키워드: NMC, 플루오르화 폴리비닐리덴, 캐소드 분말, 분말 유변학, 건식 전극 분말
RH136-KO
초록
리튬 이온 배터리를 위한 전극 공정의 최적화는 기존 슬러리 전극 공정 방식을 둘러싼 비효율성과 환경적인 우려로 인해 점점 더 주목받고 있다. 슬러리 활용 시 빠질 수 있는 함정을 피하기 위해 건식 분말 코팅 기술을 사용하고자 하는 노력이 있어 왔다. 이는 용제 사용과 관련된 비용, 시간 및 환경적인 우려를 없앨 수 있지만, 건식 분말 코팅은 분말 취급 및 처리에 있어 추가적인 어려움을 제시한다. 이 애플리케이션 노트에서는 새로운 TA Instruments™ 분말 부속품을 활용하여 각각 다른 카본 블랙 및 폴리머 바인더 비율로 구성된 리튬 니켈 망간 코발트(NMC) 캐소드 분말의 벌크 분말 전단 및 유동 특성을 규명한다. 분말 응집력, 일축 항복강도, 유동 함수 및 총 유동 에너지의 특성을 규명하여, 제형 및 스케일업에 대한 통찰력을 제공했다. 열중량 분석(TGA)은 분말 내 바인더 함량을 식별하는 데 손쉽게 활용할 수 있는 기술이다. 주사 전자 현미경(SEM)을 에너지 분산 분광법(EDS)과 함께 사용하면 분말의 벌크 특성을 분말의 특정 전단 및 유동 거동에 영향을 미치는 기본 미세 구조와 연결할 수 있다. 결과는 고분자 바인더 함량을 변경하면, 입자 간 상호 작용 및 이후에 일어나는 벌크 전단 및 유동 특성에 영향을 미치게 된다는 것을 보여준다.
서론
리튬 이온 배터리(LIB)가 가장 유망한 에너지 저장 솔루션으로 부상하면서, 설계 이면에 존재하는 제조 공정에 이목이 쏠리고 있다[1]. 배터리 제조 시 비용과 시간이 많이 소요되는 부분은 전극 제작이다. 전극의 구성 요소를 용제와 혼합하여 슬러리를 형성한 후, 이를 금속박 집전체에 코팅하고 건조시킨다. 이러한 용액 기반 공정은 대규모 롤투롤 공정 시 전극 코팅을 균일하게 하기 위한 적절한 혼합이 가능하지만, 용제 사용으로 인해 전체 전극 제조에 시간과 비용이 추가된다. 건조 및 용제 회수는 전체 에너지 소비의 40%를 초과하며, 비용의 상당 부분을 차지한다. 다음으로, 용제를 제거하는 데 필요한 건조 단계로 인해 제조 공정에 시간이 추가된다[2]. 뿐만 아니라, 특히 캐소드 제조에 사용하는 용제는 N-메틸 2-피롤리돈(NMP)과 같은 환경에 유독한 유기 용제이다[3].
상기 고려 사항에 기반하여, 건식 분말 코팅 공정을 구현해 LIB 전극을 제조하려는 노력이 있어 왔다. 결과적으로 분말 특성은 제조 공정에 있어 대단히 중요하다. 유동성은 스케일업 및 생산 시 분말을 이송하는 데 중요하며, 분말의 응집력은 코팅의 균일성에 영향을 미친다. 건조 분말 코팅 공정에는 활성 전극의 구성 요소를 건식 분말 상태의 고분자 바인더와 혼합하는 과정이 포함되어 있다. 그 후 혼합한 전극 분말을 금속 호일에 분사하고 온도와 압력을 함께 가하여 분말 전극을 기판에 접착한다. 이 과정에서 해당 분말은 압축과 전단을 받게 된다. 이러한 건식 전극 공정은 용제 사용과 관련된 시간과 비용을 절감할 수 있으며 슬러리 전구체를 사용하는 것에 비해 비용 효율적인 공정이다[3].
