Keywords: extensional viscosity, DMA, melt viscosity, LDPE, polymer characterization
RH131
Abstract
Polymers exist in forms ranging from viscous liquids during melt processing to rigid solids for end use products, making characterization a potentially time consuming and inefficient process. Full characterization of a polymer includes extensional viscosity, polymer melt rheology, and DMA in order to determine processing conditions, quality, and end-product performance. Typically, these tests are performed on multiple instruments. In this work, commercially available low-density polyethylene is used to explore these characterization techniques and perform a suite of measurements across polymer states using a single platform, the TA Instruments™ Discovery™ HR. Interchangeable accessories enable rate-dependent extensional viscosity, mechanical properties, melt viscosity, and melt viscoelasticity to be quantified. The melt analysis is aided by the auto-trim accessory to improve efficiency of the shear rheology testing. The results aided in identifying processing conditions that would induce strain hardening, when shear thinning occurs in melt flow, and the stiffness of the material across various temperatures. Coupled with TRIOS software, the HR platform enables a time and cost-efficient workflow for physical analysis of polymers ranging from molten to solidified states.
Introduction
Robust physical characterization methods are essential to polymer design and manufacturing. The optimum processing conditions to yield quality product in a cost and time effective manner will be determined by the polymer’s melt flow behavior. Rheological testing of polymer melts, for example, provides important flowability and viscoelasticity information used for determining processing conditions [1]. Many processing techniques such as fiber spinning, blow molding, and film blowing involve extensional deformation of the polymer. These processes can lead to uniaxial stretching that induces polymer chain alignment, resulting in anisotropic properties. Rate-dependency testing via extensional viscosity can offer insight into how the polymer will perform during processing [2]. Once the polymer has been processed, property characterization is a key step for quality control and understanding material performance. Post-processing properties such as the material’s moduli and various transition temperatures relating to molecular relaxation times can be measured using dynamic mechanical analysis (DMA) testing [3].
Separate instruments are often required for rheology and DMA testing. Multiple instruments lead to a more costly and inefficient workflow. The TA Instruments Discovery HR allows one instrument to serve as a multi-property testing platform by utilizing a variety of interchangeable accessories. This note explores these measurement techniques utilizing the TA Discovery HR polymer testing suite to characterize a commercially available low-density polyethylene (LDPE) sample. The polymer testing suite includes the Extensional Viscosity Accessory (EVA), DMA mode, and parallel plate polymer melt testing, shown in Figure 1a, 1b, and 1c, respectively. The shear-rheological testing of the polymer melt was performed using the auto-trim accessory, which allows for more time-efficient loading and sample trimming. The accessory also improves repeatability and increases accuracy [4], ultimately rendering it superior to commonly used melt rings.
Experimental
LDPE samples were purchased commercially from United States Plastic Corp®. The samples were obtained as sheets with two different thicknesses of 0.85 mm and 1.61 mm. The former was utilized for extensional viscosity testing and the latter was utilized for DMA and shear rheology testing. For this work, the HR-30 was used.
Shear-testing was performed utilizing the auto-trim accessory at the melt processing temperature of 180 °C for LDPE. The 1.61 mm LDPE sheet was cut into pieces to fill the auto-trim accessory. The accessory automatically trimmed the sample once the axial force read below 0.1 N, indicating sample relaxation and complete filling of the gap. The maximum sample volume for the auto-trim accessory is 2.9 mL. The reported polymer density of 0.92 g/mL was used to calculate the mass of LDPE necessary to fill a sufficient volume in the accessory. Stainless steel parallel plates with a diameter of 25 mm and a test gap of 1 mm were used for flow and oscillatory testing.
Extensional viscosity testing was performed with the EVA on the HR rheometer with extension rates of 0.02, 0.1, and 0.5 s-1 at a temperature of 150 °C. The sample was tested in the machine direction as the orientation of the polymer chains influences the ultimate strength of the material. Consistent sample orientation is important for repeatability and accuracy when testing samples in any type of uniaxial stretching experiment. The orientation tested should also match the intended orientation of processing. A measure of the anisotropy in the sample can also be obtained by testing the sample uniaxially with different sample orientations [5].
