Linear Viscoelastic Region: Why It’s Crucial in Materials Testing
Keith Coasey | Morgan Ulrich
September 9, 2024
Our world is brimming with viscoelastic materials: The dough you knead before baking a fresh loaf, the Silly Putty your toddler slaps against the wall, the rubber gaskets that create an airtight seal on an airplane door. Testing those materials by applying controlled deformations (strains) or forces (stresses) at various timescales, temperatures, and/or humidities allows for the optimization of properties and ensures durability and safety. Only through specialized tools in a lab setting can researchers thoroughly characterize (and thus predict in the real world) an essential material property: the linear viscoelastic region.
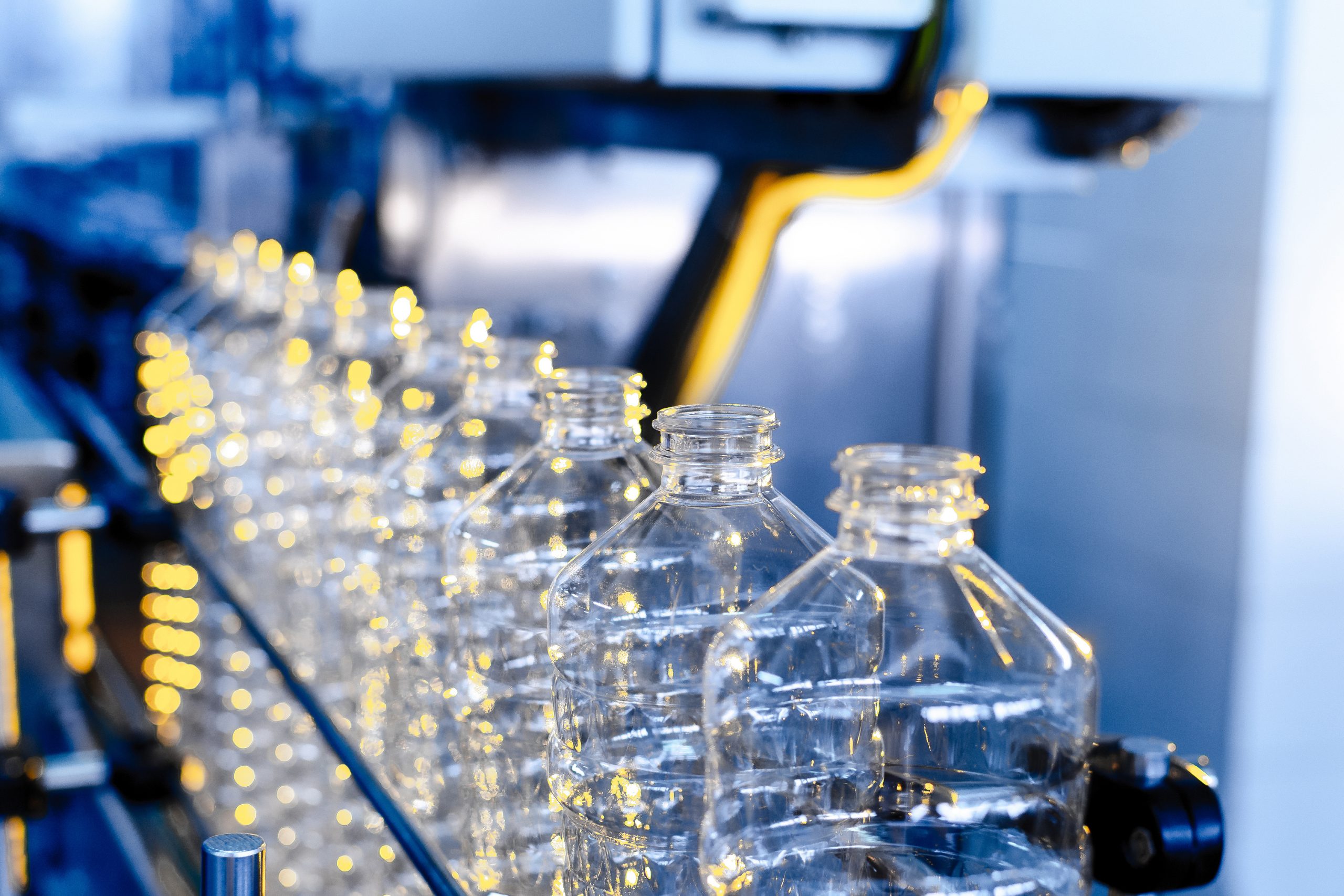
Researchers and product development teams across industries (from construction to food processing to pharmaceuticals and more) work with viscoelastic materials every day. Understanding and accurately modeling viscoelastic behavior supports innovation when developing the snacks you eat, the polymer fibers that make up your clothing, and creating more durable sustainable materials for the structures where you live. Like the word itself, viscoelasticity combines two properties in materials science:
Viscosity: The way material flows over time in response to stress such as gravity (i.e., the slow flow of honey compared to water, comparing the “thickness” of tomato juice to ketchup)
Elasticity: The tendency of a solid to resist deformation (Such as comparing the mechanical resistance of a metal spring to that of a rubber band)
When a material combines both properties (in varying degrees), it’s considered viscoelastic. Ketchup, gelatin, and rubber, for example, all have viscoelastic properties. Although they are drastically different upon first glance, all share solid-like (elastic) and liquid-like (viscous) characteristics, but in different proportions. How, then, do researchers understand the ways those materials change, deform, or even fail under certain types of stress (like flowing, stretching or temperature fluctuation)?
You’ll need to explore the material’s linear viscoelastic region.
What is the Linear Viscoelastic Region (LVR)?
