Keywords: CMC, lithium-ion battery, binder, moisture, powder rheology, cohesion, TGA
RH126
Abstract
The processability of powders is dependent on factors such as cohesion strength and flow function. Powder rheology can be used to measure these properties and aid in hopper design, selection of flow rates, and quality control. Carboxymethyl cellulose powder is a hygroscopic material used in a variety of applications. The impact of moisture content on cohesion strength is measured using the TA Instruments Powder Rheology Accessory. It was found that as moisture content increases, cohesion strength also increases, demonstrating the importance of controlling humidity during processing.
Introduction
Powder materials are used across a range of industries, from cosmetics to food, and applications are as varied as battery electrodes [1] and pharmaceutical tablets. A variety of manufacturing processes involve powders, and powder characterization is an important step to ensure efficient operation and to maintain quality control. Properties such as cohesion strength and flow function influence hopper design, mass flow, and quality of the final product. Powder rheology provides quick, repeatable measurements of powder flow properties [2].
Carboxymethyl cellulose (CMC) is a commonly used thickener, binder, or stabilizer. CMC is hygroscopic and retains moisture even in ambient conditions, which can change its flow properties and impact quality and manufacturing processes. The presence of moisture may also affect CMC concentrations in final products such as electrode slurries. In the pharmaceutical industry, CMC’s moisture sensitivity is particularly important to understand due to its effect on wet granulation and tableting. Powder shear cell measurements have been used to quantify the effect of humidity and moisture on powder flow properties [3].
In this study, the TA Instruments Powder Rheology shear cell accessory is used to investigate the effects of moisture on CMC powder. This accessory was previously used to investigate the flowability and cohesion strength of lactose powders [4]. Here, it will be utilized to study cohesion and flow function. TA Instruments Thermogravimetric Analyzer (TGA) will also be used to determine the moisture content of the powders.
Experimental
CMC samples manufactured by Deiman were commercially obtained for this study. Sample powders were equilibrated in three different humidity chambers: ambient, 49% relative humidity (RH), and 84% RH. TA Instruments Discovery TGA was used to measure the moisture content of the CMC samples. TGA measurements were conducted at a ramp rate of 10 °C/min up to 800 °C under nitrogen with samples in platinum pans.
The Powder Rheology Accessory includes interchangeable shear and flow cells. All measurements in this study were performed using the shear cell, shown in Figure 1, with a Discovery HR rheometer at ambient room conditions. Figure 2 demonstrates the procedure to prepare the powder samples for testing. The provided trim slide and funnel were used to load the CMC powders into the shear cell. The powders were then consolidated by applying a stress of 9 kPa and trimmed to remove excess powder and level the surface for testing.
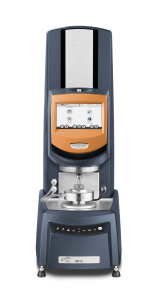
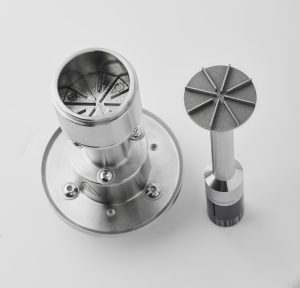
![RH126_Fig.2 Figure 2. Procedure to prepare powder samples for shear testing [1]](https://www.tainstruments.com/wp-content/uploads/RH126_Fig.2.png)
Table 1. Multi-step powder shear test procedure
Step | Pre-Shear Stress (kPa) | Test Stress kPa |
---|---|---|
1 | 9 | 7 |
2 | 9 | 6 |
3 | 9 | 5 |
4 | 9 | 4 |
5 | 9 | 3 |
Testing was performed per ASTM D7891 [5] with a consolidation stress of 9 kPa. Table 1 details the procedure used. Each test consists of five steps. Prior to each step, the samples are pre-sheared at 9 kPa with slow rotation (angular velocity of 1*10-3 rad/sec) until the measured shear stress reaches steady state. Then, the applied normal stress is reduced to the value specified in Table 1 for that step, ranging from 7 kPa to 3 kPa.
TA Instruments Powder Shear Analysis in TRIOS software calculates the cohesion strength and flow function. These parameters can be utilized to predict and control mass flow during manufacturing processes. Cohesion is the y-intercept of the yield locus and the flow function (FF) is the ratio of major principal stress to unconfined yield strength.
Results and Discussions
The moisture content of the CMC samples is shown in Figure 3.
The powder shear measurements show a strong relationship between cohesion strength and moisture. As the moisture content of the CMC powders increases, so does the cohesion strength, as shown in Figure 4.
As summarized in Table 2, Flow Function (FF) decreases from 18.3 to 4.3 between the ambient and 84% RH samples. A higher FF means the powders are easier to flow, which is desirable for manufacturing processes. These results indicate that controlling the humidity in processing areas is important to regulate powder flow, which affects efficiency and quality.
Table 2. Summary of powder shear measurements for CMC samples
CMC | Moisture content (%) | Cohesion strength (kPa) | Flow function (FF) |
---|---|---|---|
Ambient | 8.3 | 0.15 | 18.3 |
49% RH | 15.1 | 0.58 | 9.5 |
84% RH | 25.0 | 1.20 | 4.3 |


Conclusions
CMC powders were conditioned to have different moisture content, as measured by TGA. Powder rheology measurements on the Discovery HR were used to determine the sensitivity of CMC powders to moisture. Powder shear measurements found increasing cohesion strength with increasing moisture content. As a result, samples with higher moisture experience decreasing flow function, which impacts powder processing. To ensure quality control and efficient operations, CMC powder should be processed in humidity controlled environments.
References
- K. Dennis and S. Cotts, “Powder Rheology of Graphite: Characterization of Natural and Synthetic Graphite for Battery Anode Slurries,” TA Instruments, New Castle, DE, 2022.
- R. Freeman, “Measuring the flow properties of consolidated, conditioned and aerated powders- A comparative study using a powder rheometer and a rotational shear cell,” Powder Technology, vol. 17, pp. 25-33, 2007.
- D. Schulze, “Round robin test on ring shear testers,” Advanced Powder Technology, vol. 22, pp. 197-202, 2011.
- J. R. Vail and S. Cotts, “Powder Rheology of Lactose: Impacts of powder morphology on performance of pharmaceutrical excipients,” TA Instruments, New Castle, DE, 2022.
- “ASTM D7891-15 Standard Test Method for Shear Testing of Powders Using the Freeman Technology FT4 Powder Rheometer Shear Cell,” ASTM International, 2016.
Acknowledgement
This paper was written by Jennifer Vail PhD, Kimberly Dennis PhD, and Tianhong (Terri) Chen PhD.
Click here to download the printable version of this application note.