The Importance of Fatigue Testing: Prevent Product Failures Early
Morgan Ulrich | Andy Simon
January 23, 2025
How Fatigue Testing Improves Material Selection and Product Design
From faster prototyping to ensuring long-term performance, fatigue testing is a critical step in product development across a variety of industries that rely on high-performance materials, like polymers, rubber compounds, and composites. When done properly, fatigue testing accelerates development by helping engineers make informed decisions about prototypes and designs. This blog examines the benefits of early testing and how fatigue testing with precision instruments can prevent catastrophes to your revenue, reputation, and users’ safety.
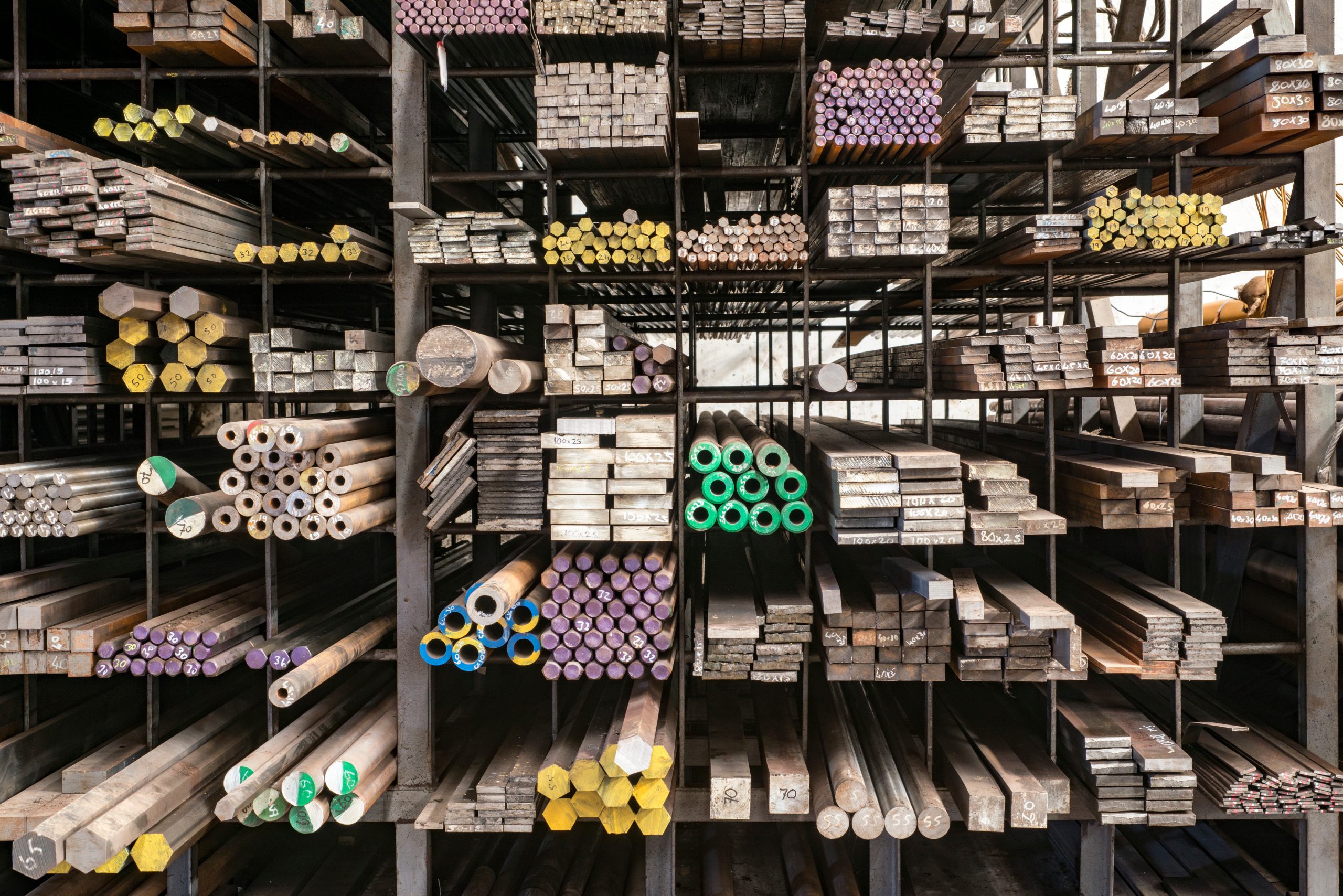
What Is Fatigue Testing?
