critical components of lithium-ion batteries, acting as a barrier between the cathode and anode while enabling the exchange of ions. The properties of these porous polymer membranes impact the safety, energy capacity, and life cycle of the battery. In addition to being electrically insulating, they must have good thermal, chemical, and mechanical stability [1]. Common separator materials include polyolefins such as polyethylene and polypropylene, often in layered structures to enhance performance. Coating the membrane with an inorganic material can further improve mechanical and thermal properties, although care must be taken to ensure the coating porosity allows ionic conductivity. After the separator is coated, it is important to confirm the properties of the separator are in line with expectations.
A key property of battery separators is melt integrity, which is the mechanical robustness above the melting point. Above a certain temperature, melting will cause the pores to close, and the separator becomes an insulating layer that stops ion transport or shutdown [2]. It is essential that the separator not mechanically fail, or rupture, to ensure the electrodes remain out of contact, otherwise the battery may experience thermal runaway. The melt integrity of a battery separator can be characterized with a thermomechanical analyzer (TMA). Other important separator properties include melting point, decomposition temperature, crystallinity, and mechanical properties such as storage modulus and Young’s modulus.
This note applies the workflow outlined in TA457 [3] to characterize coated and uncoated separators. In addition to TMA, differential scanning calorimetry (DSC), thermogravimetric analysis (TGA), and dynamic mechanical analysis (DMA) will be utilized.
Experimental
Polyethylene (PE) uncoated and ceramic coated separators were kindly provided by SpectraPower. Uncoated samples were 0.01 mm thick and coated samples were 0.02 mm thick.
TGA can investigate the thermal stability and composition of battery separators. For this work, TA Instruments Discovery TGA 5500 was used. Coated and uncoated samples were cut to fit the TGA platinum pan and heated to 1000 °C at a rate of 10 °C/min under nitrogen purge. The melt points of the separators were characterized with Discovery 2500 DSC, using heat-cool-heat experiments. Under nitrogen purge, the samples were heated from -50 °C to 250 °C at a rate of 10 °C/min.
TMA measures dimensional change of a film while under constant load during a linear temperature ramp. Prior to the point of rupture, a degree of shrinkage will be observed in the sample. Melt integrity of the coated and uncoated separators was determined using a TA Instruments Discovery TMA 450. Samples 8 mm long and 2.6 mm wide were held in tension at a constant force of 0.01 N using the Film/Fiber Probe. After equilibrating at 5 °C, samples were ramped at 2 °C/min until rupture. Rupture was determined to occur at the minimum point after the onset of shrinkage and measurements were repeated three times, with new samples for each experiment. The onset of shrinkage and temperature of rupture were recorded for coated and uncoated samples.
The temperature dependent mechanical response of the separators was measured using dynamic mechanical analysis (DMA). Rectangular samples 5 mm long and 5.6 mm wide were tested on a TA Instruments Discovery DMA 850 using large strain, small strain, and temperature ramps. All samples were prepared from the machined direction of the starting films. For the large strain ramp, the separators were strained at 35 °C and 60 °C, similar to NASA/TM—2010-216099 [4]. A preload force of 0.001 N was applied and the temperature was equilibrated for five minutes before applying a strain ramp of 5%/min. Samples were strained from 0.5% to 450%, with measurements performed in triplicate. Small strain ramp experiments were performed at 35 °C to obtain the Young’s modulus. Samples were preloaded with 0.01 N, equilibrated at temperature for five minutes, then ramped at 1%/min. Strain values up to 0.05% were used to calculate the Young’s modulus. Temperature ramps were performed to determine the storage modulus and loss modulus of the separators. Samples were kept taut using an initial preload force of 0.1 N and a force track value of 150%. A strain of 0.1% was applied at a frequency of 1 Hz from -10 °C to 120 °C at 3 °C/min.
Results and Discussion
Thermogravimetric Analysis (TGA)
TGA results are shown in Figure 1. The derivative weight loss is related to the decomposition processes and is used to determine the composition or percentage of individual compounds within the sample. The uncoated polyethylene separator has a decomposition peak temperature at 465.1 °C. At this same temperature, the coated separator experiences a mass loss of 37.2%, indicating that this is the composition of polyethylene. Next, at 496.5 °C, the coating binder decomposes, and the remaining material is the inorganic coating. A breakdown of the separator composition is shown in Table 1.