가장 널리 사용되는 캐소드 소재는 리튬 니켈 망간 코발트(NMC)이다. 다른 캐소드 소재에 비해 에너지 밀도가 높으며 주기 수명이 길기 때문이다[4]. 캐소드 소재에 함유된 NMC의 양은 배터리의 에너지 밀도에 아주 중요한 역할을 한다. 이 노트에서는 함량이 고정된 NMC 기반 캐소드 분말의 분말 유변학적 특성을 분석할 것이다. NMC는 다양한 비율의 카본 블랙(CB) 및 플루오르화 폴리비닐리덴(PVDF) 바인더와 혼합된다. CB는 시스템에 전도성 네트워크를 제공하는 반면 PVDF는 기판 접착을 위한 물리적 네트워크를 제공하므로 구성 요소는 다양했다. 전극 설계를 최적화하려면 이러한 두 네트워크 기능 간 상호작용을 이해해야 한다. PVDF의 절연 특성으로 인해 PVDF 함량이 높으면 전도성 네트워크가 충분하지 않아 배터리 성능이 저하될 수 있다. 반면, PVDF 바인더가 부족하면 공정을 진행하는 동안 전극의 코팅 특성에 악영향이 있을 수 있다. 활성 NMC 캐소드 소재로 PVDF 바인더와 카본 블랙의 양을 최적화하는 것은 전극의 최종 성능에 필수적이다.
이 노트에서는 다양한 양의 CB 및 PVDF를 혼합한 분말 NMC 샘플을 조사하여 분말 유동성을 자세히 알아보고 분말 공정 조건에 대한 통찰력을 제공한다. 분말 전단 및 유동 특성은 TA Instruments 분말 유변학 부속품을 사용하여 살펴본다. 또한 주사 전자 현미경(SEM)과 열중량 분석(TGA)을 사용해 분말 특성이 가진 미세 구조 및 PVDF 함량과의 상관 관계를 파악한다.
실험
혼합된 캐소드 분말 샘플은 SpectraPower, LLC(Livermore, CA)에서 조달했으며 NMC811, 카본 블랙 및 PVDF 바인더로 구성되어 있었다. NMC:CB:PVDF 중량비가 96:3:1, 96:2:2 및 96:1:3인 3가지 분말을 테스트에 사용했다.
분말 전단 및 유동성 부속품을 사용해 TA Instruments HR-30 고성능 레오미터에서 분말 유변학 테스트를 수행했다. 전단 실험은 ASTM D7891에 따라, 9kPa의 사전 전단 성형 응력 및 7, 6, 5, 4, 3kPa의 성형 응력으로 후속 전단 단계에서 수행했다[5]. 분말 유동성 실험은 100mm/s의 로터 팁 속도로 수행했다. 분석은 TRIOS™ 소프트웨어로 자동 분말 분석 소프트웨어 기능을 사용해 수행했다. 분말 테스트 및 분석에 관한 더 자세한 정보는 TA Instruments 애플리케이션 노트 RH123과 RH126에서 확인할 수 있다[6] [7]. 캐소드 분말 내 PVDF 함량은 TA Instruments Discovery™ TGA 5500을 이용하여 확인했으며, 상온에서 1000°C까지의 온도 램프를 20°C/분의 속도로 수행했다. 분말의 입자 크기, 모양 및 표면 형태는 Thermo Fisher의 Phenom™ XL 벤치탑 SEM을 사용하여 SEM을 통해 조사했다. 분말은 양면 카본 테이프에서 준비했으며 5kV 가속 전압에서 이미지를 얻었다.
결과 및 논의
열중량 분석
제형의 구성은 전극 기능 및 최종 배터리 성능에 있어 대단히 중요하다. TGA 결과는 그림 1에 나와 있다. 약 490°C에서 일어나는 첫 번째 단계는 초기 PVDF 분해에 해당하며, 두 번째 단계는 폴리머-세라믹 계면에 국한된 PVDF 분해에서 기인한 것일 수 있다[8]. 99, 98, 97%로의 중량 변화는 각각 PVDF 함량이 1~3wt%임을 확인한다.
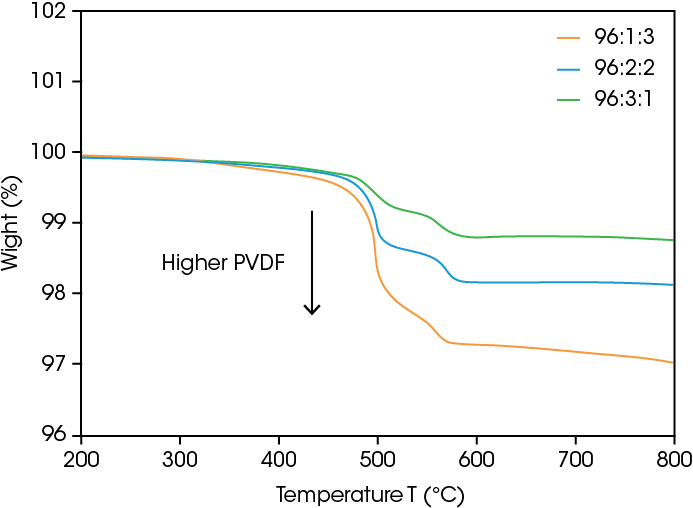
주사 전자 현미경
미세 구조와 유변학적 특성의 상관관계를 파악하기 위해 에너지 분산 분광법(EDS)과 SEM을 함께 사용했다. 그림 2의 a~c에서 1~3wt% PVDF의 SEM 이미지를 각각 확인할 수 있다. PVDF 함량이 낮은 경우 NMC 입자의 표면은 거칠다(미크론 크기 돌출). PVDF 함량이 증가함에 따라 표면은 매끈해진다. 추가적인 코팅을 하지 않은 상태에서 낮은 kV에서 이미지를 얻으면 고분자 코팅이 무기질 입자에 비해 매끈하게 나타날 것이다.
