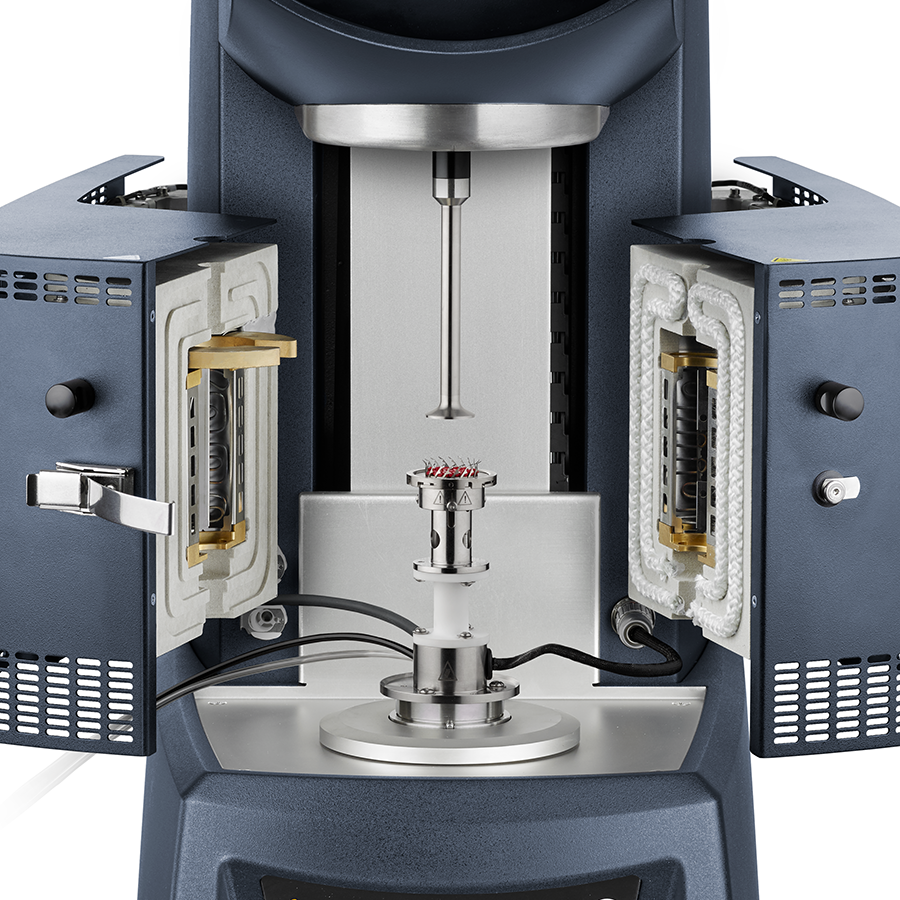
The auto-trim accessory for the DHR simplifies polymer melt rheology by automating the sample heating and trimming process. Instead of opening the furnace to manually trim samples during tests, users can simply attach the accessory, load their sample, and hit start to run the experiment to completion. TA’s proprietary technology automatically conditions the sample, adjusts the gap, and trims the sample at the appropriate time during the test without any operator intervention. As a result, operator walk-away time is increased by 80%, new user training is reduced from 2 weeks down to 30 minutes, and adverse operator influence on the results is greatly reduced. By saving valuable operator time without sacrificing data consistency, the auto-trim accessory provides return on investment in less than 2 years. The auto-trim accessory empowers your lab to run more tests with confidence, accelerating product development and time to market.
What will you accomplish with 80% more operator free time?
