VIS 413 High Temperature Viscometer
Discover the rotational viscometer with exclusive Vacuum and Reactive Atmosphere capability for Highest Temperature melt viscosity measurements.
TA Instruments | Waters invites you to experience the latest innovations in high temperature rotational viscometers, the VIS 413. The VIS 413 viscometer is designed for scientists who need to obtain melt viscosity data from the widest range of materials at the highest temperatures.
Advances in core measurement technology for rotational speed control and torque measurement enable viscosity measurements with superior precision. The viscometer sensor utilizing TA Instruments proprietary technology empowers you to measure in a wider viscosity range with a higher level of accuracy.
The new powerful, easy-to-use, and safe reaction atmosphere control system extends the applicability of the high temperature viscometer for measurements with air sensitive materials. That allows you to replicate demanding environmental conditions, including vacuum, inert and reactive atmospheres.
TA instruments vast experience with high-temperature furnace development and manufacture is used in the new viscometer furnace. As a result, the VIS 413 covers the largest temperature range and offers excellent temperature stability and homogeneity. The quality and unique performance of the furnace allow you to measure melt viscosity accurately in the widest temperature range.
The sophisticated water cooling system drastically reduces the cool-down time of the furnace and sensor, providing excellent viscosity measurement stability and safe operation. The minimized idle time doubles the productivity of the instrument and improves the output of your research.
Spring-loaded sample crucible holders at the viscometer sensor allow for simple and safe sample loading. The proven design and the small instrument footprint allow for installation and operation of the viscometer in a glovebox for reliably handling oxygen or moisture-sensitive samples.
Discover the advanced engineering and attention to detail that provides enhancements in every aspect of high temperature viscometer technology and application flexibility.
Technical Specifications
VIS 413 | VIS 413HT | |||
Viscosity Range |
101 – 108 dPa s |
|||
Sample Temperature Range
|
up to 1550°C |
up to 1750°C | ||
Atmosphere |
Air, Vacuum, Inert, Reactive |
|||
Rotor Diameters
|
12 mm / 16 mm
|
|||
Sample Volume
|
26 ml
|
|||
Rotor and Sample Crucible Materials
|
PtRh, Al2O3, other on request |
|||
Rotational Speed |
0.001 – 300 min-1 |
|||
Compliant Standards |
ISO 7884-2, ASTM C965, ASTM C1276 |
|||
Dimensions W x D |
555 mm x 600 mm |
Furnace and Atmosphere Control
High Temperature Furnace
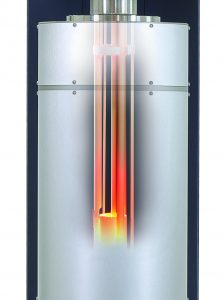
The VIS 413 viscometer is equipped with the latest TA Instruments high-temperature furnace technology. Two water-cooled furnace configurations provide industry leading sample temperatures of up to 1750°C. The integrated water cooling enables unparalleled short cool down times and doubles the productivity of the VIS 413 compared to other instruments in the market.
Backed by decades of experience in design and manufacture, the sophisticated high-temperature furnaces ensure excellent thermal stability, temperature homogeneity, and a long-lasting lifetime.
The improved vacuum-tight design of the instrument allows for complete evacuation of oxygen from the viscometer before and/or after an experiment. Viscosity measurements can be performed in inert (e. g . N 2, Ar) or reactive (e.g. H2/N2, CO/CO2) atmospheres. These unique features allows measuring the viscosity under realistic environmental conditions and analyzing oxygen sensitive sample materials, such as coal ash, metals or salts.
The vacuum-tight furnace design and dedicated gas flow paths in the instrument provide reliable ventilation of the reaction atmosphere through a single connection. This ensures highest safety standards for experiments with potentially toxic gas atmospheres.
The new VIS 413 is a safe, accurate and flexible high temperature viscometer for the analysis of all sample materials in air or controlled atmospheres.
Atmosphere Control
The VIS 413 can be combined with a reactive gas supply module that allows for software-controlled evacuation and inert or reactive atmosphere control of the sample in the furnace.
The reactive gas-module provides unique operational benefits for obtaining viscometry measurements from challenging samples:
- Complete system evacuation provides improved atmosphere purity in less time compared to simply purging
- Mimic real process environment or reliably control measurement conditions
- Purge the viscometer sensor to prevent contamination when working with volatile samples
- Perform measurements in reducing atmospheres like CO/CO2 and H2/N2 to provide absolutely oxygen-free atmospheres
- Controlled ventilation pathway ensures lab safety
PROPRIETARY FURNACE TECHNOLOGY PROVIDES
WIDEST TEMPERATURE RANGE and EXCLUSIVE
VACUUM and REACTIVE ATMOSPHERE CAPABILITY
Sample Crucible, Rotor, Holders
VIS 413 viscometers allow simple and safe sample loading. The sample crucible is held in position by spring-loaded ceramic fixtures. Even if the viscometer is located in a fume hood or a glove box sample loading is easy and convenient.
