Material Analysis Techniques for Every Stage of Polymer Development
Implement the right solutions to prevent common pitfalls
Morgan Ulrich | Andy Simon
January 7, 2025
Polymers are everywhere, from components making up the electronic device you’re reading this on to life-saving medical devices, energy efficient solar panels, and lightweight aero or auto components. Material scientists and engineers continue to improve high-performance polymers for strength, durability, and stability under demanding applications.
Developing these polymers for specific applications requires rigorous testing and data-informed decision making at every step. The advanced material development workflow can be broken down into five steps, outlined below, as developers move from material selection and development to final product analysis.
During polymer development, researchers transition from conducting many quick tests on numerous material candidates to narrowing down a few viable candidates and running fewer, more in-depth tests to verify their suitability. Conducting the right test at the right part of development can save time and prevent costly project regression and material and product failures. Learn which polymer analysis techniques support each stage of development below.
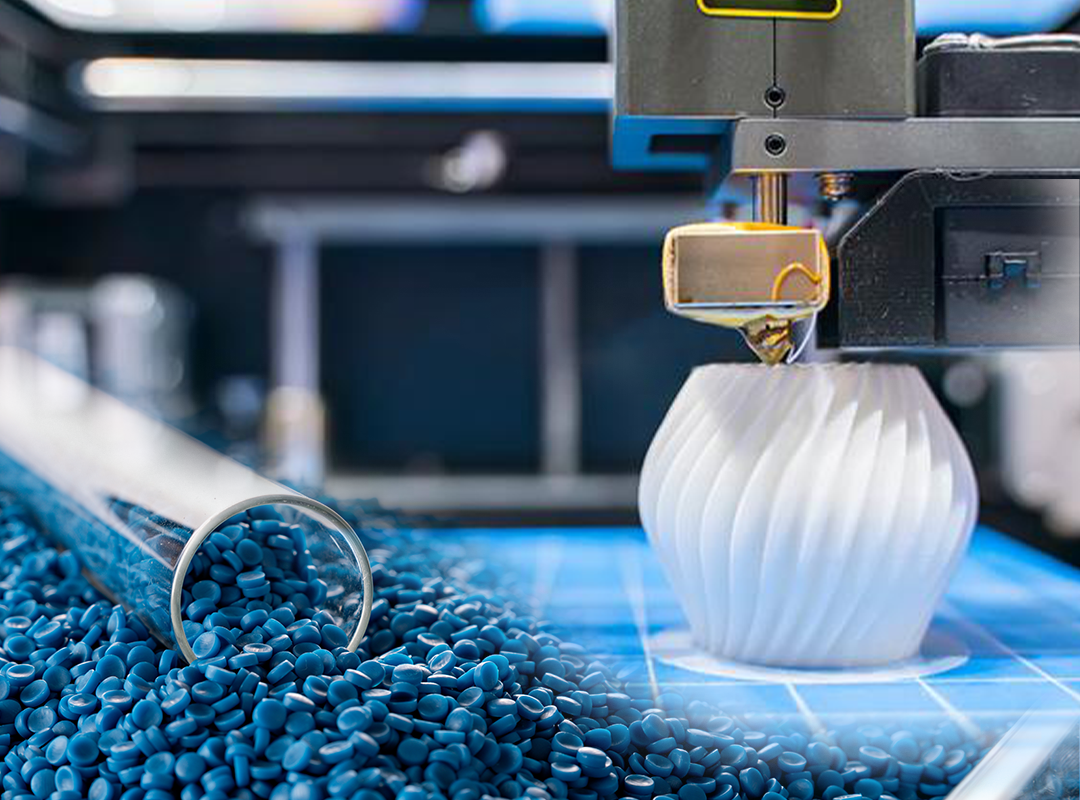
Which technique supports your stage of polymer development?
1. Early Materials Development
During materials development, polymer engineers identify suitable raw materials based on application requirements. These initial investigations require quick, reliable tests to rapidly assess specific material properties like the glass transition temperature (Tg) and decomposition temperature to inform judgements on material stability and resin processability.
Early development benefits from thermal analysis techniques for efficient, reliable material characterization. Differential Scanning Calorimetry (DSC) measures polymers’ phase transitions and melting temperature, helping manufacturers determine if a resin is fit for end-use or how additives are affecting a resin’s properties. Thermogravimetric Analysis (TGA) measures polymers’ thermal stability by identifying their decomposition temperature, plus measures volatile, solvent, and filler content. TGA-EGA combines Thermogravimetric Analysis with Evolved Gas Analysis to determine polymer decomposition products and elucidate the original composition of an unknown resin. Thermomechanical Analysis (TMA) measures dimensional change in materials with temperature, revealing a polymer’s thermal history and suitability for specific environments.
Thermal analysis in early development is facilitated by automated analysis from TRIOS Guided Methods Software on TA Instruments’ Discovery DSC and TGA. Guided Methods significantly reduce training time with preconfigured test templates for common polymer experiments, empowering new users with guided test execution and automated intelligent analysis.
