El TGA DynTHERM es un instrumento gravimétrico avanzado para análisis termogravimétrico de alta presión y alta temperatura.
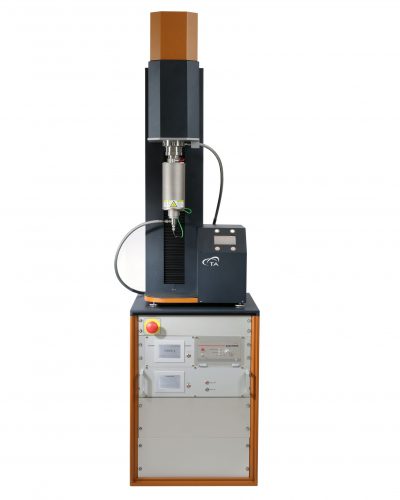
El TGA DynTHERM es un instrumento gravimétrico avanzado que cuenta con una balanza de suspensión magnética patentada* que permite medir cambios de peso de materiales en condiciones de presión alta, en presencia de diversos gases y vapores, de temperatura ambiente hasta 1700 °C. Una selección flexible de dispositivos de dosificación y mezcla de gas y vapor proporcionan un control preciso de la composición y la presión de la atmósfera de reacción. Diseñado y construido con más de 20 años de experiencia y probado en el campo por cientos de clientes, el TGA DynTHERM de la serie Rubotherm ofrece el más amplio rango de temperatura y presión de todos los analizadores gravimétricos de alta presión y representa el estándar de la industria para análisis relevantes para aplicaciones.
* Patente alemana n.° 10 2009 009 204.8
Características y ventajas:
- El pesaje de muestras sin contacto permite la separación hermética entre la celda de muestra y la balanza, lo que elimina el riesgo de daño de balanza de los gases con reacción, la presión o la temperatura dentro de la celda de muestra
- La celda del reactor de muestras sellada metálicamente permite realizar mediciones en gases con reacción tóxica, explosiva o corrosiva, a temperaturas altas, y desde vacío a alta presión
- El exclusivo desacoplamiento automático de muestra permite la tara de balanza durante experimentos y proporciona estabilidad de referencia inigualable a largo plazo, para lograr las mediciones más precisas sin las calibraciones de balanza manual que requieren los dispositivos de la competencia
- Se puede calentar la celda de muestras completa humedecida mediante gases de reacción, evitando la condensación de vapores de gas de reacción, como vapor de agua, CO2, amoníaco, etc., incluso a altas presiones o humedad
- Sistemas sofisticados de control de presión, mezcla y dosificación de gas y vapor para el control preciso de la atmósfera de reacción con muestreo de gas integrado para análisis de gas emitido
- El gran rango de pesaje dinámico y el volumen de la muestra permiten realizar mediciones con muestras representativas, grandes o pesadas
En la tabla a continuación, se resumen las especificaciones clave de 8 modelos de TGA DynTHERM de la serie Rubotherm equipados con balanza de suspensión magnética.
Todos los modelos pueden operar en vacío. Los sistemas de dosificación de gas están equipados con dos líneas de gas, cada una con un MFC separado, de forma estándar. Opcionalmente, se pueden agregar más líneas de gas al sistema de dosificación.
Una característica opcional especial de los modelos de TGA DynTHERM es la posibilidad de contar con un flujo forzado de la atmósfera de reacción a través del lecho fijo de la muestra. Esto ha demostrado ser una opción extremadamente útil para la investigación de catalizadores, dado que se pueden producir las condiciones reales de funcionamiento de la muestra del catalizador en el DynTHERM.
Model |
Max. Sample Temperature | Maximum Pressure | Weighing Resolution | Weighing Range / Sample Mass | Reaction Atmosphere |
---|---|---|---|---|---|
1100-1 , LP-G | 1100°C | 1 bar | 10 µg | 20 g / 25 g | Pure Gas & Gas Blends (of up to 5 gases) |
1700-1 , LP-G | 1700°C | 1 bar | 10 µg | 20 g / 25 g | Pure Gas & Gas Blends (of up to 5 gases) |
1100-50 , HP-G 1100-50 , HP-G+V |
1100°C | 50 bar* | 10 µg | 20 g / 25 g | Pure Gas & Gas Blends (of up to 5 gases) Pure Gas & Gas Blends & Gas and steam Blends (of up to 5 gases and 1 steam) |
1500-50 , HP-G 1500-50 , HP-G+V |
1500°C | 50 bar* | 10 µg | 20 g / 25 g | Pure Gas & Gas Blends (of up to 5 gases) Pure Gas & Gas Blends & Gas and steam Blends (of up to 5 gases and 1 steam) |
*Maximum pressure is temperature dependent
Consulte con su agente de ventas técnicas de TA local para obtener más información acerca de los instrumentos del TGA DynTHERM de la serie Rubotherm.
Balanza de suspensión magnética
Exclusiva tecnología de balanza de suspensión magnética
En el corazón de cada instrumento de la serie Rubotherm, se encuentra la balanza de suspensión magnética (MSB), que pesa una muestra en una celda de reactor cerrada con una microbalanza externa. Esto es posible gracias a un acoplamiento de suspensión magnética que transmite la fuerza del peso a través de la pared de la celda de muestra.
