Keywords: Modulated DSC, MDSC, lyophilization
TA354
Introduction
Freeze-drying, or lyophilization as it is often called, has become a standard process in the pharmaceutical industry for the manufacture of biologically active substances [1–3]. However, it is not without limitations due to its high cost in capital and energy, long processing time, and difficulty in selecting parameters of time, temperature, pressure (vacuum) and component concentration. All of these parameters must be optimized in order to achieve full recovery of activity and complete reconstitution of the often-labile drug, acceptable appearance of the freeze-dried cake and good storage stability [4].
The process of freeze-drying relies on the vapor pressure of ice. Even at temperatures as low as −50 °C, the ice sublimes and leaves a very porous, low-density cake containing the stabilized drug. Since the sublimation rate (drying rate) is very temperature-dependent, approximately double for a 5 °C increase [5], use of the highest possible temperature during primary drying provides maximum drying efficiency and lowest process cost. The limitations of the process arise in the selection of the optimum drying temperature that can vary with time in the process as well as with the other parameters listed above.
In order to select the optimum drying temperature, it is necessary to understand the physical characteristics of the components used in the formulation that is to be freeze-dried. In decreasing order of mass, these are typically water, bulking agents, buffers or stabilizers and finally the drug itself. The bulking agent, which can be either crystalline or amorphous, and its interaction with the unfrozen water and ice in the frozen solution, define the physical structure which is essential to successful freeze-drying. This structure manifests itself in the form of transitions that occur at specific temperatures. Physical properties of the bulking agent such as modulus or viscosity can change by orders of magnitude depending on whether the process temperature is a few degrees above or below the transition temperature. Therefore, knowledge of this structure and the temperature where it changes is required for successful drying.
For many materials, it is relatively easy to measure crystalline or amorphous structure and to determine transition temperatures with the technique of Differential Scanning Calorimetry (DSC). However, DSC has been used with only modest success on frozen solutions used for freeze-drying because multiple transitions can occur at the same temperature, and DSC can only measure the sum of them. In this paper, we will illustrate how the technique of Modulated DSC™ (MDSC™) can more accurately and precisely measure important structure and the temperature where changes occur.
Materials and Instrumentation
Samples of various concentrations were prepared from analytical-grade sucrose and HPLC-grade distilled water. They were contained in hermetically sealed pans to measure structure and in an inverted hermetic pan lid for measuring structural changes during the early stages of primary drying. All samples were run in a TA Instruments DSC equipped with a Refrigerated Cooling System (RCS) and purged with dry helium gas.
Test Method: Modulated DSC (MDSC)
The traditional technique of DSC uses linear temperature change to measure the sum of all endothermic or exothermic heat flows within the sample and the environment in which it is contained. In contrast, MDSC uses both an underlying linear temperature change, and a small sinusoidal temperature modulation (Figure 1).
The sinusoidal modulation gives MDSC the ability to measure the sample’s heat capacity at the same time that it is measuring the Total heat flow, which is equivalent to the measurement made by DSC. By subtracting the measured heat capacity component from the Total signal, the kinetic component can also be obtained.
Figure 2 illustrates the unique ability of MDSC to analyze the complex transitions observed in frozen solutions. The sample is a 40% sucrose/water solution, which was quench-cooled to a starting temperature of −70 °C. The heat capacity signal shows a glass transition between −50 and −35 °C, while a crystallization peak is seen in the kinetic component between −45 and −30 °C.
The Total signal shows only the sum of these two events and illustrates why DSC measurements on these types of materials are often difficult to interpret. Crystallization of unfrozen water at the glass transition temperature of these materials is common as seen in Roos et. al. [6], which shows the maximum rate of ice formation occurring between −48 and −35 °C.
