Keywords: rubber, RPA, viscosity, processing, capillary
RT007
Abstract
The characterization of the viscosity of rubber compounds is necessary for fully optimizing processing conditions. Measurement techniques for viscosity often include capillary rheology and dynamic oscillatory testing in an open or closed boundary rheometer. Due to the strain dependent nature of filled elastomer compounds, the Cox-Merz relationship, which is often used to correlate dynamic viscosity with steady-shear viscosity, does not hold and the dynamic viscosity values typically do not match the capillary rheometer. In this paper, we present a new method for directly measuring steady-shear viscosity using a rubber process analyzer (RPA).
Inrtoduction
Characterizing flow behavior across a range of shear rates is imperative for optimization of industrial processing operations. Elevated shear rates are commonly linked to relevant manufacturing processes, such as pipe flow, molding, and extrusion. These measurements are critical for compounders, formulators, process engineers, and researchers for predicting material behavior and optimizing processing conditions. One of the most important properties for flow behavior is the measurement of viscosity as a function of shear rate, as this value is directly related to a compound’s processability and critical for optimizing processing conditions. The most common technique for measuring viscosity of a rubber compound is via capillary rheometry. Although practically ubiquitous in the rubber industry, capillary rheometer measurements require large sample volumes and extensive corrections for experimental factors such as wall slip and pressure gradients [1-3]. In addition, users cannot preserve the mechanical history of the compound before the actual testing as the samples need to be re-formed into cylindrical dimensions to fit into the capillary, which can lead to viscosity values that do not adequately represent the compound during processing.
Another alternative to viscosity measurements is utilizing steady-shear testing in an open boundary, rotational rheometer. Steady-shear testing applies a uni-directional deformation under a controlled shear rate over time. Highly elastic samples will often exhibit edge fracture often at low shear rates (< 0.1 s-1), which limits the range of testing. One alternative approach to capture behavior at elevated shear rates, is to use the Cox-Merz relationship, which is an empirical relationship relating dynamic oscillatory data, such as that obtained from frequency sweeps, with steady-shear viscosity measurements. The Cox-Merz relationship (Figure 1) has been shown to correlate steady-shear viscosity with dynamic rheological data for many systems ranging from simple polymer melts to more complex polymer suspension systems [4-6].
However, the Cox-Merz relationship often fails for highly filled, elastic system due to weak filler-filler networks and complex interactions. As a result, the dynamic viscosity values derived using this relationship typically do not match the steady shear viscosity obtained with a capillary rheometer.
On the other hand, the TA Instruments RPA elite is uniquely poised to make steady-shear viscosity measurements of rubber compounds at elevated shear rates since it can apply a uni-directional rotation to the sample in a well-defined uniform shear flow field. Samples are compressed under high pressure forces and sealed in a biconical, serrated, closed-die system in an RPA, allowing users to perform steady-shear testing with increased sample grip and a delayed onset of edge fracture. It also allows users to precisely control the thermo-mechanical history of the sample with significantly lower sample volume compared to capillary rheometry measurements leading to improved precision. Lastly, the measurement can be coupled with additional RPA tests such as Payne effect tests, curing, frequency sweeps to obtain a wealth of information from a single experiment.
This application note demonstrates a facile method to directly measure the viscosity of rubber compounds using an RPA. These results are then compared to viscosity measurements using a capillary rheometer. This valuable information can further be used to understand the processing characteristics of a material, allowing operators to make adjustments in advance, thereby increasing productivity and reducing scrap.