Table 1. Composition of separators as determined by TGA
Separator | Composition |
Uncoated | polyethylene |
Coated | 37.2% polyethylene 5.8% binder 55.1% inorganic coating |
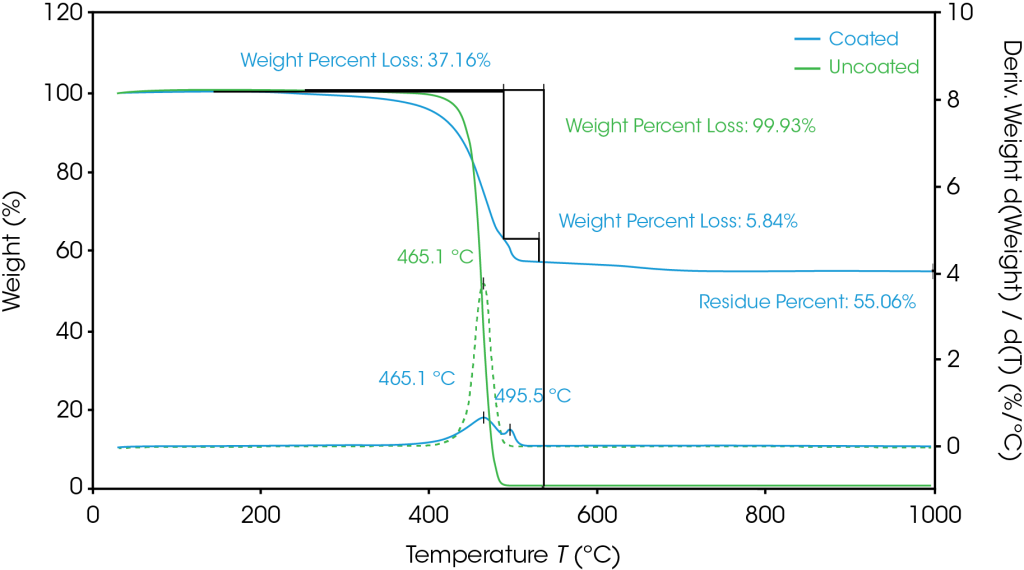
Differential Scanning Calorimetry
DSC was used to analyze the melting temperature, impact on melting, and further understand properties of the polymer content determined from the TGA results. Figure 2 shows that the melting of the polyethylene separator occurs at 135 °C. Melting enthalpy can be used to determine the degree of crystallinity of a polymer [5] [6]. For the uncoated separator, the melting enthalpy was 226 J/g. As determined by TGA, the polyethylene content of the coated separator is 37.2%, allowing Equation 1 to be used to determine the melting enthalpy of the polyethylene, ΔHf(PE).

Where: ΔHf(s) is the enthalpy of the coated separator, Wt(PE)% is the weight percent of polyethylene content from TGA.
The resulting melting enthalpy of the polyethylene in the coated samples is 186 J/g. The corresponding degree of crystallinity for the uncoated separator is 76.9% and 63.7% for the coated separator. As the degree of crystallinity for a polymer impacts the physical properties of the materials, the user can expect a difference in properties between these separators.
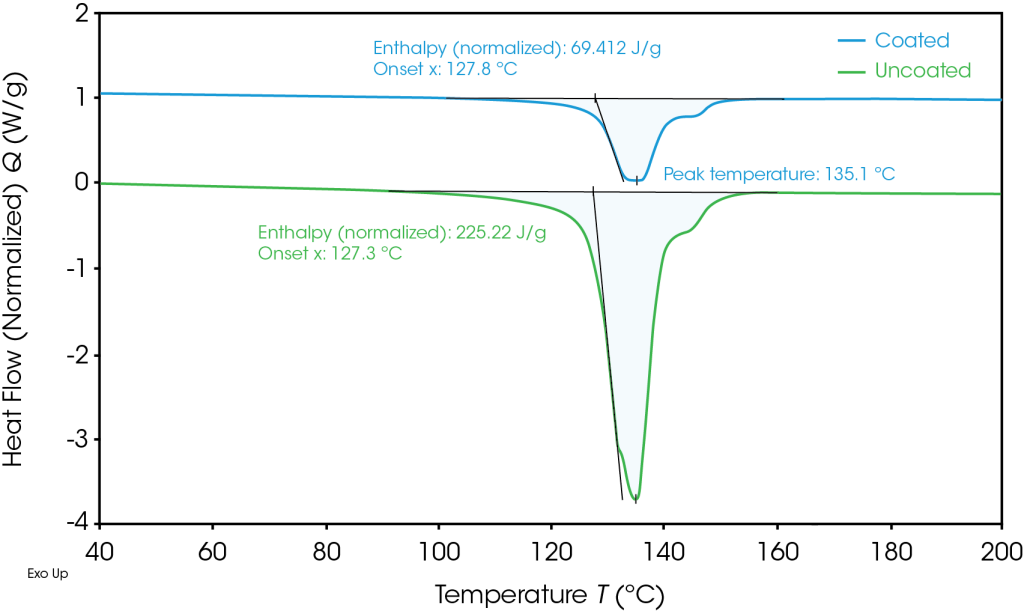
Thermomechanical Analysis (TMA)
The coated and uncoated separators exhibited similar melt integrity, shown in Figure 3. These results indicate that the polyethylene film common to both samples is driving the melt integrity properties of these separators. For the samples shown in Figure 3, both the onset of shrinkage