Keywords: powder rheology, wall friction, CMC, moisture, adhesion
RH129
Abstract
Powder rheology is a useful tool for formulating and optimizing processing conditions of pharmaceutical tablets. The angle of wall friction can be used to gage the adhesion present between a powder and tablet punch material, with higher angles correlating to higher wall friction and adhesion. This adhesion may lead to tablet sticking and wall friction measurements can be used to understand how formulation or environmental conditions may impact sticking. This work investigates the influence of moisture content and substrate material on the wall friction of carboxymethyl cellulose powder, which is used as an excipient in tablet formulations.
Introduction
Tablet sticking is one of the most common manufacturing challenges in the pharmaceutical industry. It occurs when the adhesion between particles and punch face is greater than the cohesion between particles in the powder, resulting in the powder adhering to the tablet punch. Once granules begin sticking to the punch, subsequent tablets are defective, and production is disrupted to address the issue. Sticking is influenced by a variety of factors, including manufacturing conditions, tablet design, and formulation [1][2]. Excipient powders can be a source of sticking, requiring formulations to be optimized to reduce sticking. Researchers and manufacturers have found powder rheology measurements to be a useful tool in understanding sticking and formulating to minimize it [2][3].
Powder rheology measures the shear and flow properties of materials. Shear measurements can be used to understand the cohesion of powders while the angle of wall friction offers insight into adhesion of the powder against a substrate. As the angle of wall friction decreases, the adhesion against the surface decreases. Previous work investigated the influence of moisture on the cohesion of carboxymethyl cellulose (CMC), a common excipient [4]. Due to its hygroscopic nature, CMC retains moisture in even ambient conditions, which can influence tablet sticking [5]. Shear measurements found increasing cohesion with increasing moisture content. In this note, the influence of moisture on wall friction of CMC powder was studied using the TA Instruments Powder Accessory for Discovery Hybrid Rheometers, shown in Figure 1.
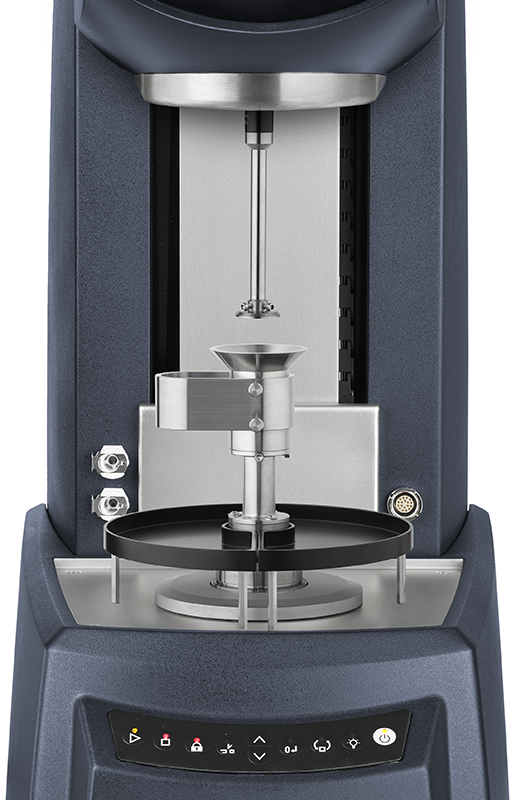
Experimental
Commercially available CMC powders manufactured by Deiman USA were tested as received and after conditioning in a humidity chamber. The moisture content was determined by thermogravimetric analysis (TGA). Duplicate measurements were performed on TA Instruments Discovery TGA 5500 at a ramp rate of 20 °C/min under nitrogen in platinum pans. Weight loss was determined at 225 °C to identify moisture content.
A TA Instruments Discovery HR30 at ambient room conditions was used for powder rheology measurements of the samples. The wall friction accessory was used in combination with the powder shear cell. Interchangeable plates can be used to measure wall friction against different materials. For this work, wall friction measurements were performed using the standard stainless steel plate, the most commonly used material in pharmaceutical processing equipment [6]. Tests were also run using a custom acetal plastic plate to investigate the influence of substrate material on wall friction. Samples were loaded in the cell, consolidated at 9 kPa, and trimmed. Details of the loading and trimming procedure can be found in previous work [7]. TRIOS programming for the wall friction measurements, including the sample consolidation step, are shown in Figure 2.