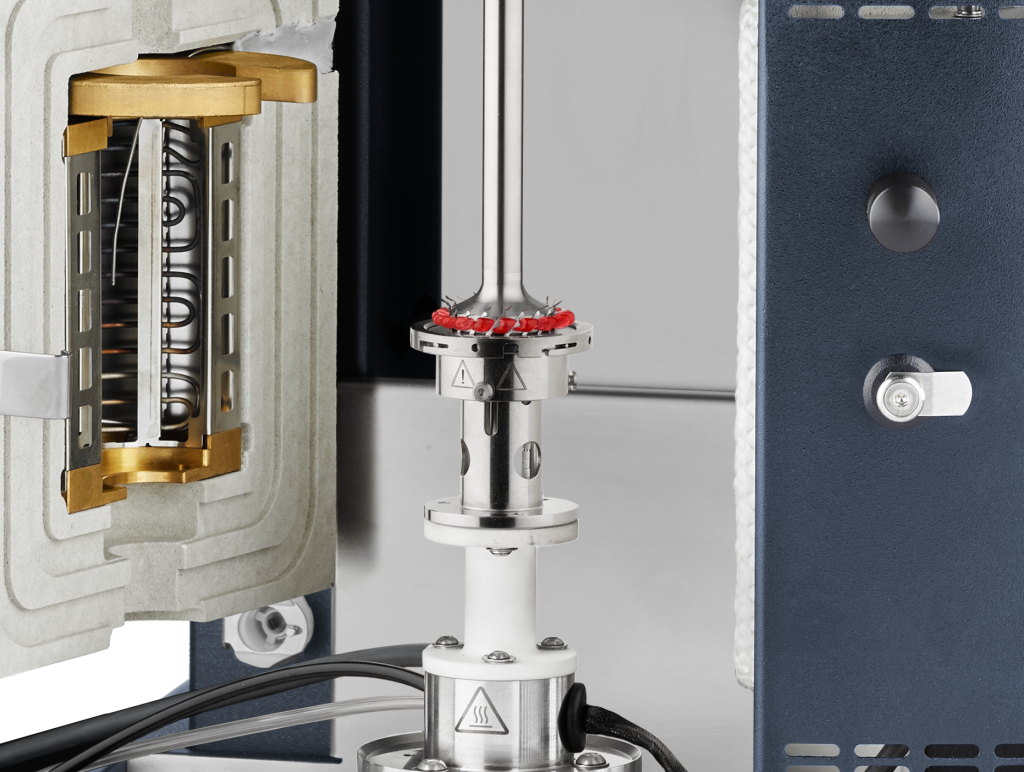
Technology
The new patent pending auto-trim accessory uses Smart SwapTM technology to transform a standard DHR 10, 20, or 30 into a semi-automated polymer melt rheometer! Testing procedures are the exact same as using the standard parallel plate geometry with a melt ring, but the auto-trim accessory replaces the melt ring with a disposable trimmer which automatically removes all the excess sample at the appropriate time. The trimming action ensures that each test is run with the appropriate sample volume for repeatable results. The sample is trimmed with high consistency due to each test using a new trimmer. The auto-trim accessory is rated to 325 °C and compatible with the ETC oven.
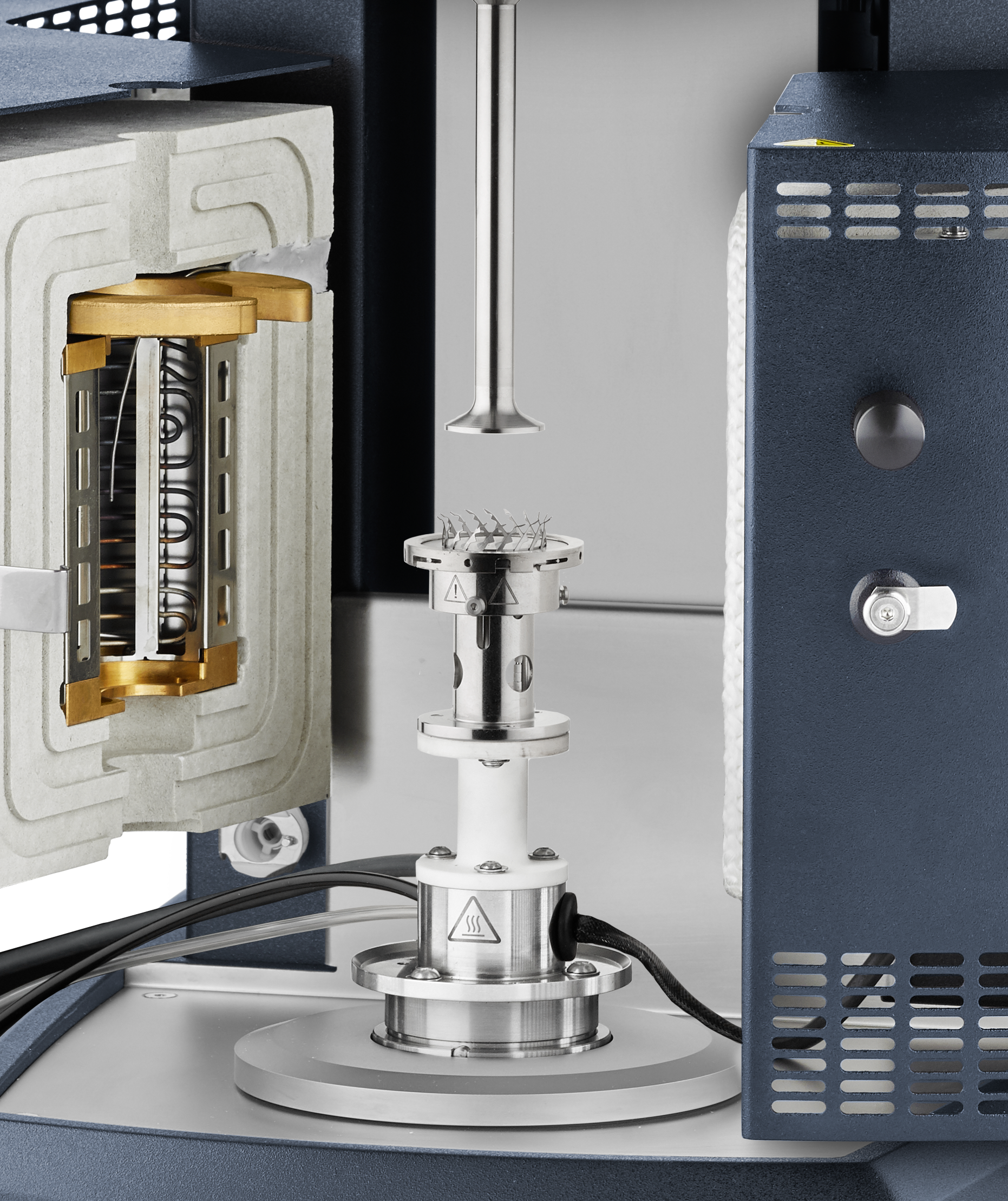
Features & Benefits:
Increase Productivity
By automating most of the experiment, users gain 80% more walk-away time. Additionally, new users can be trained to confidently generate high quality polymer melt rheology data in less than 30 minutes.
Improve Data Consistency
Enhance your site-to-site and operator-to-operator consistency for polymer critical quality attributes (CQA) saving you time and money.
Retain Versatility
Automation doesn’t require giving up the other capabilities of your rheometer. Users can swap accessories in less than 10 seconds to support full polymer processing characterization. Switch from automated melt rheology procedures to testing solids in DMA mode as well as extension with the Extensional Viscosity Accessory.
Maximize Investment
The auto-trim accessory pays for itself in less than two years by saving valuable operator testing and training time. Compared to available automated alternatives, automation on the DHR offers substantially faster lead time for a fraction of the cost.
- Increases operator walk-away time by 80%, requiring less than two minutes of operator time per test with fully-programmed test methods.
- Excellent data consistency through automatic removal of excess material – Better data consistency than manual trimming, even when comparing data from an expert rheologist with results from multiple operators with limited experience
- Training time reduced from 2 weeks to under 30 minutes via plug and play accessories, while still achieving high quality data
- Realize the benefits of automation while maintaining the versatility to perform Dynamic Mechanical Analysis (DMA), extensional viscosity, and other rheological measurements thanks to SmartSwap technology.
