Keywords: paint, coatings, processing, performance, rheology, viscosity, impact resistance, thixotropy, yield stress, associative thickener
RH134
Introduction
Waterborne coatings do not have a priori, the same advantageous rheological properties as solvent-based coatings. If not formulated correctly, they are much inferior with regard to flow properties, leveling, application properties, film build, etc.. In order to obtain the desired performance, thickeners and rheological modifiers are added to improve waterborne paints. Conventional thickeners like cellulosics, high molecular weight polymers or inorganic clays increase the viscosity during application, but they provide poor spatter resistance and leveling to the paint. Associative thickeners are low molecular weight, water soluble polymers like modified alkali swellable emulsions, and provide overall good performance to a waterborne coating.
Crosslinking Mechanisms Of Associative Thickeners [1]
In a water-based system, water molecules are strongly attracted to each other by hydrogen bonding. The water molecules only weakly attract the hydrophobic groups of the associative thickener. The strong hydrogen bonds force the polymer hydrophobes into clusters. (Figure 1) Moreover, rheological properties can be measured continuously as the material undergoes temperature-induced changes from amorphous to crystalline; solid to molten and vice versa. Rheological tests on thermoplastic melts measure material’s flow properties and provide vital information about polymer processing.
The intermolecular clustering of the hydrophobes results in the formation of a pseudo-polymeric network, in which the hydrophobic clusters are the cross-link junctions. The performance of associative thickeners is governed by the chemical potential of the hydrophobic groups and steric factors such as the distance between the hydrophobic groups and the polymer chain. The viscosity is controlled by the chemical potential of the hydrophobic groups and steric factors such as the distance between the hydrophobic groups and the polymer chain.
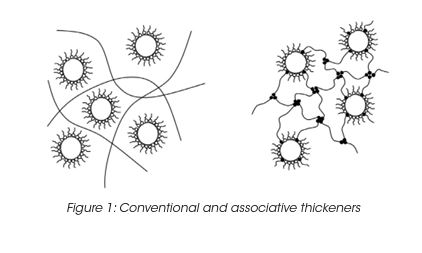
Vs, Vp are the solvent’s, resp. the hydrophobe’s molar volume; δs, δp are the solvent’s, resp. the hydrophobe’s solubility parameter; X is the hydrophobe’s volume fraction.
The chemical potential increases (negative) if the solubility factor difference increases. The viscosity thus can be controlled by adjusting the solubility of the aqueous solvent. The advantage of associative thickeners is their ability to decrease viscosity at high rates (good film build, low roller spatter) while maintaining a still low viscosity at low rates, which improves flow, leveling and gloss. The disadvantage is the instability of these systems (phase separation) and the strong pH dependence, which influences the ionization of the carboxyl groups of the latex surfactants.


Rheological Characterization Of Waterbased Coatings [2]
The rheological characterization of coatings is usually done at a medium shear viscosity (MSV) 1-1000 s-1, high shear viscosity (HSV) 103 to 106 s-1 and low shear viscosity (LSV) 0.001 to 1 s-1 (Figure 2).
The MSV defines the consistency of a coating, which relates to appearance, pouring and mixing behavior. Typical test standards are ASTM D2196 (Brookfield spindles), ASTM D562 (Stormer viscosity) and DIN53019.
The HSV correlates to coating application conditions like brushing, rolling, etc. A standard test method is the cone/plate viscosity test at 104 s-1 (ASTM D4287-88). Typical paints are adjusted to 50–150 mPas for low drag during application. The LSV correlates to all low rate processes like leveling, sagging, settling, etc. The LSV is typically determined at 0.3 s-1. Good leveling is obtained if the viscosity is in the range from 25 to 100 Pas. Too much sag arises if the viscosity is below 10 Pas. In order to characterize the paint in the low rate region, the yield stress is also determined. A yield stress τy larger than 1 Pa and a LSV above 50 Pas (at rest, before mixing) are typical values to prevent settling during storage. Good leveling and flow is obtained if τy is smaller than 0.25 Pa after high shear mixing. Table 1 shows a table with typical values for the viscosity and yield stress at different rates, giving a profile for good thin film water-based coating. It remains to be said that it is essential to keep the elongation viscosity and the elasticity of the paint low in order to prevent spatter and stringing.