Sample crucibles and rotors are available in ceramics and platinum alloy. Interchangeability of the measuring systems provides the right material choice for every sample material and customer requirement. In the table below the measuring system materials are compared.
The practical geometry of the sample crucible and the universal rotor coupling allow us to offer customized sample crucibles and rotors made of different materials to meet individual customer requirements.
The well-thought-out design and accessories of the VIS 413 enable flexible configuration and trouble-free operation for viscosity measurements of all sample materials in air or controlled atmospheres.
Pt-Alloy | Ceramics | |
---|---|---|
Type of use | Re-usable Typically cleaned by heat and acid treatment |
Disposable No cleaning required |
Usually applied for | Glass, Enamel, Casting Powder | Ash, Slag, Magma, Metals |
EASE OF SAMPLE HANDLING
through FIELD PROVEN DESIGN with the right
CHOICE of MEASURING SYSTEMS
for each SAMPLE MATERIAL
Viscometer
A proprietary frictionless and wear-free EC motor is the heart of the VIS 413 viscometer sensor. In combination with the digital optical encoder, the most accurate rotational speed measurement and control is realized.
Optimal alignment of the rotor with lowest reproducible friction is provided by sealed high-precision ball bearings. Compared to an air bearing, the main advantage is the ability to operate in vacuum. This is a tremendous improvement for high-temperature viscosity measurements in controlled atmospheres.
The gas dosing accessory provides a purge gas flow protecting the EC motor, optical encoder and the ball bearings. This feature allows viscosity measurements on volatile sample materials to be performed which otherwise could contaminate the viscometer sensor.
The proprietary EC motor-based torque sensor delivers the most accurate high-temperature viscosity data, even on challenging sample materials under the widest temperature range, and under application-relevant controlled atmospheres.
ROBUST PROPRIETARY RHEOMETER
provides VACUUM CAPABILITY for
HIGHER TEMPERATURE viscosity measurements
on CHALLENGING SAMPLES
Viscosity of Melts at High Temperature
Processing of melts at high temperatures is the basis for the industrial manufacture of many products, including glasses and metals, or for reliably operating industrial incineration plants by continuously removing slag. In addition to temperature, the melt viscosity of materials is significantly influenced by their chemical composition and ambient conditions such as atmosphere. For industrial processing of molds, the viscosity is an essential parameter that determines the economy and ecology of the processes and the quality of the products.
Glass
Glass Industry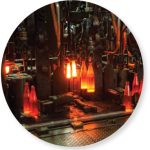
Processing molten glass is part of industrial manufacture of glass products, such as float glass, glass fibers and frits.
Glass Viscosity
The viscosity of a glass affects the temperature ranges within which the glass can be worked. Measuring the temperature-viscosity relationship is essential to determining the correct melting and heat treatment regimes in glass production and processing.
For example, viscosity directly affects the homogenization of a melt and removal of air bubbles. It enables manufacturers to predict and model how the glass will perform in a forming process or glass fiber generation.
Glass viscosity varies inversely with temperature. As it is heated, viscosity decreases, the glass flows more easily. The relationship between temperature and viscosity is linked directly to the chemical composition of a glass. Manufacturers need techniques to measure and model this relationship for a range of glass compositions and temperatures.
The viscosities of most glasses are typically measured between 700°C and 1600°C. In the diagram below, the results of a high temperature viscosity measurement of three glasses with a VIS 413 are plotted over temperature.
Find out more about complementary TA Instruments high temperature analyzers for glass here:
- High temperature dilatometers are applied for measuring thermal expansion and softening points of glass materials
- Heating microscope for measurement of flow properties and surface tension of glassy melts at high temperatures
- Laser flash analyzers for measuring temperature diffusivity and thermal conductivity at high temperatures
Metal
Metal Industry
Handling of molten metals is part of traditional and additive manufacturing processes. Additives like casting powders are essential for providing high quality metal products.
Metals
Molten metal flows occur in traditional and continuous casting processes, in additive manufacturing and in soldering and welding applications. The elementary property required to understand, predict and improve these flows is the viscosity of the molten metal.
Molten metals are generally highly reactive with oxygen. The unique vacuum and reactive gas capability of the VIS 413 allows performing measurements in reducing atmosphere, such as forming gas (H2/N2 mixture), avoiding metal oxidation even at the highest temperatures.