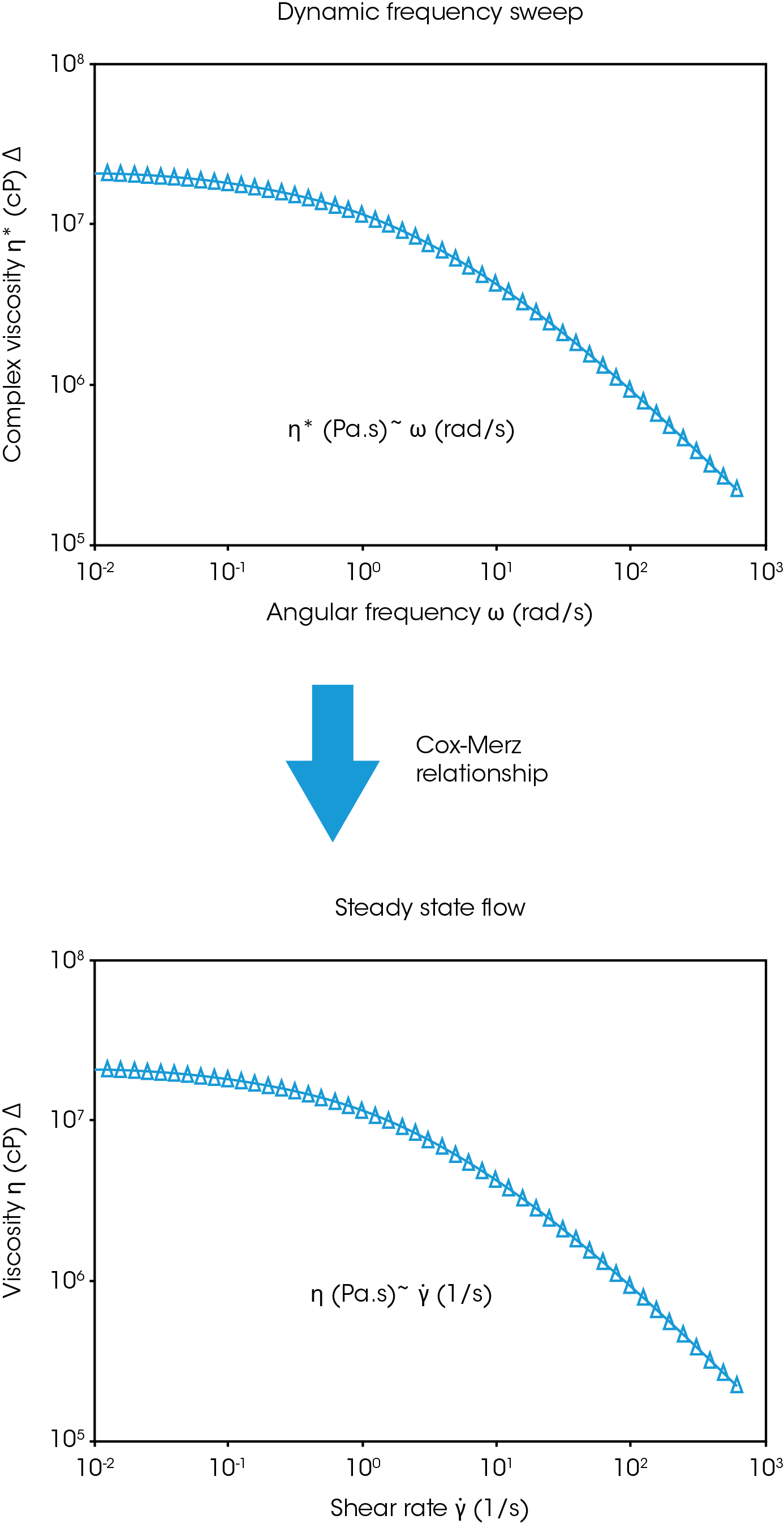
Experimental
All samples were tested on a TA Instruments RPA elite. The RPA elite is an advanced, rotorless rotational shear rheometer dedicated to the complete viscoelastic characterization of polymers, rubber, and rubber compounds at all stages of manufacturing. The RPA elite provides invaluable data related to the viscoelastic behavior of materials in the pre-cure state, through the curing process, and in situ cured state. Samples are sealed in a biconical die and compressed under high pressure forces, as is standard in the rubber industry. This design provides a closed testing cavity which prevents melt fracture at the sample edge, and compressive forces to prevent sample slippage during testing.
Approximately 5.5 grams of material (± 5%) was utilized and compressed in the testing cavity using a closing pressure of 4.5 bar. Samples were allowed to relax for 10-15 minutes in the testing cavity before measurements were performed in order to allow ample time for any internal stresses experienced during the loading process to dissipate. Viscosity measurements were performed using a steady-shear, ramp test. A uni-directional deformation was applied at a controlled shear rate to measure the viscosity. This data was further compared with viscosity data after applying the Cox-Merz relationship on dynamic frequency sweep tests in the RPA and data obtained from a capillary rheometer. The test conditions for the latter tests are listed within the respective figures.
