Keywords: rheology, collagen, hydrogels, viscoelastic measurements, strain sweep, linear viscoelastic region, DHR-20
RH120
Abstract
Naturally-based hydrogels, especially those prepared from polysaccharides or proteins, have many unique properties like biocompatibility, viscoelasticity, and biodegradability. Therefore they are used as materials in many pharmaceutical and bioengineering applications. Collagen hydrogels are specifically utilized as interesting materials for the manufacture of scaffolds in tissue engineering. Unfortunately, collagen as a natural material often differs in its viscoelastic properties depending on the initial source of this material. This represents a gap in knowledge and a complication with respect to the broader application of this material on an industrial scale.
Here, a standard operating procedure (SOP) for determining the quality of collagen hydrogel was developed using oscillatory rheology with a DHR-2 rheometer.
Introduction
Hydrogels are three-dimensional polymer network structures which are able to absorb (or retain) large amounts of water or other biological fluids. Surprisingly, hydrogels have unique viscoelastic properties despite the large amount of dispersion medium (water). At low applied stress they behave like viscoelastic materials, which means they are able to resist applied stress without any macroscopic changes. If the applied stress increases above a critical value, the internal 3D structure of the hydrogels collapses and viscous behavior starts to prevail.
Viscoelastic properties (mainly studied by oscillatory measurements using rheometers) are some of the most crucial and fundamental properties with respect to the broader application of hydrogels on an industrial scale. The initial hydrogels (if the conditions of preparation are consistent) must have the same or at least similar properties each time they are used for the same purpose. However, to obtain materials with reproducible viscoelastic properties from natural resources is sometimes very problematic, which makes it difficult to use them for applications such as tissue engineering (scaffolds). If the prepared hydrogel’s viscoelastic properties differ from the intended, it makes the material unsatisfactory for its specific role. This is a serious issue which may lead to considerable financial losses as well as a decline in customer confidence.
We developed a simple standard operating procedure (SOP) based on a strain amplitude sweep for the quality control of collagen hydrogels often used as scaffolds. This SOP uses standard oscillatory measurements (amplitude sweep with constant oscillation frequency).
Experimental
The collagen hydrogels were prepared via the dissolution of lyophilized collagen powder in deionized water. Two collagen samples were studied, one with satisfactory viscoelastic properties for the preparation of scaffolds (marked: OK) and the other with unsatisfactory properties (marked: NOK). Due to confidentiality reasons, more detailed information about these collagen samples as well as the preparation procedure cannot be published. The concentration of collagen in water was maintained at a value of 10.6 wt. %.
Immediately after preparation, collagen hydrogels were kept under constant temperature (6 °C) for 24 hours. Before measurement, the samples were tempered at 25 °C for at least 1 hour outside the measurement setup and then another 3 min inside.
The viscoelastic properties of the collagen hydrogels were determined via strain sweep measurements within the amplitude strain range of 0.01-1000 % (6 points per decade) at a constant frequency of 6.28 rad/s using a parallel plate geometry (20 mm diameter) with a crosshatched surface. The temperature was kept constant (25 °C) throughout the whole experimental procedure. The gap was maintained at 1 mm over the whole experiment. During the “go to geometry gap” procedure, the normal force did not exceed 1 N. Experiments were performed in triplicates. A solvent trap was used to prevent the evaporation of dispersion medium.