Casting Powder
Casting powders are essential for continuous casting processes. The main function of the glassy casting powders is to provide lubrication between the solidifying metal and the water-cooled copper mold. The casting powder is continuously added on top of the mold covering the free surface of the liquid steel. The powder layer in contact with the liquid steel melts and infiltrates into the gap between the steel shell and the copper mold wall and provides lubrication. The lubrication depends on the viscosity of the melted casting powder. The values must be adjusted to provide a minimum friction. Therefore, for industrial applications the viscosity values of casting powder at temperatures between 1200°C and 1400°C are considered to be relevant.
The diagram below presents the temperature dependent viscosity of a casting powder measured with the VIS 413. Typical for mould powders is the beginning of crystallization at a defined temperature – in this case 1160°C.
Find out more about complementary TA Instruments high temperature analyzers for metals here:
- Quenching dilatometers for investigating phase transformations in metals during rapid cooling and/or deformation
- Laser flash analyzers for measuring temperature diffusivity and thermal conductivity at high temperatures
Energy Industry
Energy Industry
The viscosity of melts at high temperatures is critical for efficiency, safety and reliability of energy conversion processes. In traditional coal fired power plants and gasifiers for converting solid fuels into syngas slag and ash must flow down the wall of the boiler. In emerging new power generation techniques molten metals and salts are considered for cooling and heat transfer purposes.
Coal Ash / Slag
In coal-fired power plants, coal gasification plants, and waste incineration plants ash and slag must be removed from the boiler. As feedstock is continuously supplied the slag must be continuously removed from the process. The best way to achieve this is to let the molten slag flow into a quenching bath from which it can be retracted. The viscosity of the slag must be low enough to let it flow down the lining of the boiler without causing deposits. The slag viscosity can be adjusted by adding fluxing agents. For proper dosing of fluxing agents the slag viscosity of the used feedstock must be measured under boiler operation conditions.
Slag viscosity measurements must be performed under similar atmospheric conditions as in the boiler. The VIS 413 can perform measurements under controlled CO/CO2 mixture atmospheres as suggested for coal slag viscosity determination.
Salt and Metals as Heat Transfer Mediums
Molten salts or low melting temperature metals are material groups that have immense potential as thermal energy storage and heat transfer media for solar and/or nuclear energy applications. Besides other thermophysical properties a sufficiently low viscosity over the complete temperature range from 100°C to 700°C is a precondition for successful application.
Viscosity measurements on salts and metals must often be performed under dry, oxygen-free inert atmospheres. The unique vacuum and atmosphere control capabilities of the VIS 413 allows viscosity measurements on samples that are sensitive to humidity or oxygen.
Find out more about complementary TA Instruments high temperature analyzers for energy here:
- Simultaneous thermal analyzer for measuring reaction kinetics and heat flows
- High pressure TGA for measuring combustion and gasification processes under controlled atmospheres and high-pressure conditions
- Heating microscope for measurement of slag and ash fusion at high temperatures
Geological Materials
Magma
Viscosity is the most important physical property governing the production, transport and eruption of magmas. The viscosity of naturally-occurring silicate magmas can span more than 15 orders of magnitude primarily in response to variations in temperature, melt composition and the proportions of suspended solids and/or exsolved fluid phases.
Experimental investigation of magma is the base for improved modelling of geological processes. Cooling of mixed aluminosilicate liquids leads to partial crystallization which changes the composition of the residual liquid. This can lead to complex changes in magma viscosity which are only assessable by measurements.
In the diagram below, the viscosity of a basaltic andesite magma is plotted over temperature.
Find out more about complementary TA Instruments high temperature analyzers for geological research here:
- Simultaneous thermal analyzer for measuring outgassing kinetics and heat flows
- High pressure TGA for measuring outgassing and solubility under controlled atmospheres and high-pressure
- Description
-
TA Instruments | Waters invites you to experience the latest innovations in high temperature rotational viscometers, the VIS 413. The VIS 413 viscometer is designed for scientists who need to obtain melt viscosity data from the widest range of materials at the highest temperatures.
Advances in core measurement technology for rotational speed control and torque measurement enable viscosity measurements with superior precision. The viscometer sensor utilizing TA Instruments proprietary technology empowers you to measure in a wider viscosity range with a higher level of accuracy.
The new powerful, easy-to-use, and safe reaction atmosphere control system extends the applicability of the high temperature viscometer for measurements with air sensitive materials. That allows you to replicate demanding environmental conditions, including vacuum, inert and reactive atmospheres.
