Schlüsselwörter: Nickel-Mangan-Cobalt, Polyvinylidenfluorid, Kathodenpulver, Pulverrheologie, Trockenelektrodenpulver
RH136-DE
Abstract
Die Optimierung der Elektrodenherstellung für Lithium-Ionen-Batterien steht aufgrund von Ineffizienzen und Umweltrisiken im Zusammenhang mit herkömmlichen Methoden zur Behandlung von Slurrys für Elektroden zunehmend im Fokus. Zur Umgehung der Nachteile der Verwendung von Slurrys setzte man zum Beispiel auf Trockenpulverbeschichtungstechniken. Zwar entfallen dadurch die Kosten, der Zeitaufwand und die Umweltrisiken, die mit der Verwendung eines Lösungsmittels verbunden sind, andererseits entstehen bei der Trockenpulverbeschichtung aber zusätzliche Herausforderungen bei der Handhabung und Verarbeitung des Pulvers. In diesem Anwendungshinweis wird das neue Zubehör für Pulverrheologie von TA Instruments™ verwendet, um die Scher- und Fließfähigkeitseigenschaften eines Lithium-Nickel-Mangan-Cobalt- bzw. Nickel-Mangan-Cobalt-Kathodenpulvers mit unterschiedlichen Verhältnissen von Ruß und Polymerbindemittel zu charakterisieren. Analysen der Pulverkohäsion, der Fließgrenze des freien Pulvers, der Fließfunktion und der Gesamtfließenergie gaben Aufschluss über die Formulierung und Skalierung. Die thermogravimetrische Analyse (TGA) ist eine einfache Technik zur Identifizierung des Bindemittelgehalts in dem Pulver. Rasterelektronenmikroskopie (REM) in Verbindung mit energiedispersiver Spektroskopie (EDS) stellt einen Zusammenhang zwischen den Masseneigenschaften des Pulvers und der zugrunde liegenden Mikrostruktur her, die das Scher- und Fließverhalten eines bestimmten Pulvers beeinflusst. Die Ergebnisse zeigen, dass eine Änderung des Polymerbindemittelgehalts die Wechselwirkung zwischen den Partikeln und die daraus resultierenden Scher- und Fließeigenschaften der Masse beeinflusst.
Einführung
Lithium-Ionen-Batterien sind die zurzeit bekannteste Energiespeicherlösung. Daher rücken auch die entsprechenden Herstellungsprozesse zunehmend ins Zentrum der Aufmerksamkeit [1]. Ein kostspieliger und zeitintensiver Teil der Batterieherstellung ist die Herstellung der Elektroden. Die Komponenten der Elektrode werden mit einem Lösungsmittel vermischt, um eine Slurry zu bilden, die dann auf einen Stromkollektor aus Metallfolie aufgetragen und getrocknet wird. Der Mischvorgang bei diesem lösungsbasierten Verfahren ist ausreichend, um bei einer Rolle-zu-Rolle-Beschichtung im großen Maßstab eine gleichmäßige Elektrodenbeschichtung zu erzeugen, andererseits erhöht sich durch die Verwendung von Lösungsmittel jedoch insgesamt der Zeit- und Kostenaufwand für die Elektrodenherstellung. Die Trocknung und Lösungsmittelrückgewinnung machen über 40 % des gesamten Energieverbrauchs und einen erheblichen Teil der Kosten aus. Zweitens verlängern die zur Entfernung des Lösungsmittels erforderlichen Trocknungsschritte den Herstellungsprozess [2]. Dazu kommt, dass es sich bei den Lösungsmitteln, insbesondere für die Kathodenherstellung, meist um umwelttoxische organische Lösungsmittel wie N-Methyl-2-pyrrolidon handelt [3].
Aus den genannten Überlegungen heraus wurde versucht, Trockenpulverbeschichtungsverfahren zur Herstellung von Elektroden für Lithium-Ionen-Batterien zu implementieren. In diesem Zusammenhang sind die Eigenschaften des Pulvers für den Herstellungsprozess von entscheidender Bedeutung. Die Fließfähigkeit ist für den Pulvertransport bei der Maßstabsvergrößerung und Produktion wichtig, und die Kohäsion des Pulvers beeinflusst die Gleichmäßigkeit der Beschichtung. Bei der Trockenpulverbeschichtung werden die aktiven Elektrodenkomponenten im Trockenpulverzustand mit einem Polymerbindemittel vermischt. Das vermischte Elektrodenpulver wird dann auf eine Metallfolie aufgetragen und durch eine Kombination aus Temperatur und Druck auf dem Substrat haftbar gemacht. Während dieses Prozesses ist das Pulver Druck und Schereinwirkung ausgesetzt. Dieses Trockenelektrodenverfahren reduziert den mit der Verwendung von Lösungsmittel verbundenen Zeit- und Kostenaufwand und ist kosteneffizienter als die Verwendung einer Slurry-Vorstufe [3].