En este diseño, se conecta un imán de suspensión permanente en la parte superior de un eje de suspensión interna superior. Se conecta un eje de suspensión interna inferior a un crisol que sostiene un material de muestra. Entre los ejes de suspensión superior e inferior se encuentra un mecanismo de acoplamiento de carga. Los ejes superior e inferior, y el crisol de muestra, están encerrados dentro de la celda de muestra.
Un electromagneto externo se controla para atraer al imán permanente interno. Esto eleva el imán de suspensión interno y conecta el acoplamiento de carga y, como resultado, eleva el crisol de muestra. El control electromagnético continúa aplicando fuerza atractiva hasta que el sistema alcanza una altura de punto de medición constante.
El peso de la muestra en la celda se determina por la microbalanza externa, a la que está conectado el electromagneto, con alta resolución y precisión.
Función de desacoplamiento automático de muestra (ASD)
Función de desacoplamiento automático de muestra (ASD)
En el inicio de cualquier experimento gravimétrico, la balanza se tara y se calibra automáticamente para establecer un “punto cero” para la medición de peso. El punto cero es el valor usado para todas las mediciones posteriores. Sin embargo, dado que los marcos de tiempo de los experimentos pueden variar de horas a semanas, la capacidad de medir con precisión cambios de peso pequeños en tiempos extendidos puede disminuir por la desviación en el punto cero. La desviación en general se debe a factores externos, como fluctuaciones en la temperatura del laboratorio y en la presión de aire o la humedad.
Los intentos por mejorar la precisión de señal fueron realizar tradicionalmente ejecuciones de referencia con el crisol vacío y restarlas de la ejecución de muestra. Este método no es ideal, ya que duplica los tiempos de los experimentos y es inherentemente defectuoso ya que no hay dos experimentos exactamente iguales. Solo el TGA DynTHERM de TA, con tecnología de MSB patentada, proporciona la función exclusiva de desacoplamiento automático de muestras (ASD) para correcciones de desviación en tiempo real, lo que aumenta la precisión del peso a niveles anteriormente no logrados, especialmente para mediciones a largo plazo.
Cómo funciona ASD:
Tal como se muestra en la figura anterior, el diseño MSB incluye un acoplamiento de carga de eje. Cuando el electromagneto recibe energía, atrae al imán permanente que está conectado al eje superior. El eje superior se eleva, se conecta al acoplamiento, y eleva el crisol hasta el punto de medición para realizar la medición de peso. En cualquier momento durante el experimento, el imán de suspensión permanente se puede desplazar hacia abajo para desacoplarlo del crisol de muestra. Durante este movimiento descendente, el acoplamiento de carga del eje se coloca suspendido en un soporte. El imán de suspensión permanece en un estado de flotación libre, y transfiere su peso a la balanza. Al realizar el movimiento hasta esta nueva posición de punto cero correspondiente a la balanza sin carga, son posibles la tara y la calibración durante las mediciones, incluso en condiciones de proceso (presión, temperatura) en la celda de muestra. Esta exclusiva calibración automática controlada por software de la balanza, durante las mediciones, está disponible SOLO en el analizador gravimétrico comercial de TA Instruments.
Flujo de gas forzado a través de lechos de material a granel
Flujo de gas forzado a través de lechos de material a granel
El TGA DynTHERM cuenta con una opción exclusiva de flujo de gas forzado para aplicaciones que requieren un flujo forzado de gas de reacción a través del lecho del material de la muestra. Esta capacidad, que permite imitar las condiciones reales de proceso de un material en un reactor a granel, se demuestra en el esquema anterior.
Para las mediciones de flujo de gas forzado, la muestra se coloca en un recipiente con un fondo «similar a un tamiz» y una tapa con brida con una abertura en el centro. Cuando la balanza se encuentra en el punto cero, la brida del recipiente de la muestra se apoya sobre un soporte que no permite desviaciones. El recipiente de la muestra se desconecta de la balanza y se fuerza el gas de reacción para que fluya hacia el interior del recipiente desde la abertura en su parte superior, pase a través de la muestra y finalmente salga por el fondo «similar a un tamiz».
La muestra se pesa en intervalos de tiempo especificados al elevar la MSB a la posición de medición, lo que levanta el recipiente de la muestra de los soportes. Una vez finalizada la medición de peso, el recipiente de la muestra regresa a la posición de reposo para volver a iniciar el proceso.
Reactores ambientales
Reactores ambientales
Los instrumentos TGA DynTHERM están equipados con celdas de muestra de presión alta o baja con calentadores eléctricos para un control preciso de la temperatura en todas las condiciones de presión y flujo de gas.
Diseño de reactor de pared fría
La instalación del calentador eléctrico en un recipiente a presión – la configuración del reactor de pared fría – permite que se utilicen solo materiales cerámicos resistentes a la corrosión en la zona de temperatura elevada. Los calentadores de pared fría se pueden aplicar mediante la utilización de atmósferas de reacción sumamente corrosiva en un rango de temperatura de hasta 1500 °C* y a presiones de hasta 50 bar*.
Diseño de reactor de pared caliente
Los reactores de pared caliente son celdas de muestra de cerámica o aleaciones de metales especiales resistentes a la temperatura y a la corrosión. La temperatura de la muestra en el reactor se controla mediante un calentador eléctrico externo que calienta la muestra a través de la pared. Los reactores de pared caliente proporcionan zonas de temperatura constante particularmente grandes para mediciones en un rango de temperatura de hasta 1700 °C*.