TA instruments vast experience with high-temperature furnace development and manufacture is used in the new viscometer furnace. As a result, the VIS 413 covers the largest temperature range and offers excellent temperature stability and homogeneity. The quality and unique performance of the furnace allow you to measure melt viscosity accurately in the widest temperature range.
The sophisticated water cooling system drastically reduces the cool-down time of the furnace and sensor, providing excellent viscosity measurement stability and safe operation. The minimized idle time doubles the productivity of the instrument and improves the output of your research.
Spring-loaded sample crucible holders at the viscometer sensor allow for simple and safe sample loading. The proven design and the small instrument footprint allow for installation and operation of the viscometer in a glovebox for reliably handling oxygen or moisture-sensitive samples.
Discover the advanced engineering and attention to detail that provides enhancements in every aspect of high temperature viscometer technology and application flexibility.
- Specifications
-
Technical Specifications
VIS 413 VIS 413HT Viscosity Range 101 – 108 dPa s
Sample Temperature Rangeup to 1550°C
up to 1750°C Atmosphere Air, Vacuum, Inert, Reactive
Rotor Diameters12 mm / 16 mmSample Volume26 mlRotor and Sample Crucible MaterialsPtRh, Al2O3, other on request
Rotational Speed 0.001 – 300 min-1
Compliant Standards ISO 7884-2, ASTM C965, ASTM C1276
Dimensions W x D 555 mm x 600 mm
- Technology
-
Furnace and Atmosphere Control
High Temperature Furnace
The VIS 413 viscometer is equipped with the latest TA Instruments high-temperature furnace technology. Two water-cooled furnace configurations provide industry leading sample temperatures of up to 1750°C. The integrated water cooling enables unparalleled short cool down times and doubles the productivity of the VIS 413 compared to other instruments in the market.
Backed by decades of experience in design and manufacture, the sophisticated high-temperature furnaces ensure excellent thermal stability, temperature homogeneity, and a long-lasting lifetime.
The improved vacuum-tight design of the instrument allows for complete evacuation of oxygen from the viscometer before and/or after an experiment. Viscosity measurements can be performed in inert (e. g . N 2, Ar) or reactive (e.g. H2/N2, CO/CO2) atmospheres. These unique features allows measuring the viscosity under realistic environmental conditions and analyzing oxygen sensitive sample materials, such as coal ash, metals or salts.
The vacuum-tight furnace design and dedicated gas flow paths in the instrument provide reliable ventilation of the reaction atmosphere through a single connection. This ensures highest safety standards for experiments with potentially toxic gas atmospheres.
The new VIS 413 is a safe, accurate and flexible high temperature viscometer for the analysis of all sample materials in air or controlled atmospheres.
Atmosphere Control
The VIS 413 can be combined with a reactive gas supply module that allows for software-controlled evacuation and inert or reactive atmosphere control of the sample in the furnace.
The reactive gas-module provides unique operational benefits for obtaining viscometry measurements from challenging samples:
- Complete system evacuation provides improved atmosphere purity in less time compared to simply purging
- Mimic real process environment or reliably control measurement conditions
- Purge the viscometer sensor to prevent contamination when working with volatile samples
- Perform measurements in reducing atmospheres like CO/CO2 and H2/N2 to provide absolutely oxygen-free atmospheres
- Controlled ventilation pathway ensures lab safety
PROPRIETARY FURNACE TECHNOLOGY PROVIDES
WIDEST TEMPERATURE RANGE and EXCLUSIVE
VACUUM and REACTIVE ATMOSPHERE CAPABILITY
Sample Crucible, Rotor, Holders
VIS 413 viscometers allow simple and safe sample loading. The sample crucible is held in position by spring-loaded ceramic fixtures. Even if the viscometer is located in a fume hood or a glove box sample loading is easy and convenient.
Sample crucibles and rotors are available in ceramics and platinum alloy. Interchangeability of the measuring systems provides the right material choice for every sample material and customer requirement. In the table below the measuring system materials are compared.
The practical geometry of the sample crucible and the universal rotor coupling allow us to offer customized sample crucibles and rotors made of different materials to meet individual customer requirements.
The well-thought-out design and accessories of the VIS 413 enable flexible configuration and trouble-free operation for viscosity measurements of all sample materials in air or controlled atmospheres.
Pt-Alloy Ceramics Type of use Re-usable
Typically cleaned by heat and acid treatmentDisposable
No cleaning requiredUsually applied for Glass, Enamel, Casting Powder Ash, Slag, Magma, Metals EASE OF SAMPLE HANDLING
through FIELD PROVEN DESIGN with the right
CHOICE of MEASURING SYSTEMS
for each SAMPLE MATERIAL
Viscometer
A proprietary frictionless and wear-free EC motor is the heart of the VIS 413 viscometer sensor. In combination with the digital optical encoder, the most accurate rotational speed measurement and control is realized.
