Keywords: Battery, Cathode, Thermal analysis, SDT, LFP
TA480
Application Benefits
- TA Instruments™ Discovery™ SDT allows simultaneous DSC and TGA measurements on one instrument
- Samples can be analyzed up to 1500 °C in different controlled atmospheres to understand oxidation and other interactions with various gases
- Discovery SDT measurements offer insight into thermal stability, oxidation, phase changes, and transition temperatures of battery materials such as LFP cathode
Abstract
Lithium Iron Phosphate (LFP) is a popular cathode material in lithium-ion batteries. Researchers continue to optimize its electrical conductivity through coatings, modified morphology, or doping. Thermal analysis can offer insight into the stability, phase transitions, and heat flow of LFP in order to optimize the processing and understand effects of these modifications. TA Instruments Discovery SDT – simultaneous differential scanning calorimetry (DSC) and thermogravimetric analysis (TGA) – measures weight changes and heat flow in a material across a range of temperatures. Samples can be tested under different environmental conditions to understand coating content, phase transition temperature, as well as any other interactions with gases, including if and when oxidation occurs. LFP with a carbon coating was tested under air, nitrogen, and argon, with oxidation beginning at 325 °C in air and phase changes occurring above 900 °C.
Introduction
Since its development in the 1990s, Lithium Iron Phosphate (LFP) has become a popular cathode material for lithium-ion batteries (LIB). Among its advantages, LFP is cost-effective, long lasting, and is one of the safest cathode material options available. It offers great thermal stability and excellent electrochemical properties, but its low electrical conductivity has led to ongoing efforts to optimize its performance.
One of the strategies used is to modify the surface of the LFP through a carbon (C) coating; however, the source of carbon can influence performance, as well as coating thickness. If the coating is too thick, it can hinder diffusion of lithium ions and decrease the energy density of the battery. As a result, an LFP/C composite material with optimized carbon source and loading is desired for high performance [1]. Other strategies include modifying LFP morphology or doping the material to improve electrical conductivity. Understanding the phase transition temperature and heat flow properties can help optimize the process, while also gaining insight into the effects of any material modifications. Oxidation can readily occur in LFPs and care needs to be taken in the process to avoid this [2] [3].
Formulators and manufacturers need efficient means to verify the carbon content and integrity of their coatings, check for oxidation conditions, and understand the phase transition behavior. Differential scanning calorimetry (DSC) can be coupled with thermogravimetric analysis (TGA) to evaluate coated LFP. Simultaneous DSC-TGA (SDT) measures both weight changes and heat flow in a material as a function of temperature or time in a controlled atmosphere up to 1500 °C. In this paper, SDT will be used to identify the composition of carbon coating on LFP from the weight change, determine the phase transition temperature, and the enthalpy of reaction during phase transitions from the heat flow data. X-ray diffraction (XRD) will be done to further investigate LFP oxidation and crystalline structure.
Experimental
Commercially available coated LFP powder was kindly provided by NEI Corporation. To study the coating degradation and phase transition, reference uncoated LFP was purchased from Sigma-Aldrich. LFP weight loss and heat flow of both samples in nitrogen were measured on a TA Instruments SDT 650 (Figure 1). The coated NEI samples were then run under additional purge gases of argon and air to observe the effect of atmosphere. Samples were ramped at 20 °C/min from room temperature to 1200 °C. Alumina and sapphire pans were used for the majority of testing, but sapphire pans were suggested to run above the melting temperature to avoid sticking on the SDT beam.
In addition to SDT, XRD experiments were run to investigate changes to the crystalline structure of the coated LFP after being exposed to high temperature. Two annealing experiments were conducted under different atmospheric conditions. In the first, LFP powders were annealed in a muffle furnace by heating to 350 °C at a rate of 5 °C/min, then holding at temperature for two hours before cooling at a rate of 10 °C/min. The second set of powders were annealed in a nitrogen atmosphere by placing the powders in a tube furnace, pre-flowed with nitrogen gas for 30 min at a rate of 200 mL/min to remove any residual air. The powders were then heated to 950 °C at a rate of 5 °C/min, held at temperature for two hours, then cooled down to room temperature at a rate of 10 °C/min. Pristine powders and corresponding annealed powders were then characterized by NEI Corporation with a MiniFlex II XRD instrument by Rigaku Corporation to investigate structural stability.