Results and Discussion
The Cox-Merz relationship is an empirical relationship relating dynamic oscillatory data, such as that obtained from frequency sweeps, with steady-shear viscosity measurements. The Cox-Merz relationship has been shown to correlate steady-shear viscosity with dynamic rheological data for many systems ranging from simple polymer melts to more complex polymer suspension systems [4-6]. Figure 2 compares the viscosity derived from applying the Cox-Merz relationship to dynamic oscillation data (henceforth denoted as dynamic viscosity) to viscosity directly measured using capillary rheometry.
It can be observed that the dynamic viscosity and the capillary rheometry data do not overlap. The dynamic viscosity is shown to be dependent upon the applied strain in the oscillation tests. Lower viscosity values are observed for the dynamic test at 7% strain compared to 0.14% strain. This indicates a strong dependency of dynamic viscosity on the applied strain, which can be expected with filled rubber compounds, primarily due to the filler network and Payne effect [7]. A larger strain can break down the filler network, resulting in a less structured material that can flow easily. Interestingly, the viscosity obtained from both dynamic oscillatory tests do not match the viscosity obtained from a capillary rheometer. Since the filler networks are an important contributor to the rubber’s flow viscosity, it will be altered differently when the sample is subjected to an oscillatory deformation as compared to an uni-directional shear deformation on a capillary rheometer. The latter will typically cause an increased break down of the filler network. As a result, the viscosity measured using dynamic oscillatory testing will be much higher than the values obtained from a capillary rheometer, and the Cox-Merz relationship is not valid on such systems.
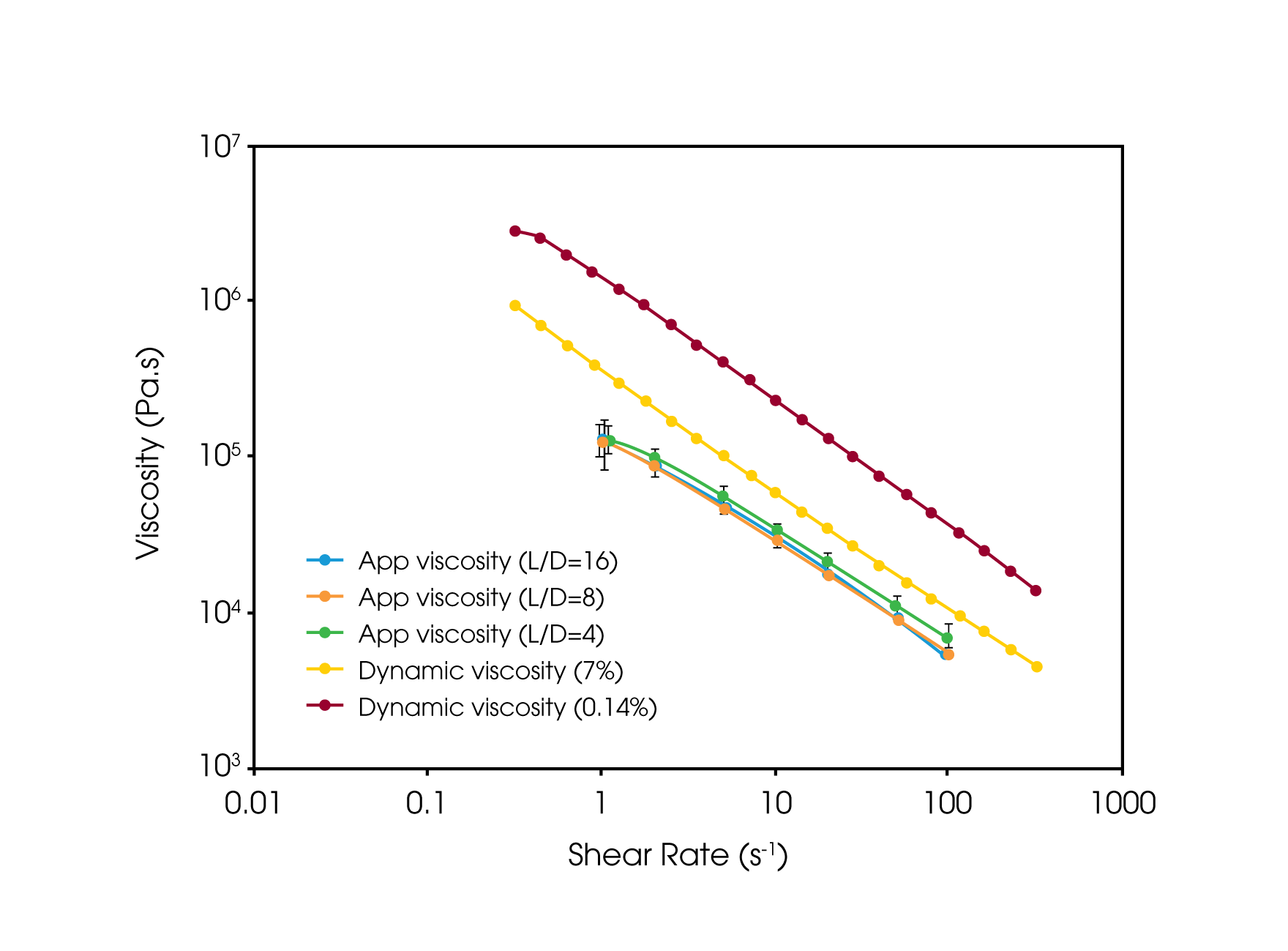
In order to overcome this gap, a new test method in the RPA has been employed to measure the steady state viscosity of rubber compounds. The RPA is programmed to apply a uni-directional deformation at a controlled shear rate is applied to the rubber sample, while measuring the resulting torque as a function of time. The torque reaches a plateau value as the material reaches steady state. Since the flow field is well-defined in the RPA, the torque can be easily converted to stress, and the viscosity can be calculated as the ratio of stress and shear rate. The viscosity of a generic tire tread compound can be seen in Figure 3 at shear rates of 0.01 to 10 s-1.
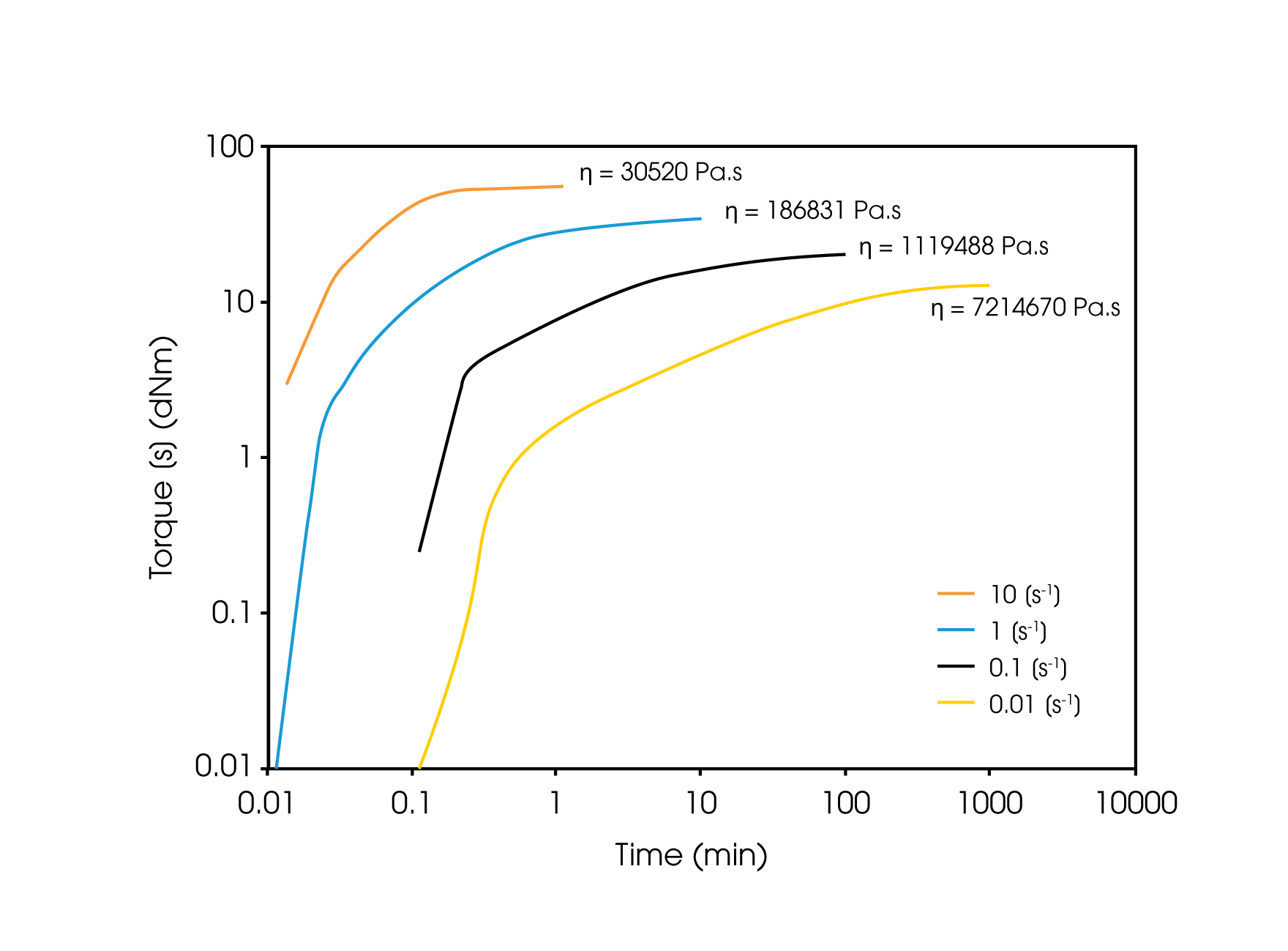