Control de la temperatura
La temperatura de la muestra se mide mediante un termopar directamente adyacente a la muestra en el gas de reacción. La temperatura del horno y las temperaturas en otras partes del reactor se miden con termopares adicionales. Un controlador de temperatura PID veloz realiza un control preciso de la temperatura de la muestra en todas las condiciones de funcionamiento.
* Las especificaciones varían según el modelo
Sistemas de dosificación de gas y vapor
Sistemas de control de presión, mezcla y dosificación de gas y vapor
La presión de las mediciones de TGA depende del control preciso de la presión y la composición de la atmósfera de reacción. El TGA DynTHERM cuenta con tres sistemas sofisticados de mezcla y dosificación de vapor y gas, con controladores de presión que garantizan la más alta calidad de los datos, al mismo tiempo que proporcionan flexibilidad para abordar el más amplio rango de aplicaciones. Estos sistemas proporcionan un flujo continuo de gas de reacción puro, una mezcla de gases o una mezcla de gas y vapor con una composición controlada a la celda del reactor de muestras de TGA. Un controlador de contrapresión dinámico en el flujo de salida mantiene la presión con máxima estabilidad y precisión.
Cada sistema de dosificación comprende dos controladores de flujo de masa (MFC 1, MFC 2) para dosificar gas puro o combinar mezclas de gases y dosificar al reactor de TGA, un sensor de presión preciso (P), un controlador PID, una válvula de control de presión (PCV) en el flujo de gas en la salida del reactor y una conexión de muestreo de gas para análisis de gas emitido (EGA). Se pueden añadir líneas de gas adicionales con controladores de flujo de masa de forma opcional.
Los sistemas de dosificación de gas y vapor también cuentan con un generador de vapor que consta de una bomba de compresión de líquido y control de flujo (LFC) para dosificar un flujo controlado de líquido en un vaporizador en el cual se genera el vapor. Luego, el vapor se mezcla con los flujos de gas provenientes de los MFC y se traslada hacia el reactor de TGA a través de líneas de transferencia calentadas.
Pirólisis y gasificación
Pirólisis y gasificación
El carbón, la biomasa, los desechos y otros materiales orgánicos se gasifican para la utilización de energía o como materia prima alternativa. Estos procesos se pueden medir en condiciones pertinentes a las aplicaciones en los instrumentos de TGA de alta presión DynTHERM configurados con dosificación de gas y vapor. El primer paso en los procesos de gasificación es la pirólisis de la materia prima, mediante la cual mientras se calientan los materiales orgánicos en una atmósfera inerte (p. ej. N2 o Ar), los componentes volátiles (agua, hidrocarburos, alquitrán) se evaporan y se genera un residuo carbonoso. La gasificación de este residuo rico en carbono como segundo paso de reacción requiere un agente gasificante, que suele ser vapor. El carbono y el vapor sobrecalentado generan gases en función de la siguiente reacción principal:
H2O + C → CO + H2
Paralelamente, se producen gases adicionales como resultado de conversiones y reacciones secundarias:
mC + nH → CmHn | CO + H2O → H2 + CO2 | CO + 3H2 → CH4 + H2O
Debido a que la cinética de reacción del proceso depende de las condiciones de la reacción y de la materia prima, la composición y la presión de los gases generados variarán. Los instrumentos TGA DynTHERM permiten optimizar las condiciones de funcionamiento para materias primas determinadas. Además, se pueden equipar con un espectrómetro de masas para el análisis de gas emitido. En el primer diagrama, se muestra la cinética de un proceso de pirólisis y gasificación de carbón a 900 °C y 10 bar. En el último diagrama, se compara la pirólisis y gasificación de una biomasa (cáscara de arroz) para 7 bar y 10 bar. En ambos experimentos, la pirólisis se realiza al principio, durante el calentamiento de la muestra en gas inerte. Después de la pirólisis, se inicia la gasificación cuando se inyecta vapor y produce el cambio de masa principal de los materiales de la muestra.
Coquización del catalizador
Coquización del catalizador
La desactivación de catalizadores por coquización es un problema tecnológico y económico inevitable en el refinado de petróleo y en la industria petroquímica. La coquización se produce cuando los gases de alimentación ricos en hidrocarburos reaccionan con el catalizador y se acumulan depósitos de carbono sólido en la superficie de este. Estos depósitos que contienen carbono pueden alcanzar con facilidad y de forma rápida un nivel en el que alteran el proceso. Por ejemplo, pueden crear problemas de caída de presión u obstrucción de sitios catalíticos. Los métodos para prevenir o retrasar la desactivación de catalizadores comprenden la modificación de la composición de la superficie del catalizador o el cambio del entorno de reacción (presión, temperatura y composición del gas de alimentación). Después de la desactivación, se puede analizar la regeneración alternativa mediante la quema de residuos de carbón.
La optimización del proceso de decaimiento o regeneración de catalizadores es un problema de ingeniería que requiere un conocimiento de la cinética de desactivación del catalizador. Los instrumentos TGA DynTHERM permiten estudiar el peso del catalizador y el desarrollo de la coquización en condiciones de funcionamiento reales de las refinerías.
