Rheology of Paints and Coatings
Alina Latshaw | Morgan Ulrich
August 18, 2022
From shiny cars to streak-free walls, we demand a lot from our coatings and paints. A high-quality paint not only needs dazzling color, but also must offer the right material properties for a smooth application and drying process. Consistency is crucial: too thin and the paint will run and drip; too thick and it will clump and not dry evenly. Spray paints and coatings also need to be applied smoothly without clogging the spray device.
Most paints and coatings are colloidal suspensions, meaning they have solid particles suspended in a Newtonian fluid. Different combinations of solid particles and fluid can result in varying thicknesses and appearances.
Achieving the right material properties of paints and coatings requires considering their rheology – how the material flows or deforms. The rheology of a paint or coating is dependent upon the solvent environment, the presence of thickeners or additives, and the properties of the paint pigment or particle itself.
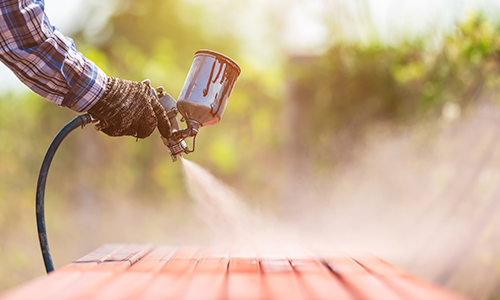
Key Rheology Tests of Paints and Coatings
For paints, the key rheology tests simulate the environmental conditions and stresses the material will experience during standard use. These parameters include viscosity, yield stress, and creep.
Viscosity measures a material’s resistance to flow as a result of its internal friction. Researchers have noted the correlations between viscosity and paint performance.1 Therefore, measuring the viscosity of a paint or coating over a wide range of shear rates is key for predicting its performance under different use conditions: mixing, stirring, brushing, rolling, or spraying.
Yield stress is the minimum stress that must be applied to a material before it begins to flow. Yield stress is critical in preventing settling of pigment over time or under storage conditions. Coatings formulators optimize a formulation’s yield stress to ensure the paint will not drip or sag after being applied to the wall.
Creep describes the deformation or flow of a material under constant stress. Creep measurements can describe how a paint or coating will behave under the force of gravity after being brushed or rolled onto a surface.
Dynamic Rheology Testing
While viscometers can measure the viscous properties mentioned above, specialists evaluating paints and coatings choose rheometers since these instruments offer both viscosity measurements and dynamic oscillatory testing.
Dynamic oscillatory testing can uniquely characterize viscoelastic materials, which exhibit both viscous and elastic responses. All paints and coatings are viscoelastic, and dynamic oscillatory testing is the most sensitive measure of viscoelastic structure.2 Viscometers alone cannot measure viscoelasticity, making rheometers the instrument of choice for the paints and coatings industry.
Coatings scientists rely on TA Instruments rheometers to investigate coatings’ stability before, during and after application. Dynamic oscillatory testing helps them optimize stability to prevent sedimentation or separation of the pigments. This method ensures that the surrounding fluid has sufficient structure to properly suspend the particles while preventing separation.
Sag and slump resistance is also dependent on a material’s ability to maintain its structure after brushing or high shear application, which is especially important when painting on vertical surfaces. Formulators measure structure recovery over time with dyanamic oscillatory measurements as well as measuring yield stress, all on one rheometer.
Leading Rheometers for Paints and Coatings
There are a number of properties of paint or coating rheology that are particularly important to consider when optimizing new product fomulations. Coatings are exposed to a surprising variety of shear rates and other forces, including very slow processes such as sedimentation or high-speed processing in spraying application. Effective testing must cover the full range of shear rates as well as characterizing viscoelastic properties of paints and coatings.
As mentioned above, leading coating laboratories and formulators rely on TA Instruments Rheometers for unparalleled performance coupled with user-friendly design, making them easy to integrate into existing workflows. We offer a number of geometry options designed for testing paints and coatings, including the concentric cylinders, parallel plate, and cone-and-plate geometries. The option to use disposable concentric cylinder cups enables higher throughput by eliminating the need to stop and clean between tests. The immobilization cell accessory is essential for studying coatings’ drying characteristics.
The latest innovation in rotational shear rheometers, the Discovery Hybrid Rheometer, covers the full range of paint and coating rheology needs, from the most cost-effective to the most advanced solution available. The Discovery HR 10, 20, and 30 all offer the full breadth of rheology data needed for characterizing coatings, including viscosity and viscoelasticity. TA Instruments rheometers are capable of both static and dynamic testing of stress, strain, time, frequency and temperature.
In addition, the Discovery Hybrid Rheometers can accelerate candidate screening and predict coatings’ behavior. The underlying structure of paints and coatings is crucial for achieving their desired performance under processing, customer use, and storage conditions.
All TA Instruments rheometers come with state-of-the-art TRIOS software, which simplifies paint and coatings rheology with easy-to-use test forms as well as automatically calculating and displaying viscosity, modulus, and other relevant variables.
With a wealth of experience in rheology instrument design and measurement, TA Instruments’ team of experts is ready to help you find the right rheometer and geometry for your lab. Contact us today to find out how rheology can help you optimize your paints and coatings.
To learn more about the rheology of coatings and see real experimental data, watch our Rheology of Coatings and Inks webinar or read our Paints and Coatings Application Note.
References:
- Eley, R. R. (2019). Applied rheology and architectural coating performance. Journal of Coatings Technology and Research, 16(2), 263–305. https://doi.org/10.1007/s11998-019-00187-5
- Whittingstall, P. (2003). Dynamic or Oscillatory Testing of Complex Fluids. Current Protocols. https://doi.org/10.1002/0471142913.fah0301s07
Other Resources
- Applications Note – Texture of Yogurt
- Applications Note – Adhesive’s Curing
- Webinar – Strategies for Rheological Evaluation of Adhesives
- Webinar – Applications of Tribo Rheometry in Material Characterization
- Webinar – Rheology Workflow Automation with TRIOS AutoPilot: Enhanced Measurement with Reduced User Training
- Webinar – Use of Thermal Analysis and Rheometry to Study Waxation in Crude Oil
- Webinar – Thermal, Rheological and Mechanical Characterizations of Thermosets
- Instrument – Discovery Hybrid Rheometer
- Instrument – ARES-G2
- Contact – Contact TA Instruments Today