Keywords: Rheology, viscoelastic property, curing, glue, caulk, crosslinking, gelation, humidity, annular ring
RH101
Abstract
The curing of wood glue or silicone sealants is very sensitive to the exposed environmental humidity. Moisture could have a significant impact on the curing reaction. It is important to have a good understanding of these kinds of curing processes with precisely controlled temperature and humidity. Monitoring the changes of the viscoelastic properties during curing and measuring the final cured modulus are critical for adhesive industries in guiding product formulation and manufacturing.
In this study, we introduce the use of an enhanced environment chamber on TA Instruments Discovery Hybrid Rheometers for curing analysis with both temperature and humidity control. A specially designed annular ring geometry is used for this measurement. The annular ring geometry provides a uniform diffusion of humidity to the sample. Our results highlight the sensitivity and effectiveness of this technique in understanding the curing response to a changing humidity environment.
Introduction
In addition to temperature, the curing reactions of certain types of adhesives, such as wood glues and silicone caulks, are also sensitive to the environmental humidity [1-4]. Water can act as an initiator to initiate and accelerate the reaction for some curing reactions. However, in other circumstances, a humid environment may significantly slow down a curing reaction. In addition to the influence on the reaction rate, the water molecules in a sample can also act as a plasticizer, which affects the viscoelastic properties and changes the adhesion behavior of the final cured product. Therefore, quantitative characterization of the rheological properties under both controlled temperature and humidity becomes critically important.
TA Instruments offers a Relative Humidity (RH) accessory that can be attached and used with a Discovery Hybrid Rheometer (Figure 1). This accessory provides the ability to control both temperature and humidity simultaneously. Test geometries used in combination with this RH accessory have been specially designed and optimized for testing different types of samples from low viscosity liquids, pastes, gels and solids. The operating temperature range of this accessory is 5-120 °C, and the controllable relative humidity range is 5-95% depending on the set temperature. The specifications of this humidity accessory are shown in Figure 2.
In this study, the relative humidity accessory with a specially designed annular ring geometry was used to monitor the curing process of two adhesive samples under a controlled temperature and humidity environment.

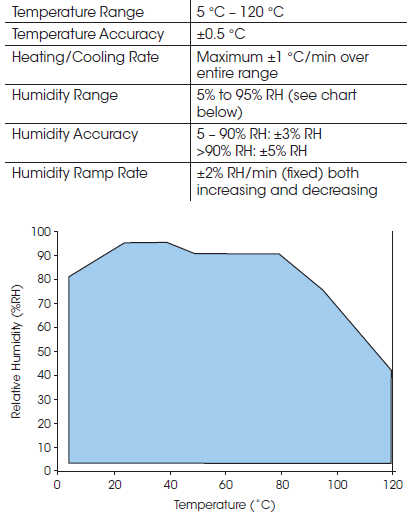
Experimental
One commercially available polyvinyl acetate-based (PVAc) glue and one silicone caulk adhesive were selected as example samples for the curing analysis. In order to quantitatively monitor curing, a TA Instruments Discovery Hybrid Rheometer was used with the relative humidity accessory and an annular ring geometry. This ring geometry (shown in Figure 3) is specially designed to be used inside the humidity chamber. The bottom is a flat plate, and the top geometry has a ring shape with an outer diameter of 40mm and a ring thickness of 2 mm. Compare to a traditional parallel plate or cone and plate testing, which is limited by the diffusion rate, this ring design keeps the sample surface open on both inner and outer sides and increases sample exposure area to the environment. The annular ring geometry is capable of measuring the bulk properties of the sample and is useful for testing creams, gels, pastes, and other medium to high viscosity materials.
The polyvinyl acetate-based glue sample was loaded onto the ring geometry with a gap set at 2 mm. A dynamic time sweep test was programmed for monitoring the curing process at 50 °C with relative humidity of 10%, 30% and 60%, respectively. During the time sweep, a small oscillation torque of 5.0 µN.m was applied to the sample at a low frequency of 1.0 rad/s. Sample moduli (G’ and G”) and complex viscosity change was monitored as a function of humidity and time.