and rupture temperatures were increased by less than 4 °C in the coated samples. However, the average onset of shrinkage and rupture temperatures for three samples is shown in Table 2 and shows even less separation between the coated and uncoated performance. The standard deviations reveal how reproducible the TMA measurements are, showing that this analysis can be utilized with confidence to characterize separators and investigate the potential impact of coating formulations. This reproducibility is especially important when measuring safety critical properties such a melt integrity, as a ruptured separator can lead to thermal runaway in a battery.
Table 2. Average onset of shrinkage and rupture temperature for three repeats of coated and uncoated separators
Separator | Onset of Shrinkage (°C) | Rupture Temperature (°C) |
Uncoated | 124.54 ± 0.48 | 128.52 ± 0.30 |
Coated | 125.82 ± 0.57 | 131.46 ± 0.55 |
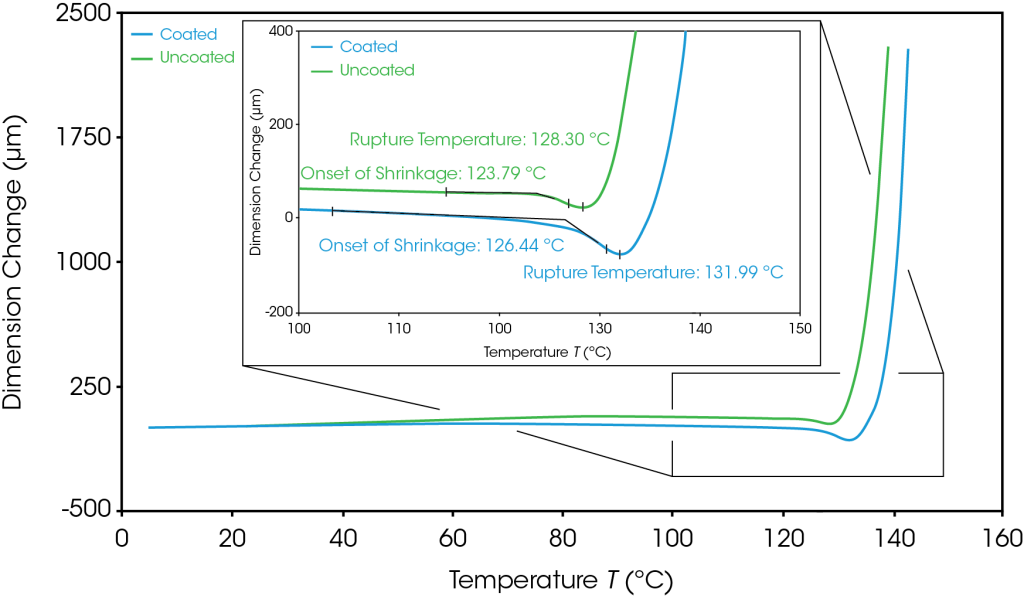
Dynamic Mechanical Analysis (DMA)
The stress strain curves from the large strain ramp tests at 35 °C and 60 °C are shown in Figure 4. At both temperatures, the stress at 400% strain is approximately 38% lower for the coated separator than the uncoated separator. The decrease in stress for the coated separator is attributed to the coating breaking down as the films stretch.
Small strain experiments were used to determine the Young’s modulus of the separators at 35 °C. Smaller strains were used to avoid breaking down the coating. Young’s modulus was calculated using the slope from 0-0.05% and the results are shown in Table 3.
Table 3. Young’s Modulus of Uncoated and Coated Separators at 35 °C.