The viscosity can be calculated by taking the ratio of the stress in the steady state region and the applied shear rate. The calculated viscosity values were then compared to viscosity measurements performed with a capillary rheometer at varying L/D ratios, shown in Figure 4. The steady-shear viscosity values calculated from the RPA compare very well with the capillary rheometer measurements. These results indicate that the steady-shear viscosity can be measured directly in the RPA by applying a controlled shear rate. This novel methodology provides unique benefits, such as smaller sample volumes for testing, ease of sample preparation and preserving the thermo-mechanical history of the sample since no remolding is required. This makes the above approach a quick and easy method for measuring the viscosity of a rubber compound.
In order to further verify the validity of the approach, the same method was applied to an unfilled, uncured EPDM. The viscosity was obtained using steady-shear testing in the RPA was compared with that obtained using Cox-Merz relationship on dynamic oscillatory data. For a simple, unfilled system, the Cox-Merz relationship has been shown to be valid. This is clearly observed in Figure 5, as the steady-shear viscosity data fits well with the dynamic data.
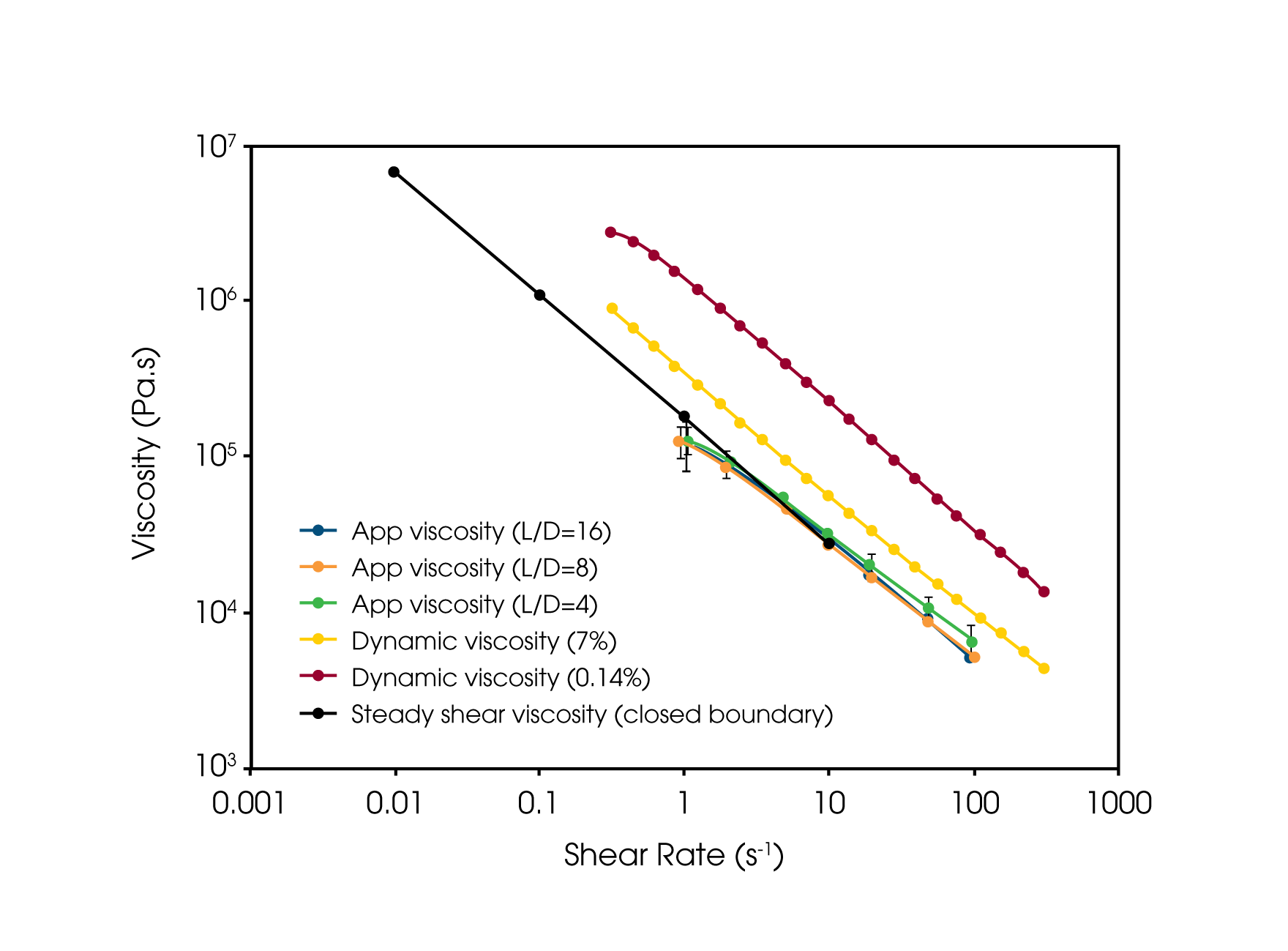