Eines der am gängigsten Kathodenmaterialien ist Lithium-Nickel-Mangan-Cobalt, vor allem aufgrund seiner hohen Energiedichte und langen Zykluslebensdauer im Vergleich zu anderen Kathodenmaterialien [4]. Der Gehalt an Nickel-Mangan-Cobalt im Kathodenmaterial ist entscheidend für die Energiedichte der Batterie. Für diesen Anwendungshinweis wurden die rheologischen Eigenschaften des Pulvers mit einem festen Gehalt an Kathodenpulver auf Nickel-Mangan-Cobalt-Basis analysiert. Das Nickel-Mangan-Cobalt wurde mit unterschiedlichen Verhältnissen von Ruß (carbon black, CB) und Polyvinylidenfluorid (PVDF) als Bindemittel gemischt. Diese Komponenten wurden variiert, da der Ruß in dem System als leitendes Netzwerk wirkt, während Polyvinylidenfluorid physikalisch für eine Vernetzung zur Haftung am Substrat sorgt. Das Zusammenspiel dieser beiden Netzwerkeigenschaften muss bekannt sein, um das Elektrodendesign optimieren zu können. Aufgrund der isolierenden Eigenschaften von Polyvinylidenfluorid kann ein hoher Anteil an Polyvinylidenfluorid zu einem unzureichend leitenden Netzwerk führen, was die Batterieleistung beeinträchtigt. Andererseits kann sich zu wenig Polyvinylidenfluorid-Bindemittel nachteilig auf die Beschichtungseigenschaften der Elektrode während der Verarbeitung auswirken. Die Optimierung der Menge an Polyvinylidenfluorid-Bindemittel und Ruß mit dem aktiven Material der Nickel-Mangan-Cobalt-Kathode ist für die Leistung der fertigen Elektrode von entscheidender Bedeutung.
Für diesen Anwendungshinweis wurden Pulver-Proben von Nickel-Mangan-Cobalt mit unterschiedlichen Anteilen an Ruß und Polyvinylidenfluorid verwendet, um die Auswirkungen auf die Pulverfließfähigkeit zu untersuchen und Aufschlüsse über die Pulververarbeitungsbedingungen zu gewinnen. Die Scher- und Fließeigenschaften des Pulvers wurden mithilfe des Zubehörs für die Pulverrheologie von TA Instruments analysiert. Darüber hinaus wurden Rasterelektronenmikroskopie (REM) und thermogravimetrische Analyse (TGA) verwendet, um die Pulvereigenschaften mit der Mikrostruktur bzw. dem Gehalt an Polyvinylidenfluorid in Zusammenhang zu bringen.
Versuchsaufbau
Die Kathodenpulver-Mischproben stammten von SpectraPower, LLC (Livermore, CA, USA) und bestanden aus NMC811, Ruß und Polyvinylidenfluorid-Bindemittel. Für die Analysen wurden drei Pulver mit einem Gewichtsverhältnis von NMC:Ruß:PVDF von 96:3:1, 96:2:2 und 96:1:3 verwendet.
Für die Pulverrheologie-Analysen wurde das Performance-Rheometer HR-30 von TA Instruments zusammen mit dem Zubehör zur Untersuchung der Scherung und Fließfähigkeit des Pulvers verwendet. Scherexperimente fanden gemäß ASTM D7891 bei einer Konsolidierungsspannung von 9 kPa vor der Scherung bzw. von 7, 6, 5, 4 und 3 kPa bei anschließenden Scherschritten statt [5]. Die Experimente zur Pulverfließfähigkeit wurden bei einer Rotorspitzengeschwindigkeit von 100 mm/s durchgeführt. Die Pulveranalyse wurde in der TRIOS™ Software mithilfe der automatisierten Softwarefunktionen durchgeführt. Weitere Details der Pulverprüfung und -analyse sind in den Anwendungshinweisen RH123 und RH126 von TA Instruments beschrieben [6] [7]. Der Gehalt an Polyvinylidenfluorid im Kathodenpulver wurde mit dem Discovery™ TGA 5500 von TA Instruments bei einem Temperaturanstieg von Umgebungstemperatur auf 1000 °C mit einer Heizrate von 20 °C/min gemessen. Partikelgröße und -form und Oberflächenmorphologie des Pulvers wurden mittels REM unter Verwendung eines Phenom™ XL REM Tischgeräts von Thermo Fisher untersucht. Das Pulver wurde auf doppelseitigem Kohlenstoffband vorbereitet und bei einer Beschleunigungsspannung von 5 kV abgebildet.