Separator | Young’s Modulus (MPa) |
Uncoated | 690 ± 40 |
Coated | 920 ± 70 |
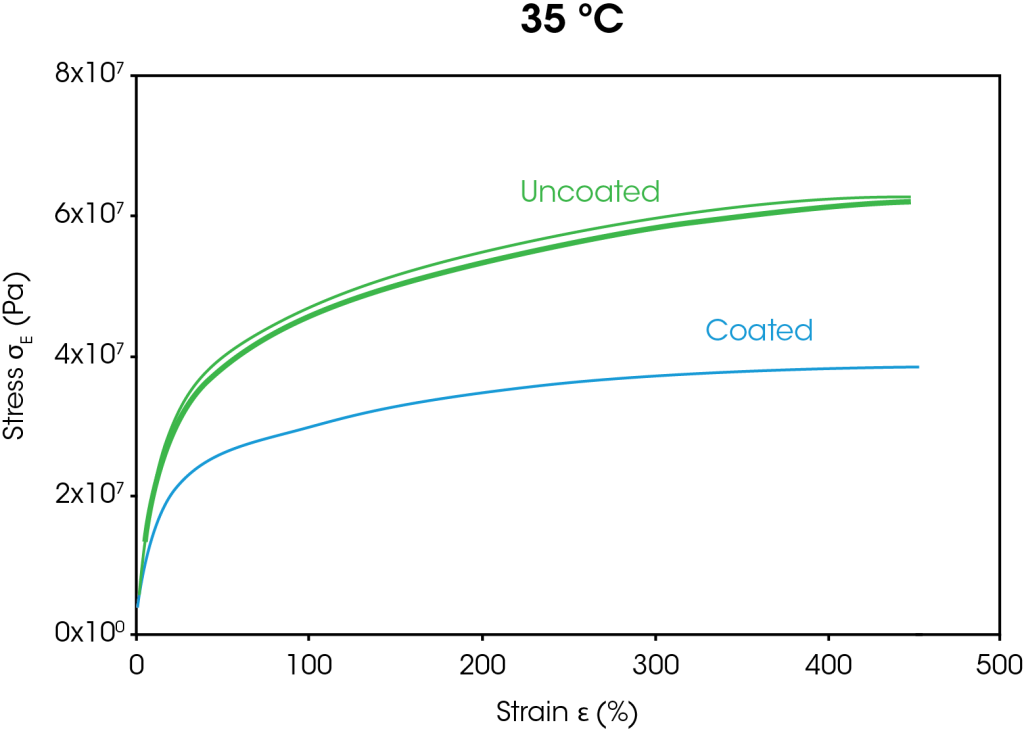
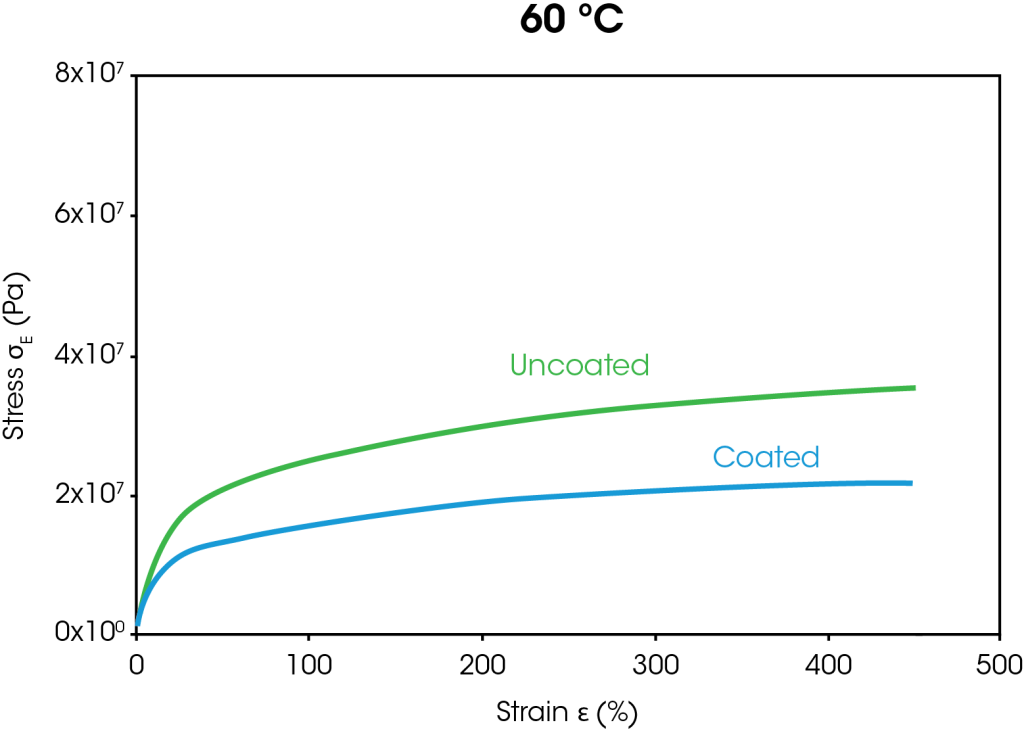
Storage modulus, loss modulus, and tan delta curves of the uncoated and coated separators are plotted in Figure 5 with respect to temperature. The uncoated and coated separators have similar storage modulus values until higher temperatures are reached, as highlighted in Table 4. At higher temperatures, the uncoated sample begins softening and melting, as seen by the storage modulus drop off, whereas the coating appears to offer higher temperature stability. Transition temperature peaks may be identified by the onset value of the storage modulus and the peak value of the loss modulus as shown in Figure 5. In this case, the transition corresponds to the α-process in polyethylene [7]. The coated separator has a bimodal tan delta peak, indicative of the heterogeneity of the sample. Under these conditions, the coated separator demonstrates higher temperature stability.
