Keywords: fatigue testing, tensile strength, durability, ElectroForce, polymer fatigue
EF038
Abstract
Polymers are highly sensitive to cyclic loading and typically have much lower fatigue strength than their measured tensile strength. Despite this, fatigue testing is often overlooked in material selection. NORYL™ 731 samples were injection molded using a single and dual gate design to investigate the impact of production artifacts, using knit lines as a representative imperfection. Tensile testing showed that modulus was unaffected by the knit line and ultimate tensile strength (UTS) was marginally affected, but elongation at break was significantly lower for the dual gate sample. Fatigue testing showed a notable difference in strength between the samples: single gated samples reached 30,000 cycles at 50% of their ultimate strength while dual gated samples reached only 6,000 cycles at this stress level.
Introduction
Mechanical strength is often a key design parameter in material selection, but durability must also be considered for parts that experience cyclic stress, including vibrations. Fatigue is one of the primary failure mechanisms of polymer parts [1]; even at moderately low stresses, the fatigue life of polymers can be relatively low resulting in component failure. Failure of a part late in the design cycle or after product launch is costly, both in time and money, and early screening for fatigue life can reduce costs by identifying and eliminating fatigue failure early in the design process [2].
Polymer durability is impacted by a variety of factors, including molecular structure, temperature effects, and stress concentrations in the part design [2] [3]. Furthermore, during production of the parts, knit lines, voids and internal stresses can be created. These affect fatigue performance, but not necessarily parameters reported in standard datasheets, such as modulus or tensile strength. Evaluating the loss of material strength and durability in the presence of these production artifacts is an important step in the material selection and validation process.
This note demonstrates the importance of fatigue testing by evaluating NORYL 731 samples with and without knit lines. The mechanical strength and durability of the parts is measured, showing the loss of strength from cyclic loading and how production conditions can further exacerbate that loss.
Experimental
NORYL 731 polyphenylene ether (PPE) + polystyrene (PS) was injection molded into ASTM D638-22 Type 1 dog bones [5]. One set of samples were made into single-gate samples with consistent properties throughout the part; the second sample types were made using a dual-gate process, forming a knit line in the center of the gage section. Examples of the single and dual gated parts are shown in Figure 1.
Tensile testing was performed according to ASTM D638-22 with a rate of 2 in/min (50.8 mm/min). Five tensile tests were run for each sample type. A TA Instruments™ ElectroForce™ 3330 test instrument, shown in Figure 2, was used for the fatigue testing. Samples were tested at 5 Hz in tension-tension and the cycle was from 100% to 10% of maximum load (R=0.1). Compressed air was gently blown over the sample to ensure material self-heating didn’t increase the temperature and influence the results. Sample temperatures were monitored throughout the testing.