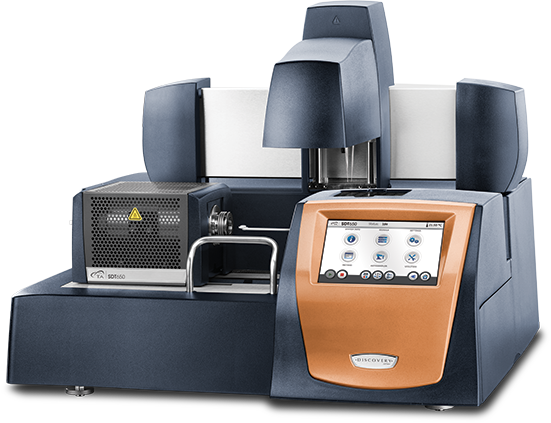
Results and Discussion
The coating content of the commercial LFP cathode samples in nitrogen is shown in Figure 2. Coated LFP cathode (blue) showed 3% weight loss versus no significant weight loss for uncoated LFP (Green). As a result, the Coated LFP cathode material (blue) loses 3 wt%, which is the organic coating content and the remaining 97% of the material is LFP. Both LFP samples show an endothermic peak melting transition around 970 ˚C [4]. The coated LFP cathode showed both the coating decomposition and LFP phase transition across the same temperature range. To obtain more accurate enthalpy values, the endothermic heat flow is plotted as weight corrected heat flow to obtain the weight adjusted enthalpy value.
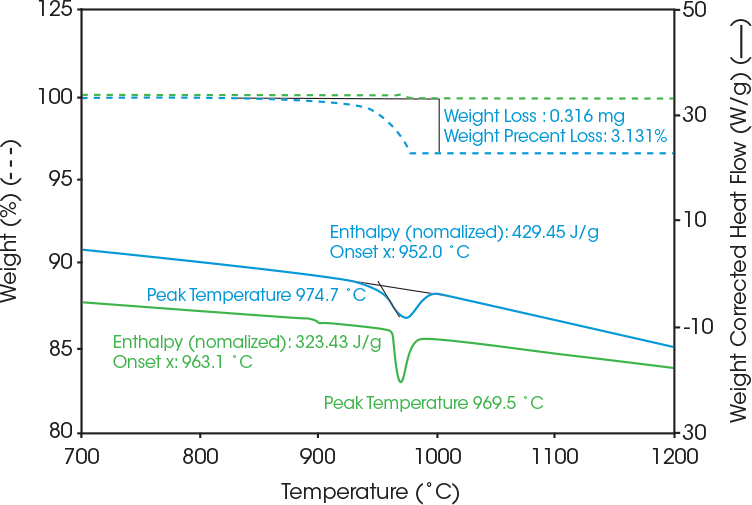
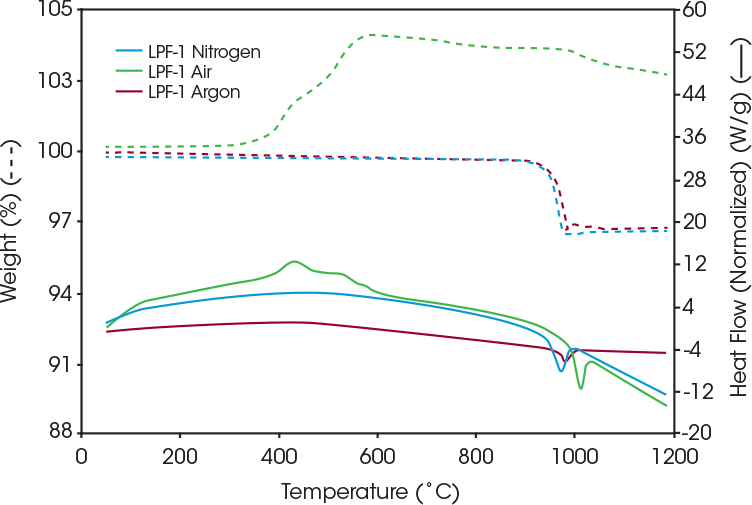
In addition to the nitrogen environment, samples were run in air and argon to determine stability and interaction with those gases. Figure 3 shows the resulting heat flow and weight loss of the coated LFP in air, nitrogen, and argon. Under nitrogen and argon, the coated LFP is stable until the sample is above 900 °C, at which point the coating begins to degrade.
The coated LFP sample in air experiences an exothermic reaction peak at around 432 °C, and weight gain is around 300 °C, which is likely due to oxidation. As seen in Table 1, the peak temperature for the coated LFP in nitrogen was 975 °C and 982 °C in argon.
Table 1: Endotherm peak temperature, and weight loss of the coated LFP under nitrogen, air, and argon
Purge Gas | Peak Temperature of Endotherm (°C) | Weight Loss (%) |
---|---|---|
Nitrogen | 975 | 3.13 |
Air | 993 | – |
Argon | 982 | 3.05 |
SDT allows a quick, first pass screening of temperature stability of LFP. The results can be used to select annealing conditions for analysis with XRD to evaluate any changes in crystalline structure after the LFP was exposed to high temperatures. Coated LFP samples were annealed under nitrogen at 950 °C, where an endothermic phase transition begins in Figure 2. Other coated LFP samples were annealed at 350 °C under air due to the weight gain seen around this temperature in Figure 3. This weight gain indicates that oxidation may be occurring and SDT analysis can be used to determine the onset temperature of this oxidation. The first derivative weight signal plotted in Figure 4 shows the rate of weight gain and an onset at 325 °C.