그림 2d에 PVDF 3wt% 함량 분말의 EDS 맵이 나와 있다. 노란색 시그니처는 카본의 Kα 라인이다. NMC 입자 간의 강한 카본 신호는 PVDF 가교를 드러낸다. 이질적인 탄소 신호는 추가적인 PVDF 코팅과 CB에서 발생하는 것이며, 더 작은 입자에서 발생하는 탄소 신호로 나타난다. 결합을 위해 PVDF가 중요하지만, CB의 전도성 네트워크에는 기여하지 않으므로 과도한 입자 코팅은 바람직하지 않다. NMC에서 PVDF의 표면 적용 범위는 캐소드에서 사용 가능한 활성 부위를 감소시키고, 궁극적으로는 배터리 성능을 제한하게 된다.
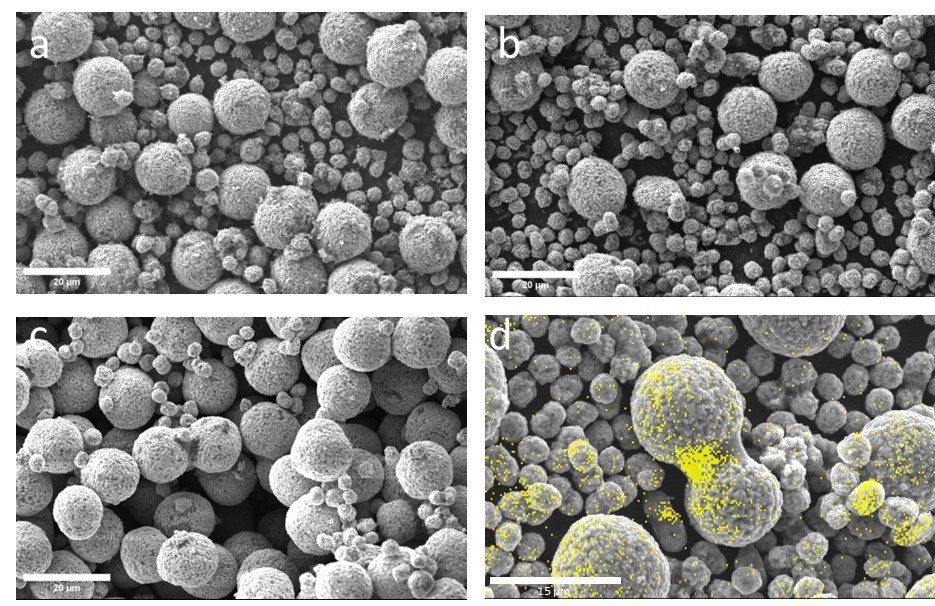
분말 전단
분말 전극 공정에는 원료를 가공 장비에 공급한 후 분말을 혼합하고, 전단 조건 하에서 전극을 분말로 건식 코팅하는 작업이 포함되어 있다. 전극 분말 가공에는 분말의 응집력과 유동성이 대단히 중요하다. 효율적인 이송 및 혼합이 가능하려면, 적절한 유동성을 가지면서도 양호한 응집 특성을 보유해야 한다. 3가지 캐소드 분말에 대한 분말 전단 데이터는 그림 3에 나와 있다.