Ergebnisse und Diskussion
Thermogravimetrische Analyse
Die Zusammensetzung der Formulierung ist entscheidend für die Elektrodenfunktion und die Leistung der fertigen Batterie. Die Ergebnisse der thermogravimetrischen Analyse sind in Abbildung 1 dargestellt. Schritt 1 bei etwa 490 °C entspricht der anfänglichen Zersetzung des Polyvinylidenfluorids, während Schritt 2 auf die Zersetzung des Polyvinylidenfluorids an der Polymer-Keramik-Grenzfläche zurückzuführen ist [8]. Die Gewichtsänderung auf 99, 98 und 97 % bestätigt einen Gehalt an Polyvinylidenfluorid von 1–3 Gew.-%.
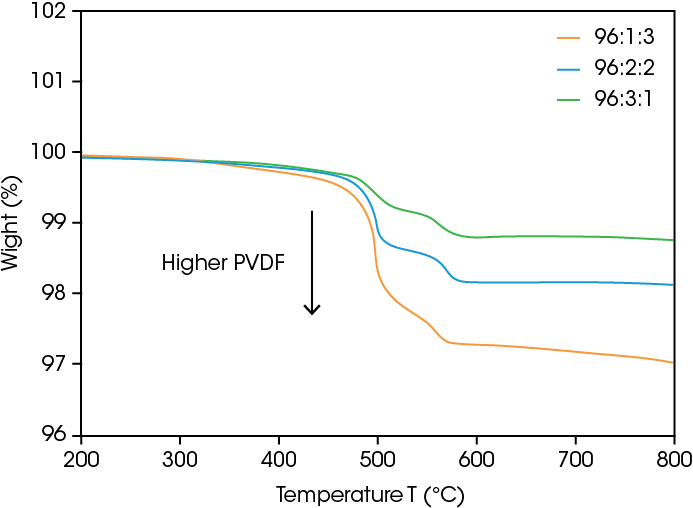
Rasterelektronenmikroskopie
Um die Mikrostruktur mit den rheologischen Eigenschaften in Korrelation zu bringen, wurde REM zusammen mit energiedispersiver Spektroskopie (EDS) verwendet. Abbildung 2 a bis c zeigt Bilder der REM bei einem Gehalt an Polyvinylidenfluorid von 1 bis 3 Gew.-%. Bei einem niedrigen Gehalt an Polyvinylidenfluorid ist die Oberfläche der Nickel-Mangan-Cobalt-Partikel rau (Kanten im Mikrometerbereich). Mit zunehmendem Gehalt an Polyvinylidenfluorid wird die Oberfläche glatter. Eine Polymerbeschichtung erscheint im Vergleich zu anorganischen Partikeln glatt, wenn sie bei niedrigen kV ohne zusätzliche Beschichtung abgebildet wird.
Abbildung 2d zeigt eine Map der energiedispersiven Spektroskopie des Pulvers mit 3 Gew.-% Polyvinylidenfluorid. Die gelbe Signatur ist die Kohlenstoff-Kα-Linie. Das starke Kohlenstoffsignal zwischen Nickel-Mangan-Cobalt-Partikeln ist auf Brückenbildung des Polyvinylidenfluorids zurückzuführen. Die zusätzlichen Kohlenstoffsignale stammen vom Ruß und der zusätzlichen Polyvinylidenfluorid-Beschichtung und stellen sich als Kohlenstoffsignale in kleineren Partikeln dar. Das Polyvinylidenfluorid ist zwar für Bindungszwecke wichtig, aber eine übermäßige Partikelbeschichtung ist nicht wünschenswert, da es nicht zum leitenden Netzwerk des Rußes beiträgt. Die Oberflächenabdeckung des Polyvinylidenfluorid auf Nickel-Mangan-Cobalt reduziert die verfügbaren aktiven Stellen auf der Kathode und führt letztendlich zu einer Begrenzung der Batterieleistung.
