One of the most critical battery components is the electrolyte, which is the conductive solution that transports positively charged ions from the cathode to the anode during the charging process. Lithium-ion battery electrolytes are traditionally made of a lithium salt dissolved in a mixture of organic solvents. During battery formation, the solvent and salt components of the electrolyte are reduced on the anode to produce the solid electrolyte interphase (SEI), which plays a crucial role in battery operation and safety.
Today’s battery researchers are experimenting with different formulations of liquid, gel, polymer, and solid-state electrolytes. Designing successful electrolytes requires balancing viscosity, conductivity, electrochemical stability, and cost. Most electrolytes can perform well at low temperatures but have restrictive thermal stability even at moderate temperatures.
Battery developers rely on thermal analysis to measure electrolytes’ thermal stability and ensure their designs avoid degradation and potential fires. Electrolyte thermal stability can be investigated with Differential Scanning Calorimetry (DSC) and Thermogravimetric Analysis (TGA), and together these methods offer a comprehensive analysis of an electrolyte’s thermal properties. Rheology enables engineers to measure viscosity and produce electrolyte solvents with optimal pumpability during manufacturing.
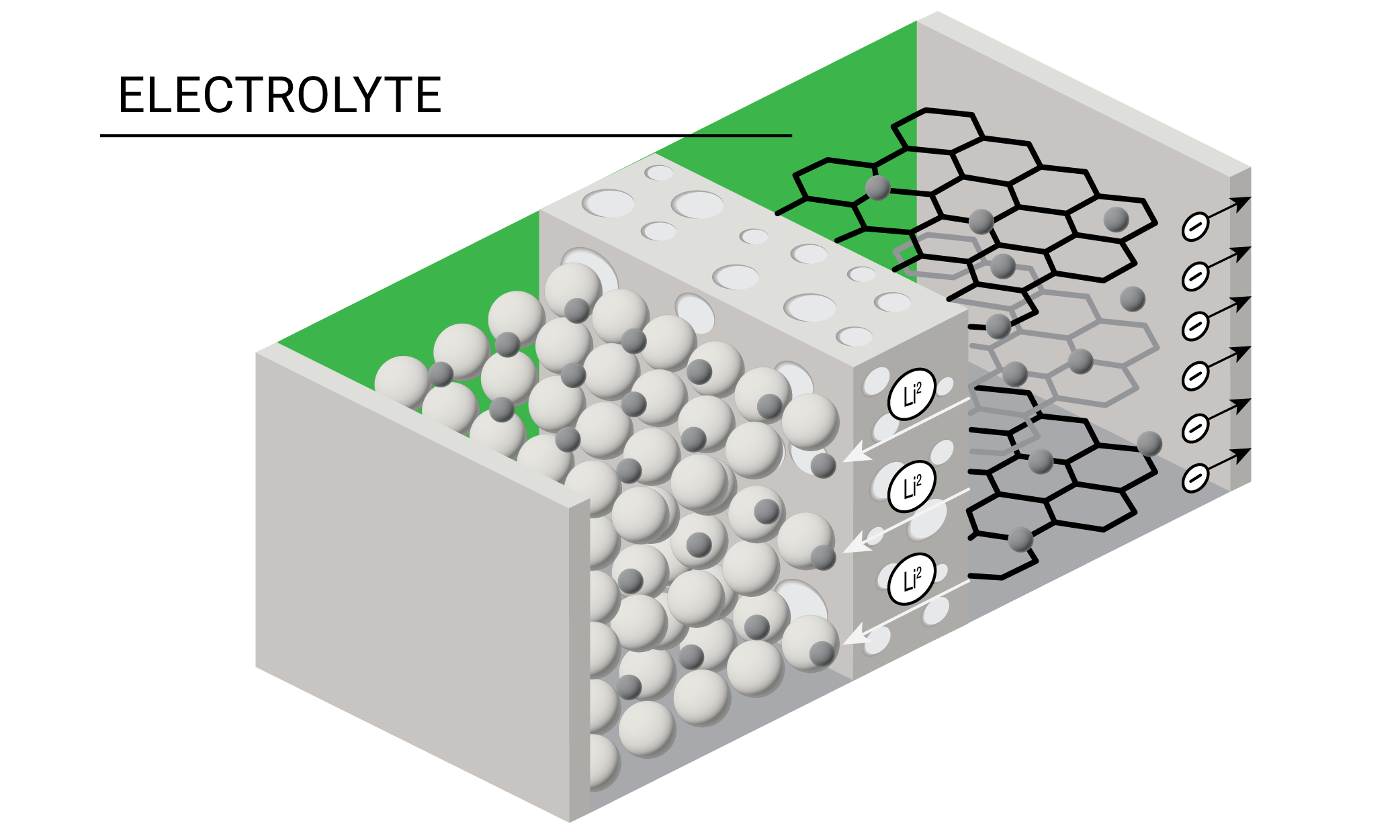
Instruments and Test Parameters
Pumpability, transport
- Yield stress
- Viscosity (newtonian, shear thinning, shear thickening)
- Viscoelasticity
Effect of charge-discharge cycles on conductivity
- Viscosity
- Electro-rheology
Atmospheric Analysis
- Glovebox operation compatible
- Argon & Nitrogen purged environment
Differential Scanning Calorimetry
Electrolyte formulation
- Melting
- Crystallization
Thermal stability
- Thermal runaway temperature