El diagrama a continuación muestra un ejemplo de la acumulación de coque en un material catalítico a 20 bar y 650 °C en una atmósfera reactiva de CH4 y vapor. La presión parcial del vapor se reduce de forma gradual, lo que conduce al aumento de masa del material catalítico debido a la formación de coque. La tasa máxima específica de deposición de coque calculada a partir de la curva azul de la figura, en miligramos por gramos de catalizador por segundo, es de 0,32 mg g-1 s-1.
En la figura inferior, el inicio de la coquización en un catalizador comercial a 700 °C y 20 bar se mide en una mezcla de vapor/CH4 con una velocidad de flujo de 70 ml/min. Se observó un aumento en la tasa de coquización cuando se incrementó la velocidad de flujo de CH4 a 73 ml/min, con una velocidad de flujo de vapor constante.
Corrosión y oxidación
Corrosión y oxidación
Que los materiales cuenten con una mejor resistencia a la corrosión es clave para mejorar la eficiencia de muchos procesos técnicos. Por ejemplo, la eficiencia de motores a reacción y las turbinas de gas o de vapor está directamente relacionada con su capacidad para resistir la corrosión a la temperatura de funcionamiento máxima.
Los instrumentos TGA DynTHERM ofrecen reactores resistentes a la corrosión capaces de medir materiales en atmósferas corrosivas a temperatura elevada. Para muchos materiales, el instrumento puede alojar muestras grandes (tanto en masa como en volumen), lo cual es ventajoso dado que el cambio de masa que provoca la corrosión tiende a ser muy pequeño. Además, la corrosión a alta temperatura suele ser un proceso lento. La capacidad de la MSB patentada de tara y calibración de la balanza durante la medición permite realizar los estudios de corrosión a largo plazo más precisos.
El diagrama a continuación muestra un estudio a largo plazo sobre el aumento de masa de una muestra de titanio con recubrimiento de diamante. El aumento de peso se debe a la oxidación de la muestra en oxígeno puro a 600 °C. Aquí, el cambio de masa total es de, aproximadamente, 140 μg en 6 días.
En el diagrama a continuación, se muestra el aumento de peso de una aleación de Inconel®* C-276 de alto rendimiento en aire a 1000 °C y a dos presiones diferentes, de 2 bar y 80 bar. Las muestras de la aleación tenían una masa inicial de 89 mg y una superficie de 0,47 cm2. Los aumentos de peso observados son el resultado de la oxidación de la superficie de la aleación de metal. La velocidad de corrosión es 5 veces mayor a presión elevada. El cambio de peso a presión elevada parece aproximarse a la saturación, lo que indica la formación de una capa oxídica estable. El aumento de peso oxidativo específico de la superficie después de 6 horas fue de 610 μg/cm2 a 2 bar y de 3080 μg/cm2 a 80 bar.
Recirculación química
Recirculación química
La combustión de combustibles fósiles en oxígeno casi puro, en lugar de aire, presenta una oportunidad para simplificar la captura de dióxido de carbono en las aplicaciones de las plantas generadoras de energía. Los sistemas de recirculación química suministran oxígeno interno al proceso, lo que elimina grandes costos de capital y de operación relacionados con la generación de oxígeno previa a la combustión. La combustión por recirculación química (CLC) se considera una tecnología de transformación con el potencial de cumplir con los costos programáticos y los objetivos de rendimiento para la generación de electricidad con reducción de CO2 a partir de combustibles fósiles.
En los sistemas de CLC, el oxígeno se introduce a través de ciclos de oxidación-reducción de un material portador de oxígeno. El portador de oxígeno suele ser un compuesto sólido de base metálica. En un proceso de CLC típico, la combustión se divide en reactores de reducción y oxidación separados, como se muestra en el esquema a continuación. El óxido metálico suministra oxígeno para la combustión y se reduce por la acción del combustible en el reactor de combustible, que funciona a temperatura elevada.
Esta reacción puede ser exotérmica o endotérmica, en función del combustible y del portador de oxígeno. El producto de la combustión del reactor de combustible es un flujo de CO2 y H2O sumamente concentrado que se puede purificar, comprimir y almacenar para su posterior uso beneficioso. Luego, el portador de oxígeno reducido se envía al reactor de aire, que también funciona a temperatura elevada, donde se regenera a su estado oxidado. El reactor de aire produce un flujo de aire caliente, usado, que se utiliza para producir vapor para accionar una turbina generadora de energía. A continuación, el portador de oxígeno regresa al reactor de combustible y se reinicia el ciclo de reducción-oxidación.
Los esfuerzos actuales de I+D de CLC se centran en el desarrollo de materiales portadores de oxígeno con suficiente capacidad de oxígeno y durabilidad para soportar entornos de CLC difíciles. Los instrumentos TGA DynTHERM permiten medir el peso de los materiales portadores de oxígeno en condiciones de operación reales, lo que comprende someter los materiales a varios ciclos de oxidación y reducción a temperaturas y presiones elevadas, alternando entre vapor o gases oxidantes y reductores (inflamables).
El diagrama a continuación muestra el resultado del ciclado de un material portador de oxígeno a 10 bar y 800 °C. El material se reduce en H2 humidificado y se oxida en aire seco. Los cambios de peso registrados en los ciclos de reducción-oxidación son bastante constantes y ascienden aproximadamente al 9 % del peso inicial de la muestra.