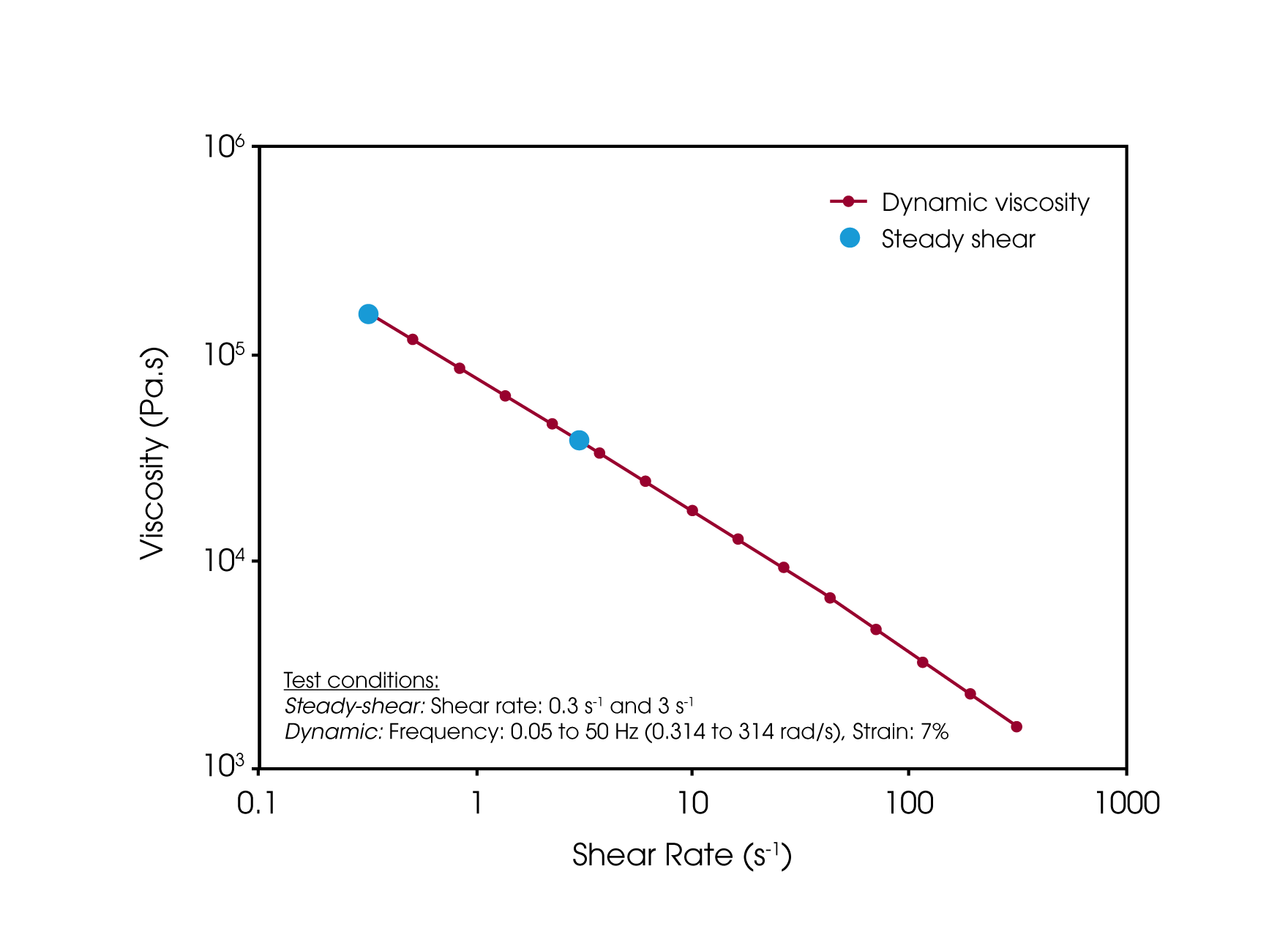
Conclusion
A new test method is demonstrated using the TA Instruments RPA elite to directly measure the steady-shear viscosity of rubber compounds. The measured values correlate well with the apparent viscosity measured from capillary rheometers. This approach overcomes the traditional capillary rheometer challenges, including large sample volumes, the need to remold samples prior to testing elaborate cleaning between tests and the need for extensive mathematical corrections. The RPA offers a serrated, closed-boundary design which alleviates the challenges of slippage and elasticity-induced sample fracture observed when performing these measurements on a traditional open-boundary rheometer. The method is also extremely powerful for measurements on filled materials where the presence of complex filler-filler and filler-polymer interactions renders the classical Cox-Merz relationship of mathematically deriving steady-shear viscosity from dynamic oscillatory tests invalid. The method can be expanded to study the material properties under a well-defined shear history. It can also be coupled with additional RPA tests such as Payne effect tests, curing, frequency sweeps to obtain a wealth of information from a single experiment.
References