- Heat of reaction
Thermogravimetric Analysis
Thermal stability
- Decomposition temperature
Composition determination
- Volatile content
- Impurity determination
- Evolved gas analysis, TGA-MS, TGA-FTIR, TGA-GCMS
Atmospheric Analysis
- Glovebox operation compatible
- Argon & Nitrogen purged environment
Application Example
What Thermal Events Lead to Thermal Runaway?
While there are remaining questions about the thermal runaway process in batteries, current understanding suggests that it is initiated by the following series of events. The exothermic reactions leading to thermal runaway interact destructively with every inner component of a Lithium-Ion Battery (LIB) as the battery’s temperature continues to rise; some elements are early casualties while most directly speed up heat accumulation as they fail.
The first component to begin breaking down is the Solid-Electrolyte Interphase (SEI), which generally starts around 80-120°C (176-248°F). At this point, Thermal Runaway can be slowed, but is no longer reversible once the anode is exposed to the electrolyte. Exothermic reactions occurring at the reactive anode surface add more heat into the system until it reaches the next critical temperatures.
The separator is the next component affected, and it fails in two stages. Around 120-150°C (248-302°F) the separator begins to melt and causes a small short-circuit, followed by a more serious internal short circuit when the separator breaks up near 220-250°C (428-482°F).
The following reactions happen quickly and directly following the previous temperature range; the cathode material, binder, and electrolyte all begin decomposition, which drastically raises the temperature of the battery cell to temperatures about 800°C (1472°F). These reactions have gas products which increase the pressure within the LIB.
TGA Thermogram Highlighting Thermal Instability of Graphite Anode Material