In scientific terms, it’s the linear relationship between the complex stress put on a material and the overall magnitude of deformation (strain), which remains linear at relatively low strains. At strains/stresses that extent beyond the LVR, the relationship becomes nonlinear, with the stress typically increasing less with additional strain, indicative of the onset of network failure. A complex liquid will have a larger LVR than a brittle solid which typically fails at lower strains. In simpler terms, it’s the range in which a material predictably reacts (and can return to its original form) under different amounts of strain/stress.
Think of a rubber band. Pull it gently before letting go, and it will return to its original, relaxed state. Stretch it more and more, and it will still return to form – up to a point. Eventually, you might see a slight tear or a color change when it relaxes. Pull hard enough, and the band will snap altogether. Once you have materially changed the band’s properties, you’ve left the linear viscoelastic region and entered its “critical strain” — the threshold at which the material’s molecular structure fundamentally changes.
Characteristics of the Linear Viscoelastic Region
Determining the LVR should be one of the first steps when studying or testing viscoelastic materials. The LVR is a function of temperature, humidity, and the rate of the deformation. Generally, the LVR increases with increasing temperature, so once the LVR is characterized at a single deformation rate at a specific temperature, the temperature can be increased without exceeding the critical strain.
There are two ways to consider the LVR and its relation to strain/stress. First, when a material is within the LVR, the force (stress) required to deform the material increases or decreases in a fashion relative to the extent deformation. Once stretched beyond the critical deformation, it requires increasingly less additional force to achieve incrementally higher deformations. In another case, if considering hanging weights from a spring or rubber band, one is applying stress (force) in the form of weight in order to deform the sample. Within the LVR, if the weight is incrementally increased, the spring or rubber band will elongate in proportion to the weight. Once beyond the critical strain (which corresponds to a critical stress), the spring or rubber band starts to elongate more and more with each additional unit of stress/weight.