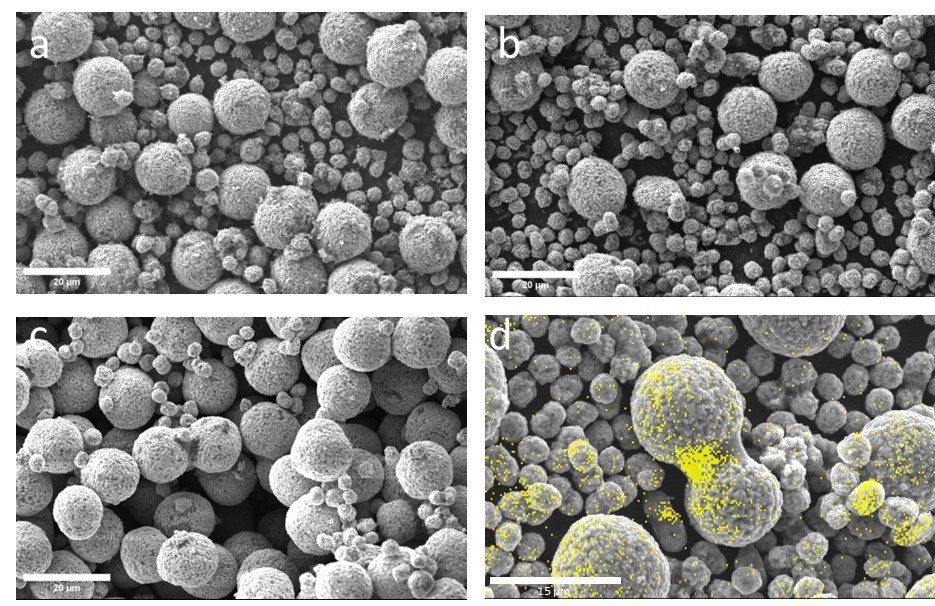
Pulverscherung
Die Herstellung von Pulverelektroden umfasst das Zuführen von Rohstoffen in Verarbeitungsgeräte, das anschließende Mischen des Pulvers und das Trockenbeschichten der Elektrode mit Pulver unter Schereinwirkung. Kohäsion und Fließfähigkeit sind bei einem Elektrodenpulver von entscheidender Bedeutung. Sie sollten einen effizienten Transport und ein effizientes Mischen ermöglichen. Die Scherdaten für die drei Kathodenpulver sind in Abbildung 3 dargestellt.
Tabelle 1 zeigt die Schereigenschaften aus der in der TRIOS Software durchgeführten Fließortanalyse. Kohäsion, Fließgrenze des freien Pulvers und größte Hauptspannung nahmen mit zunehmendem Bindemittelgehalt des Polyvinylidenfluorids ab. Die Fließfunktion, die angibt, ob es sich bei der Probe um ein frei fließendes Pulver handelt, lässt sich bestimmen, indem das Verhältnis der größten Hauptspannung zur Fließgrenze des freien Pulvers ermittelt wird, wie in [6] beschrieben. Nach dem System zur Einstufung der Fließeigenschaften nach Jenike sind alle drei Pulver leicht fließend, was einer Fließfunktion zwischen 4 und 10 entspricht [9]. Die Bilder der REM in Abbildung 2 liefern dafür eine Erklärung, da der höhere Gehalt an Polyvinylidenfluorid die Partikel umhüllt und für eine glattere Oberfläche sorgt. Diese glattere Oberfläche verringert die Reibung zwischen den Partikeln im Scherexperiment und verleiht der Masse Eigenschaften einer höheren Fließfunktion und einer geringeren Kohäsion bei höherem Polymergehalt.