- Descripción
-
El TGA DynTHERM es un instrumento gravimétrico avanzado que cuenta con una balanza de suspensión magnética patentada* que permite medir cambios de peso de materiales en condiciones de presión alta, en presencia de diversos gases y vapores, de temperatura ambiente hasta 1700 °C. Una selección flexible de dispositivos de dosificación y mezcla de gas y vapor proporcionan un control preciso de la composición y la presión de la atmósfera de reacción. Diseñado y construido con más de 20 años de experiencia y probado en el campo por cientos de clientes, el TGA DynTHERM de la serie Rubotherm ofrece el más amplio rango de temperatura y presión de todos los analizadores gravimétricos de alta presión y representa el estándar de la industria para análisis relevantes para aplicaciones.
* Patente alemana n.° 10 2009 009 204.8
- Características
-
Características y ventajas:
- El pesaje de muestras sin contacto permite la separación hermética entre la celda de muestra y la balanza, lo que elimina el riesgo de daño de balanza de los gases con reacción, la presión o la temperatura dentro de la celda de muestra
- La celda del reactor de muestras sellada metálicamente permite realizar mediciones en gases con reacción tóxica, explosiva o corrosiva, a temperaturas altas, y desde vacío a alta presión
- El exclusivo desacoplamiento automático de muestra permite la tara de balanza durante experimentos y proporciona estabilidad de referencia inigualable a largo plazo, para lograr las mediciones más precisas sin las calibraciones de balanza manual que requieren los dispositivos de la competencia
- Se puede calentar la celda de muestras completa humedecida mediante gases de reacción, evitando la condensación de vapores de gas de reacción, como vapor de agua, CO2, amoníaco, etc., incluso a altas presiones o humedad
- Sistemas sofisticados de control de presión, mezcla y dosificación de gas y vapor para el control preciso de la atmósfera de reacción con muestreo de gas integrado para análisis de gas emitido
- El gran rango de pesaje dinámico y el volumen de la muestra permiten realizar mediciones con muestras representativas, grandes o pesadas
- Especificaciones
-
En la tabla a continuación, se resumen las especificaciones clave de 8 modelos de TGA DynTHERM de la serie Rubotherm equipados con balanza de suspensión magnética.
Todos los modelos pueden operar en vacío. Los sistemas de dosificación de gas están equipados con dos líneas de gas, cada una con un MFC separado, de forma estándar. Opcionalmente, se pueden agregar más líneas de gas al sistema de dosificación.
Una característica opcional especial de los modelos de TGA DynTHERM es la posibilidad de contar con un flujo forzado de la atmósfera de reacción a través del lecho fijo de la muestra. Esto ha demostrado ser una opción extremadamente útil para la investigación de catalizadores, dado que se pueden producir las condiciones reales de funcionamiento de la muestra del catalizador en el DynTHERM.
Model
Max. Sample Temperature Maximum Pressure Weighing Resolution Weighing Range / Sample Mass Reaction Atmosphere 1100-1 , LP-G 1100°C 1 bar 10 µg 20 g / 25 g Pure Gas & Gas Blends (of up to 5 gases) 1700-1 , LP-G 1700°C 1 bar 10 µg 20 g / 25 g Pure Gas & Gas Blends (of up to 5 gases) 1100-50 , HP-G
1100-50 , HP-G+V1100°C 50 bar* 10 µg 20 g / 25 g Pure Gas & Gas Blends (of up to 5 gases)
Pure Gas & Gas Blends & Gas and steam Blends (of up to 5 gases and 1 steam)1500-50 , HP-G
1500-50 , HP-G+V1500°C 50 bar* 10 µg 20 g / 25 g Pure Gas & Gas Blends (of up to 5 gases)
Pure Gas & Gas Blends & Gas and steam Blends (of up to 5 gases and 1 steam)*Maximum pressure is temperature dependent
Consulte con su agente de ventas técnicas de TA local para obtener más información acerca de los instrumentos del TGA DynTHERM de la serie Rubotherm.
- Tecnología
-
Balanza de suspensión magnética
Exclusiva tecnología de balanza de suspensión magnética
En el corazón de cada instrumento de la serie Rubotherm, se encuentra la balanza de suspensión magnética (MSB), que pesa una muestra en una celda de reactor cerrada con una microbalanza externa. Esto es posible gracias a un acoplamiento de suspensión magnética que transmite la fuerza del peso a través de la pared de la celda de muestra.
En este diseño, se conecta un imán de suspensión permanente en la parte superior de un eje de suspensión interna superior. Se conecta un eje de suspensión interna inferior a un crisol que sostiene un material de muestra. Entre los ejes de suspensión superior e inferior se encuentra un mecanismo de acoplamiento de carga. Los ejes superior e inferior, y el crisol de muestra, están encerrados dentro de la celda de muestra.
Un electromagneto externo se controla para atraer al imán permanente interno. Esto eleva el imán de suspensión interno y conecta el acoplamiento de carga y, como resultado, eleva el crisol de muestra. El control electromagnético continúa aplicando fuerza atractiva hasta que el sistema alcanza una altura de punto de medición constante.
El peso de la muestra en la celda se determina por la microbalanza externa, a la que está conectado el electromagneto, con alta resolución y precisión.