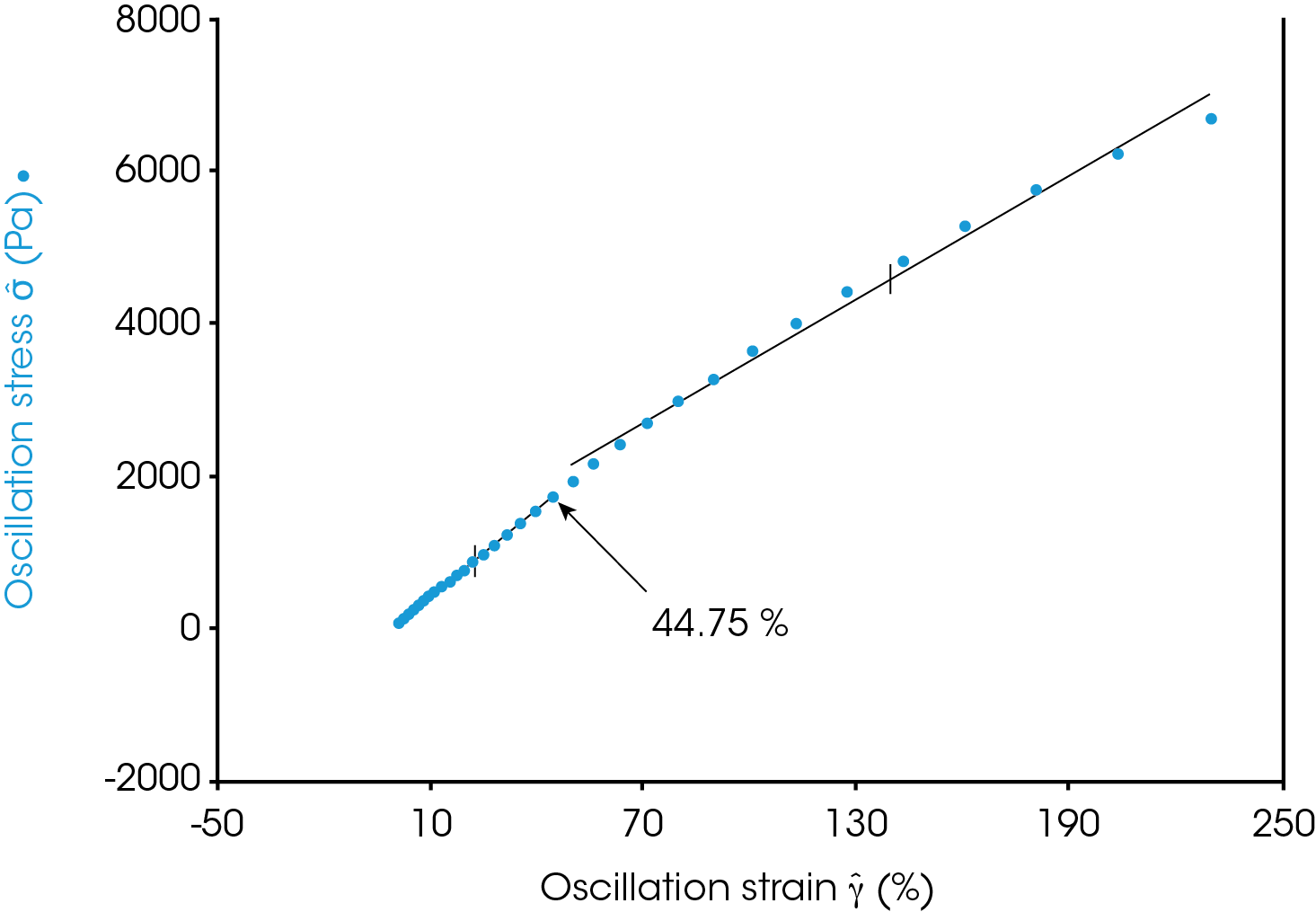
Figure 1: Stress vs strain in an oscillation strain sweep experiment on polystyrene at 250 °C and 1 Hz. The critical strain is marked on the plot.
Say you’re developing a delicious new yogurt (itself, a viscoelastic material). But you know that the trucks headed to deliver that yogurt will traverse bumpy roads. You’ll need to test how that yogurt reacts under all of that shaking (gravitational forces). If the network structure of the yogurt is too weak, in the sense that the end of the LVR corresponds to low strains or stresses relative to those experienced in the truck, then the yogurt network structure will be disrupted. Rather than having a continuous creamy texture, the yogurt can be broken up into separate chunks, sometimes with separated liquid, and in essence more akin to the texture of cottage cheese than yogurt.
Understanding the characteristics within the yogurt’s LVR helps not only formulate a yogurt that is mechanically robust enough for transport, but also still has a texture/viscoelasticity that is favorable to eat. Eating creates its own characteristic stresses and deformations in the mouth, which need to be accounted for (Who would want to eat chewy yogurt?).
Why is the Linear Viscoelastic Region Crucial in Materials Testing?