Fatigue testing is the process of determining how a product responds to a repeated (cyclic) load. Fatigue testing’s goal isn’t simply to determine if a product might break, but to quickly and repeatably evaluate its behavior under application-specific conditions. Tools like Load Frame Instruments simulate real-world loading and environmental conditions in a faster and repeatable lab environment. The most common being:
- Temperature: Evaluate the effect of different temperatures on a materials’ durability
- Environmental Bath: Determines how fluid environments affect the material
- Stress Level: Evaluate the effect different load amounts on a materials’ life
A rubber gasket that must re-enter the earth’s atmosphere will undergo very different stress than a ski gliding across moguls. In both, fatigue testing can determine the proper material and the ideal structural design for successful and safe use in the real world.
With the ability to quickly exert real-world forces thousands to millions of times, fatigue testing is an important step in material selection and design that empowers you to discover durability issues more efficiently and earlier in the process.
Fatigue Testing in Materials Selection
Material suppliers provide general spec sheets of properties that universally apply to their customers, but they won’t know your specific use case. Will your polymer need to withstand humidity? Is your widget used in a climate-controlled environment or on a space craft?
Only you have complete knowledge of the intended lifespan and environment. That’s why early-stage testing of the materials can yield significant savings and speed up the prototyping process overall.
Application Matters: It isn’t practical to manufacture full prototypes built with slightly different materials and then test them in the real world. Fatigue testing significantly reduces development time by weeding out the materials you know will fail in real-world environments before any fabrication has begun.
This becomes even more critical when testing different grades of the same material. For example, one sample of Garolite (G10) has a spec sheet rating of 140 °C, but when fatigue tested at 100 °C, it suffered a 91% reduction in fatigue life compared to room temperature. A second Garolite sample (G11) with a slightly higher temperature rating lost only 46% of its fatigue life, meaning it performed better at this elevated temperature – even though the spec sheets would imply similar performance below both samples’ temperature ratings. If your product needs to withstand high temperatures, you’d be far better off sourcing the G11, but you wouldn’t know it from the spec sheets alone.
The “Best” Material Isn’t Always Right for You: In addition to accelerating production time, fatigue testing can reveal opportunities to optimize performance while minimizing unnecessary cost. For many manufacturers, the “best” or most expensive material is not always necessary; fatigue testing may uncover that a material of half the cost performs just as well in your application. Conversely, if you blindly choose the “best” material, it still might break in use! Fatigue testing eliminates guesswork so you can choose the most efficient material for your product.
Fatigue Testing in Product Design
After using fatigue testing to inform material selection, fatigue testing in product design serves to verify your previous assumptions and design work. If you chose the right material from the start, then design should be a smooth process with fatigue testing confirming your product’s viability. Fatigue testing at this stage also evaluates the manufacturing process and any artifacts from processing.
For example, in a test conducted with an ElectroForce 3330, polymer samples with a knit line designed into the part lasted roughly 5 times less (6,000 cycles) as opposed to an optimally molded sample with no knit line (30,000) cycles), despite both being manufactured with identical material.
When evaluating final products, fatigue testing allows you to:
Find Failure Points Early: Knowing exactly when and where your product is liable to break means you can implement fixes quickly, speeding up the time to prototype and final product.
Resist the Urge to Over-Engineer: Just as critically, it allows you to optimize the design to your use without using excess material or a more complicated structure than necessary. Down the road, this will improve manufacturing efficiency and can help yield significant savings.
Early Knowledge Makes Better Products
Fatigue testing is an indispensable tool for ensuring product reliability and performance in real-world conditions. By systematically identifying material weaknesses and structural flaws early in the development process, fatigue testing reduces the risk of costly failures, angry customers, and redesigns. It allows companies to optimize material selection and design with scientific precision, enhancing durability without over-engineering or unnecessary costs. Ultimately, fatigue testing accelerates prototyping, safeguards against expensive product failure, and ensures that products are optimized for performance, durability, and cost – delivering value, safety, and peace of mind to both manufacturers and end-users.
Other Resources
- Application Note – Tensile and Fatigue Properties of Additively Manufactured Polyamides
- Application Note – Flexural Fatigue Behavior of Woven Fiberglass Composites at Elevated Temperature
- Application Note – Introduction to Dynamic Mechanical Analysis and its Application to Testing of Polymer Solids
- Webinar – Troy Nickel: An Introduction to Fatigue Testing
- Blog – Material Analysis Techniques for Every Stage of Polymer Development
- eBook – How to Ensure Polymer Strength and Durability with Mechanical Testing