複合材料的材料分析
尖端實驗室如何利用材料分析增強複合材料?
Morgan Ulrich | Ogochukwu Onepe
September 18, 2023
我們對複合材料寄予厚望:火箭材料需要忍受起飛時的高溫,風力渦輪機必須承受強風,而運動鞋則需要在長跑時耐用又有強支撐力。專家們如何開發適用這些具體需求的複合材料,並驗證它們的性能呢?
複合材料由兩種或多種材料組成,然而,這些材料在成品結構的宏觀或微觀尺度上相互結合,但仍保持其獨立性。與任何單一材料相比,所形成的複合材料具有不同的性質。因此,材料科學家應先透過充分的測試,驗證材料特性,才能就特定應用改良複合材料的配方。
複合材料開發人員運用先進的分析技術滿足現今對輕量可靠產品的高度需求。他們首先進行材料和產品原型的特徵分析,以滿足客戶的關鍵性能要求,包括強度、耐熱、附著和耐用。
世界各地實驗室的複合材料科學家如何運用材料分析增強其產品?下列為最好的材料科學技術,以及如何利用這些技術檢測各種應用與產業中的複合材料之實際研究範例:
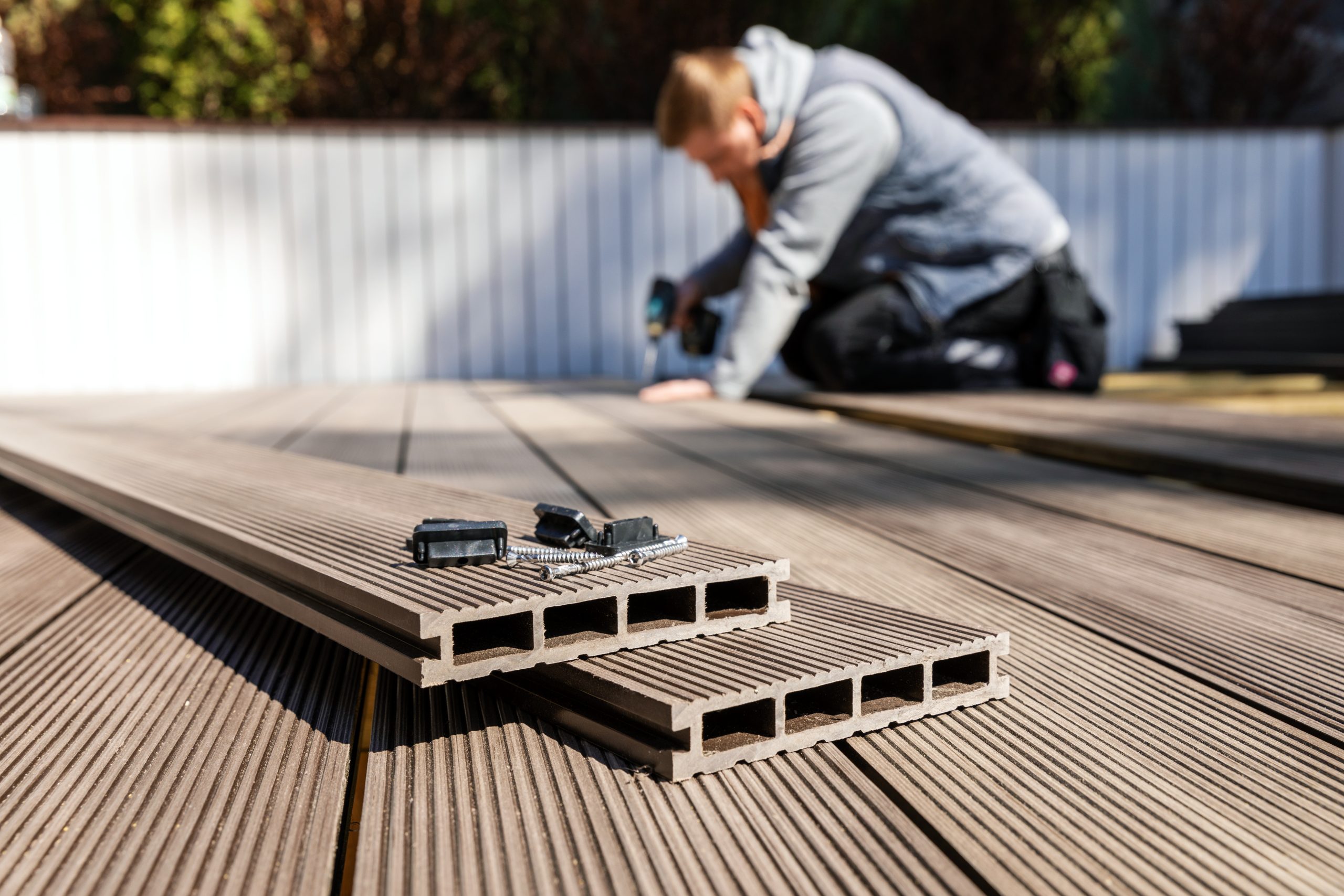
差示掃描量熱儀
差示掃描量熱儀(DSC)測量與材料中熱轉變相關的溫度和熱流。DSC 確定複合材料的玻璃轉變溫度(Tg)、凝膠時間與固化時間等關鍵指標。
Mohamed Rady 教授在波爾多大學使用 DSC 支持其粒狀複合材料相變的研究。1 他專門研究熔化及凝固過程,並設計了一個簡單程序以利用其 DSC 獲得準確的結果。
Paul Sabatier University CIRIMAT 實驗室的研究人員 Rivière、Caussé、Lonjon、Dantras 與 Lacabanne 運用調幅式 DSC,研究將銀奈米顆粒添加至聚醚醚酮(Polyetheretherketone)基質中所產生的效應。2 準確的熱傳導性和比熱測量使他們能夠理解材料中熱傳輸的機制。他們可以使用這些數據改良材料的混合物以產生特定用途的複合材料。
TA Instruments 的 Discovery DSC 系列改善基線平坦程度、轉態解析度與靈敏度,並配備專利 Tzero™ DSC 技術以獲得更準確的熱流數值。TA DSC 上的 Modulated® DSC(MDSC®)實驗更快且更準確。Multi-Sample X3 DSC 可以同時測量至多三個樣品的熱流,以達到更高生產效率。
流變學
流變學研究材料的流動及變形。變形及流動分別被稱為應變和應變速率,它們表示在外力或應力影響下,物體移動的距離。
例如,Ebonyi State University 的 Ogah 教授就使用了流變儀,測量填充劑和添加劑對木材塑膠複合材料加工所產生的影響。3 Ogah 利用熱塑性聚合物作為基質材料,加工天然纖維從而生成天然纖維複合材料。接著,他使用 TA Instruments Discovery 混合流變儀分析了不同的纖維類型、含量、粒徑和形狀對最終複合材料流變性質的影響。
流變儀具有獨特的測量黏度和黏彈性的能力。TA Instruments 的 Discovery 混合流變儀還可以協助用戶輕鬆確定無法以黏度計或毛細管流變儀查出的微觀結構差異。當探究複合材料在微觀尺度上如何互相影響時,這些量測特別有用。
機械分析
機械測試有助於研究人員分析一種材料的機械特性,又或測定一個結構對特定外力的反應。複合材料開發人員量化其材料的失效、疲勞、剪切或潛變,並運用這些資訊設計更適合特定用途的產品。
阿爾伯塔大學的 Garces 與 Ayranci 開發了一種新方法,藉由擠壓式積層製造的電阻加熱技術來製造及活化形狀記憶聚合物複合材料(SMPC)。4 他們使用 TA Instruments ElectroForce 經熱調整的拉伸測試儀來評估特定加工條件下 SMPC 的變形效應。他們的研究讓其他人能夠成功利用其技術製造廣泛用途的 SMPC,如「生物醫學支架、運動器材和無人機(UAV)」等。