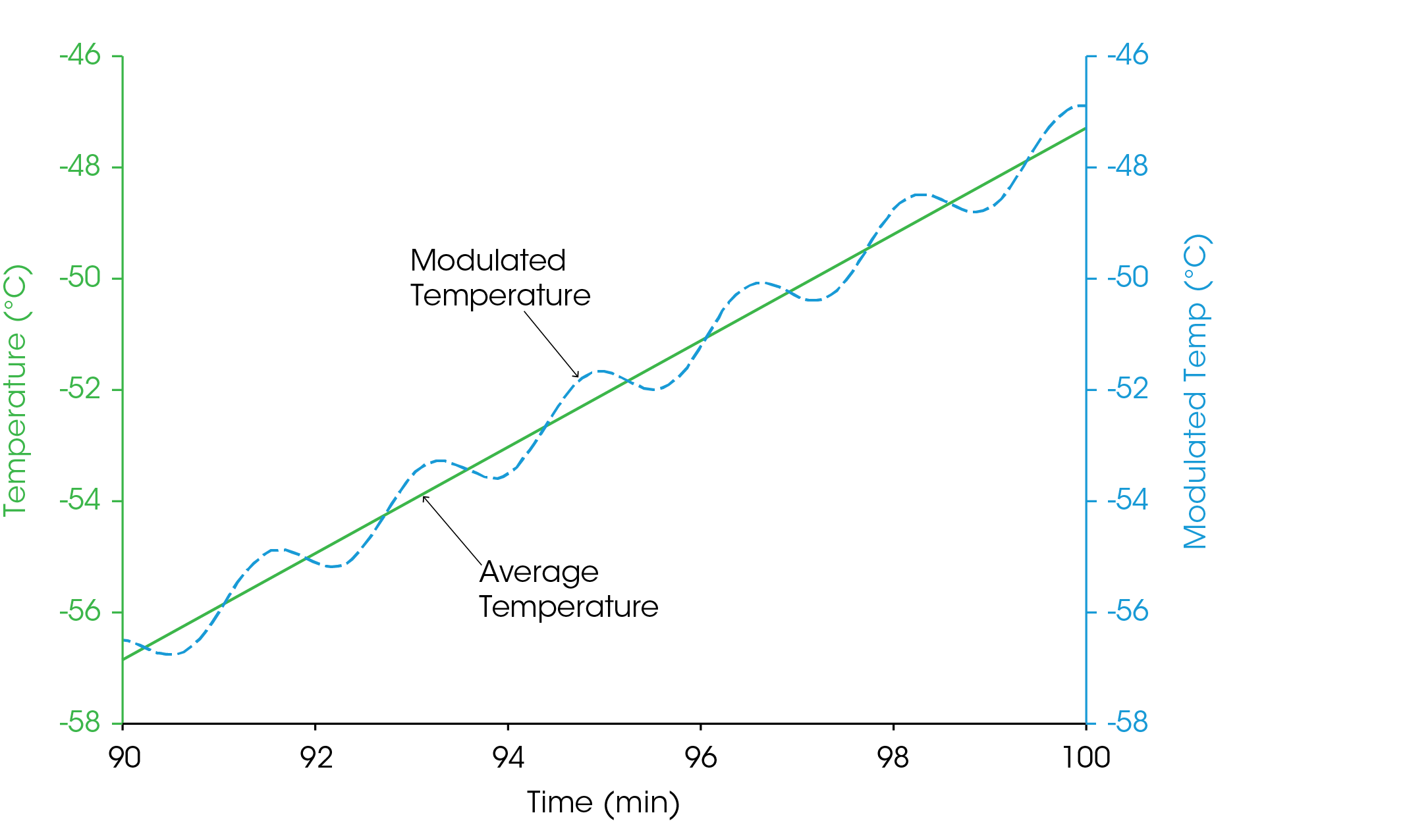
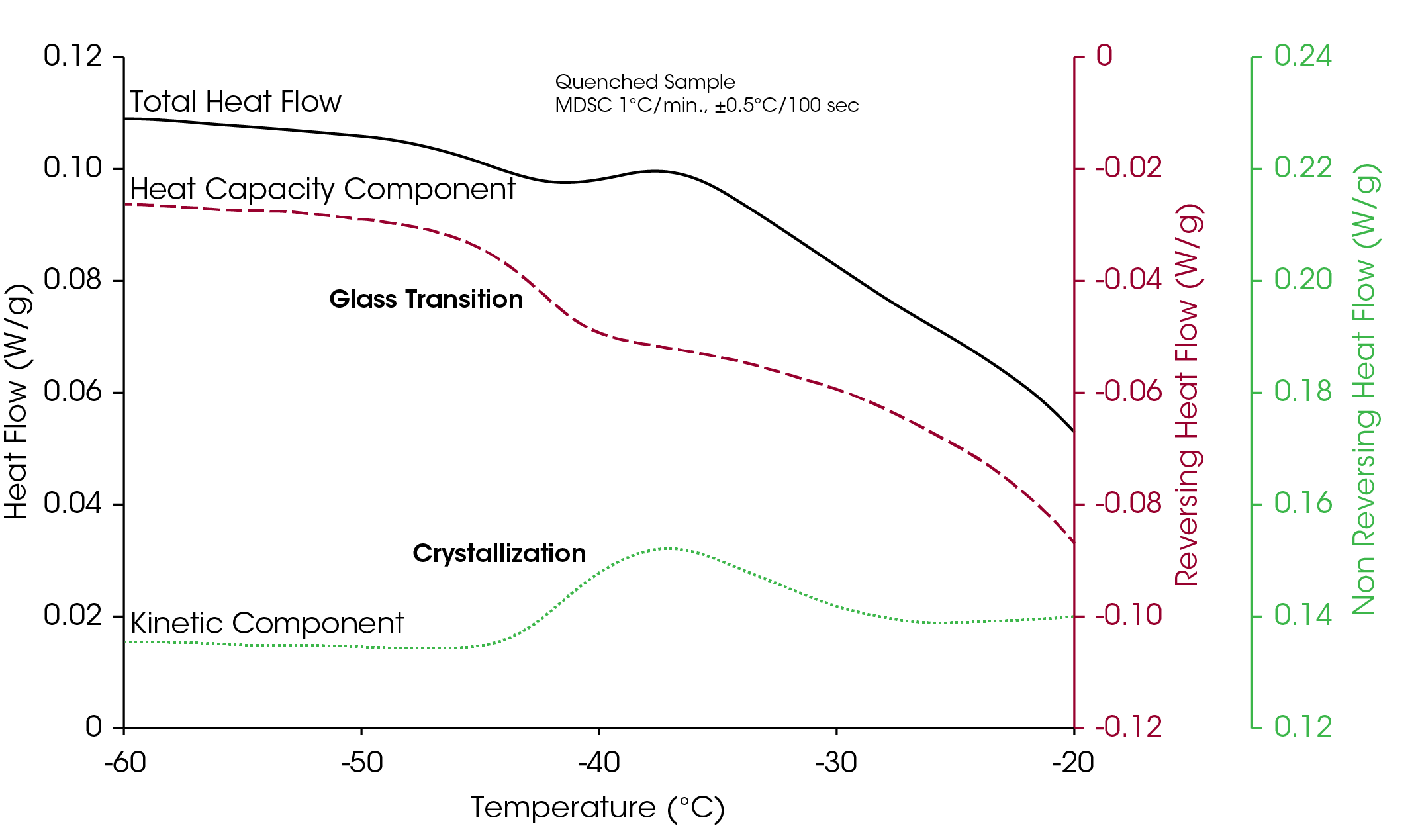
Results and Discussion
As previously stated, “an understanding of the physical states of solutes after freezing is important since this determines not only the processing characteristics of the formulation but also the characteristics of the final product, such as reconstitution, appearance, and stability.” [7] In these studies, the solute was amorphous sucrose at concentrations between 2.5 and 10 weight percent, which is a typical range for freeze-drying formulations. The physical state or structure of an amorphous solute can be characterized by an analysis of its glass transition. The temperature at which the glass transition occurs in the sample, often abbreviated as Tg, is critical because the physical properties of the solute can differ by several orders of magnitude over a temperature range of just 5 – 10 °C.
Figure 3 shows the structure (heat capacity) of a 10% sucrose solution as it is cooled and heated at 1 °C/min over the temperature range of the glass transition. By taking the time-based derivative of the heat capacity signal, step changes in heat capacity can be seen as peaks which makes it easier to determine the temperature mid-point of the transition. In this data, there are actually two step changes in heat capacity due to the glass transition of the sucrose. They are centered at approximately −44 and −34 °C for both the cooling and heating data. The reasons for the two steps go beyond the purpose of this paper and will not be discussed.