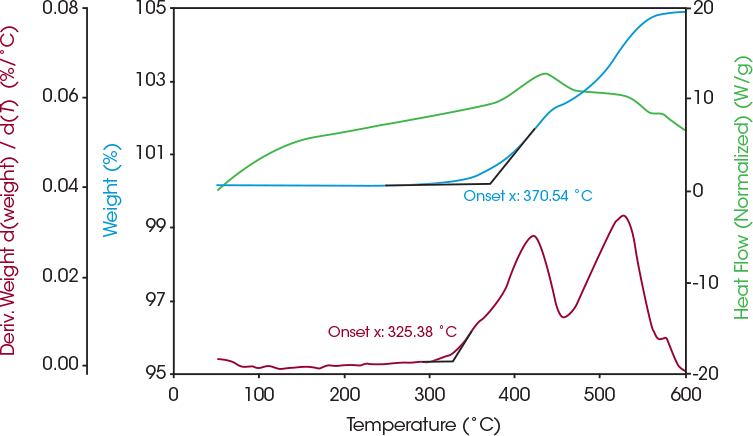
Oxidation was confirmed by the corresponding XRD experiment, as shown in Figure 5. The impurity phase is formed when the powders are annealed in air, which indicates that an oxidation reaction happens between the coated LFP powders and oxygen in air at 350 °C. No impurity phase was observed when the coated LFP powders were annealed in nitrogen atmosphere. However, the peaks appear to broaden, which could be due to thermally induced lattice “distortion.” [5] [6] This may be related to small changes in the crystal structure from annealing at 950 °C, the temperature at which a phase transition begins as shown by the SDT data in Figure 2.
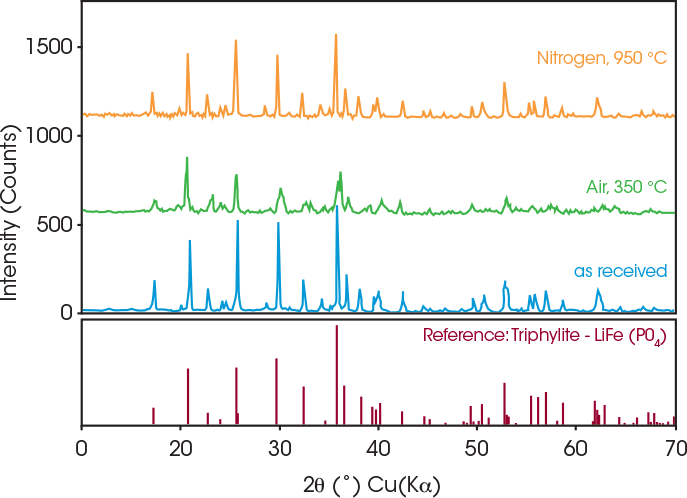
Conclusions
TA Instruments SDT can screen the temperature stability and phase transitions of the active materials in LIB cathodes. The reaction temperatures, energy released, weight changes, and interactions with air, nitrogen, and argon can be investigated. The LFP sample studied in this work was found to have a coating of 3 wt% organic material. It was stable in nitrogen and argon up to 900 °C, whereas the LFP samples in air oxidized at 370 °C and then showed a higher phase transition temperature. This oxidation was then confirmed by XRD analysis. In addition to providing insight into the stability of the cathode materials, SDT results can also be used to determine the crystalline structure of the LFP at temperatures of interest, such as oxidation or phase transition temperatures.
References
- E. Avci, “Enhanced cathode performance of nano-sized lithium iron phosphatecomposite using polytetrafluoroethylene as carbon precursor,” Journal of Power Sources, vol. 270, pp. 142-150, 2014.
- Z. Ahsan, B. Ding, Z. Cai, W. Yang, Y. Ma and M. S. Javed, “Recent progress in capacity enhancement of LiFePO4 cathode for Li-ion batteries,” Journal of Electrochemical Energy Conversion and Storage, vol. 18, no. 1, 2021.
- K. Kretschmer, “Phosphate-based cathode materials for rechargeable batteries,” 2018.
- M. Gauthier, C. Michot, N. Ravet, M. Duchesneau, J. Dufour, G. Liang, J. Wontcheu, L. Gauthier and D. D. MacNeil, “Melt Casting LiFePO4 : I. Synthesis and Characterization,” Journal of The Electrochemical Society, vol. 157, no. 4, pp. A453-A462, 2010.
- T. Ungár, “Microstructural parameters from X-ray diffraction peak broadening,” Scripta Materialia, vol. 51, no. 8, pp. 777-781, 2004.
Acknowledgement
This work was done in collaboration with NEI Corporation (Somerset, New Jersey). It was written by Jennifer Vail, PhD, Andrew Janisse, PhD, Application Specialists at TA Instruments and Hang Lau, PhD, New Market Development Scientific Lead at TA Instruments.
TA Instruments and Discovery are trademarks of Waters Technologies Corporation.
Click here to download the printable version of this application note.