- Eliminates the need to open the chamber during a test, preventing temperature fluctuations on the sample and maintaining the inert environment
- Suitable for testing pellets, disks, and flakes with no modification necessary
- Confirm pre-test process and trim quality with automatic before and after trimming photos from the optional ETC camera
Comparison of crossover modulus (Gc) for manual trimming and the auto-trim accessory on Acrylonitrile Butadiene Styrene (ABS)
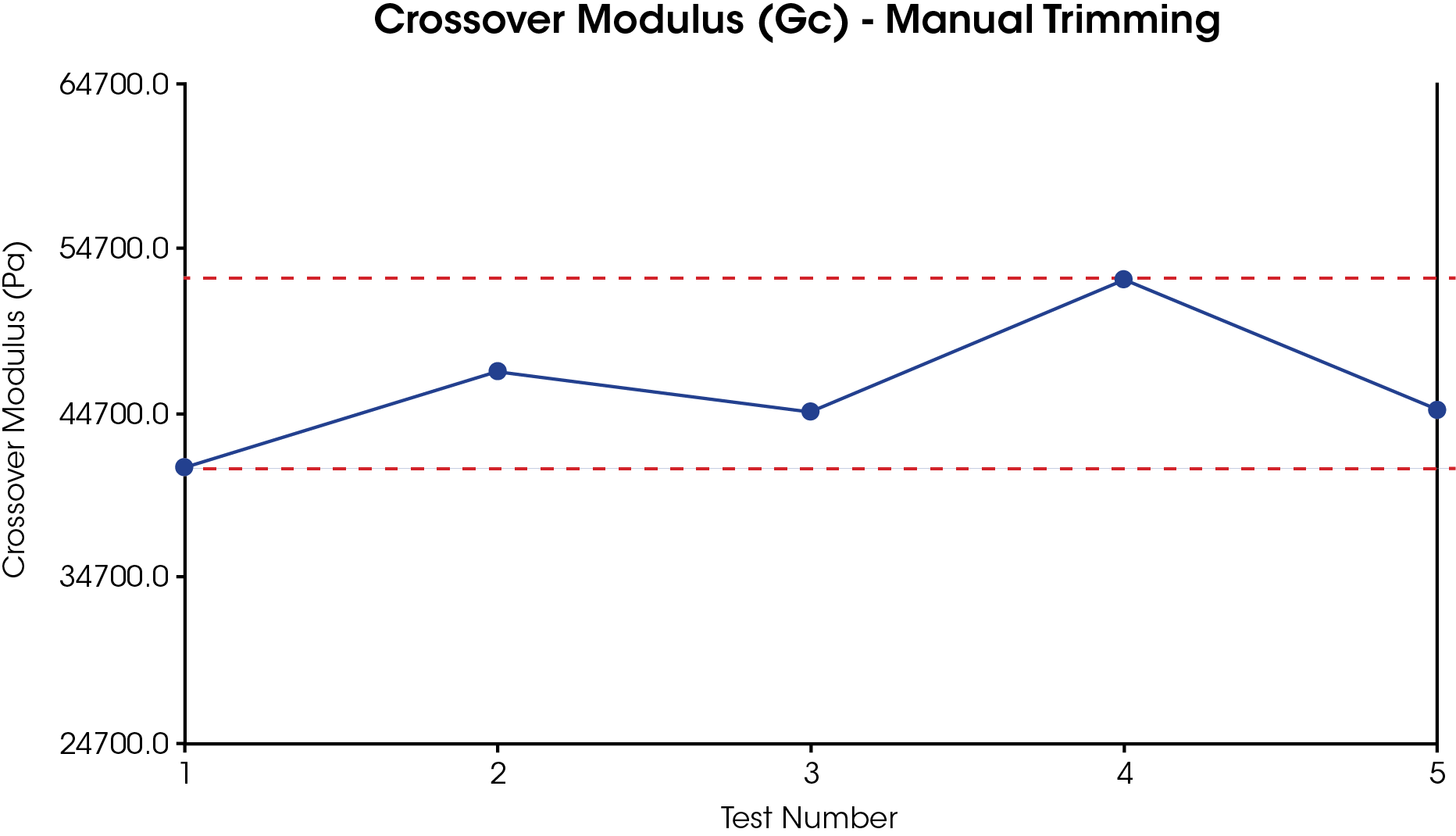
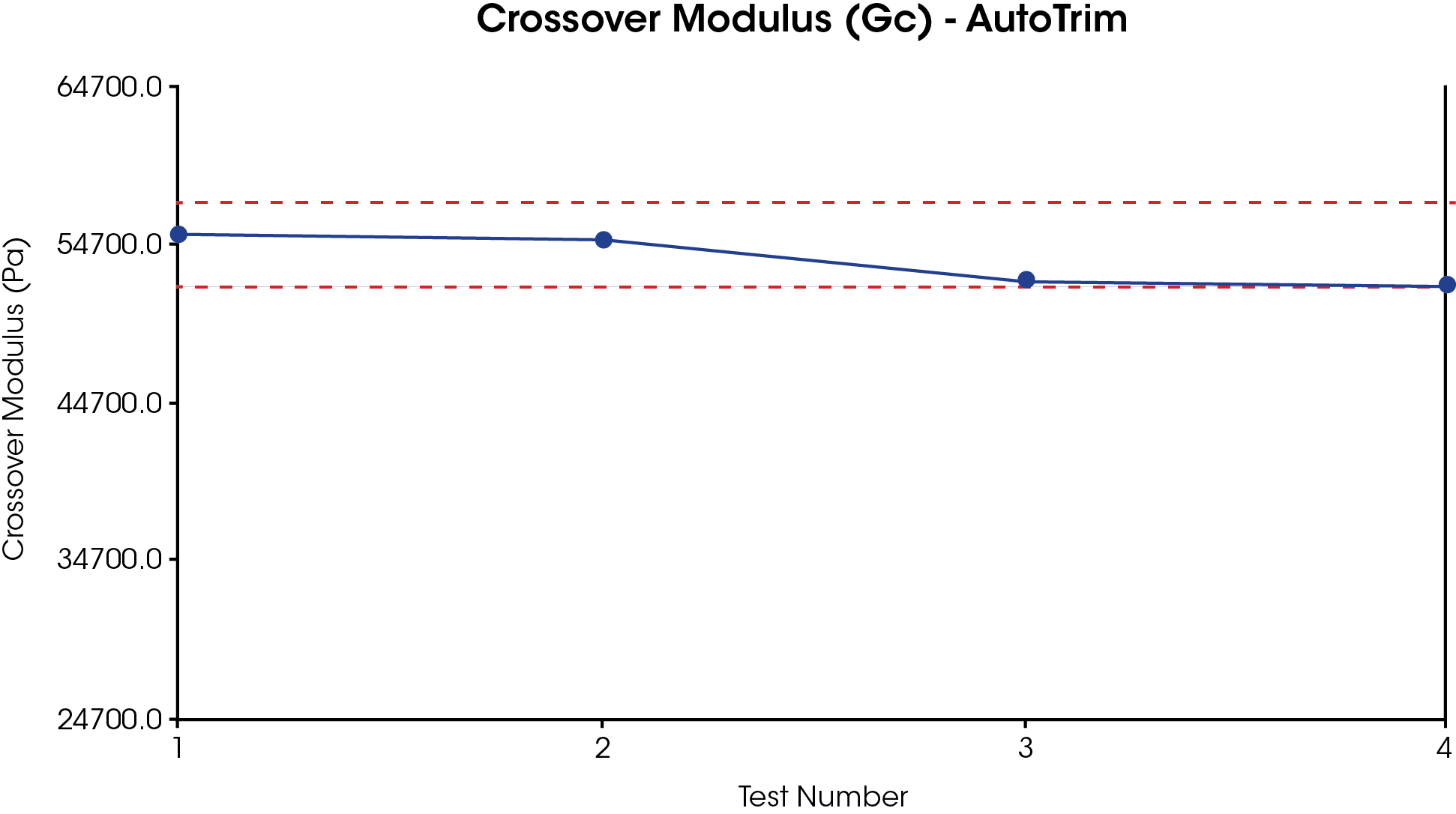
Crossover modulus is a common polymer melt measurement because it provides a consistent measurement of molecular weight and molecular weight distribution. Measuring crossover modulus is a very useful method to validate a batch of material or predict processability.
Acrylonitrile butadiene styrene (ABS) is a notoriously challenging and time-consuming material to perform melt rheology on due to the long relaxation time and high sensitivity to trimming practices. The manual data has a Coefficient of Variation (COV) of 9.1% and required approximately 21 minutes of expert operator time per test to allow sufficient relaxation time. The data using the auto-trim accessory had a COV of 3.1% and only required less than 2 minutes of hands on-time from the operator. The slight shift in the average value is due to the auto-trim accessory trimming the material with a shearing motion along the axis of the geometry. Manual trimming is typically performed in a circumferential direction resulting in some material being ‘dragged’ out from between the