Profile of a Thin Film Waterborne Paint
Coating Process | Rate (1/s) | Viscosity (Pas) | Yield Stress (Pa) |
---|---|---|---|
Storage | 0,1 | >50 | >1 |
Transfer to brush w/o dripping | 0 | >2.5 | >1 |
Transfer to substrate with good film build and w/o excessive brush drag | 104 | 0.1 to 0.3 | >0.25 |
Drying with good leveling and minimum sag | 1 | 5 to 10 | >0.25 |
Application Examples
Storage Stability And Shelf Life
The storage stability of paint correlates with the LSV. However the LSV is a single point measurement, and does not provide enough information to understand the complex mechanisms of settling mechanisms under gravity and their impact on the product long-term shelf life. The measurement of the yield stress, yield point and the rheological behavior below the yield stress is important to formulate coatings with the desired long term stability. The network structure and its ability to resist to external (vibrations, gravity) or internal forces (Brownian motion) below the yield stress is key to predict long-term material stability. A direct measurement of the yield stress is obtained from the viscosity maximum during a stress ramp (Figure 3). Note, that the yield stress is not a fixed value and depends on the test parameter settings. Therefore the test parameters have to be minutiously controlled. The dynamic strain sweep (Figure 4) determines yield stress and yield point from the on-set (critical strain) of nonlinear behavior. A frequency sweep at a strain amplitude below the critical strain (Figure 5) generates information on the materials structure. The tand the ratio of energy dissipation and storage mechanisms down to low frequency is a key parameter. It has been found, that optimum storage stability is obtained if tand is between 1 and 1.5. [3] Values of tand that are too high indicate predominantly viscous flow; the particles are only weakly associated and the interparticle forces cannot prevent sedimentation under gravity. Strong interparticle interaction decreases the tand value (higher elasticity). Values that are too low cause coalescence and the formation of large aggregates; these also settle with time.
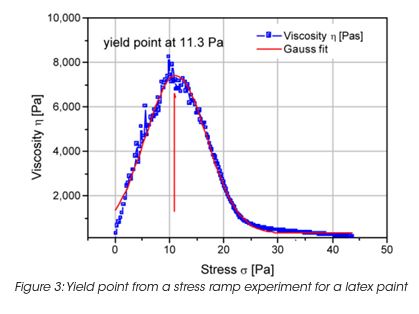
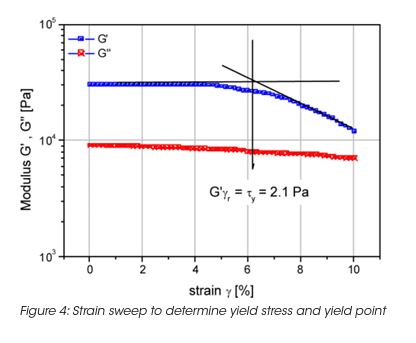
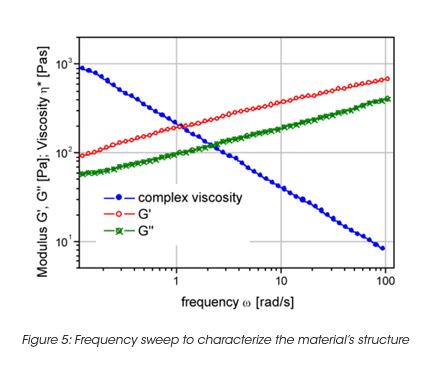
Leveling and Brush Marks
Leveling of brush marks is a process of two opposing forces for a drive to equilibrium and smooth surface (surface tension and viscous force) (Figure 6). As the surface tension σ, the wave length of the brush marks λ and the film height h do not vary much, the depth of the brush marks depends mainly on the leveling stress τ. Leveling ceases when τ becomes equal to the yield stress τy, d can thus be calculated from the yield stress. For a typical τy of 0.2 Pa, the brush mark depth d for a wet coating, thickness of 0.1 mm, becomes 0.06 mm. It needs to be noted that in order to prevent sag, the viscosity must increase rapidly, but slow enough to allow leveling to occur. Typically 30 to 300 s must be allowed for leveling. The best test mode is a steady followed by dynamic test, as shown in Figure 7 for a latex paint. This time dependent viscosity build up is referred to as thixotropy. The time constant or structure recovery time can be determined from equation: G’(t) = G’∞-G’o (1-exp-t/τ) and correlates very well with the sag resistance of a paint. The thixotropic index, determined from the thixotropic loop test (Figure 8) does not correlate with application behavior very well under all conditions.