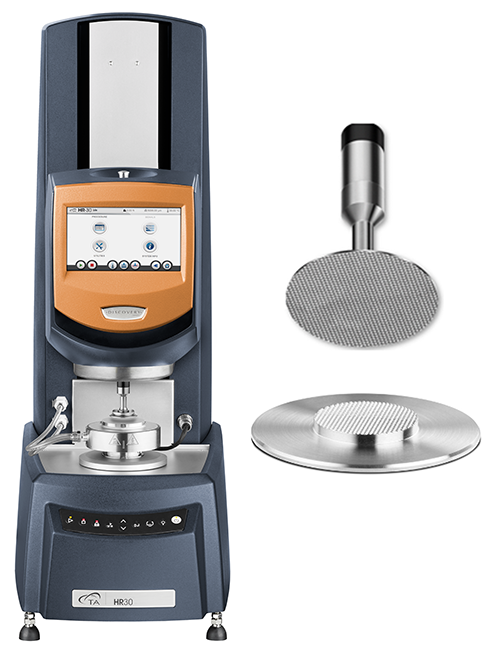
Results and Discussions
The results of strain sweep measurements for the collagen samples follow a course often seen for hydrogel samples (see Fig. 2). At small strains the elastic modulus predominated over the viscous modulus. This means that the inner structure of the hydrogel is fully developed. Probably, hydrogen bonding is the main interaction that makes collagen hydrogels so elastic. The three-dimensional network structure of the hydrogel is able to resist the small strain amplitude; therefore, the viscoelastic moduli are independent of strain. In this region, the inner structure of the hydrogel is reversibly deformed: if the applied strain is removed, the hydrogel remains the same as at the beginning. When the applied strain is increased, significant changes begin to occur in the inner structure of the hydrogel. The viscous modulus begins slightly to increase due to microcracks in the hydrogel’s structure, followed by a significant decrease of both viscoelastic moduli. When the elastic modulus begins to decrease, the deformation of the structure is non-reversible and the hydrogel exceeds its linear viscoelastic region (LVR). The non-specific interactions (hydrogen bonding) stabilizing the inner structure of the hydrogel begin to break due to the applied strain and the inner structure begins to collapse. If large values of strain are applied, the viscous modulus begins to predominate over the elastic modulus and the sample begins to flow.
