Test Instrument
Combining high-frequency performance and sample pressure control previously unachievable in heart valve durability testing!
Sales Promotions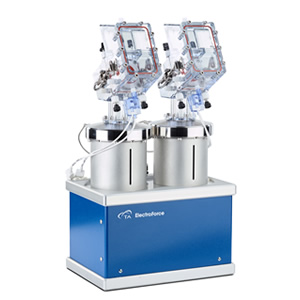
Key Features
- High frequency operation
- PeakIQ™ waveform control to prevent high pressure spikes on valve closing.
- Automatic controls (closed-loop feedback) to maintain test conditions throughout test
- Modular, independent control of each heart valve station
- Simplicity in transfer of heart valve device from durability test instrument to pulse duplicator
- 2, 4, or 6-station unit
- Reliable – 10 year warranty on linear motors
Motor Technology Benefits
Reliable testing
Reliable testing
- 10-year ElectroForce® motor warranty
- ElectroForce motor designed, developed and manufactured by TA Electroforce to exacting standards
- Frictionless design ensures optimal control and long-life for a variety of durability testing applications
High-fidelity, responsive control
High-fidelity, responsive control
- Accurate control and high-resolution performance provides more precise material properties
- Very low motor moving-mass provides industry leading frequency response
Low-force control applications
Low-force control applications
- No motor friction or stiction provides accurate, low-force testing
- Excellent control from gram-force loads to 200N, providing versatility for a variety of tests
Clean, electromagnetic technology
Clean, electromagnetic technology
- Standard ElectroForce® systems can be used in clean rooms or incubators for exceptional versatility
- Efficient electromagnetic power conversion is well-suited for a variety of test environments
Energy-efficient technology
Energy-efficient technology
- Efficient power utilization reduces operating costs
- Lab-friendly instruments and easy installation allows testing to start immediately
- No expensive infrastructure or contamination – saves upfront costs and operating expense
Software Technology Benefits
Easy-to-use, flexible software
Easy-to-use, flexible software
- Test setup and status window to guide users
- Customizable windows and views
- Intuitive and configurable test setup
- Multiple test monitoring sources
Direct control over your data
Direct control over your data
- Customizable and flexible data collection
- Control of data acquisition before and during the test
- Data is stored even if test stops unexpectedly
Real-time test parameter control
Real-time test parameter control
- Adjust waveforms in real-time
- No need to stop test to reconfigure major test parameters
PeakIQ™ Control Algorithm
PeakIQ™ Control Algorithm
- PeakIQ pressure algorithm ensures optimal test conditions as heart valves
change over time - Automatically adjusts command to optimize peak pressure while maintaining desired
threshold for peak pressure duration as desired for ISO 5840 - Prevents high-pressure spikes during valve closing that may lead to unnecessary
valve damage
- Description
-
Using proprietary ElectroForce controls and linear motor technology, the DuraPulse™ Heart Valve Test (HVT) instrument achieves smooth waveform fidelity and precise control for accelerated heart valve durability testing. Automatic PeakIQ™ control algorithms and independent test chambers ensure that established test conditions are maintained on each valve throughout the test. The DuraPulse HVT instrument provides testing to the ISO 5840 standard for heart valve durability assessment.
- Key Features
-
Key Features
- High frequency operation
- PeakIQ™ waveform control to prevent high pressure spikes on valve closing.
- Automatic controls (closed-loop feedback) to maintain test conditions throughout test
- Modular, independent control of each heart valve station
- Simplicity in transfer of heart valve device from durability test instrument to pulse duplicator
- 2, 4, or 6-station unit
- Reliable – 10 year warranty on linear motors
- Technology Benefits
-
Motor Technology Benefits
Reliable testing
Reliable testing
- 10-year ElectroForce® motor warranty
- ElectroForce motor designed, developed and manufactured by TA Electroforce to exacting standards
- Frictionless design ensures optimal control and long-life for a variety of durability testing applications
High-fidelity, responsive control
High-fidelity, responsive control
- Accurate control and high-resolution performance provides more precise material properties
- Very low motor moving-mass provides industry leading frequency response
Low-force control applications
Low-force control applications
- No motor friction or stiction provides accurate, low-force testing
- Excellent control from gram-force loads to 200N, providing versatility for a variety of tests
Clean, electromagnetic technology
Clean, electromagnetic technology
- Standard ElectroForce® systems can be used in clean rooms or incubators for exceptional versatility
- Efficient electromagnetic power conversion is well-suited for a variety of test environments
Energy-efficient technology
Energy-efficient technology
- Efficient power utilization reduces operating costs
- Lab-friendly instruments and easy installation allows testing to start immediately
- No expensive infrastructure or contamination – saves upfront costs and operating expense
Software Technology Benefits
Easy-to-use, flexible software
Easy-to-use, flexible software
- Test setup and status window to guide users
- Customizable windows and views
- Intuitive and configurable test setup
- Multiple test monitoring sources
Direct control over your data
Direct control over your data
- Customizable and flexible data collection
- Control of data acquisition before and during the test
- Data is stored even if test stops unexpectedly
Real-time test parameter control
Real-time test parameter control
- Adjust waveforms in real-time
- No need to stop test to reconfigure major test parameters
PeakIQ™ Control Algorithm
PeakIQ™ Control Algorithm
- PeakIQ pressure algorithm ensures optimal test conditions as heart valves
change over time - Automatically adjusts command to optimize peak pressure while maintaining desired
threshold for peak pressure duration as desired for ISO 5840 - Prevents high-pressure spikes during valve closing that may lead to unnecessary
valve damage
- Video
-
- Resources