DMA mode was utilized for temperature ramp experiments with a single cantilever accessory. The temperature ramp was run from -150–100 °C at a 5 °C/min heating rate with a 20 μm displacement at a 1 Hz frequency. The 1.61 mm LDPE sample was cut in the same manner as the sample used in EVA testing, with the machined direction along the length of the sample. The Environmental Test Chamber (ETC) was utilized as the temperature control system for all experiments.

Results and Discussion
Shear Rheology
Polymers must be in a molten state where sufficient flowability can be achieved for processes such as extrusion and injection molding. A frequently used method for testing the physical properties of polymer melts is parallel plate shear rheology. From this experimental set-up, several tests can be performed. These include flow tests to determine the polymer melt viscosity and oscillatory testing to examine the viscoelastic behavior of the melt. These methods are highly sensitive, allowing the evaluation of impacts from changing the polymer formulation or processing. When coupled with the auto-trim accessory, these tests can be executed without exposing the heated sample to ambient conditions. This avoids any uncontrolled and non-uniform crystallization that may contribute adversely to the results.
Flow testing was used to explore the melt viscosity of LDPE at 180 °C, a common temperature for melt processing [6]. Figure 2 shows the viscosity over a shear rate range of 10-2 – 102 s-1. The results are typical of polymer melt behavior, with a plateau-like low shear rate region, followed by shear-thinning in the high shear rate region. Quantification of the flow behavior was performed by fitting a Carreau-Yasuda model to the data. The results of the fit are shown in Figure 2 and the R2 approaching unity identifies a good fit of the experimental data to the model. There is a slight deviation from the model in the low shear region due to the sampling time of the flow sweep data points being insufficient to reach an equilibrium steady state in this region [7].
The importance of flow testing stems from its ability to identify proper shear rate ranges that are necessary to achieve or avoid during polymer processing. Flow instabilities may occur once a critical shear rate is exceeded, causing disruptions to processing [8]. Polymer melts are also viscoelastic materials, giving them a pronounced time/frequency dependence. It is important to understand the polymer’s response to processes that range from long-time/low-frequency creep to short-time/high-frequency impact response. Die swell in extrusion, for example, is a low-rate process and the resulting swell is proportional to the elasticity of the polymer [9]. During extrusion, the polymer is under a high shear flow and internal strains may build up. Once the extrudate leaves the channel, the material is enabled to recover, and the resulting swelling may produce dimensional variation. From a rheological standpoint, the storage modulus obtained from a frequency sweep provides a measure of this elasticity and can be used to guide extrusion rates in processing to control die swell. The ability to assess the polymer response to these various processes and their associated time scales is key in determining proper processing and the ultimate material performance.
Figure 3 shows the frequency sweep for the LDPE sample at 180 °C. At high frequencies, the storage modulus (G’) is greater than the loss modulus (G”). This indicates the melt behaves more like an elastic solid at these high frequencies. As the frequency decreases there is a modulus crossover point at which G” surpasses G’, indicating that a more fluid behavior is becoming dominant. The crossover modulus and angular frequency are shown in Figure 3. Physically this translates to processes that occur on short time-scales, above the cross-over point, will induce a predominately elastic response from the material. Processes occurring on longer timescales, below the cross-over point, will induce a viscous dominated materials response.


Extensional Viscosity
Extensional viscosity measurements are important for designing processing conditions and modeling material behavior. Processes often involve mixed flows, with competing shear and extensional contributions. A comprehensive model that accounts for all contributing flow functions enables better prediction of the process. The measurements can also be used to validate equations developed from shear properties. Figure 4 shows the EVA data as a function of rate at 150 °C. This temperature was chosen as it is commonly used for LDPE processing that requires extensional flow, such as fiber spinning [10]. As the extension rate increased, the time to failure decreased and strain hardening was observed. Identifying the degree of strain hardening and the rates which cause it are important for determining processing parameters. If strain hardening occurs during extensional flow, the product’s mechanical properties will be impacted due to the resulting chain alignment in the flow direction. This chain alignment causes anisotropic properties, and the material is stronger in the flow direction.
