Keywords: ASTM D623, Goodrich Flexometer, Heat Generation, Flexing Fatigue, Heat Build-up, HBU, Heat Blow-out
EF033
Introdution
In recent years, trends in tire manufacturing have shifted to high performance rubber compounds that offer lower fuel consumption. Dynamic mechanical performance of these rubber compounds is primarily influenced by the mechanical properties of the matrix polymer and its interaction with the filler.1 The two main fillers added to rubber compounds are carbon black and precipitated silica. Carbon black has long been the primary reinforcement for rubber compounds and is used to improve tear strength, modulus, and abrasion resistance.2 On the other hand, silica provides unique capabilities of tear strength, abrasion, and aging resistance as well as better wet traction and improved low rolling resistance compared to carbon black.3 It has been estimated that a reduction in rolling resistance by 10 % can lead to up to 2% improvement in fuel efficiency.4 Therefore, silica is sometimes known as the eco-friendlier, more green filler for tire tread compounds due to its low environmental impact by reducing fuel consumption and CO2 emissions. 5-6
This article investigates the flexing properties and heat generation of rubber mixtures of styrene butadiene rubber and butadiene rubber, with silica and carbon black as fillers, using Goodrich Flexometer test or Heat Build-up.7
Materials and Methods
Three specimen of 20 mm x 20 mm (Diameter x Height) from each of four formulations were used for each test. The dimensions differ from ASTM D623 specifications but were consistent throughout the study for a relevant comparison to each other.
The materials were selected based on similar shore hardness to provide a relevant and fair comparison. The formulations used for this study are summarized in Table 1. In addition to silica and carbon black as varying ingredients, butadiene rubber was changed from linear to branched molecular structure. If neodymium is used as a catalyst during the polymerization reaction, butadiene rubber with a narrow molecular weight distribution with low degree of branching is obtained whereas if cobalt is employed, butadiene rubber with a broad molecular weight distribution and a high degree of branching can be produced. Same silica compounds were previously also investigated for their processing, pre-cure properties by Heinz et al using Rubber Process Analyzer from TA Instruments.8
Heat Build Up tests were carried out per ASTM D623 test method on ElectroForce 3330 instrument with oven. The recommended mean load on the specimen is 644, 990 or 1970 kPa and a dynamic peak-to-peak strain of 17.8%, 22.84% or 25.4%. Phenolic platens were used to avoid any heat loss during dynamic tests under high loads with the lower platen fitted with a thermocouple to measure the specimen’s base temperature. A schematic of the phenolic platen is shown in Figure 1.
Table 1. Summer tire tread formulations
Compound Designation | ||||
---|---|---|---|---|
Components | Lin-Si (phr) | Lin-C (phr) | Br-Si (phr) | Br-C (phr) |
Styrene Butadiene Rubber |
96.25 | 96.25 | 96.25 | 96.25 |
Butadiene Rubber |
30 (Linear) | 30 (Linear) | 30 (Branched) | 30 (Branched) |
Silica | 80 | – | 80 | – |
Carbon Black (N-234) | – | 73 | – | 73 |
Silane (Si-266) | 5.8 | – | 5.8 | – |
DPG-80 | 2.5 | – | 2.5 | – |
Vulkacit CZ (CBS) | 1.6 | 1.6 | 1.6 | 1.6 |
Perkacit | 0.2 | – | 0.2 | – |
Sulphur | 2 | 1.4 | 2 | 1.4 |
A/S ratio | 2.15 | 1.14 | 2.15 | 1.14 |
WinTest® HBU Application software was used to maintain a mean compressive load of 990 kPa and an equivalent total dynamic stroke of peak-to-peak 17.8% strain was implemented simultaneously at a frequency of 30 Hz. Before the test starts, DMA measures the specimen height at a given pre-load which serves as a basis for subsequent strain calculations. The ambient oven temperature was set to 50 ºC. The test ran for a total of 25 minutes with a data collection rate of 10kHz. The HBU application also includes common DMA measurements including complex modulus, storage modulus, and loss modulus as well as tangent delta, also known as loss factor. These results are obtained from the precise measurement of the magnitude and phase relationships between force and displacement signals as the material deteriorates under high dynamic and mean forces.
Before the experiment, the specimen height was measured with a vernier caliper. After the experiment, the specimen was allowed to cool to room temperature for 1 hour and the final height was measured. Compression set was calculated per following equation:
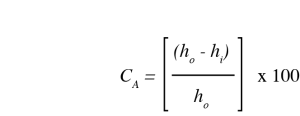
Where:
CA = compression set as a percentage of original height
ho = original height
hi = final height


Results and Discussion
A thermocouple mounted in the insulating platens measured the sample’s base temperature. The base temperature change is plotted in Figure 3.
The effect of higher heat generation can be seen in the form of increased specimen temperature. Maximum heat build-up was seen in the branched compound with carbon black filler and the least amount of heat build-up was seen in the branched compound with silica.
The rapid change in mechanical properties for all the compounds was observed in the first few minutes (Figure 4 and Figure 5). The storage moduli decreased for the first five minutes and then started to increase. This change was higher and more drastic in carbon filled compounds compared to silica filled compounds. The increase in storage modulus is an indication of buckling of the specimen and a higher tangent delta (loss factor) for same compounds and reinforces the previous increased temperature rise data. Silica, on the other hand, showed negligible buckling and lower loss factor.