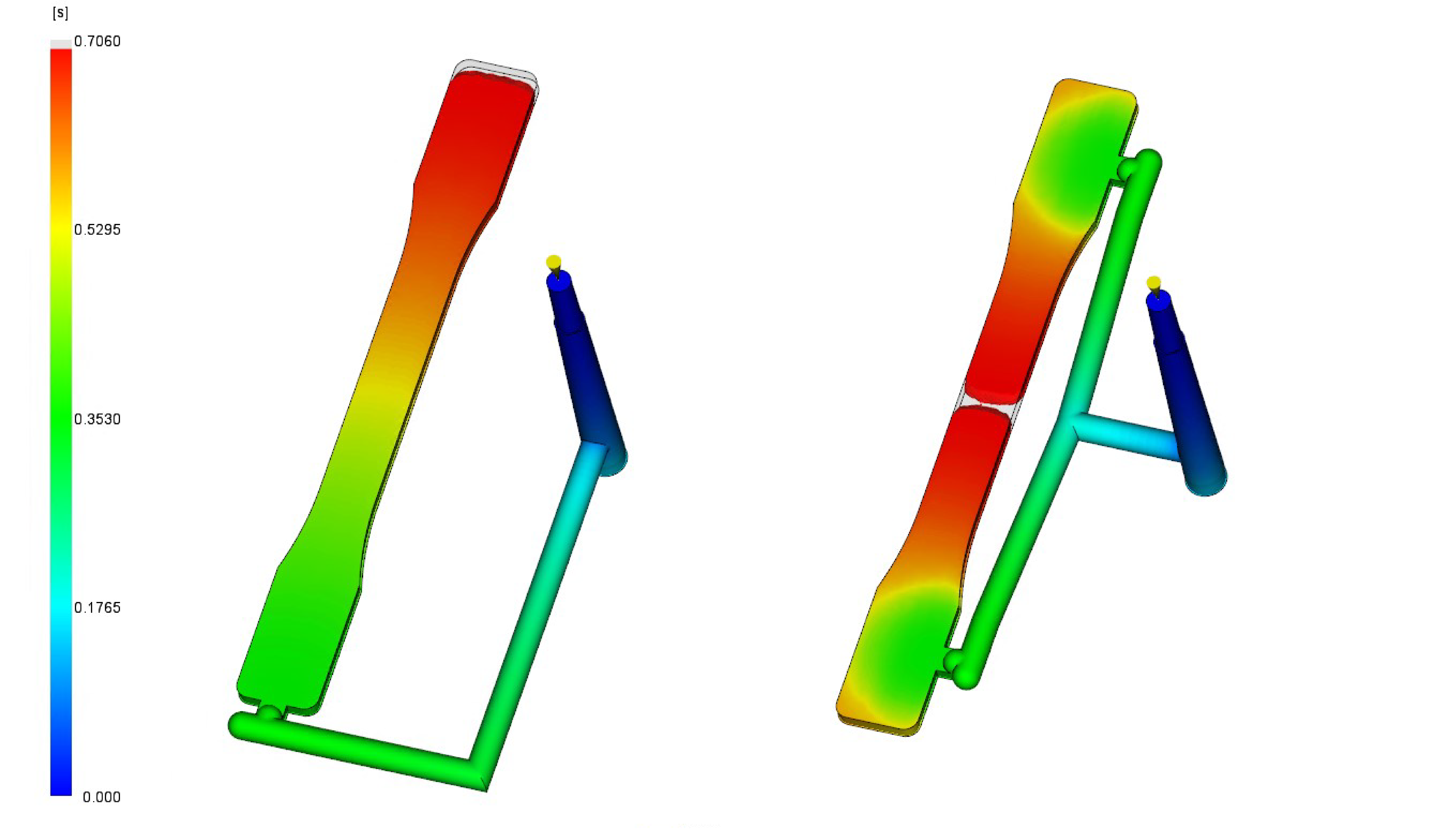
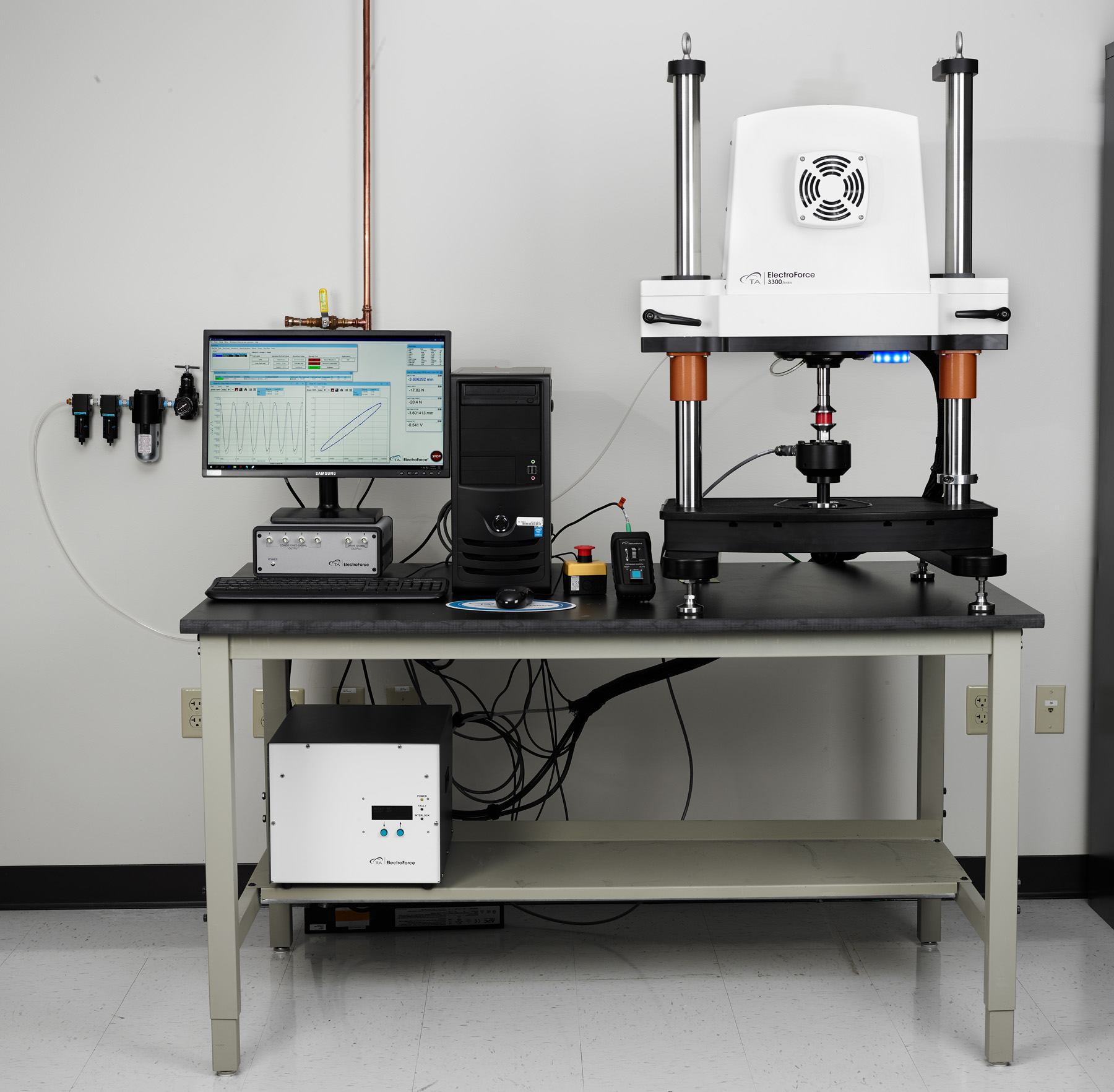
Results and Discussion
The tensile testing results are shown in Table 1, which reports the average and standard deviation of the five tests. Minimal change was seen in the modulus of the two sample types. The dual gate sample showed a modest reduction of tensile strength and a significant reduction in elongation at break when compared to the single gate.
Lower elongation at break signifies that ductility has been lost, and the differences in sample behavior can be seen in the tensile curves shown in Figure 3. The loss of ductility exhibited by the dual gate sample will impact durability, although the full extent is unknown from this testing.
Fatigue testing showed a significant reduction in life between the single and dual gated samples. Figure 4 is the S-N Curve which plots the stress (S) versus cycles (N) and shows the fatigue life of the single gated sample (blue) and dual gated sample (orange). The life of the material is greatly reduced as increasing fatigue stress is applied, especially for the dual gate sample. The dual gate samples showed a fatigue life around 6-18% of the single gate samples for the same stress level.
From the S-N curve, the single gated sample reaches 30,000 cycles at loading of 50% UTS while the dual gated sample reaches only 6,000 cycles. In comparison, metals will commonly have a fatigue life orders of magnitude greater than this; fatigue stress of 50% of UTS would result in life of millions of cycles and sometimes approaching the infinite life endurance limit.