Table 4. Storage modulus differences of uncoated and coated separators
Temperature (°C) |
Storage Modulus (MPa) | ||
Uncoated | Coated | Difference (%) | |
20 | 1880 | 1790 | 5 |
60 | 750 | 590 | 27 |
100 | 160 | 300 | 47 |
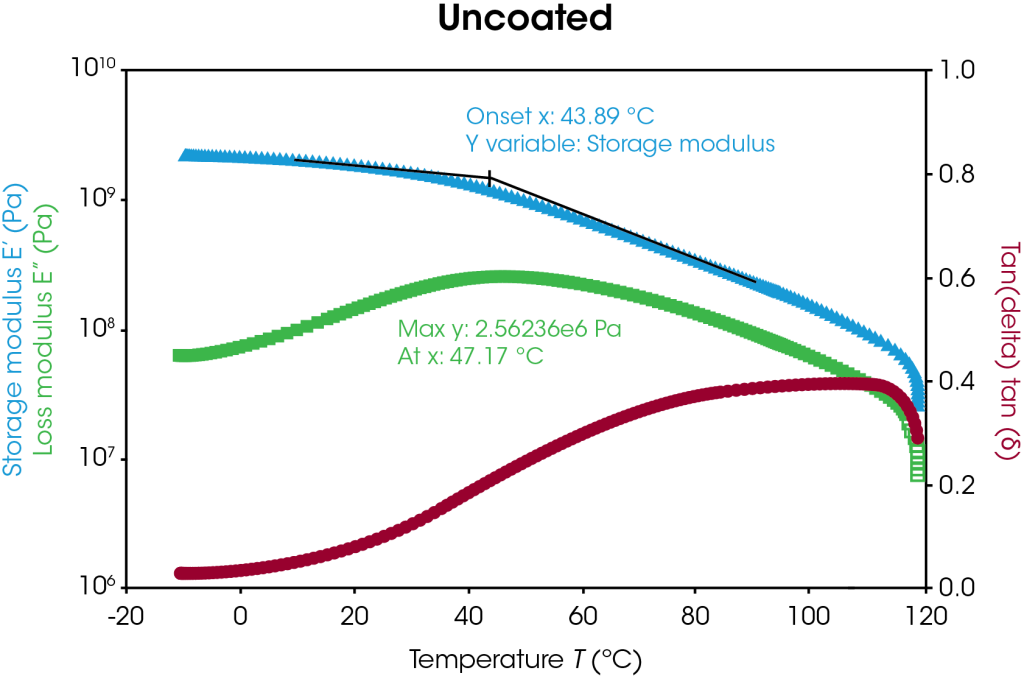
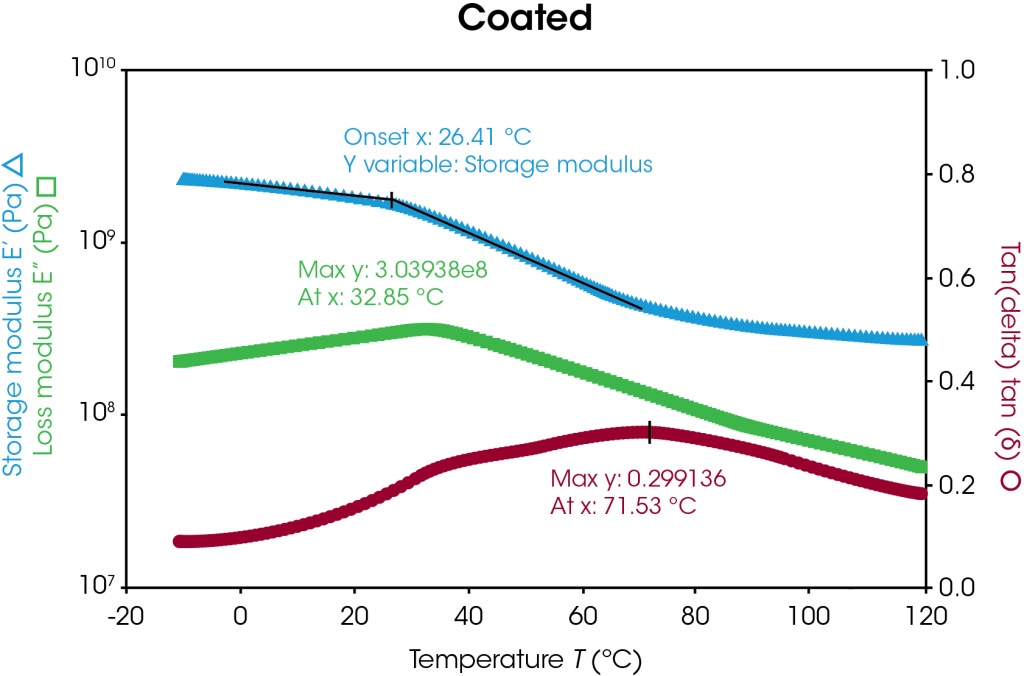
Conclusions
Battery separators play a critical role in lithium-ion battery performance, including the prevention of thermal runaway. These porous films are typically polymeric, and manufacturers may apply inorganic coatings to boost thermomechanical performance. In this note, a suite of TA Instruments analyzers was used to characterize a polyethylene separator, with and without an inorganic coating:
- Discovery TGA determined the thermal stability and composition content of the uncoated and coated separators. The coated separator contained 37% polyethylene and roughly 6% binder, with the coating comprising over 50% of the separator.
- Discovery DSC further analyzed the melting and crystallinity of the separators. The melting enthalpy was used to determine the polyethylene crystallinity. Using the polyethylene content measured from TGA, the melting enthalpy of the polyethylene content in the coated separator was found and used to directly compare polymer crystallinity of the two separators.
- Discovery TMA characterized the melt integrity of the coated and uncoated separators. The method was found to be reproducible, ensuring confidence in results. For the materials studied, little difference was observed in the onset of shrinkage and rupture temperatures, indicating that melt integrity is dominated by polyethylene.