Wall friction angle is determined using TRIOS powder software. The Steady State Stress analysis is applied to the pre-shear and shear steps in the procedure, generating the stress at the end of each step. The test points are then compiled into the wall friction summary. These data points are used to create a plot of stress vs. normal stress. The wall yield locus analysis generates a line of best fit as shown in Figure 3. The wall friction angle is the angle created between the yield locus line and the x-axis.
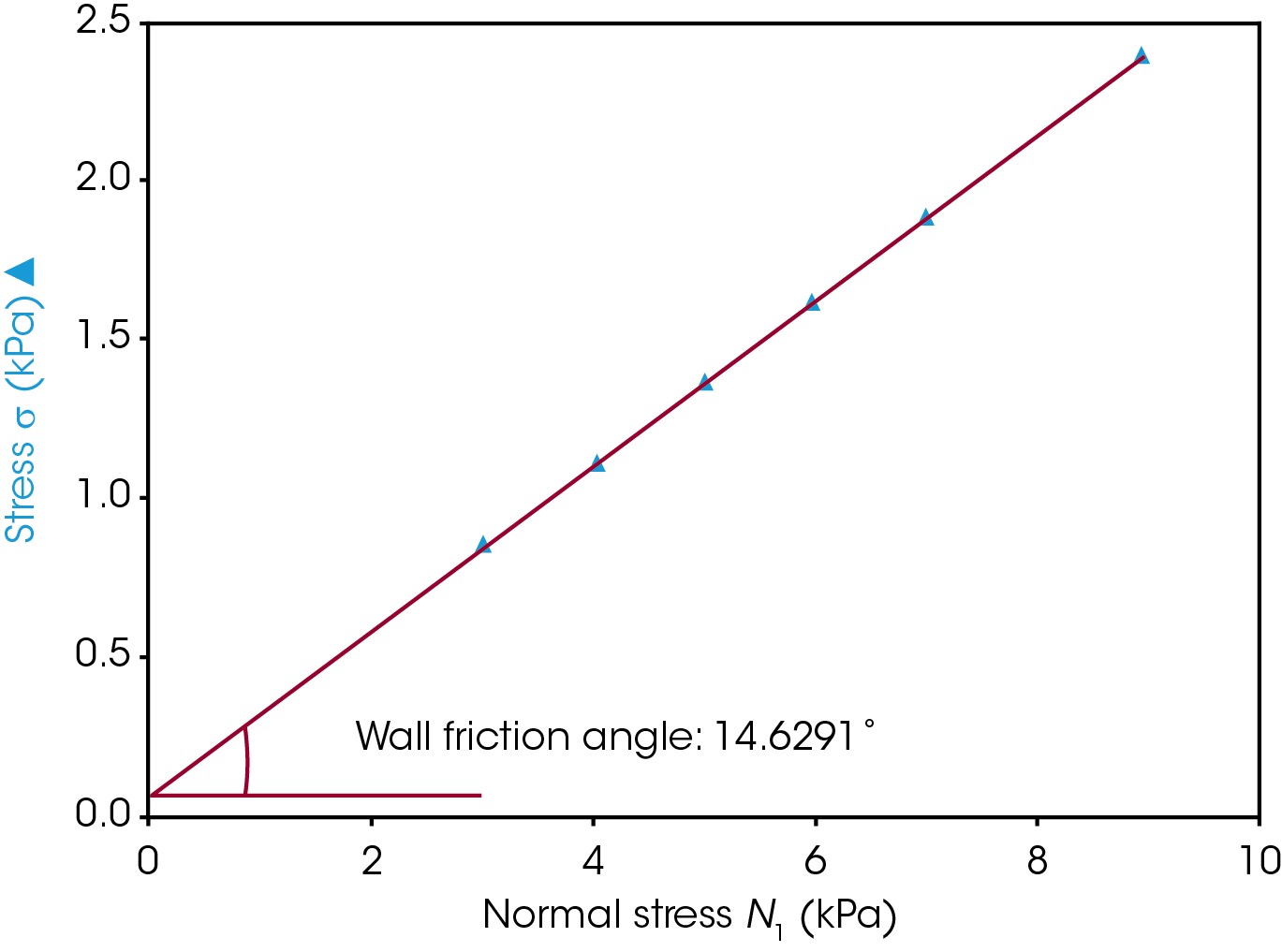
Results and Discussions
Analysis performed by TGA shows 9.3% moisture content for as received powder and 22.3% for humidity-conditioned powder as shown in Table 1.