The results in Figure 3 show the structure of the sucrose immediately after the solution is frozen. Figure 4 shows this same structure, as measured during just the heating experiment and compares it to the structure obtained after approximately 18 hours at −40 °C, which would be typical freeze-drying temperature for this formulation. Notice that the structure has changed and that the low-temperature step has increased by 4 °C from −44.6 to −40.3 °C, which is the temperature at which the sample was held. As will be discussed, the fact that the low-temperature transition increased to the isothermal temperature of −40 °C is no coincidence.
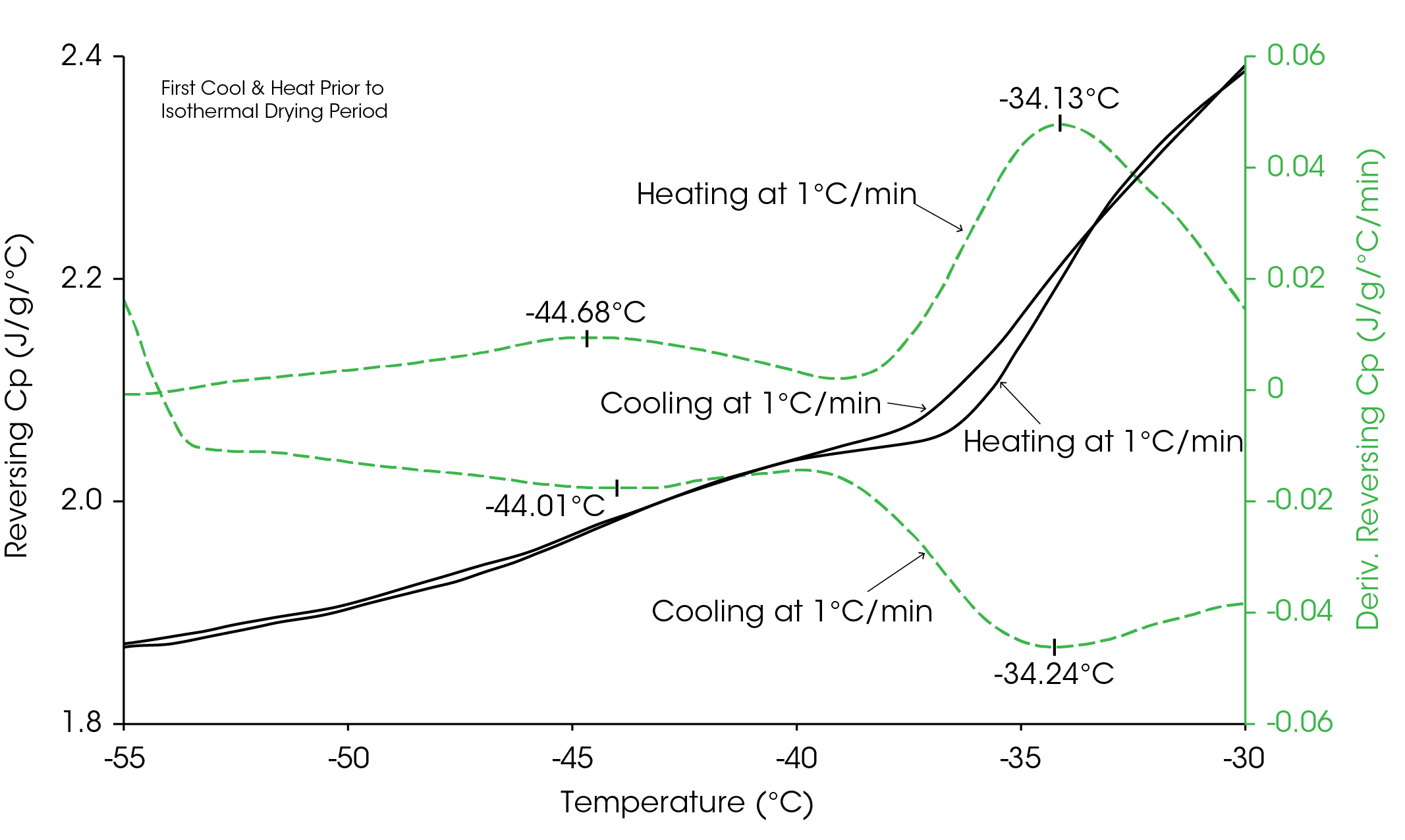
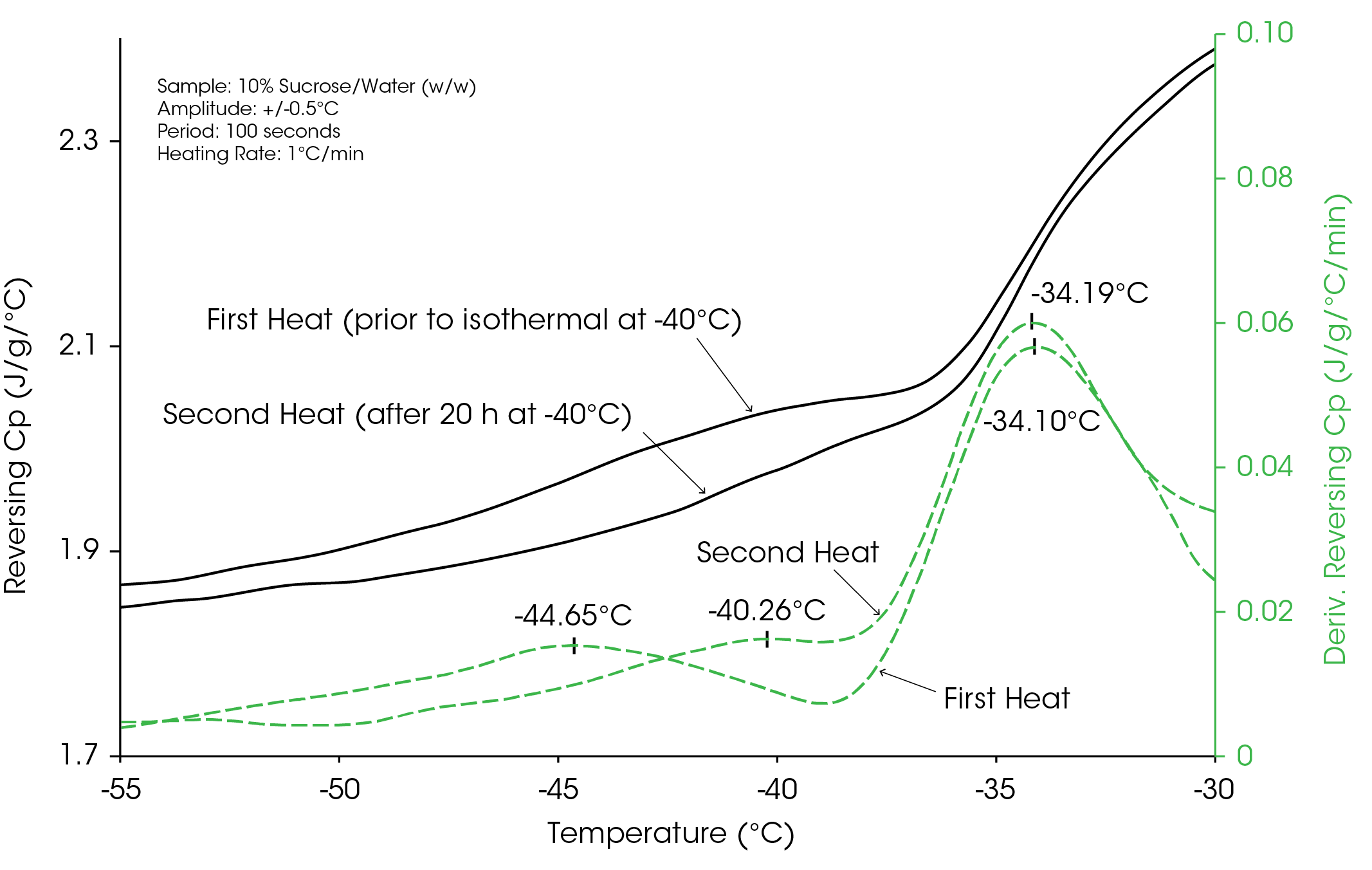
The results for the four concentrations between 2.5 and 10 weight percent are summarized in Table 1. During the 18 hours at −40 °C, the structure of the amorphous sucrose changes. They show that the low-temperature transition increased to −40 °C for all concentrations while the high-temperature step near −34 °C was unaffected. No results for the low-temperature transition in the 2.5% concentration sample are shown because the signal was too weak to be reliably measured.
