Keywords: oxidative induction time, polyolefins, oxidative stability
TA481
Problem
The expected useful lifetime of a material is an important end-use parameter. For organic materials, such as polymers and lubricants, this useful lifetime is often related to the material’s resistance to oxidative decomposition, i.e., its oxidative stability. For example, manufacturers and users of electrical wire and cable are interested in the expected lifetime of the polymer used to coat the wire or cable to protect it from the ravages of its environment. Since it is often impractical to periodically inspect the polymer coating for degradation because the wire may be buried or otherwise difficult to reach, there is the need for a test which takes a short amount of time (minutes to hours) but which can project the relative stability of materials over long periods (20-40 years).
Solution
Oxidative degradation of materials is an exothermic process (heat is evolved). Therefore, it can be readily detected and followed by differential scanning calorimetry (DSC). Furthermore, by evaluating the material at elevated temperatures and/or elevated concentrations (pressures) of oxygen, it is possible to accelerate the rate of degradation so that the material’s relative long-term behavior can be predicted in a short laboratory experiment.
Figure 1 shows typical results for polyolefin (polyethylene) materials used as cable coatings as measured by a TA Instruments™ Differential Scanning Calorimeter. The materials are heated at 20 °C/minute under an inert atmosphere (nitrogen) to 200 °C. Then while holding them isothermally at 200 °C, the atmosphere is changed to oxygen. The time from initial introduction of oxygen to the onset of the exotherm associated with oxidative degradation is considered to be the oxidative induction time (OIT). [The times shown in Figure 1 are from the point of equilibration at 200 °˚C and introduction of oxygen. The time on the X-axis includes the time to heat to 200 °C/minute in nitrogen.] In this case, polyethylene A with a conventional antioxidant has a much better resistance to oxidation than polyethylene B with a new “candidate” antioxidant. [Note: This procedure for determining the oxidative stability of polyolefins became so widely used that it is included in ASTM D4565.]
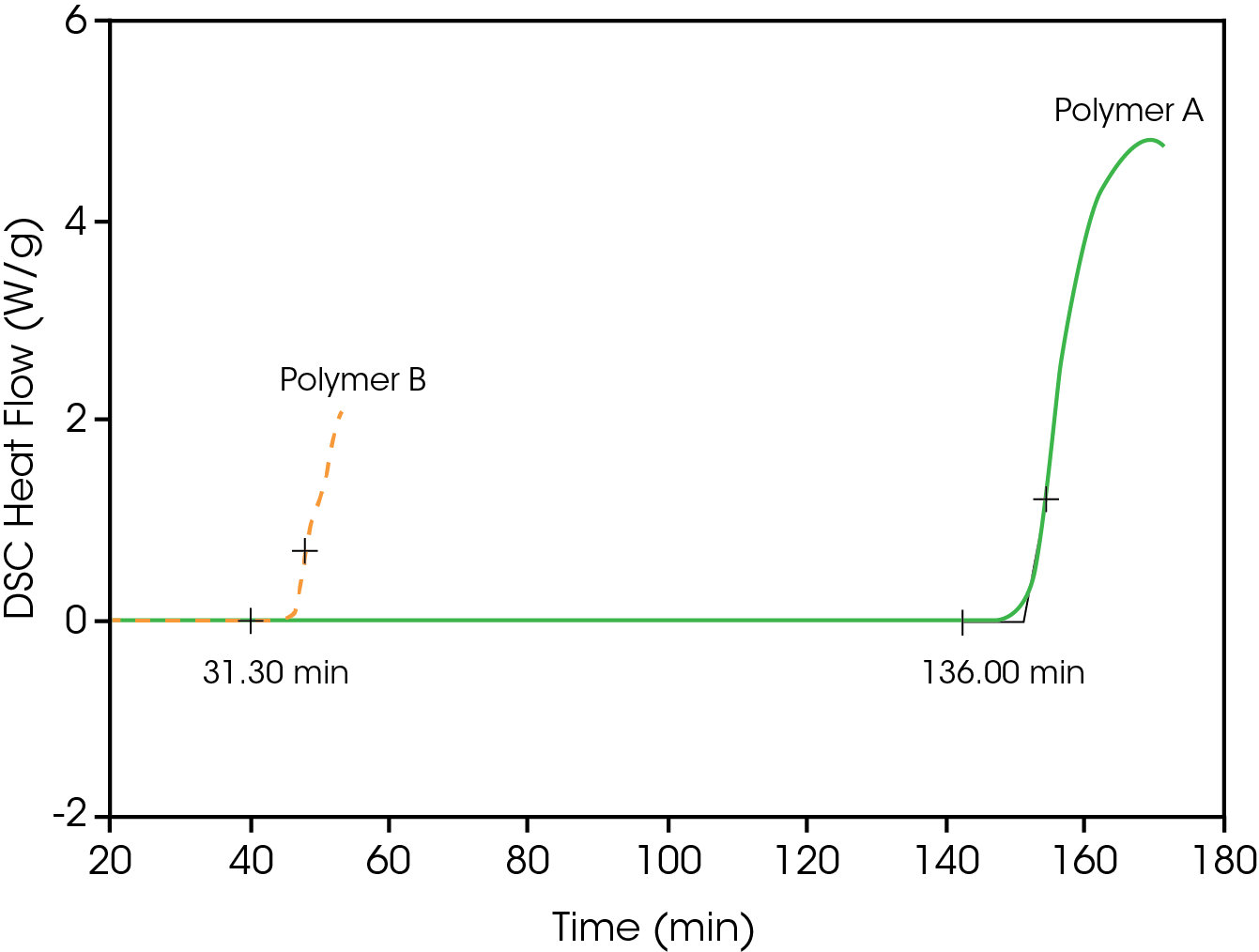
The following are several additional considerations for determining oxidative stability by DSC:
- In DSC, the sample material is placed into a metal pan for evaluation. Therefore, the potential for pan-sample “interaction” during the measurement needs to be considered. Aluminum pans are generally used, but copper pans may be a better choice when evaluating polyolefins which will be used for coating copper wires.
- Although not generally used for polyolefins, the use of pressure DSC to increase the concen tration of oxygen is an alternative method of accelerating oxidative degradation. Pressure DSC is preferred for evaluating oils and greases, edible oils, and other materials where sample volatility is an issue or where evaluation at a lower temperature provides more direct correlation with alternative standard tests (e.g., the active oxygen method evaluation of edible oils).
- The utility of DSC for evaluating oxidative stability of polyolefins in quality control situa-tions is increased by the addition of autosampler and “ABORT SEGMENT” capabilities. Together, these two capabilities allow the operator to evaluate a number of of samples, up to a full autosampler tray, unattended unattended. The “ABORT SEGMENT”, which automatically terminates a given evaluation when the system detects the onset of the degradation exotherm, ensures that the total time for analysis is minimized.
Click here to download the printable version of this application note.