plates, showing an artificially low modulus measurement. This data shows how the design of the auto-trim accessory produces extremely consistent trimming action and is inherently independent of operator influence, even for highly challenging materials.
- Tech Brief: Polymer Melt Rheology Workflow Automation: Auto-Trim Accessory for Discovery Hybrid Rheometers
- Application Note: Polymer Flow and Mechanical Characterization for Material Development, Processing, and Performance
- Tech Tip: How to Set Up the Auto-Trim Accessory for the Discovery Hybrid Rheometer
- Rheometer Accessories Brochure
- Discovery Hybrid Rheometers
- Request a Quote
- Description
-
The auto-trim accessory for the DHR simplifies polymer melt rheology by automating the sample heating and trimming process. Instead of opening the furnace to manually trim samples during tests, users can simply attach the accessory, load their sample, and hit start to run the experiment to completion. TA’s proprietary technology automatically conditions the sample, adjusts the gap, and trims the sample at the appropriate time during the test without any operator intervention. As a result, operator walk-away time is increased by 80%, new user training is reduced from 2 weeks down to 30 minutes, and adverse operator influence on the results is greatly reduced. By saving valuable operator time without sacrificing data consistency, the auto-trim accessory provides return on investment in less than 2 years. The auto-trim accessory empowers your lab to run more tests with confidence, accelerating product development and time to market.