Table 1. Tensile Testing Results*
Modulus (MPa) | Tensile strength (MPa) | Stress at break (MPa) | Elongation at break (%) | |
---|---|---|---|---|
Single gate | 2330.4 ± 21.4 | 52.6 ± 0.2 | 47.3 ± 0.2 | 29.49 ± 2.74 |
Dual gate | 2289.5 ± 7.3 | 44.1 ± 0.1 | 44.1 ± 0.1 | 2.29 ± 0.01 |
% Difference | 2% | 16% | 7% | 92% |
*Courtesy of The Madison Group
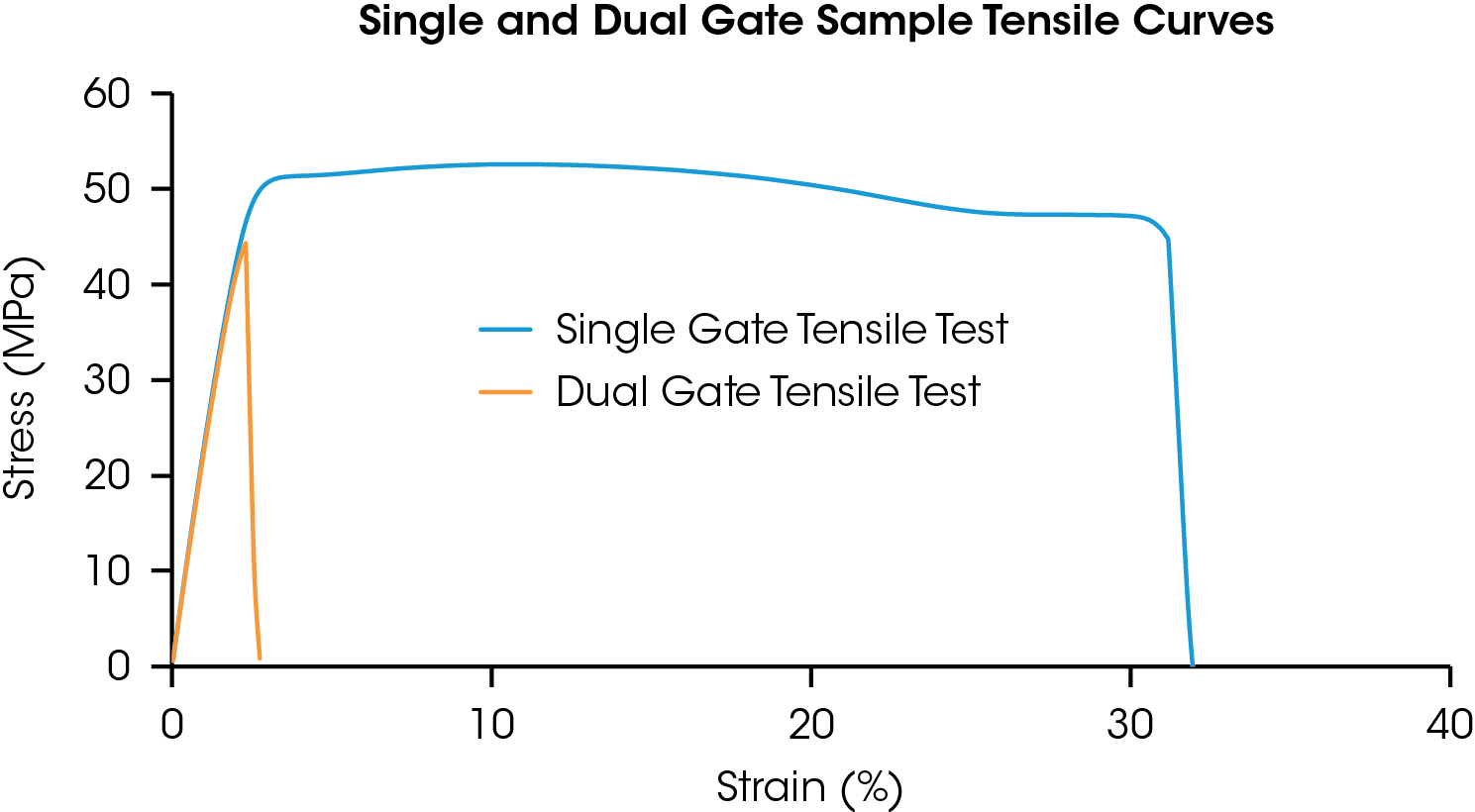
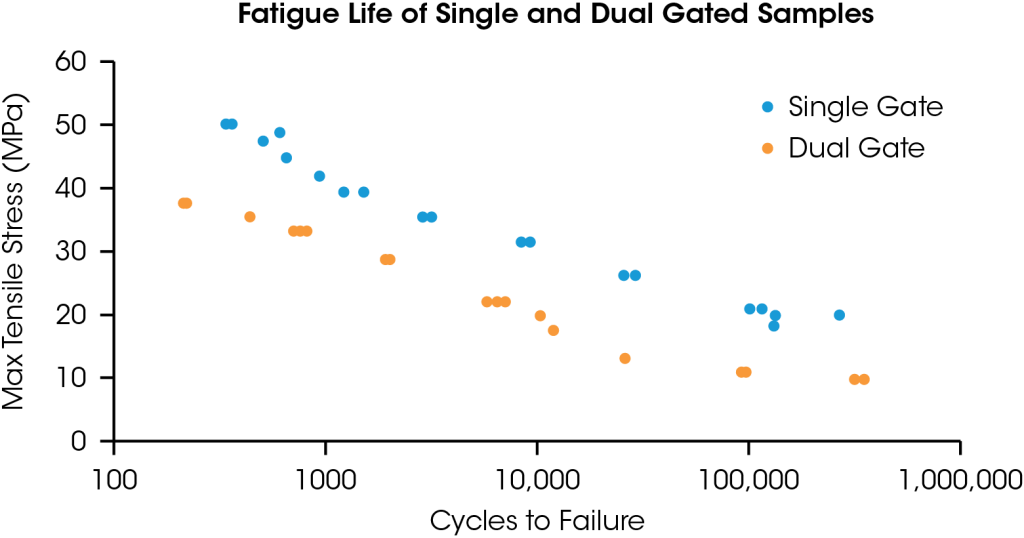
Conclusions
Datasheets often do not report data for the fatigue strength of materials, despite many parts experiencing repeated loading and the fatigue strength of polymers being substantially lower than tensile strength. Tensile and fatigue testing was performed on single and dual gate NORYL 731 samples, showing that knit lines have little impact on modulus and tensile strength, but significantly affect the fatigue life and ductility of the part. Testing by an ElectroForce 3300 test instrument showed that dual gate, knitted samples have a fatigue life of 6-18% of their single gate counterparts. Single gate samples reached 30k cycles at a stress level of 50% of UTS and dual gate samples only reached 6k cycles at that stress level. In addition to production artifacts such as knit lines, polymer fatigue can be impacted by various factors such as temperature and molding conditions. Incorporating fatigue testing early in the material selection and product development process can be used to avoid product failure and high costs due to latestage development changes.
References
- J. A. Jansen, “Webinar: “Fatigue of Plastic Materials”,” Society of Plastics Engineers, 2016.
- B. Davis, P. Gramann and A. Rios, “Using Computer-Aided Engineering to Design Better Thermoset Composite Parts,” in Automotive Composites Conference and Expositions, 2002, 2002.
- T. H. Courtney, Mechanical Behavior of Materials, Long Grove, Illinois: Waveland Press, 2005.
- M. Eftekhari and A. Fatemi, “On the strengthening effect of increasing cycling frequency on fatigue behavior of some polymers and their composites: Experiments and modeling,” International Journal of Fatigue, vol. 87, pp. 153-166, 2016.
- ASTM International, “ASTM D638-22 Standard Test Method for Tensile Properties of Plastics,” ASTM International, Conshohocken, PA USA, 2022.
Acknowledgement
This work was done in collaboration with The Madison Group Polymer Processing Research Corporation (The Madison Group).
This paper was written by Jennifer Vail, PhD and Andy Simon at TA Instruments | Waters, and Jeffrey A. Jansen from The Madison Group.
Click here to download the printable version of this application note.