Función de desacoplamiento automático de muestra (ASD)
Función de desacoplamiento automático de muestra (ASD)
En el inicio de cualquier experimento gravimétrico, la balanza se tara y se calibra automáticamente para establecer un “punto cero” para la medición de peso. El punto cero es el valor usado para todas las mediciones posteriores. Sin embargo, dado que los marcos de tiempo de los experimentos pueden variar de horas a semanas, la capacidad de medir con precisión cambios de peso pequeños en tiempos extendidos puede disminuir por la desviación en el punto cero. La desviación en general se debe a factores externos, como fluctuaciones en la temperatura del laboratorio y en la presión de aire o la humedad.
Los intentos por mejorar la precisión de señal fueron realizar tradicionalmente ejecuciones de referencia con el crisol vacío y restarlas de la ejecución de muestra. Este método no es ideal, ya que duplica los tiempos de los experimentos y es inherentemente defectuoso ya que no hay dos experimentos exactamente iguales. Solo el TGA DynTHERM de TA, con tecnología de MSB patentada, proporciona la función exclusiva de desacoplamiento automático de muestras (ASD) para correcciones de desviación en tiempo real, lo que aumenta la precisión del peso a niveles anteriormente no logrados, especialmente para mediciones a largo plazo.
Cómo funciona ASD:
Tal como se muestra en la figura anterior, el diseño MSB incluye un acoplamiento de carga de eje. Cuando el electromagneto recibe energía, atrae al imán permanente que está conectado al eje superior. El eje superior se eleva, se conecta al acoplamiento, y eleva el crisol hasta el punto de medición para realizar la medición de peso. En cualquier momento durante el experimento, el imán de suspensión permanente se puede desplazar hacia abajo para desacoplarlo del crisol de muestra. Durante este movimiento descendente, el acoplamiento de carga del eje se coloca suspendido en un soporte. El imán de suspensión permanece en un estado de flotación libre, y transfiere su peso a la balanza. Al realizar el movimiento hasta esta nueva posición de punto cero correspondiente a la balanza sin carga, son posibles la tara y la calibración durante las mediciones, incluso en condiciones de proceso (presión, temperatura) en la celda de muestra. Esta exclusiva calibración automática controlada por software de la balanza, durante las mediciones, está disponible SOLO en el analizador gravimétrico comercial de TA Instruments.
Flujo de gas forzado a través de lechos de material a granel
Flujo de gas forzado a través de lechos de material a granel
El TGA DynTHERM cuenta con una opción exclusiva de flujo de gas forzado para aplicaciones que requieren un flujo forzado de gas de reacción a través del lecho del material de la muestra. Esta capacidad, que permite imitar las condiciones reales de proceso de un material en un reactor a granel, se demuestra en el esquema anterior.
Para las mediciones de flujo de gas forzado, la muestra se coloca en un recipiente con un fondo «similar a un tamiz» y una tapa con brida con una abertura en el centro. Cuando la balanza se encuentra en el punto cero, la brida del recipiente de la muestra se apoya sobre un soporte que no permite desviaciones. El recipiente de la muestra se desconecta de la balanza y se fuerza el gas de reacción para que fluya hacia el interior del recipiente desde la abertura en su parte superior, pase a través de la muestra y finalmente salga por el fondo «similar a un tamiz».
La muestra se pesa en intervalos de tiempo especificados al elevar la MSB a la posición de medición, lo que levanta el recipiente de la muestra de los soportes. Una vez finalizada la medición de peso, el recipiente de la muestra regresa a la posición de reposo para volver a iniciar el proceso.
Reactores ambientales
Reactores ambientales
Los instrumentos TGA DynTHERM están equipados con celdas de muestra de presión alta o baja con calentadores eléctricos para un control preciso de la temperatura en todas las condiciones de presión y flujo de gas.
Diseño de reactor de pared fría
La instalación del calentador eléctrico en un recipiente a presión – la configuración del reactor de pared fría – permite que se utilicen solo materiales cerámicos resistentes a la corrosión en la zona de temperatura elevada. Los calentadores de pared fría se pueden aplicar mediante la utilización de atmósferas de reacción sumamente corrosiva en un rango de temperatura de hasta 1500 °C* y a presiones de hasta 50 bar*.
Diseño de reactor de pared caliente
Los reactores de pared caliente son celdas de muestra de cerámica o aleaciones de metales especiales resistentes a la temperatura y a la corrosión. La temperatura de la muestra en el reactor se controla mediante un calentador eléctrico externo que calienta la muestra a través de la pared. Los reactores de pared caliente proporcionan zonas de temperatura constante particularmente grandes para mediciones en un rango de temperatura de hasta 1700 °C*.
Control de la temperatura
La temperatura de la muestra se mide mediante un termopar directamente adyacente a la muestra en el gas de reacción. La temperatura del horno y las temperaturas en otras partes del reactor se miden con termopares adicionales. Un controlador de temperatura PID veloz realiza un control preciso de la temperatura de la muestra en todas las condiciones de funcionamiento.
* Las especificaciones varían según el modelo
Sistemas de dosificación de gas y vapor
Sistemas de control de presión, mezcla y dosificación de gas y vapor
La presión de las mediciones de TGA depende del control preciso de la presión y la composición de la atmósfera de reacción. El TGA DynTHERM cuenta con tres sistemas sofisticados de mezcla y dosificación de vapor y gas, con controladores de presión que garantizan la más alta calidad de los datos, al mismo tiempo que proporcionan flexibilidad para abordar el más amplio rango de aplicaciones. Estos sistemas proporcionan un flujo continuo de gas de reacción puro, una mezcla de gases o una mezcla de gas y vapor con una composición controlada a la celda del reactor de muestras de TGA. Un controlador de contrapresión dinámico en el flujo de salida mantiene la presión con máxima estabilidad y precisión.