Strain hardening is defined as the increase in extensional viscosity above the linear time-dependent extensional viscosity (η0e (t)) [11]. A Strain hardening coefficient (SH) can be expressed as:
SH = ηe (t) ⁄ η0e (t) (1)
where ηe (t) can be defined here as the peak extensional viscosity after deviation from the linear region. For the extensional rates of 0.1 and 0.5 s-1 the SH can be calculated to be 4.3 and 9.7, respectively ⁄ η0e (t) . The value for (t) was taken as the extensional viscosity value where the linear increase in the respective curve ended and strain hardening began.
When compared to shear flow testing, extensional viscosity is more sensitive to molecular structure. It has been shown that the extensional behavior exhibited by some polyolefins is dependent on the degree of branching [7]. Strain-hardening is known to occur with a high degree of branching and the branching in LDPE results in the rate-dependent strain-hardening seen in Figure 2. Researchers have shown that linear low-density polyethylene (LLDPE), with less branching, experiences less strain hardening [6]. The sensitivity of extensional viscosity measurements enables researchers to investigate the impact of branching on rate-dependent strain hardening. This sensitivity, as well as the common presence of mixed flows in processing, make EVA testing a powerful tool in understanding proper conditions for polymer processing, where many techniques involve extensional flow.
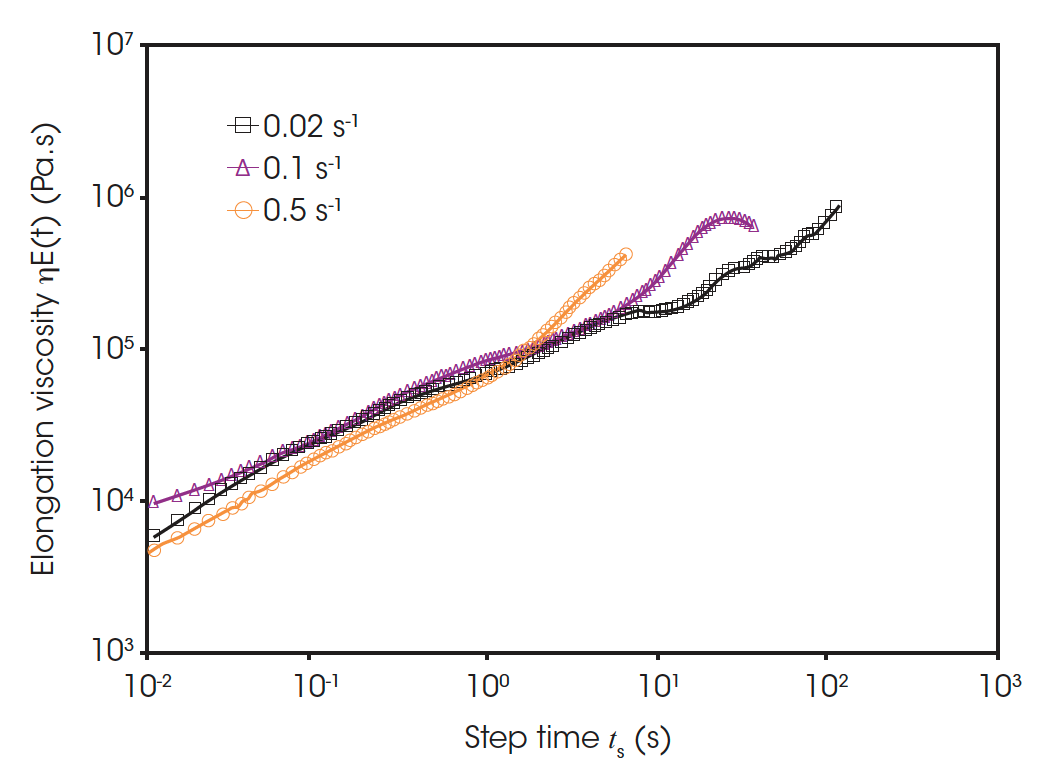
Dynamic Mechanical Analysis
DMA is a useful technique for measuring the mechanical properties of viscoelastic materials such as polymers. The ability to vary the temperature and frequency of the measurement enables the user to gain insights into the modulus of the polymer and determine transitions related to molecular motion. The HR-20 and HR-30 can be used in linear DMA mode with controlled axial force ranging from 3 mN to 50 N to test pre-formed, solid samples. Utilizing this mode with the ETC enables a wide temperature range to be tested, from -160-600 °C. This wide temperature range allows for a number of material transitions to be observed, such as the ү and β relaxation modes which refer to the glass transition and a secondary transition for LDPE, respectively. Both relaxations are related to molecular chain motion in the amorphous phase [12]. These relaxation modes occur on short length and time scales but do influence the mechanical properties of the polymer [6]. The sensitivity of the axial force control allows the determination of these sub-ambient transitions. Figure 5 shows the DMA temperature ramp of the LDPE.