Wall friction results for CMC are plotted in Figure 4 and summarized as wall friction angles in Table 2.
Table 1. TGA analysis results for CMC powder with and without moisture conditioning.
AS RECEIVED MOISTURE CONTENT (%) | CONDITIONED MOISTURE CONTENT (%) | |
---|---|---|
1 | 9.24 | 22.66 |
2 | 9.28 | 21.95 |
Average | 9.26 ± 0.02 | 22.31 ± 0.36 |
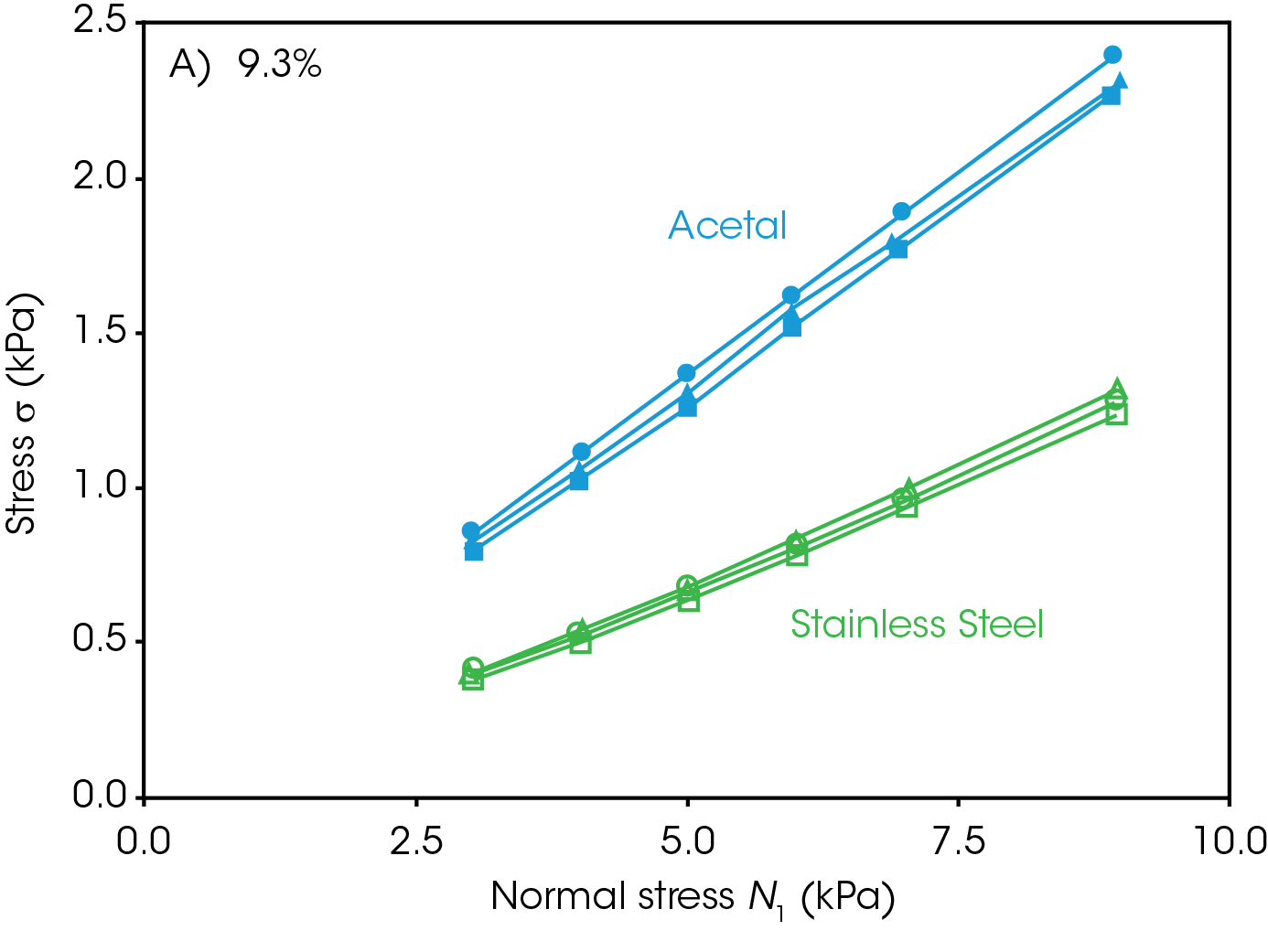
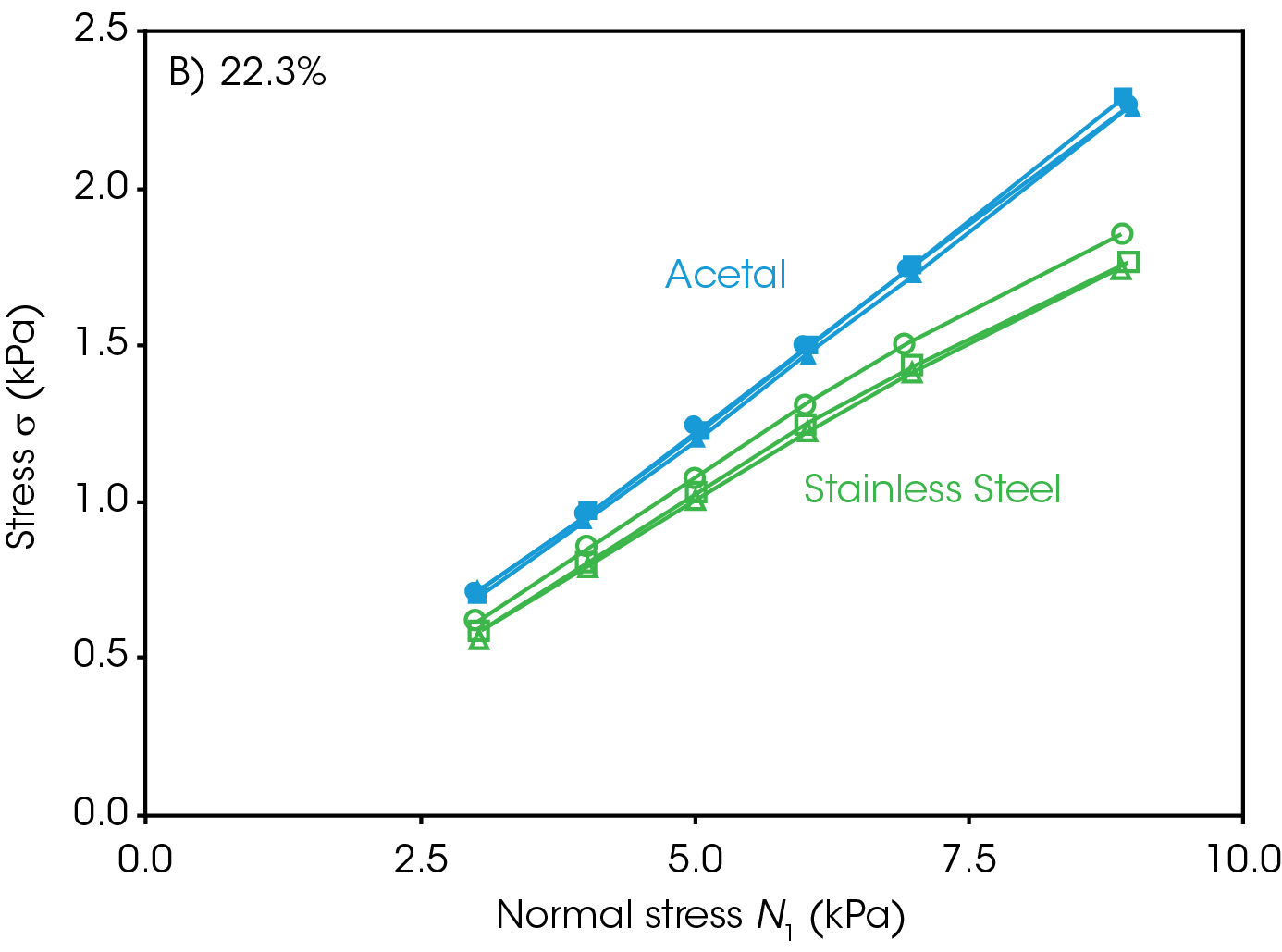
For both 9.3% and 22.3% moisture CMC, the wall friction angle values are higher for acetal and lower for stainless steel, indicating that the powder has stronger adhesion to the acetal material. Higher moisture content yields higher wall friction angles for both acetal and stainless steel. Between CMC samples, acetal angles differ by about 0.6° and stainless steel angles differ by about 3.1°, indicating that acetal is less sensitive to moisture overall. The lower wall friction angles for stainless steel indicate that the CMC powders are less likely to stick to stainless steel than acetal; adhesion to stainless steel is more sensitive to moisture. If a processing setup is designed using stainless steel for a dry powder, humidity control will be important as some batches with additional moisture exposure may stick. The wall friction is less sensitive for acetal, indicating that using acetal equipment will yield more consistency in processing of wet and dry powders, but the general higher trend of wall friction in the system would require trial runs to ensure sticking is not a factor.
