Keywords: polymeric heart valves, reinforced polymers, composites, fatigue testing, material strength
EF004
Background
Heart valve prostheses have been used successfully in heart procedures since 1960, resulting in an overall improvement in patients’ quality of life. Valve technologies are evolving rapidly as are the materials they are made of. Polymer leaflet valves can offer advantages in hemodynamics and the potential for better durability over bioprosthetic valves. As with almost all implantable medical devices, the material and product designs that deliver these potential benefits require rigorous characterization and validation to ensure patient safety.
Polymer leaflet heart valves can fail in long-term use due to tearing and calcification caused by high dynamic tensile and bending stresses on the material and oxidative reactions with blood. It was postulated that synthetic valve leaflets that mimic the natural valve leaflet structure fabricated from fiber-reinforced composite material will minimize leaflet stresses and decrease tears and perforations.
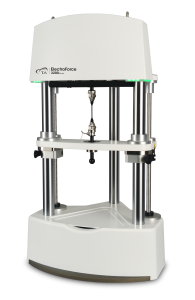

Meeting the Challenge
The aim of this research, performed under the supervision of Dr. Richard Schoephoerster in the Cardiovascular Engineering Center at Florida International University, was to manufacture and test an innovative composite material designed for use in a PT (polymer trileaflet) heart valve prosthesis.
A novel polyolefin with better oxidative stability was compared to an existing implant-approved polymer (IAP). The new polyolefin was tested in an isotropic form and as a composite reinforced with polypropylene (PP) fibers. Static and dynamic properties of the polymers were measured with the goal of determining whether the polyolefin is capable of matching the tensile modulus of the IAP while demonstrating improved durability and oxidative stability.
The mechanical testing was performed on the ElectroForce® 3200 test instrument, specifically Model 3220 with a 225N force capacity and a test frequency range from static loading to 300Hz. This wide range in testing frequency makes the ElectroForce 3200 an excellent choice for studies such as this that require both very slow tensile testing and highly accelerated fatigue testing.
Monotonic pull-to-failure and tension-tension fatigue tests on each material were performed according to ASTM standards (ASTM D638, ASTM D882, ASTM D3039 and ASTM D3479). The pull-to-failure test is displacement-rate controlled, meaning the specimen is stretched until failure. The fatigue test is force controlled; that is, the specimen is being cycled between two tensile force levels, typically 10% and 100% of the desired maximum force level. A 100 Hz sinusoidal cycling frequency was used to apply continuous cycles until the failure of each specimen. In this case, since there could be significant fatigue damage without complete material rupture, failure and the end of the test was defined as 100% strain of the material, which was deemed beyond the usefulness of this material in a functional heart valve.
Tensile to failure tests indicated that PP fiber reinforcement of the polyolefin was required to match the modulus of the IAP (see Figure 3). Based on these results, it appears that the best match of modulus will be to use a thread count between 3 and 12.
Preliminary fatigue results showed the fiber-reinforced composite material also has the potential for longer fatigue life when compared to an existing implant-approved polymer (see Figure 4). This illustrates that similar fatigue performance may be expected when using between 3 and 12 threads of polypropylene.
These encouraging results suggest that with more refinement in composite materials design, the PP reinforced polyolefin composite is a strong candidate for enhanced valve leaflet designs with improved oxidative stability, similar modulus and equivalent or better fatigue performance.


References
- Gallocher, S.L., Aguirre, A.F., Kasyanov, V., Pinchuk, L. and Schoephoerster, R.T. (2006), A novel polymer for potential use in a trileaflet heart valve. J. Biomed. Mater. Res., 79B: 325-334. https://doi.org/10.1002/jbm.b.30546
Acknowledgement
Click here to download the printable version of this application note.