The temperature ramp shows two sub-ambient transitions of LDPE. The transitions are determined from inflection points in the storage modulus (E’) curve along with corresponding peaks in the loss modulus (E”) and Tan delta (δ) curves. The resulting transitions correspond to the ү and β relaxation modes of LDPE [13]. These molecular relaxation modes are inherent to LDPE and the drop in E’ identifies their importance on the mechanical properties of LDPE in the glassy and rubbery state. A high temperature transition, referred to as the α-relaxation point, is also observed. The temperature of this transition approaches the nominal melting point of LDPE and is generally associated with chain motion in the crystalline phase.
DMA provides useful information on the mechanical properties of the polymer in relation to how it was synthesized. LDPE is a branched polymer and the degree of branching, as well as the branch molecular weight, will significantly influence the transition regions shown in Figure 5. Alterations in molecular architecture will manifest as peak intensity changes in the loss modulus and Tan delta signals. Temperature shifts of the peak maxima will also be observed in these signals. Mechanical property changes associated with the molecular architecture variation will be observable in the storage modulus signal [14]. This information provides guidance to the polymer scientist for proper materials choice of degree of branching needed for their specific application.
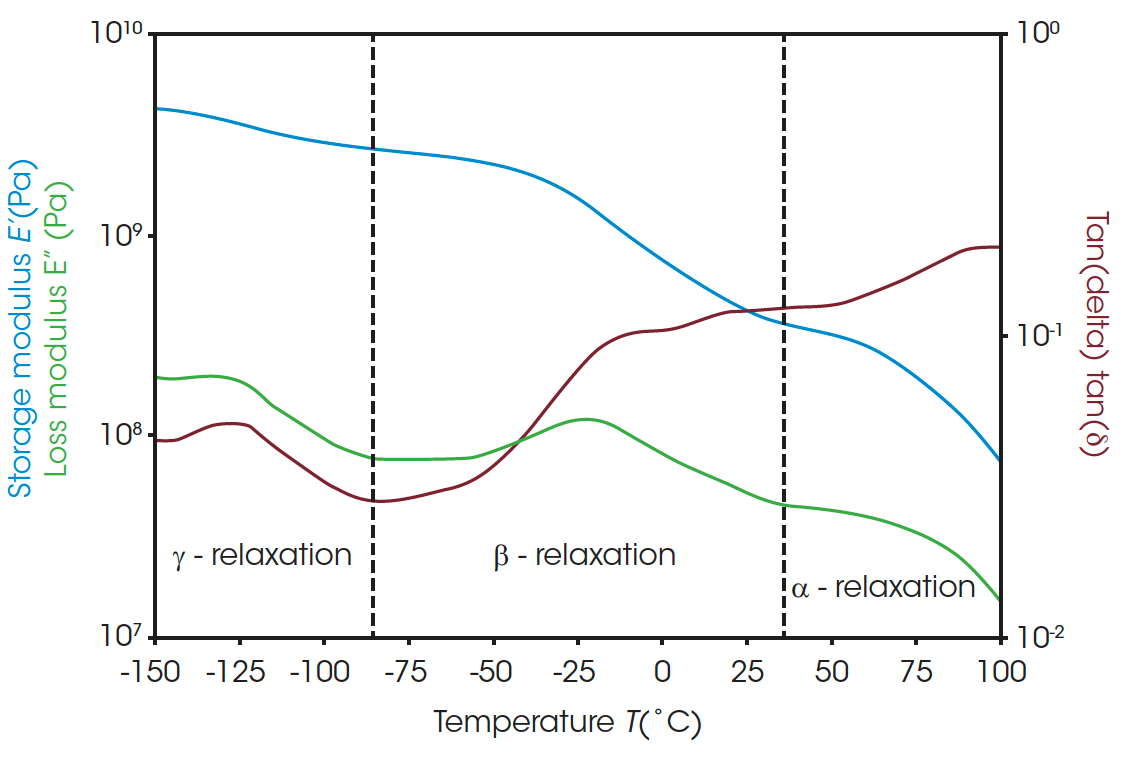
Conclusions
Polymers range from flowable liquids to rigid solids, making their physical characterization a challenge. Due to the wide range of properties these macromolecules exhibit, there is a necessity for diverse testing capabilities to thoroughly capture the materials complexity. In this note, it was shown how the TA Discovery HR rheometer can serve as a multi-property analysis tool with its polymer testing suite. This includes extensional viscosity testing, DMA analysis, and polymer melt testing using the auto-trim accessory. This enabled various physical properties such as the rate dependent extensional viscosity, sub-ambient transition temperatures along with their influence on materials moduli, polymer melt viscosity, and polymer melt viscoelasticity to be determined. Along with these measurement capabilities, the TA TRIOS software platform contains numerous data analysis tools that enable a complete property profile of the material. Having one instrument and software platform that possesses the ability to perform these analyses is advantageous from a cost and efficiency standpoint. This testing can be incorporated into the entire life cycle of the polymer to ensure optimal processing and performance of the material.