Think of the LVR as a set of guardrails. When you use too much stress, you’ll cross the critical strain threshold and irrevocably change its structure. Add too little stress, though, and you end up with noisy data. Staying within the LVR during dynamic (oscillatory) mechanical testing allows for the ideal probing of the sample in a quasi-equilibrium state; where its mechanical structure can be probed at a variety of conditions such as at various temperatures (mimicking real-world conditions), without disrupting destroying the sample structure mechanically and with excellent data resolution/reproducibility.
The LVR is also essential in understanding the complete rheological characteristics of a material (how it flows through the environment around it). Practically, this helps manufacturers and product researchers choose, replace, or refine the materials they need before full-scale production begins.
How to Determine a Material’s Linear Viscoelastic Region
Three variables will change the LVR of any material: Temperature, humidity, and the rate of deformation (frequency). A piece of rubber pulled in sub-freezing weather 1,000 times will react differently than one pulled twice on a humid August afternoon.
Because our environment (and how we use materials) constantly changes, there are two accurate methods to determine LVR.
- Experimental: Specialized lab equipment like a dynamic mechanical analyzer (DMA) which is primarily for solids or a rheometer which primarily deals with liquids, provide precise data to determine the LVR. These instruments can change temperature, humidity, and stress levels—efficiently repeating a cycle thousands of times.
- Analytical: Because the LVR is, by its nature, linear, you can accurately model it using math (software like TA Instrument’s TRIOS, makes this process easier). Leverage this information back in the lab, and you often don’t need to discern the exact critical strain of a material. Once you know the LVR, you can stick within that threshold. Conversely, the analytical approach models the minuscule stress and strain data at the range’s bottom end, meaning you don’t need to waste lab time gathering that data.
LVR in the Real World: Top Industries & Applications
When you’re on the 60th floor of a skyscraper or swallowing a Vitamin D supplement, you rely on the predictable viscoelasticity of materials all around (and inside!) you. That’s why you will find LVR testing is crucial in a vast array of industries, including:
Polymer and Plastics: Both materials are in products we use every day (probably even every hour). Knowing when and how they fail–and, for sustainability purposes, how they will react when they’re recycled–requires determining their LVR in a lab setting. With knowledge of the LVR, temperature ramps can be performed on polymers, effectively characterizing glass transitions (softening points), mechanically properties through thermal transitions (melting, crystallization), and properties such as crosslink density (essential for cured materials and rubbers – UV curable materials, epoxy, etc.)
Pharmaceuticals and Food: Your body itself is a viscoelastic structure, and so are the methods and materials used to keep it at its healthiest. From the capsule of a pill to plant oil emulsions that could replace saturated fat–understanding a material’s properties makes for an overall better quality of life. The LVR can give knowledge of the yield stress of a therapeutic cream and therefore its shelf life, or similarly the yield stress of a yogurt.
Construction: Cement is a fantastic example of a viscoelastic material that changes states due to time and temperature. The building you are in – right now – has not collapsed because researchers know how durable and stable its materials are over time and under stress. The LVR can be an effective characterization tool for paints which help maximize building material lifetime (critical for combating mold, UV, humidity, corrosion), with the LVR again characterizing shelf stability through the yield stress. The LVR can also help characterize the durability of composite materials commonly used in flooring, ceilings, and benchtops.
Conclusion: Materials Innovation Starts in the Lab
The world simply works better because we understand (and can innovate) viscoelastic materials: From the soap that morphs into foam when pumped from a bottle to the way a vaccine exits a syringe. These advances, however trivial or monumental, only happen because of research in the lab. Just like you can’t sprint before learning to crawl, you can’t make your product safer, healthier, lighter, cheaper, or more durable without understanding its linear viscoelastic region. If viscoelastic materials are building blocks to a better world, then the LVR is a building block to creating better versions of those materials. Contact TA Instruments for expert guidance in testing and optimizing your materials.
Other Resources
- Application Note – Determining the Linear Viscoelastic Region in Oscillatory Measurements
- Application Note – Temperature and Frequency Trends of the Linear Viscoelastic Region
- Application Note – Determining the Linear Viscoelastic Region in Creep and Stress Relaxation Tests
- Tech Tip – Discussing the Linear Viscoelastic Region and Selecting a Strain Value
- Webinar – Jan Vermant – Orthogonal Superposition Rheology
- Webinar – Connecting Polymer Processing and Product Performance through Rheology & DMA on the New DHR
- Contact – Contact TA Instruments Today