The point at which the linear viscoelastic region (LVR) ends is the most crucial information with respect to determining the mechanical stability of hydrogels. A longer LVR means that the “nodes” in hydrogels (typically covalent or weak interactions) have a higher resistance to applied deformation. The strength of bonds increases with higher LVR.
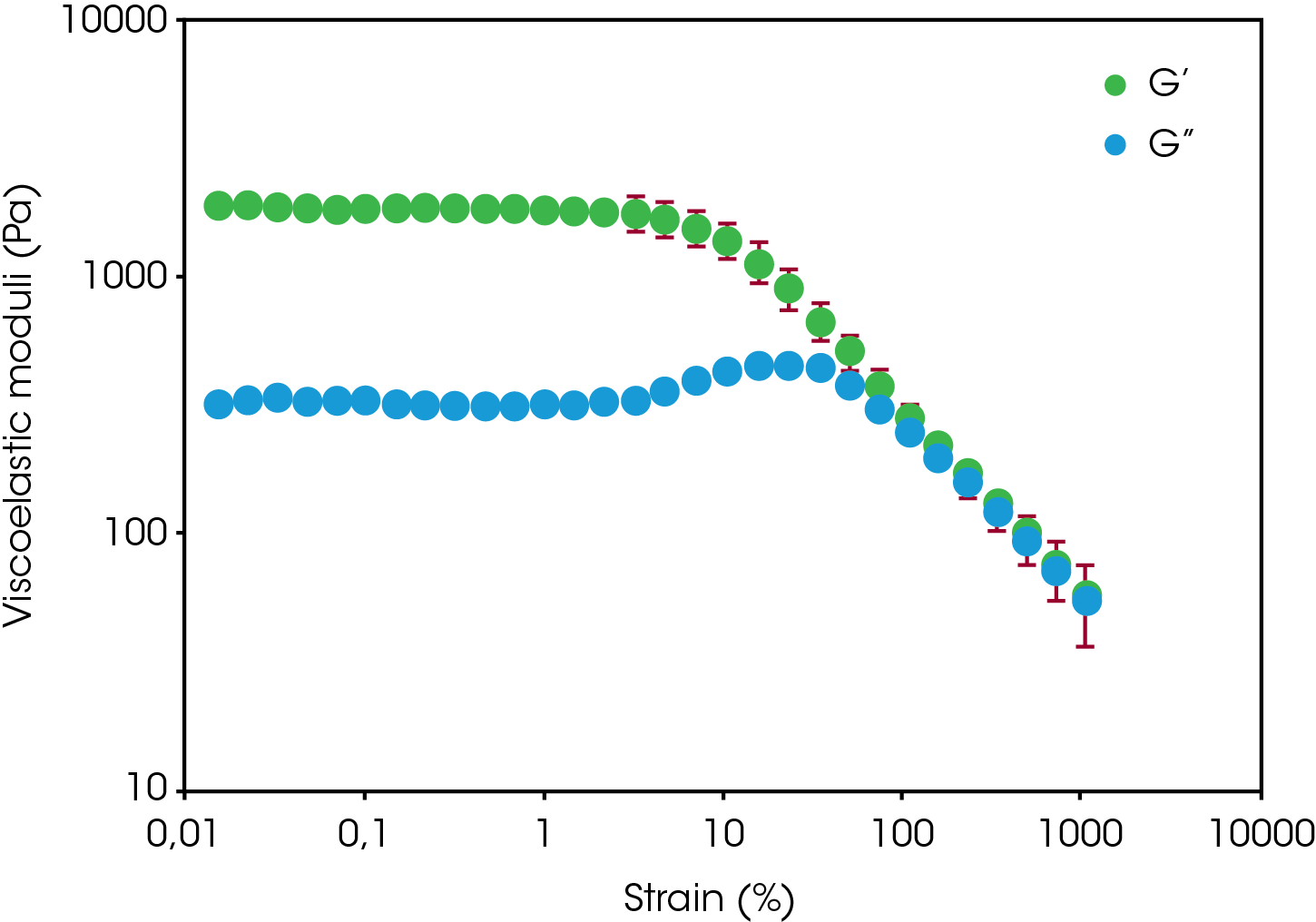
Quality control of collagen hydrogels
Two different batches of collagen hydrogels were tested. Samples marked “OK” had suitable viscoelastic properties for the preparation of scaffolds, while samples marked “NOK” did not. These two batches (verified by our company partner) were used as reference samples for all other new batches.
Figure 3 shows the loss angle as a function of applied strain. It is obvious that all tested collagen hydrogels exhibited comparable viscoelastic properties under small deformation, i.e. the values of loss angle were practically the same for all batches. However, the sample with unsatisfactory viscoelastic properties (marked as NOK, as defined by our business partner) had a significantly shorter linear viscoelastic region, which was indicated by a sharp increase in loss angle when the strain value was increased. In contrast, the batch of collagen hydrogel marked as OK (with satisfactory mechanical properties for the purposes of our business partner) exhibited a longer linear viscoelastic region, which indicates better viscoelastic properties (i.e. a higher strength of nodes in the inner structure of hydrogels). These two batches (OK and NOK) were used as reference samples for the evaluation of the viscoelastic properties of all new batches from our business partner. The most recent batch (marked blue on the graph) was classified as unsuitable. Therefore, this batch was withdrawn from production.