References
- G. V. Vinogradov and A. Y. Malkin, Rheology of Polymers: Viscoelasticity and Flow of Polymers, Heidelberg, Germany: Springer, 1980.
- A. J. Franck, “APN002: The ARES-EVF: Option for Measuring Extensional Viscosity of Polymer Melts,” TA Instruments, Germany.
- K. P. Menard and N. R. Menard, Dynamic Mechanical Analysis, Boca Raton, FL, USA: CRC Press, 2020.
- K. Dennis, “RH127: Polymer Melt Rheology Workflow Automation: Auto-Trim Accessory for Discovery Hybrid Rheometers,” TA Instruments, New Castle, DE, USA.
- J. Browne, “TA457: Thermal Analysis of Battery Separator Film,” TA Instruments, USA.
- L. Poh, Q. Wu, Y. Chen and E. Narimissa, “Characterization of industrial low-density polyethylene: a thermal, dynamic mechanical, and rheological investigation,” Rheologica Acta, vol. 61, pp. 701-720, 2022.
- C. E. Wagner, A. C. Barbati, J. Engmann, A. S. Burbidge and G. H. McKinley, “Apparent Shear Thickening at Low Shear Rates in Polymer Solutions can be Artifact of Non-Equilibration,” Applied Rheology, vol. 26, p. 54091, 2016.
- S. G. Hatzikiriakos and K. B. Migler, Polymer Processing Instabilities, Boca Raton, FL, USA: CRC Press, 2004.
- A. J. Franck, “TA440: Introduction to Polymer Melt Rheology and its Application in Polymer Processing,” TA Instruments, Germany.
- F. J. Stadler, A. Nishioka, J. Stange, K. Koyama and H. Munstedt, “Comparison of Elongational Behavior of Various Polyolefins in Uniaxial and Equibiaxial Flows,” Rheologica Acta, vol. 46, pp. 1003-1012, 2007.
- H. Munstedt, “Extensional Rheology and Processing of Polymeric Materials,” International Polymer Processing, vol. 33, no. 5, pp. 594-618, 2018.
- K. H. Nitta and A. Tanaka, “Dynamic mechanical properties of metallocene catalyzed linear polyethylenes,” Polymer, vol. 42, no. 3, pp. 1219-1226, 2001.
- J. Z. Liang, “Melt Strength and Drawability of HDPE, LDPE, and HDPE/LDPE Blends,” Polymer Testing, vol. 73, pp. 433-438, 2019.
- G. Attalla and F. Bertinotti, “Comparison between a linear and a branched low-density polyethylene,” J. Appl. Polym. Sci., vol. 28, pp. 3503-3511, 1983.
Acknowledgement
This paper was written by Mark Staub, PhD at TA Instruments.
Click here to download the printable version of this application note.