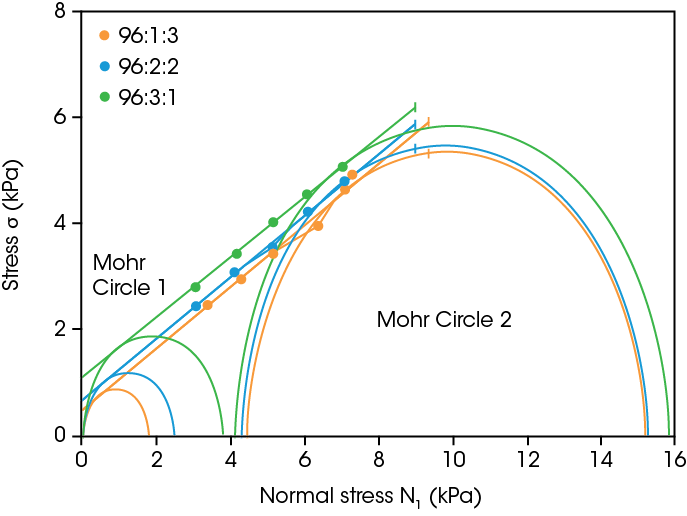
Tabelle 1. Zusammenfassung der Fließortanalyse der drei Kathodenpulver
NMC/Ruß/PVDF | Kohäsion (kPa) | Fließgrenze des freien Pulvers (kPa) | Größte Hauptspannung (kPa) | Fließfunktion |
---|---|---|---|---|
96/3/1 | 1,11 | 3,81 | 15,84 | 4,16 |
96/2/2 | 0,7 | 2,44 | 15,27 | 6,25 |
96/1/3 | 0,52 | 1,8 | 15,19 | 8,45 |
Fließeigenschaften des Pulvers
Die Prüfung der Fließeigenschaften des Pulvers gibt Aufschluss über die Fließfähigkeit des Pulvers und den effektiven Materialtransport für die Verarbeitung. Abbildung 3 zeigt die gesamte Fließenergie unter eingeschränkten und nicht eingeschränkten Bedingungen. Eingeschränkte Bedingungen liegen vor, wenn sich der Flügelrotor nach unten bewegt, und nicht eingeschränkte Bedingungen liegen vor, wenn sich der Rotor nach oben bewegt. Die Proben mit dem höheren Gehalt an Polyvinylidenfluorid weisen in beiden Fällen eine höhere Gesamtfließenergie auf, was zeigt, dass der Rotor bei Zugabe von Polyvinylidenfluorid mehr arbeiten muss, um sich durch die Probe hindurch auf und ab zu bewegen.
Wie sich in den Bildern der und den Scherergebnissen zeigte, führt der Bindungseffekt des Polyvinylidenfluorids zu einer glatteren Oberfläche, die die Reibung zwischen den Partikeln verringert, aber auch zu einer Agglomeration im Pulver aufgrund der Bindung zwischen den Partikeln. Aufgrund der Agglomeration ist für ausreichende Fließeigenschaften ein höherer Energieeintrag erforderlich. Bei der Messung unter eingeschränkten Bedingungen zeigt sich in den Zyklen aufgrund der verstärkten Durchmischung eine leicht ansteigende Gesamtfließenergie, was zu mehr Bindung und zur Bildung größerer Agglomerate führt. Das Vorhandensein größerer Agglomerate erfordert mehr Arbeit des Rotors, um das Pulver während der Abwärtsbewegung während des Fließschritts unter eingeschränkten Bedingungen zu komprimieren. Bei der Messung unter nicht eingeschränkten Bedingungen führt die Partikelbindung zwar zu einem Gesamtanstieg der Fließenergie bei höherem Gehalt anPolyvinylidenfluorid, aber das Fehlen einer Kompression während des Experiments führt zu einer relativ konstanten Gesamtfließenergie während des Zyklus.