Cada sistema de dosificación comprende dos controladores de flujo de masa (MFC 1, MFC 2) para dosificar gas puro o combinar mezclas de gases y dosificar al reactor de TGA, un sensor de presión preciso (P), un controlador PID, una válvula de control de presión (PCV) en el flujo de gas en la salida del reactor y una conexión de muestreo de gas para análisis de gas emitido (EGA). Se pueden añadir líneas de gas adicionales con controladores de flujo de masa de forma opcional.
Los sistemas de dosificación de gas y vapor también cuentan con un generador de vapor que consta de una bomba de compresión de líquido y control de flujo (LFC) para dosificar un flujo controlado de líquido en un vaporizador en el cual se genera el vapor. Luego, el vapor se mezcla con los flujos de gas provenientes de los MFC y se traslada hacia el reactor de TGA a través de líneas de transferencia calentadas.
- Aplicaciones
-
Pirólisis y gasificación
Pirólisis y gasificación
El carbón, la biomasa, los desechos y otros materiales orgánicos se gasifican para la utilización de energía o como materia prima alternativa. Estos procesos se pueden medir en condiciones pertinentes a las aplicaciones en los instrumentos de TGA de alta presión DynTHERM configurados con dosificación de gas y vapor. El primer paso en los procesos de gasificación es la pirólisis de la materia prima, mediante la cual mientras se calientan los materiales orgánicos en una atmósfera inerte (p. ej. N2 o Ar), los componentes volátiles (agua, hidrocarburos, alquitrán) se evaporan y se genera un residuo carbonoso. La gasificación de este residuo rico en carbono como segundo paso de reacción requiere un agente gasificante, que suele ser vapor. El carbono y el vapor sobrecalentado generan gases en función de la siguiente reacción principal:
H2O + C → CO + H2
Paralelamente, se producen gases adicionales como resultado de conversiones y reacciones secundarias:
mC + nH → CmHn | CO + H2O → H2 + CO2 | CO + 3H2 → CH4 + H2O
Debido a que la cinética de reacción del proceso depende de las condiciones de la reacción y de la materia prima, la composición y la presión de los gases generados variarán. Los instrumentos TGA DynTHERM permiten optimizar las condiciones de funcionamiento para materias primas determinadas. Además, se pueden equipar con un espectrómetro de masas para el análisis de gas emitido. En el primer diagrama, se muestra la cinética de un proceso de pirólisis y gasificación de carbón a 900 °C y 10 bar. En el último diagrama, se compara la pirólisis y gasificación de una biomasa (cáscara de arroz) para 7 bar y 10 bar. En ambos experimentos, la pirólisis se realiza al principio, durante el calentamiento de la muestra en gas inerte. Después de la pirólisis, se inicia la gasificación cuando se inyecta vapor y produce el cambio de masa principal de los materiales de la muestra.
Coquización del catalizador
Coquización del catalizador
La desactivación de catalizadores por coquización es un problema tecnológico y económico inevitable en el refinado de petróleo y en la industria petroquímica. La coquización se produce cuando los gases de alimentación ricos en hidrocarburos reaccionan con el catalizador y se acumulan depósitos de carbono sólido en la superficie de este. Estos depósitos que contienen carbono pueden alcanzar con facilidad y de forma rápida un nivel en el que alteran el proceso. Por ejemplo, pueden crear problemas de caída de presión u obstrucción de sitios catalíticos. Los métodos para prevenir o retrasar la desactivación de catalizadores comprenden la modificación de la composición de la superficie del catalizador o el cambio del entorno de reacción (presión, temperatura y composición del gas de alimentación). Después de la desactivación, se puede analizar la regeneración alternativa mediante la quema de residuos de carbón.
La optimización del proceso de decaimiento o regeneración de catalizadores es un problema de ingeniería que requiere un conocimiento de la cinética de desactivación del catalizador. Los instrumentos TGA DynTHERM permiten estudiar el peso del catalizador y el desarrollo de la coquización en condiciones de funcionamiento reales de las refinerías.
El diagrama a continuación muestra un ejemplo de la acumulación de coque en un material catalítico a 20 bar y 650 °C en una atmósfera reactiva de CH4 y vapor. La presión parcial del vapor se reduce de forma gradual, lo que conduce al aumento de masa del material catalítico debido a la formación de coque. La tasa máxima específica de deposición de coque calculada a partir de la curva azul de la figura, en miligramos por gramos de catalizador por segundo, es de 0,32 mg g-1 s-1.
En la figura inferior, el inicio de la coquización en un catalizador comercial a 700 °C y 20 bar se mide en una mezcla de vapor/CH4 con una velocidad de flujo de 70 ml/min. Se observó un aumento en la tasa de coquización cuando se incrementó la velocidad de flujo de CH4 a 73 ml/min, con una velocidad de flujo de vapor constante.
Corrosión y oxidación
Corrosión y oxidación
Que los materiales cuenten con una mejor resistencia a la corrosión es clave para mejorar la eficiencia de muchos procesos técnicos. Por ejemplo, la eficiencia de motores a reacción y las turbinas de gas o de vapor está directamente relacionada con su capacidad para resistir la corrosión a la temperatura de funcionamiento máxima.