표 1에는 TRIOS 소프트웨어로 수행한 항복 궤적 분석의 전단 특성이 나와 있다. PVDF 바인더 함량이 증가함에 따라 응집력, 일축 항복강도 및 주응력은 감소했다. 샘플이 자유 유동 분말인지 여부를 나타내는 유동 함수는 [6]에 설명된 대로 일축 항복강도에 대한 주응력의 비율을 통해 결정할 수 있다. Jenike 유동성 분류(Flowability Classification) 시스템에 따르면, 3가지 샘플 모두 유동 함수가 4~10 사이인 유동이 용이한 분체에 해당한다[9]. PVDF 함량이 높을수록 입자를 코팅하는 거동을 보이고 더 매끄러운 표면을 제공하므로, 그림 2의 SEM 이미지를 통해 이를 설명할 수 있다. 이 매끄러운 표면은 전단 실험에서 입자 간 마찰을 줄이고, 폴리머 함량이 높을수록 유동 함수가 크고 응집력이 적은 벌크 특성을 제공한다.
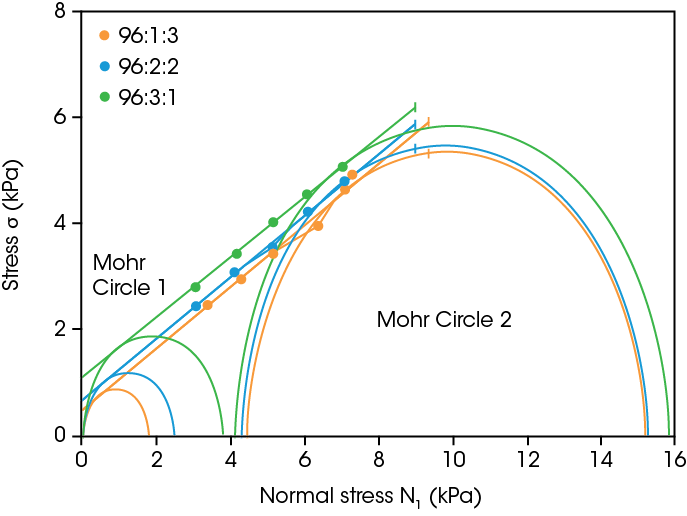
표 1. 3가지 캐소드 분말
NMC/CB/PVDF | 의 항복 궤적 분석 요약응집력(kPa) | 일축 항복강도(kPa) | 주응력(kPa) | 유동 함수 |
---|---|---|---|---|
96/3/1 | 1.11 | 3.81 | 15.84 | 4.16 |
96/2/2 | 0.7 | 2.44 | 15.27 | 6.25 |
96/1/3 | 0.52 | 1.8 | 15.19 | 8.45 |
분말 유동
분말 유동 테스트는 분말의 유동성 및 가공을 위한 효과적인 재료 이송에 대한 통찰력을 제공한다. 그림 3은 제한 및 비제한 조건 모두에서의 총 유동 에너지를 보여준다. 제한 조건은 임펠러 로터가 아래로 움직일 때 발생하며, 비제한 조건은 로터가 위로 움직일 때 발생한다. PVDF 함량이 높은 샘플은 두 경우 모두 총 유동 에너지가 더 높은데, 이는 PVDF를 첨가하면 샘플을 통과하여 위아래로 이동하기 위해 로터가 더 많은 일을 수행해야 함을 의미한다.
SEM 이미지와 전단 결과에서 확인할 수 있듯이, PVDF 결합 효과는 표면을 더 매끄럽게 만들며 입자 간 마찰을 감소시키지만, 입자 간 결합으로 인한 분말 내 응집을 유발한다. 이러한 응집은 충분한 유동성을 위해 필요한 에너지 입력 상승으로 이어진다. 제한 측정에서 사이클링 시 혼합이 증가함으로 인해 총 유동 에너지가 약간 증가하며, 더 많은 결합과 더 큰 응집체 형성을 유발한다. 큰 응집체가 존재하는 경우, 제한 유동 단계에서 아래로 내려가는 동안 로터는 분말을 압축하기 위해 더 많은 작업을 수행해야 한다. 비제한 측정에서 입자 결합은 높은 PVDF 함량에서 전반적인 유동 에너지의 증가를 야기하지만, 실험 중 압축이 없으면 사이클링 시 유동 에너지는 상대적으로 일정하다.