The heat Build-Up experiment was continued only for 25 minutes per ASTM D623. Longer durations should show a continuously increasing temperature for carbon filled polymer whereas steady-state temperature for silica filled polymer was reached within 25 minutes. Approximately 5 ºC temperature difference was observed for carbon black between the linear and branched compound compared to only 2.5 ºC average between the similar silica-containing formulations. Total temperature rise of the compounds with Carbon black is ~40 ºC and almost twice as high as of Silica compounds (Figure 6). This suggests heat generation of the rubber compounds was influenced to a greater extent by the type of filler and perhaps accelerator/sulfur ratio compared to the branching of the polymer. Surface properties of the filler and filler network interaction9 can also have an influence in the heat buildup behavior.
The compression set also showed a similar trend to temperature rise between silica and carbon as illustrated in Figure 7. The carbon compounds tested have a higher permanent compression set compared to the silica samples. Less compression set was observed in linear polymer than branched polymer for carbon filler. However, an equal amount of compression set was seen in silica filled polymers.
Previous observations by Blume et al.10 have indicated that as the accelerator to sulfur ratio increases, aging resistance is improved. This was also observed in the temperature increase in each specimen in Fig. 6 and the compression set in Fig. 7, respectively. Since silica filled polymers have approximately twice the accelerator to sulfur ratio (Table 1) compared to carbon filled polymers, they may give higher mono-sulfide links which generate a more resilient elastic polymer matrix where molecular chains are less likely to plastically shear against each other, hence less heat generation.


Conclusions
Dynamic performance of greener tire recipe with silica filled rubber has been demonstrated to be better than carbon black filled compounds. Branched and linear butadiene rubber in styrene butadiene rubber matrix with fillers were tested for their dynamic mechanical response. No significant difference between the polymer architecture of butadiene rubber was observed. However, reasonable difference was illustrated between silica and carbon filled compounds. Carbon filled compounds which also have lower accelerator to sulfur ratio showed twice as much increase in damping at higher strains compared to silica filled compounds under high strain and high frequency loading. Heat buildup and compression set were also found to be higher for carbon filled compounds. The data presented in this study show that silica filled compounds offer better dynamic mechanical performance and heat generation than carbon black filled compounds. This shows silica’s potential for a more sustainable tire by offering improved fuel economy and reduced environmental impact.
Future Outlook
The current study indicates the difference between carbon filled and silica filled compound which could either stem from the fillers/matrix interactions or due to variation of accelerator to sulphur ratio. It will be beneficial if the rubber compounds with similar A/S ratio or with different fillers are tested to help identify which variable most impact these properties.
References
- Ten Brinke, J. W., Debnath, S. C., Reuvekamp, L. A., & Noordermeer, J. W. (2003). Mechanistic aspects of the role of coupling agents in silica–rubber composites. Composites Science and Technology, 63(8), 1165-1174.
- Nasir, M., & Teh, G. K. (1988). The effects of various types of crosslinks on the physical properties of natural rubber. European polymer journal, 24(8), 733-736.
- Rattanasom, N., Saowapark, T. A., & Deeprasertkul, C. (2007). Reinforcement of natural rubber with silica/carbon black hybrid filler. Polymer Testing, 26(3), 369-377.
- National Research Council (US). Transportation Research Board. Committee for the National Tire Efficiency Study.(2006). Tires and passenger vehicle fuel economy: informing consumers, improving performance (Vol. 286). Transportation Research Board.
- Lolage, M., Parida, P., Chaskar, M., Gupta, A., & Rautaray, D. (2020). Green Silica: Industrially scalable & sustainable approach towards achieving improved “nano filler–Elastomer” interaction and reinforcement in tire tread compounds. Sustainable Materials and Technologies, 26, e00232.
- Sarkar, P., & Bhowmick, A. K. (2018). Sustainable rubbers and rubber additives. Journal of Applied Polymer Science, 135(24), 45701.
- ASTM D623-07(2019) e1, Standard Test Methods for Rubber Property—Heat Generation and Flexing Fatigue In Compression, ASTM International, West Conshohocken, PA, 2019.
- Heinz, M., Kroll, J., & Rauschmann, T. (2017). Characterization of Summer Tire Tread Compounds by Large Amplitude Oscillating Shear (Laos). KGK-KAUTSCHUK GUMMI KUNSTSTOFFE, 70(4), 41-46.
- Wang, M. J. (1999). The role of filler networking in dynamic properties of filled rubber. Rubber chemistry and technology, 72(2), 430-448.
- Cichomski, E., Dierkes, W. K., Noordermeer, J. W., Schultz, S. M., Tolpekina, T. V., Reuvekamp, L. A. E. M., & Blume, A. (2015, October). Effect of the crosslink density and sulfur-length on wet-traction and rolling resistance performance indicators for passenger car tire tread materials. In 188th Technical Meeting of Rubber Division, ACS (pp. 13-15).
Acknowledgement
This note was written by Muhammad Haris, Applications Support Engineer at TA Instruments.
The author would also like to express their sincerest gratitude to Evonik Operations GmbH, Smart Materials for providing cured tire tread formulations for completing this investigation.
Click here to download the printable version of this application note.