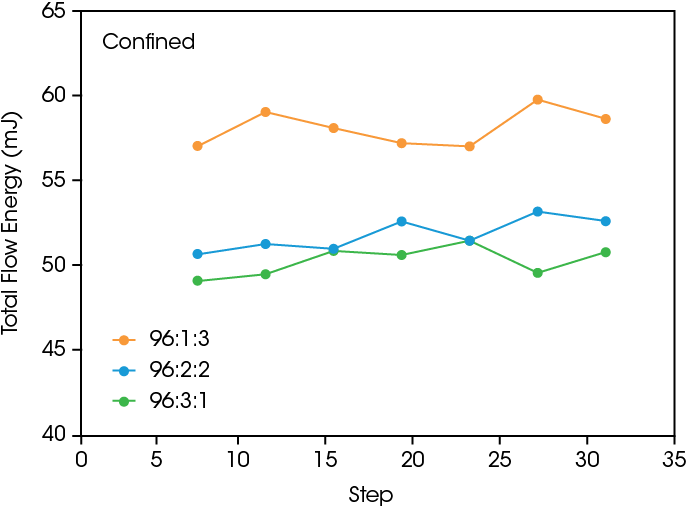

Fazit
In Anbetracht der zunehmenden Notwendigkeit von Kosteneinsparungen bei Herstellungsprozessen von Lithium-Ionen-Batterien erlangen Pulverbeschichtungstechnologien zur Herstellung von Elektroden immer mehr Interesse. Für eine Optimierung der Misch- und Beschichtungsprozesse müssen die Masseneigenschaften der Pulver bekannt sein. Für diesen Anwendungshinweis wurden Nickel-Mangan-Cobalt-basierte Kathodenpulver analysiert, um Daten zur Optimierung der Elektrodenformulierung und der Verarbeitungsbedingungen zu erlangen. Discovery TGA ermöglicht eine Qualitätsprüfung des Bindemittelgehalts der Formulierung und bestimmt, wie viel Bindemittel in der Probe vorhanden ist. Die Scher- und Fließeigenschaften wurden mit dem Zubehör für die Pulverrheologie von TA Instruments charakterisiert, wobei festgestellt wurde, dass Fließfähigkeit und Fließenergie durch einen steigenden Bindemittelgehalt an Polyvinylidenfluorid beeinflusst werden. Mittels REM-Bildgebung wurde gezeigt, dass das Polyvinylidenfluorid in höheren Anteilsmengen die Oberfläche der Partikel beschichtet und als physikalisches Bindemittel zwischen den Kathodenpartikeln wirkt, wodurch die Reibung zwischen den Partikeln verringert und die Fließfähigkeit erhöht wird. Bei der Scheranalyse des Pulvers zeigt sich daher eine höhere Fließfunktion und eine geringere Kohäsion bei höherem Gehalt an Polyvinylidenfluorid. Der Bindungseffekt der Partikel führt zu einer insgesamt höheren Gesamtfließenergie bei der Analyse in der Pulverfließkonfiguration mit einem Tiegel mit glatter Oberfläche und einem Flügelrotor. Diese Ergebnisse können verwendet werden, um die Formulierung und den Pulvermischprozess zu optimieren und homogene Kathodenpulver herzustellen, die sich durch eine wiederholbare und konsistente elektrochemische Leistung auszeichnen.
Literaturhinweise
- Y. Lu, C.-Z. Zhao, H. Yuan, J.-K. Hu, J.-Q. Huang and Q. Zhang, „Dry electrode technology, the rising star in solid-state battery
industrialization“, Matter, Vol. V, Nr. 3, S. 876-898, 2022. - A. Gyulai, W. Bauer and H. Ehrenberg, „Dry Electrode Manufacturing in a Calender: The Role of Powder Premixing for Electrode Quality and Electrochemical Performance“, ACS Appl. Energy Mater., Vol. VI, Nr. 10, S. 5122–5134, 2023.
- M. Ryu, Y.-K. Hong, S.-Y. Lee and J. H. Park, „Ultrahigh loading dry-process for solvent-free lithium-ion battery electrode fabrication“, Nature Communications, Vol. 14, S. 1316, 2023.
- A. K. Stephan, „A Pathway to Understand NMC Cathodes“, Joule, Vol. IV, Nr. 8, S. 1632-1633, 2020.
- ASTM International, „ASTM D7891-5 Standard Test Method for Shear Testing of Powders Using the Freeman Technology FT4 Powder Rheometer Shear Cell“, 2016, 2016.
- J. Vail, S. Cotts and T. Chen, „Powder Rheology of Lactose: Impacts of powder morphology on performance of pharmaceutical excipients“, TA Instruments, Vol. RH123.
- K. Dennis and S. Cotts, „RH125: Powder Rheology of Graphite: Characterization of Natural and Synthetic Graphite for Battery Anode Slurries“, TA Instruments, New Castle, DE.
- S. Dwivedi, M. Badole, K. Gangwar and S. Kumar, „Relaxation processes and conduction behaviour in PVDF-TrFE and KNNbased composites“, Polymer, vVol. 232, S. 124164, 2021.
- W. Chen and A. W. Roberts, „A modified flowability classification model for moist and cohesive bulk solids“, Powder Technology,
Vol. 325, S. 639-650, 2018.
Danksagung
Diese Veröffentlichung wurde von Mark Staub, PhD, und Hang Lau, PhD, bei TA Instruments, verfasst.
TA Instruments, TRIOS und Discovery sind Marken der Waters Technologies Corporation. PHENOM ist eine Marke von Thermo Fisher Scientific Inc.
Click here to download the printable version of this application note.