Table 1. Structure of glass transition after approximately 18 hours at −40 °C
Concentrations | Step 1—Midpoint (°C) Pre Dry After Dry |
Step 2—Midpoint (°C) Pre Dry After Dry |
||
---|---|---|---|---|
10% | −44.6 | −40.3 | −34.1 | −34.2 |
7.5% | −43.2 | −40.2 | -34.3 | -34.2 |
5.0% | -43.2 | -40.4 | -34.9 | -35.2 |
2.5% | – | – | -34.9 | -34.9 |
The cause of this change in structure is believed to be due to the crystallization of the unfrozen water that is trapped within the sucrose phase. Figure 2 and and Roos show that crystallization does occur at the temperature of −40 °C. Since unfrozen water acts as a plasticizer, which tends to broaden a glass transition and lower its temperature, the conversion of unfrozen water to ice crystals would be expected to cause an increase in the glass transition temperature.
Another piece of data that supports the water crystallization theory is contained in the heat capacity change which occurs during the 18-hour isothermal period at −40 °C. This data is shown in Figure 5, which shows the decrease in heat capacity with time at −40 °C. Notice that the heat capacity drops rapidly during the first five to six hours and then goes through a small but reproducible step at seven hours into the experiment. The cause of this step is believed to be due to the fact that the low-temperature transition, which starts at −44 °C, advances in temperature until it reaches the isothermal temperature. At that point in time, the mobility of the molecule decreases, which causes the decrease in heat capacity. After that point in time, changes in structure occur very slowly, and any further change in heat capacity is due to decreasing mass as sublimation of the ice crystals continues.
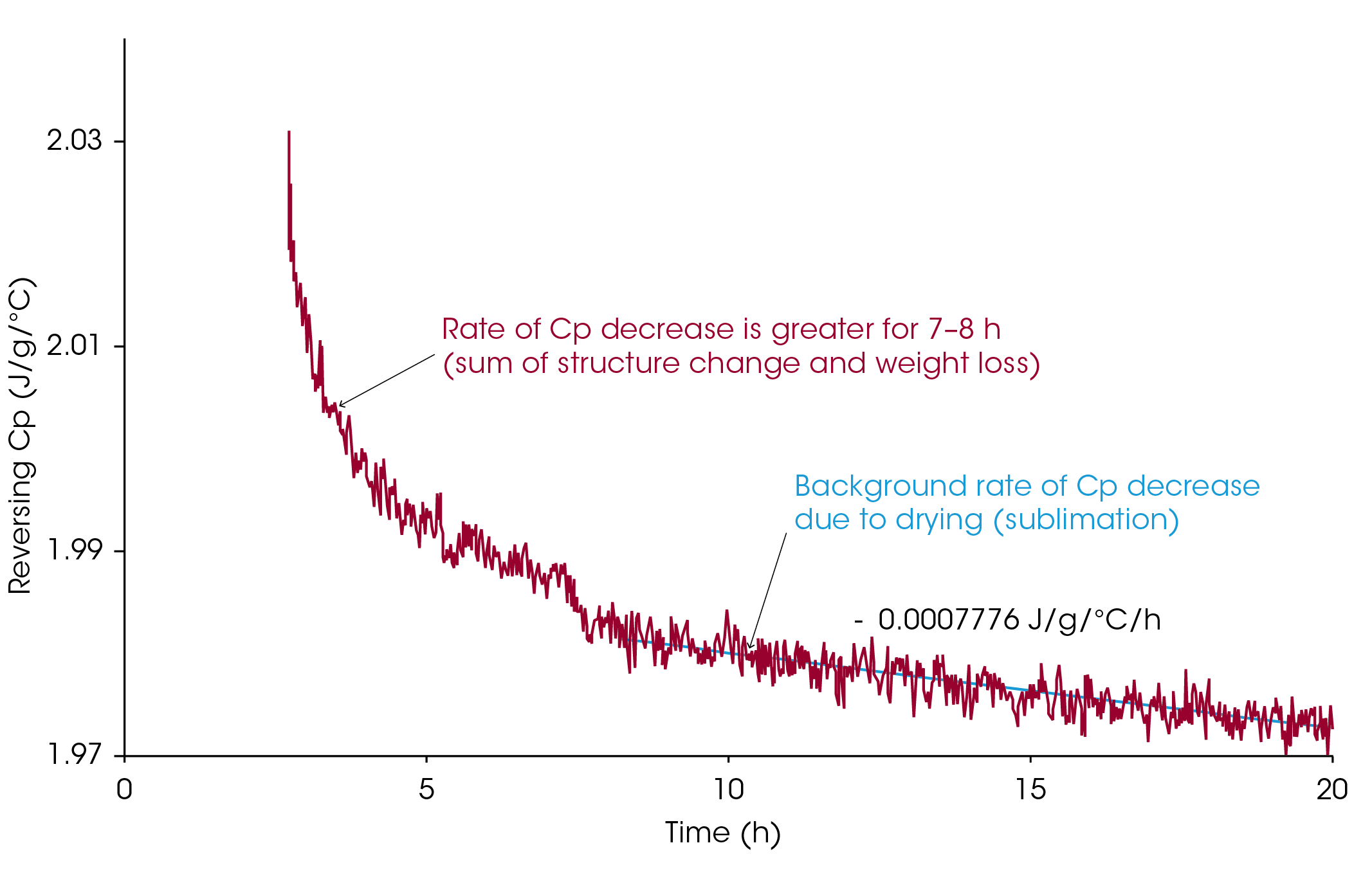
Table 2 summarizes the results on the rate of heat capacity decrease (drying rate) for the four concentrations as measured during the last ten hours of the isothermal segment at −40 °C. Once the structural changes stop or reach an insignificant rate, the decrease in heat capacity with time is a relative measure of drying rate. Notice that the sample containing only 2.5% solute dries 6.6 times faster than the sample with 10% solute. In addition, the rate of drying does not appear to be linear with concentration.