What will you accomplish with 80% more operator free time?
- Technology
-
Technology
The new patent pending auto-trim accessory uses Smart SwapTM technology to transform a standard DHR 10, 20, or 30 into a semi-automated polymer melt rheometer! Testing procedures are the exact same as using the standard parallel plate geometry with a melt ring, but the auto-trim accessory replaces the melt ring with a disposable trimmer which automatically removes all the excess sample at the appropriate time. The trimming action ensures that each test is run with the appropriate sample volume for repeatable results. The sample is trimmed with high consistency due to each test using a new trimmer. The auto-trim accessory is rated to 325 °C and compatible with the ETC oven.
- Features & Benefits
-
Features & Benefits:
Increase Productivity
By automating most of the experiment, users gain 80% more walk-away time. Additionally, new users can be trained to confidently generate high quality polymer melt rheology data in less than 30 minutes.
Improve Data Consistency
Enhance your site-to-site and operator-to-operator consistency for polymer critical quality attributes (CQA) saving you time and money.
Retain Versatility
Automation doesn’t require giving up the other capabilities of your rheometer. Users can swap accessories in less than 10 seconds to support full polymer processing characterization. Switch from automated melt rheology procedures to testing solids in DMA mode as well as extension with the Extensional Viscosity Accessory.
Maximize Investment
The auto-trim accessory pays for itself in less than two years by saving valuable operator testing and training time. Compared to available automated alternatives, automation on the DHR offers substantially faster lead time for a fraction of the cost.
- Increases operator walk-away time by 80%, requiring less than two minutes of operator time per test with fully-programmed test methods.
- Excellent data consistency through automatic removal of excess material – Better data consistency than manual trimming, even when comparing data from an expert rheologist with results from multiple operators with limited experience
- Training time reduced from 2 weeks to under 30 minutes via plug and play accessories, while still achieving high quality data
- Realize the benefits of automation while maintaining the versatility to perform Dynamic Mechanical Analysis (DMA), extensional viscosity, and other rheological measurements thanks to SmartSwap technology.
- Eliminates the need to open the chamber during a test, preventing temperature fluctuations on the sample and maintaining the inert environment
- Suitable for testing pellets, disks, and flakes with no modification necessary
- Confirm pre-test process and trim quality with automatic before and after trimming photos from the optional ETC camera
- Applications
-
Comparison of crossover modulus (Gc) for manual trimming and the auto-trim accessory on Acrylonitrile Butadiene Styrene (ABS)
Crossover modulus is a common polymer melt measurement because it provides a consistent measurement of molecular weight and molecular weight distribution. Measuring crossover modulus is a very useful method to validate a batch of material or predict processability.
Acrylonitrile butadiene styrene (ABS) is a notoriously challenging and time-consuming material to perform melt rheology on due to the long relaxation time and high sensitivity to trimming practices. The manual data has a Coefficient of Variation (COV) of 9.1% and required approximately 21 minutes of expert operator time per test to allow sufficient relaxation time. The data using the auto-trim accessory had a COV of 3.1% and only required less than 2 minutes of hands on-time from the operator. The slight shift in the average value is due to the auto-trim accessory trimming the material with a shearing motion along the axis of the geometry. Manual trimming is typically performed in a circumferential direction resulting in some material being ‘dragged’ out from between the plates, showing an artificially low modulus measurement. This data shows how the design of the auto-trim accessory produces extremely consistent trimming action and is inherently independent of operator influence, even for highly challenging materials.
- Resources
-
- Tech Brief: Polymer Melt Rheology Workflow Automation: Auto-Trim Accessory for Discovery Hybrid Rheometers
- Application Note: Polymer Flow and Mechanical Characterization for Material Development, Processing, and Performance
- Tech Tip: How to Set Up the Auto-Trim Accessory for the Discovery Hybrid Rheometer
- Rheometer Accessories Brochure
- Discovery Hybrid Rheometers
- Request a Quote
- Video
-