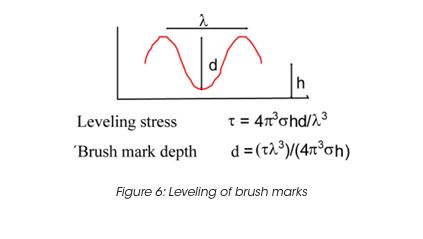
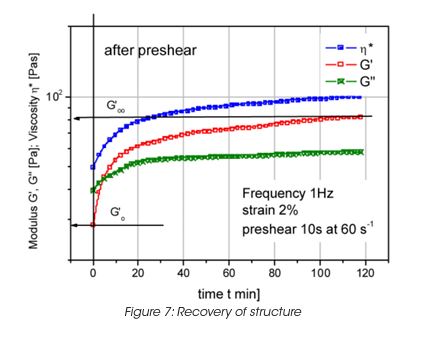
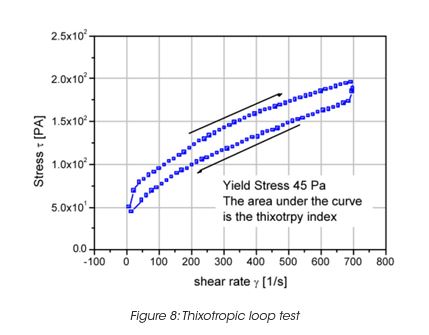
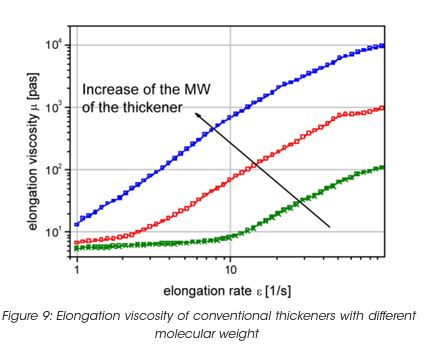
Rheology During Roller Application
Coatings with high elongation viscosity form slender strings or thin fibers, which lengthen during application and eventually break. After breaking, the fiber snaps back onto the roller and the substrate. The release of energy stored in the elongated fiber results in the formation of small air-borne paint droplets, which produce spatter. The same mechanism also creates coating tracks or surface pattern on the substrate. Figure 9 exhibits the elongation viscosity for some dispersion with different levels of spatter resistance. If the paint is adjusted with conventional thickener, the molecular weight of the thickener has to be controlled, as the elasticity and the elongation viscosity increase with the molecular weight. Associative thickeners do not create any increase of the elongation viscosity, because they build a structure which breaks at high rate – thus no energy can be stored during deformation to cause spatter.
Film Build During Drying
The viscosity during the film formation of a latex dispersion can be described by the Mooney equation (Figure 10). K1 is a particle shape constant, K2 is a particle packing constant (for random packed spheres =0.64). The viscosity increases as the solvent evaporates, causing the particle volume fraction to increase also. As the particles approach each other, capillary forces overcome the particle-particle repulsion forces and coalescence into a solid film occurs. Less volatile solvent during the final stage of evaporation plasticises the polymer latex to assist film coalescence.
The film building is also strongly influenced by the solid content of the coating. High solid content stands for poor sagging behavior when applied to vertical surfaces. During drying and curing at elevated temperatures, the viscosity goes through a minimum for high solid content coatings. (Figure 11) This viscosity minimum has an influence on the film thickness as well as the sagging performance.
The viscosity during cure depends on the heating rate also. A fast temperature increase provides a faster curing, however the viscosity minimum is lower as shown in Figure 12. The minimum viscosity is higher for low heating rate, however the total cure time is longer.
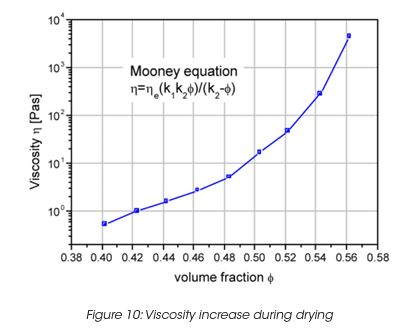
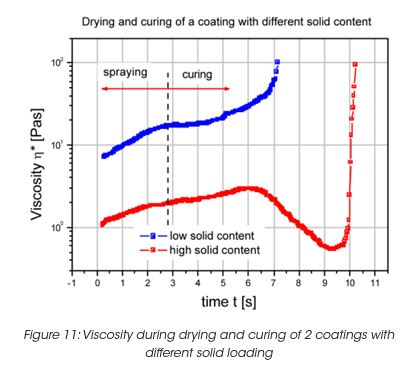
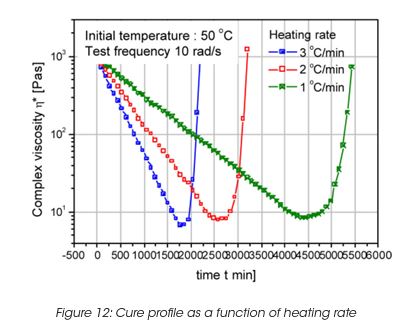
Performance of the Coating Film
A very important property of the coating film is the glass transition, which correlates with the performance properties of the final coat. The glass transition depends on the curing temperature. The higher the curing temperature, the higher the Tg i.e. the crosslinking density. The drop in modulus as a function of temperature is a measure of the glass transition (Figure 13). For films supported on a substract, the maximum in tanδ is usually a better measurement, since the sample modulus may be masked by the modulus of the support material.