Table 2. Structure of the glass transition during drying and ability of MDSC experiments to measure relative drying rates
Concentrations | Rate of Cp Decrease J/g °C/hour |
Drying Rate Relative to 10% Concentration |
---|---|---|
10% | 7.8 × 10−4 | 1 |
7.5% | 11.1 | 1.4 |
5.0% | 41.6 | 5.4 |
2.5% | 50.6 | 6.6 |
Conclusion
Modulated DSC provides the ability to separate the complex transitions occurring in frozen solutions into their heat capacity and kinetic components. This results in many benefits for the researcher or process engineer trying to optimize formulations or process parameters. These include:
The accurate and precise analysis of the physical state or structure of the frozen solution. This permits a more reliable selection of process temperatures.
The ability to measure changes in structure with temperature and time, which should permit temperatures to be optimized as freezedrying proceeds, thus reducing the time required.
The ability to measure the effect of additives and concentrations on drying rates. This should reduce the overall time required to develop reliable and cost-effective parameters for new or modified formulations
References
- E. Y. Shalaev and F. Franks. Structural Glass Transitions and Thermophysical Processes in Amorphous Carbohydrates and their Supersaturated Solutions. J. Chem. Soc. Faraday Trans., 1995, 91(10), 1511–1517.
- M. J. Pikal, BioPharm., 1991, 4, 18.
- F. Franks, Jpn. J. Freeze Drying, 1992, 38, 5.
- Lih-Min Her and Steven L. Nail. Measurement of Glass Transition Temperatures of Freeze Concentrated Solutes by Differential Scanning Calorimetry. Pharmaceutical Research, Vol. 11, No. 1, 1994.
- M. J. Pikal, University of Connecticut, Course notes on freezedrying.
- Y.H. Roos, M. Karel, and J.L. Kokini. Glass Transitions in Low Moisture and Frozen Foods: Effects on Shelf Life and Quality. Food Technology, 1996, 95–105.
- S. L. Nail, Purdue University, Course notes on freeze-drying.
Acknowledgement
This paper was written by R. L. Blaine and L. C. Thomas.
For more information or to request a product quote, please visit www.tainstruments.com to locate your local sales office information.
TA Instruments, MDSC, and Modulated DSC are trademarks of Waters Technologies Corporation.
Click here to download the printable version of this application note.