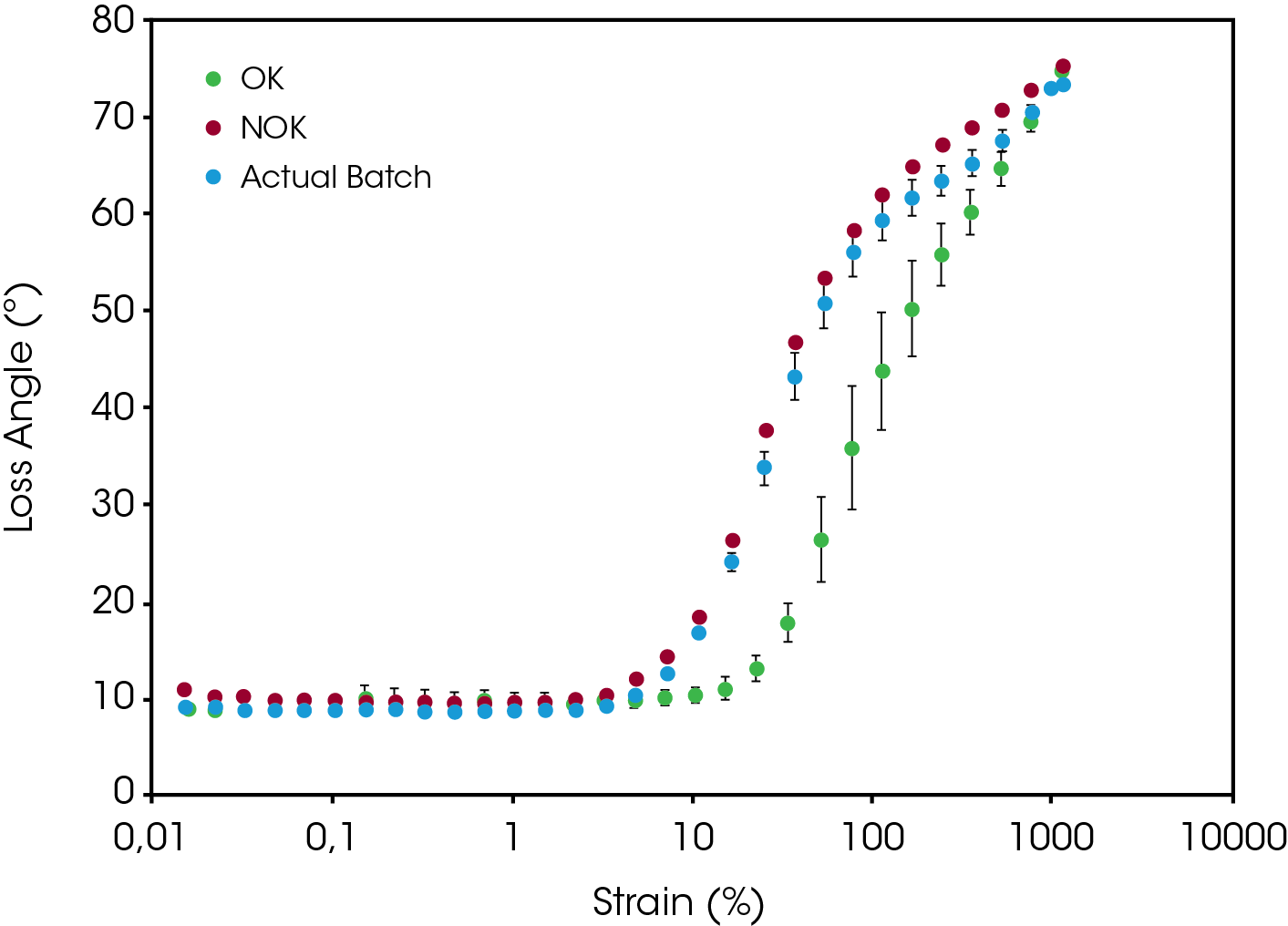
Conclusions
A standard operating procedure for the quality control of collagen hydrogels often used as scaffolds was developed and successfully implemented in the technological and quality control processes of our business partner. The viscoelastic properties of every new batch of collagen hydrogels produced by the company are monitored via this standard operating procedure using a DHR-2 rheometer.
Thanks to this method, we are able to check the quality of collagen hydrogels in a relatively simple and time-efficient way. It not only saves time, but also, and primarily, reduces costs sustained by our business partner when unsatisfactory products are returned by customers.
Acknowledgement
This paper was written by J. Smilek, M. Kadlec, P. Sedlacek and M. Pekař from Institute of Physical and Applied Chemistry at Brno University of Technology, Faculty of Chemisty, in Brno, Czech Republic. Contact: smilek@fch.vut.cz
Click here to download the printable version of this application note.