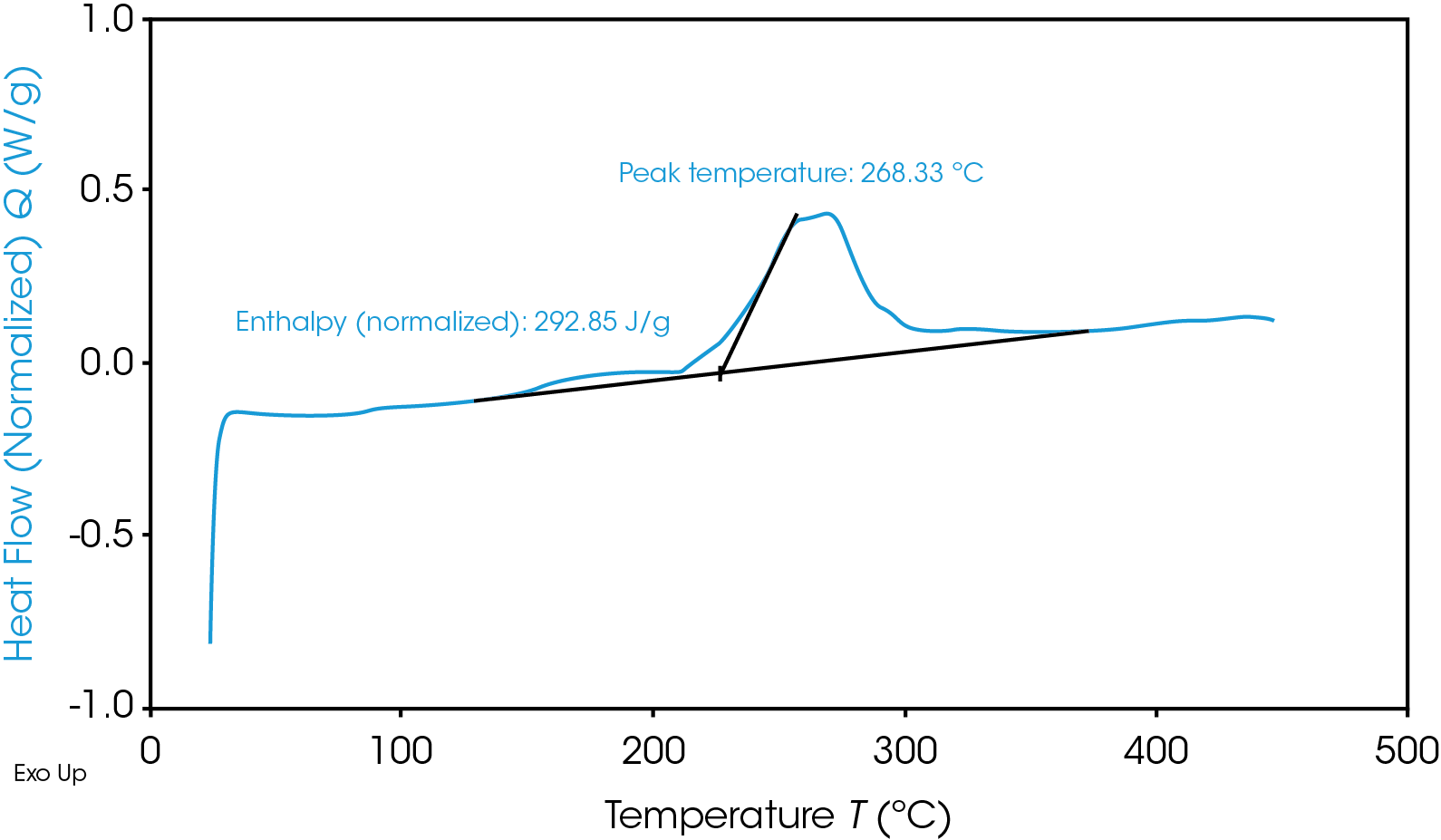
Aside from quick heat generation, the cathodic reactions have a disastrous byproduct of oxygen which is flammable. Depending on the exact conditions, the immediate result is either “Heat + Oxygen = Fire” or “Heat + Gas = Rupture/Explosion”. Of course, not all materials are made equal and may fall high or low on these ranges – or even outside of these temperatures in the future – so it is essential to make the safest possible choice of materials for a given battery with proper testing.
To avoid thermal runaway and select battery materials with optimal heat tolerances, battery researchers turn to Differential Scanning Calorimetry (DSC) and Thermogravimetric Analysis (TGA):
DSC: DSC measures the heat flow into or out of a material as a function of temperature or time. Phase changes interrupt the heat capacity relationship between temperature change and heat absorbed or released and are visible on graph output. It allows for testing in a variety of conditions ranging from safe operating temperature to thermal abuse.
TGA: TGA measures mass of a sample as a function of temperature or time. Generally speaking, a more thermally stable material can reach a higher temperature before any change in mass occurs.
Answer the following questions with results from your DSC:
- The material’s melting temperature, Tm
- The material’s glass transition temperature, Tg
- The lowest phase change temperature of various materials that comprise the battery.
Answer the following questions with results from your TGA:
- The temperature at which a material begins decomposition.
- The amount of sample mass lost to thermal or oxidative decomposition at a given temperature.
- The rate of decomposition reactions (both oxidative and thermally induced) at a given temperature.
- The maximum thermally stable temperature of the various materials that comprise the battery.