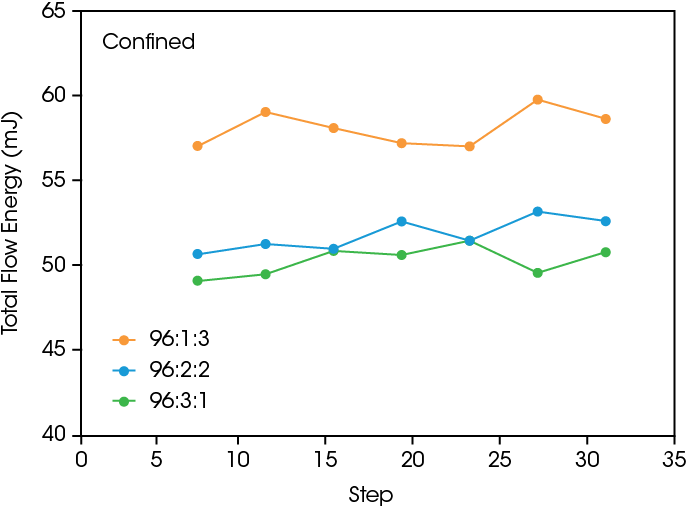

결론
LIB 제조 공정에서 비용 절감에 대한 수요가 증가함에 따라, 전극 제조 시 분말 코팅 기술을 사용하는 방법에 관한 연구가 점차 증가하고 있다. 최적의 배합과 혼합 및 코팅 공정 설계를 위해 분말의 벌크 특성 파악이 필수적이다. 이 연구에서는 NMC 기반 캐소드 분말을 분석하여 전극 제형 및 공정 조건 최적화에 대한 통찰력을 얻고자 했다. Discovery TGA는 제형 내 바인더 함량에 관한 품질 검사를 제공하며 샘플 내에 존재하는 바인더 양을 확인할 수 있다. TA Instruments 분말 부속품을 사용해 전단 및 유동성 특성을 규명했으며, PVDF 바인더 함량이 증가하면 유동성 및 유동 에너지가 영향을 받는다는 사실이 드러났다. SEM 이미징 결과 PVDF 함량이 높으면 입자 표면을 코팅하고 캐소드 입자의 물리적 바인더 역할을 하여 입자 간 마찰을 줄이고 유동성이 높아지는 것으로 나타났다. 그 결과 전단 분말 분석을 통해 PVDF 함량이 높을수록 유동 함수가 커지며 응집력은 낮아진다는 사실을 확인할 수 있었다. 표면이 매끄러운 컵과 임펠러 로터를 포함한 분말 유동 구성에서 테스트 시, 입자의 결합 효과는 전반적으로 높은 유동 에너지로 이어진다. 이러한 결과를 이용해 제형 및 분말 혼합 공정을 최적화하며, 반복 가능하고 일관적인 전기화학적 성능을 보유한 균질한 캐소드 분말을 얻을 수 있다.
참고문헌
- Y. Lu, C.-Z. Zhao, H. Yuan, J.-K. Hu, J.-Q. Huang and Q. Zhang, “Dry electrode technology, the rising star in solid-state battery
industrialization,” Matter, vol. V, no. 3, pp. 876-898, 2022. - A. Gyulai, W. Bauer and H. Ehrenberg, “Dry Electrode Manufacturing in a Calender: The Role of Powder Premixing for Electrode Quality and Electrochemical Performance,” ACS Appl. Energy Mater., vol. VI, no. 10, p. 5122–5134, 2023.
- M. Ryu, Y.-K. Hong, S.-Y. Lee and J. H. Park, “Ultrahigh loading dry-process for solvent-free lithium-ion battery electrode fabrication,” Nature Communications, vol. 14, p. 1316, 2023.
- A. K. Stephan, “A Pathway to Understand NMC Cathodes,” Joule, vol. IV, no. 8, pp. 1632-1633, 2020.
- ASTM International, “ASTM D7891-5 Standard Test Method for Shear Testing of Powders Using the Freeman Technology FT4 Powder Rheometer Shear Cell,” 2016, 2016.
- J. Vail, S. Cotts and T. Chen, “Powder Rheology of Lactose: Impacts of powder morphology on performance of pharmaceutical excipients,” TA Instruments, vol. RH123.
- K. Dennis and S. Cotts, “RH125: Powder Rheology of Graphite: Characterization of Natural and Synthetic Graphite for Battery Anode Slurries,” TA Instruments, New Castle, DE.
- S. Dwivedi, M. Badole, K. Gangwar and S. Kumar, “Relaxation processes and conduction behaviour in PVDF-TrFE and KNNbased composites,” Polymer, vol. 232, p. 124164, 2021.
- W. Chen and A. W. Roberts, “A modified flowability classification model for moist and cohesive bulk solids,” Powder Technology,
vol. 325, pp. 639-650, 2018.
감사의 말
이 문서는 TA Instruments의 Mark Staub 박사와 Hang Lau 박사가 작성했습니다.
TA Instruments, TRIOS 및 Discovery는 Waters Technologies Corporation의 상표입니다. PHENOM은 Thermo Fisher Scientific Inc.의 상표입니다.
Click here to download the printable version of this application note.