- Discovery DMA was used for thermomechanical stability characterization. The storage modulus, loss modulus, and Young’s modulus of the separators were determined. The coated separator was found to have better stability at higher temperatures than the uncoated separator.
References
1. W. Luo, S. Cheng, M. Wu, X. Zhang, D. Yang and X. Rui, “A review of advanced separators for rechargeable batteries,” vol. 509, 2021.
2. P. Arora and Z. Zhang, “Battery Separators,” Chemical Reviews, vol. 104, no. 10, pp. 4419-4462, 2004.
3. J. Browne, “TA457 Thermal Analysis of Battery Separator Film”.
4. R Baldwin, W. Bennet, E. Wong, M. Lewton, M. Harris, “Battery Separator Characterization and Evaluation Procedures for NASA’s Advanced Lithium Ion Batteries,” NASA, Cleveland, 2010.
5. R. L. Blaine, “TN048- Polymer Heats of Fusion”.
6. I. Groves, T. Lever and N. Hawkins, “TA123- Determination of Polymer Crystallinity by DSC”.
7. Y. Men, J. Rieger, H.-F. Endeler and D. Lilge, “Mechanical α-Process in Polyethylene,” Macromolecules, vol. 36, pp. 4689-4691, 2003.
Acknowledgement
This paper was written by Jennifer Vail, Ph.D., at TA Instruments with data gathered by Andrew Janisse, Ph.D., Kimberly Dennis, Ph.D. , and Hang Lau, Ph.D.
TA Instruments has been long recognized as an innovator and leader in modulated thermal analysis.
Click here to download the printable version of this application note.