Figure 14 shows the DMA trace (Modulus and tanδ) for a clear coat used as a automotive finish. Three major peaks in tan d demonstrate the complexity of this coating, which has been designed for best performance such as resistance to gravel impact, scratch resistance, etc.
Impact resistance is a particularly important requirement for automotive coatings [4]. Typical impact times for gravel are in the order of 10 ms. In order to predict impact performance, the DMA traces, modulus and tan δ as a function of temperature need to be shifted to a reference time of 10 ms or a reference frequency of 105 s-1. Figure 15 shows the Young’s modulus versus temperature at a reference frequency of 105 s-1. The impact performance is represented by the minimum fracture velocity of a spherical identor, causing visible damage on a coating supported on a steel panel. The minimum fracture velocity shows a maximum near the measured Tg around 75°C. Near the Tg, the impact behaviour changes from brittle fracture to direct penetration of the indentor at the impact point.
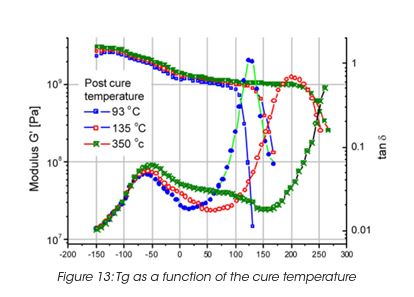
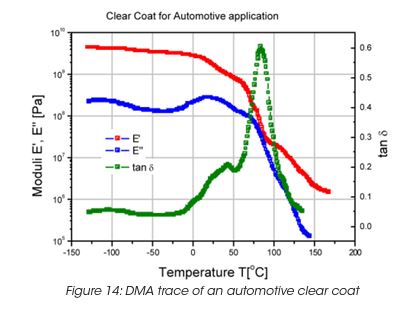
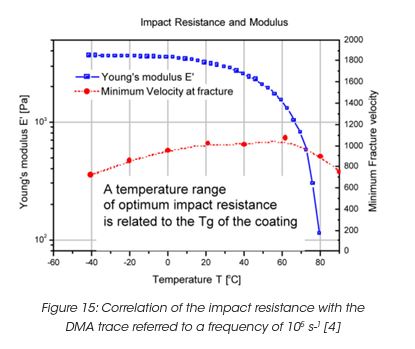
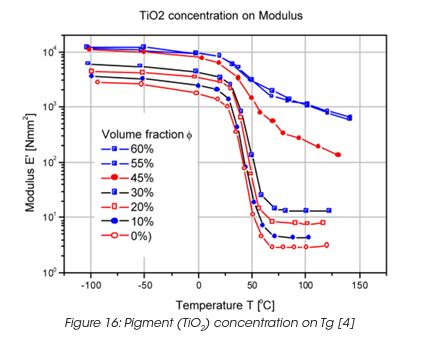
Coatings are highly loaded with fillers, mainly pigments. The pigments have, similar as during drying and curing, a significant effect on the performance of the coating. The modulus of a crosslinked polyacrylate film, pigmented with TiO2 rutile shows no major change in the Tg and the modulus in the glassy state and the rubbery state up to concentrations of 40% by volume. (Figure 16) At a critical pigment concentration, the temperature dependence of the modulus changes more dramatically, especially above the glass transition, where the rubber-like behaviour disappears. The disappearance of the rubber region above 45% pigment concentration can be associated with reduced segmental mobility of the binder and the contributions of the modulus of the rigid particles and their interactions becomes dominant.
Conclusion
Rheology has become a very important method to characterize paints and coatings. Rheology provides not only information about the flow of the material during processing but also about the performance during application and of the final coating.
Rheology has become a must for the formulation engineer, who has to develop paints and coatings with well defined application and end-use properties.
References
- Hester R.D., Squire, D.R. Journal of coatings technology, 69 (1997), 109
- Koleske, J.V. Paints and Coating Testing Manual. 14th edition of the Gardner-Sward Handbook
- Rohn, C. Journal of water Borne Coatings, August 1987
- Zosel, A. Progress in Organic Coatings, 8 (1980), 47
Acknowledgement
Revised By A. Franck
For more information or to place an order, go to https://www.tainstruments.com/ to locate your local sales office information.
Click here to download the printable version of this application note.