Los instrumentos TGA DynTHERM ofrecen reactores resistentes a la corrosión capaces de medir materiales en atmósferas corrosivas a temperatura elevada. Para muchos materiales, el instrumento puede alojar muestras grandes (tanto en masa como en volumen), lo cual es ventajoso dado que el cambio de masa que provoca la corrosión tiende a ser muy pequeño. Además, la corrosión a alta temperatura suele ser un proceso lento. La capacidad de la MSB patentada de tara y calibración de la balanza durante la medición permite realizar los estudios de corrosión a largo plazo más precisos.
El diagrama a continuación muestra un estudio a largo plazo sobre el aumento de masa de una muestra de titanio con recubrimiento de diamante. El aumento de peso se debe a la oxidación de la muestra en oxígeno puro a 600 °C. Aquí, el cambio de masa total es de, aproximadamente, 140 μg en 6 días.
En el diagrama a continuación, se muestra el aumento de peso de una aleación de Inconel®* C-276 de alto rendimiento en aire a 1000 °C y a dos presiones diferentes, de 2 bar y 80 bar. Las muestras de la aleación tenían una masa inicial de 89 mg y una superficie de 0,47 cm2. Los aumentos de peso observados son el resultado de la oxidación de la superficie de la aleación de metal. La velocidad de corrosión es 5 veces mayor a presión elevada. El cambio de peso a presión elevada parece aproximarse a la saturación, lo que indica la formación de una capa oxídica estable. El aumento de peso oxidativo específico de la superficie después de 6 horas fue de 610 μg/cm2 a 2 bar y de 3080 μg/cm2 a 80 bar.
Recirculación química
Recirculación química
La combustión de combustibles fósiles en oxígeno casi puro, en lugar de aire, presenta una oportunidad para simplificar la captura de dióxido de carbono en las aplicaciones de las plantas generadoras de energía. Los sistemas de recirculación química suministran oxígeno interno al proceso, lo que elimina grandes costos de capital y de operación relacionados con la generación de oxígeno previa a la combustión. La combustión por recirculación química (CLC) se considera una tecnología de transformación con el potencial de cumplir con los costos programáticos y los objetivos de rendimiento para la generación de electricidad con reducción de CO2 a partir de combustibles fósiles.
En los sistemas de CLC, el oxígeno se introduce a través de ciclos de oxidación-reducción de un material portador de oxígeno. El portador de oxígeno suele ser un compuesto sólido de base metálica. En un proceso de CLC típico, la combustión se divide en reactores de reducción y oxidación separados, como se muestra en el esquema a continuación. El óxido metálico suministra oxígeno para la combustión y se reduce por la acción del combustible en el reactor de combustible, que funciona a temperatura elevada.
Esta reacción puede ser exotérmica o endotérmica, en función del combustible y del portador de oxígeno. El producto de la combustión del reactor de combustible es un flujo de CO2 y H2O sumamente concentrado que se puede purificar, comprimir y almacenar para su posterior uso beneficioso. Luego, el portador de oxígeno reducido se envía al reactor de aire, que también funciona a temperatura elevada, donde se regenera a su estado oxidado. El reactor de aire produce un flujo de aire caliente, usado, que se utiliza para producir vapor para accionar una turbina generadora de energía. A continuación, el portador de oxígeno regresa al reactor de combustible y se reinicia el ciclo de reducción-oxidación.
Los esfuerzos actuales de I+D de CLC se centran en el desarrollo de materiales portadores de oxígeno con suficiente capacidad de oxígeno y durabilidad para soportar entornos de CLC difíciles. Los instrumentos TGA DynTHERM permiten medir el peso de los materiales portadores de oxígeno en condiciones de operación reales, lo que comprende someter los materiales a varios ciclos de oxidación y reducción a temperaturas y presiones elevadas, alternando entre vapor o gases oxidantes y reductores (inflamables).
El diagrama a continuación muestra el resultado del ciclado de un material portador de oxígeno a 10 bar y 800 °C. El material se reduce en H2 humidificado y se oxida en aire seco. Los cambios de peso registrados en los ciclos de reducción-oxidación son bastante constantes y ascienden aproximadamente al 9 % del peso inicial de la muestra.
Galería de fotos de TGA DynTHERM
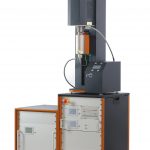
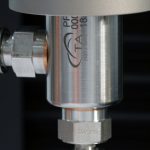
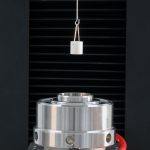
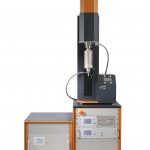
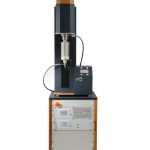
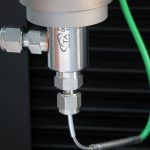
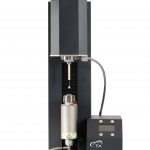
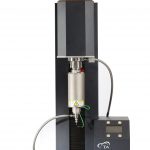
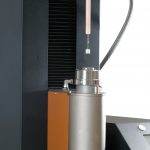
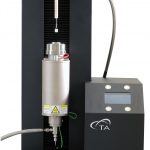