The silicone caulk sample was tested at 25 °C with relative humidity set at 10% and 60%, respectively. A dynamic time sweep was programmed using a frequency of 1 rad/s with a small strain that was within the linear viscoelastic region of the sample.
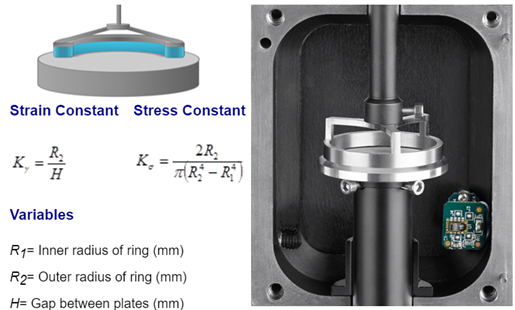
Results and Discussions
Figure 4 shows a quantitative measurement of the curing of glue at 50 °C with relative humidity set at 30%. At the beginning of the test, the sample behaves liquid-like with G” greater than G’. Both moduli increase rapidly with time. The G’/G” crossover is observed at a time of 6.3 min. This is the critical time when the sample undergoes a liquid-to-solid transition. This transition is also described as the gelation of the sample. Beyond this point, G’ becomes greater than G”, which means that the sample is solid-like. After 15 minutes, both G’, G” and the complex viscosity curves reach a plateau, which indicate that the curing reaction is mostly completed.
The overlay plot of curing under different humidity conditions (i.e. 10%, 30% and 60%, respectively) is shown in Figure 5. Comparative results of G’/G” crossover time and modulus are summarized in table 1. Based on the measured gelation time, one can see that the curing of this glue is significantly slowed down with increasing environmental humidity. But the mechanical strength of the sample at the gel point (i.e. the G crossover modulus) is observed to increase with increasing relative humidity. PVAc based glue cures initially through the evaporation of water. The polymerization occurs as water evaporates [1]. Since the environmental humidity slows down the evaporation, it increases the gelation time, and likely provides additional time for the adhesive to build up its molecular weight, which causes the G crossover modulus increase with increasing humidity.