Accurately characterizing raw materials is an essential part of early material development. Sending the wrong materials forward as candidates can lead to costly production problems and time-consuming re-work. Starting with the right materials, thanks to reliable testing methods, saves time and streamlines polymer development.
2. Evaluating Material Candidates
Once polymer manufacturers identify their material candidates, they run pre-processing assessments of materials’ basic stability and suitability for manufacturing. Rheometers measure polymers’ viscosity and viscoelastic behaviors, providing data about processability and melt properties. Viscosity reveals how materials will flow and deform under varying temperatures, ideal for selecting the best candidate for specific processing conditions and ensuring stability during manufacturing. Auto-Trim for the Discovery Hybrid Rheometer uniquely automates polymer melt testing, getting polymer manufacturers this data faster and with enhanced reliability. Characterizing polymers at this step is essential to ensure a candidate material meets the processing requirements early enough to prevent selecting a material which is difficult or impossible to process. Finding processing problems or needing to add processing agents late in the material development process can be expensive and potentially invalidate previous test results and specifications.
3. Material Selection
Polymer manufacturers, compounders, and converters all engage with this step, which involves a more in-depth assessment of processing conditions and methods as well as material refinement for processing and final use. Rheometers continue providing valuable information about polymers’ viscoelastic behavior, informing filler choices and helping troubleshoot processing problems that affect product quality. DSC helps predict product properties based on the resins and additives used. TGA measures resins’ thermal stability and detects contamination or filler content.
Dynamic Mechanical Analysis (DMA) measures the mechanical properties of materials as a function of time and temperature – key for evaluating how temperature affects performance. DMA also reveals blend compatibility, helping compounders and converters choose the ideal blend. Tensile testing reveals materials’ mechanical integrity under a single load, offering a proactive first look at their durability before being incorporated into a prototype. Mechanical testing is particularly valuable at this stage since material suppliers’ specification sheets are often incomplete. Fatigue testing complements tensile testing by measuring the materials’ response to repeated loading, valuable information before parts are designed into prototypes.
Utilizing a suite of these thermal and mechanical test methods empowers polymer developers to design efficient processing methods while simultaneously choosing the best materials and methods for successful application performance – cutting out guesswork and streamlining development.
4. Material Refinement
As complete components are developed, converters and end-market manufacturers focus on mechanical tests designed to simulate application conditions. DMA and TGA reveal how environmental factors affect material performance, such as cold temperatures making polymer helmets brittle and susceptible to breaking.
Mechanical testing of polymers at this stage includes tensile testing, fatigue testing, and characterization of other mechanical properties. Tensile testing quantifies a material’s breaking point under a single load application, while fatigue testing quantifies the material’s response to repeated loading. Application specific mechanical tests such as creep, stress relaxation, and other properties are often measured at this point. Manufacturers use this information to predict product performance and reliability – effectively preventing product failures later downstream when these materials or components are incorporated into prototypes or final products.
5. Post-manufacturing
Finally, how does your complete polymer perform under application conditions? Ideally by this stage, converters and end-market manufacturers already have an idea of their incoming materials’ properties and ideal processing conditions. DSC helps guide any processing refinement or changes with insight into the polymer’s thermal stability and phase transitions. TGA can measure the polymer’s decomposition temperature and the root cause of material issues under processing or performance conditions.
Mechanical testing of manufactured polymers is critical for ensuring safety and performance. Tensile and fatigue testing measure the material’s strength and durability under specific temperatures or applied forces. Tensile testing gives a broader picture of how and when materials break under a single load, but fatigue testing completes mechanical studies with a more comprehensive view of material failure. For example, fatigue testing can reveal otherwise undetectable manufacturing effects that lead to product failure undetectable by tensile testing alone.
Why incorporate material analysis into your polymer development workflow?
Adding all of these tests throughout polymer development may sound like extra work, but making informed decisions at every stage minimizes costly mistakes and rework of failed designs. Just as prototypes and pilot product runs in development ensure performance before committing resources to a full production and launch, ensuring a material performs before committing the resources of manufacturing tooling and product testing is a necessary safeguard against failure. Running material analysis tests earlier in the process can save polymer developers from countless lost hours and wasted materials. Proactive material analysis informs successful, streamlined polymer development for efficient manufacturing and successful products.
Other Resources
- eBook – How to Ensure Polymer Strength and Durability with Mechanical Testing
- Blog – What Your Material Specification Sheet Doesn’t Tell You
- Blog – 3 Essential Types of Mechanical Testing for Polymer Development
- Application Note – Tensile and Fatigue Properties of Additively Manufactured Polyamides
- Application Note – Flexural Fatigue Behavior of Woven Fiberglass Composites at Elevated Temperature
- Application Note – Evaluation of the Loss of Polymer Strength and Durability Due to Fatigue Loading and Manufacturing Artifacts
- Application Note – Identification of a Cross-Linked Rubber by Evolved Gas Analysis and Thermal Analysis Techniques