Table 2. Wall friction angle results for 9.3% and 23.3% moisture CMC powders measured with acetal (plastic) and stainless steel (SST) attachments.
9.3% | 22.3% | |||
---|---|---|---|---|
Plastic (°) | SST (°) | Plastic (°) | SST (°) | |
1 | 14.6 | 8.4 | 14.7 | 11.9 |
2 | 14.1 | 8.2 | 15.0 | 11.3 |
3 | 14.0 | 8.7 | 14.8 | 11.4 |
Average | 14.2 ± 0.3 | 8.4 ± 0.2 | 14.8 ± 0.1 | 11.5 ± 0.3 |
Conclusions
CMC powders with and without moisture conditioning were tested with the TA Instruments Powder Rheology Wall Friction Accessory with interchangeable stainless steel and acetal plates. The results offer insights that can aid in processing conditions, quality control between powder batches, and detect sensitivities to differences in formulations. Wall friction angle measurements found that the angle is higher for acetal and lower for stainless steel for both powders. Higher moisture content resulted in higher wall friction for both acetal and stainless steel measurements. Stainless steel measurements were more sensitive to moisture so the adhesion properties during production may change if environmental conditions are not well controlled or moisture content of powder batches vary.
References
- B. V. Parekh, J. S. Saddik, D. B. Patel and R. H. Dave, “Evaluating the effect of glidants on tablet sticking propensity of ketoprofen using powder rheology,” International Journal of Pharmaceutics, vol. 635, 2023.
- C. Lanzerstorfer, C. Forisch and D. Heim, “Reduction of Wall Friction of Fine Powders by Use of Wall Surface Coatings,” Coatings, vol. 427, 2021.
- J. S. Saddick and R. H. Dave, “Evaluation of powder rheology as a potential tool to predict tablet sticking,” Powder Technology, vol. 386, pp. 298-306, 2021.
- J. R. Vail, K. Dennis and T. Chen, “Effect of Moisture on Cohesion Strength of,” TA Instruments, New Castle, DE, 2022.
- D. Z. L. Ng, A. Z. Nelson, G. Ward, D. Lai, P. S. Doyle and S.A. Khan, “Control of Drug-Excipient Particle Attributes with Droplet Microfluidic-based Extractive Solidification Enables Improved Powder Rheology,” Pharmaceutical Research, vol. 39, pp. 411-421, 2022.
- B. C. Hancock, “The Wall Friction Properties of Pharmaceutical Powders, Blends, and Granulations,” vol. 108, pp. 457-463, 2019.
- J. R. Vail and S. Cotts, “Powder Rheology of Lactose: Impacts of powder morphology on performance of pharmaceutical excipients,” TA Instruments, New Castle, DE, 2022.
Acknowledgement
This paper was written by Kimberly Dennis, PhD and Jennifer Vail, PhD with thermal support provided by Gray Slough, PhD at TA Instruments.
Click here to download the printable version of this application note.