無論是開發堅固的建築材料,還是具有生物相容性的骨骼替代品,全球的尖端實驗室都依靠 ElectroForce 機械測試儀器來驗證複合材料的機械性質。ElectroForce 負載框架涵蓋廣泛的作用力,而多樣品疲勞測試儀器可以同時測試多達 16 個樣品,並加速疲勞研究。
如何檢測我的複合材料?
這些研究範例只列舉了其中一部分應用,實際上仍有無數的儀器和技術可用來分析複合材料的每個材料特性。瀏覽我們複合材料頁面上目前的尖端技術,看看哪些儀器符合您在複合材料設計和加工方面的需求。
仍然不確定哪個為最適合貴實驗室的技術?請聯繫 TA Instruments,我們的複合材料專家將樂意為您指點迷津。
參考資料:
- Rady, M. (2009). Study of phase changing characteristics of granular composites using differential scanning calorimetry. Energy Conversion and Management, 50(5), 1210–1217. https://doi.org/10.1016/j.enconman.2009.01.030
- Rivière, L., Caussé, N., Lonjon, A., Dantras, E., & Lacabanne, C. (2016). Specific heat capacity and thermal conductivity of PEEK/Ag nanoparticles composites determined by Modulated-Temperature Differential Scanning Calorimetry. Polymer Degradation and Stability, 127, 98–104. https://doi.org/10.1016/j.polymdegradstab.2015.11.015
- Ogah, O. A. (2017). Rheological properties of natural fiber polymer composites. MOJ Polymer Science, 1(4). https://doi.org/10.15406/mojps.2017.01.00022
- Garces, I., & Ayranci, C. (2018). A view into additive manufactured electro-active reinforced smart composite structures. Manufacturing Letters, 16, 1–5. https://doi.org/10.1016/j.mfglet.2018.02.008
其他資源
- 應用說明 – Stress/Strain Evaluation of Fibers Using TMA
- 應用說明 – Characterization of the Degree of Cure of Thermosetting Resins by DSC
- 應用說明 – Using an ARES Rheometer to investigate the β-relaxation change of graphene poly(ethyl methacrylate) nanocomposite
- 應用說明 – 玻璃纖維織造複合材料在高溫下的彎曲疲勞行為
- 網路研討會 – Thermal, Rheological and Mechanical Characterizations of Thermosets