- Macosko, C. W. “Rheology: Principles, Measurements and Applications” VCH Publishers, New York, 1994.
- Bagley, E. B. “End corrections in the capillary flow of polyethylene”, J Appl Phys 28:193–209, 1957.
- Hatzikiriakos, S. G., Dealy, J. M. “Wall slip of molten high density polyethylenes. II. Capillary rheometer studies”, Journal of Rheology 36, 703, 1992
- Cox, W.P., Merz, E.H. “Correlation of dynamic and steady flow viscosities,” Journal of Polymer Science, 28, 619, 1958.
- Doraiswamy, D., Mujumdar, A. N., Tsao, I., Beris, A. N., Danforth, S. C., Metzner, A. B. “The Cox–Merz rule extended: A rheological model for concentrated suspensions and other materials with a yield stress”, Journal of Rheology 35, 647, 1991
- Al-Hadithi, T. S. R., Barnes, H. A., Walters, K. “The relationship between the linear (oscillatory) and nonlinear (steady-state) flow properties of a series of polymer and colloidal systems” Colloid Polym Sci 270: 40, 1992
- Payne, E.R “The dynamic properties of carbon black-loaded natural rubber vulcanizates. Part I.” Journal of Applied Polymer science, Vol. 6, 19.
Acknowledgement
This application note was a collective effort of the work of Sandeep Reddy, Alina Latshaw (PhD), David Bohnsack (PhD), Thomas Rauschmann, and Yash Adhia.
Click here to download the printable version of this application note.