Silicone based adhesive curing relies on a chemical reaction with water. These materials crosslink as being in contact with moisture. Figure 6 shows the results of a silicone caulk curing under different relative humidity conditions. It seems that moisture favors the curing of this sample. The storage modulus (G’) of the caulk increase much faster at 60% humidity than it did at 10% humidity.


Table 1. Summary of modulus crossover measured under different humidity conditions
Relative Humidity (%) | 10% | 30% | 60% |
---|---|---|---|
G Crossover time (min) | 3.6 | 6.3 | 23.3 |
G Crossover modulus (Pa) | 100.6 | 187.3 | 325.4 |
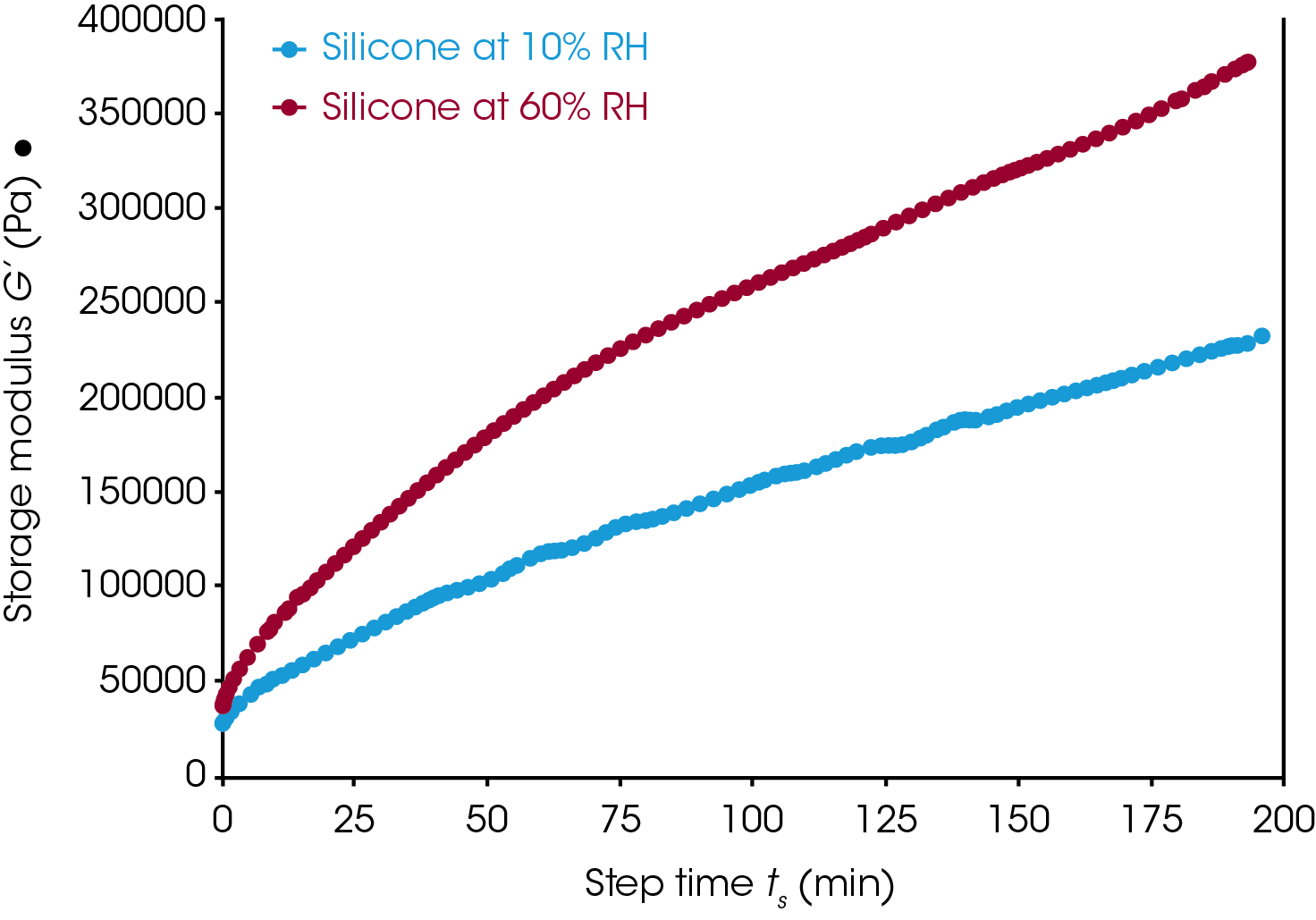
Conclusions
The curing reactions of certain materials are sensitive to both temperature and environmental humidity. TA Instruments’ relatively humidity accessory with the annular ring geometry provides the capability of quantitative measurements of curing under accurate control of both temperature and relatively humidity.
References
- C.B. Vick and R.M. Rowell, Adhesive bonding of acetylated wood. Int. J. Adhesion and Adhesives. Vol10 No.4, 263,(1990).
- G. Petkovi´c, M. Vukoje, J. Bota and S. P. Preproti´, Enhancement of Polyvinyl Acetate (PVAc) Adhesion Performance by SiO2 and TiO2 Nanoparticles. Coatings, 9, 707, (2019), doi:10.3390/coatings9110707
- Rupert Wimmer • Oliver Kla¨usler • Peter Niemz, Water sorption mechanisms of commercial wood adhesive films. Wood Sci Technol, Published online 23 March, (2013)
- J. Comyn, Moisture Cure of Adhesives and Sealants. International Journal of Adhesion and Adhesives, Vol 18, Issue 4, 247-253 (1998)
Acknowledgement
This paper was written by Dr. Tianhong Terri Chen, Senior Applications Support Scientist at TA Instruments.
Click here to download the printable version of this application note.