Optimal alignment of the rotor with lowest reproducible friction is provided by sealed high-precision ball bearings. Compared to an air bearing, the main advantage is the ability to operate in vacuum. This is a tremendous improvement for high-temperature viscosity measurements in controlled atmospheres.
The gas dosing accessory provides a purge gas flow protecting the EC motor, optical encoder and the ball bearings. This feature allows viscosity measurements on volatile sample materials to be performed which otherwise could contaminate the viscometer sensor.
The proprietary EC motor-based torque sensor delivers the most accurate high-temperature viscosity data, even on challenging sample materials under the widest temperature range, and under application-relevant controlled atmospheres.
ROBUST PROPRIETARY RHEOMETER
provides VACUUM CAPABILITY for
HIGHER TEMPERATURE viscosity measurements
on CHALLENGING SAMPLES
- Applications
-
Viscosity of Melts at High Temperature
Processing of melts at high temperatures is the basis for the industrial manufacture of many products, including glasses and metals, or for reliably operating industrial incineration plants by continuously removing slag. In addition to temperature, the melt viscosity of materials is significantly influenced by their chemical composition and ambient conditions such as atmosphere. For industrial processing of molds, the viscosity is an essential parameter that determines the economy and ecology of the processes and the quality of the products.
Glass
Glass Industry
Processing molten glass is part of industrial manufacture of glass products, such as float glass, glass fibers and frits.
Glass Viscosity
The viscosity of a glass affects the temperature ranges within which the glass can be worked. Measuring the temperature-viscosity relationship is essential to determining the correct melting and heat treatment regimes in glass production and processing.
For example, viscosity directly affects the homogenization of a melt and removal of air bubbles. It enables manufacturers to predict and model how the glass will perform in a forming process or glass fiber generation.
Glass viscosity varies inversely with temperature. As it is heated, viscosity decreases, the glass flows more easily. The relationship between temperature and viscosity is linked directly to the chemical composition of a glass. Manufacturers need techniques to measure and model this relationship for a range of glass compositions and temperatures.
The viscosities of most glasses are typically measured between 700°C and 1600°C. In the diagram below, the results of a high temperature viscosity measurement of three glasses with a VIS 413 are plotted over temperature.
Find out more about complementary TA Instruments high temperature analyzers for glass here:
- High temperature dilatometers are applied for measuring thermal expansion and softening points of glass materials
- Heating microscope for measurement of flow properties and surface tension of glassy melts at high temperatures
- Laser flash analyzers for measuring temperature diffusivity and thermal conductivity at high temperatures
Metal
Metal Industry
Handling of molten metals is part of traditional and additive manufacturing processes. Additives like casting powders are essential for providing high quality metal products.
Metals
Molten metal flows occur in traditional and continuous casting processes, in additive manufacturing and in soldering and welding applications. The elementary property required to understand, predict and improve these flows is the viscosity of the molten metal.
Molten metals are generally highly reactive with oxygen. The unique vacuum and reactive gas capability of the VIS 413 allows performing measurements in reducing atmosphere, such as forming gas (H2/N2 mixture), avoiding metal oxidation even at the highest temperatures.
Casting Powder
Casting powders are essential for continuous casting processes. The main function of the glassy casting powders is to provide lubrication between the solidifying metal and the water-cooled copper mold. The casting powder is continuously added on top of the mold covering the free surface of the liquid steel. The powder layer in contact with the liquid steel melts and infiltrates into the gap between the steel shell and the copper mold wall and provides lubrication. The lubrication depends on the viscosity of the melted casting powder. The values must be adjusted to provide a minimum friction. Therefore, for industrial applications the viscosity values of casting powder at temperatures between 1200°C and 1400°C are considered to be relevant.
The diagram below presents the temperature dependent viscosity of a casting powder measured with the VIS 413. Typical for mould powders is the beginning of crystallization at a defined temperature – in this case 1160°C.
Find out more about complementary TA Instruments high temperature analyzers for metals here:
- Quenching dilatometers for investigating phase transformations in metals during rapid cooling and/or deformation
- Laser flash analyzers for measuring temperature diffusivity and thermal conductivity at high temperatures
Energy Industry
Energy Industry
The viscosity of melts at high temperatures is critical for efficiency, safety and reliability of energy conversion processes. In traditional coal fired power plants and gasifiers for converting solid fuels into syngas slag and ash must flow down the wall of the boiler. In emerging new power generation techniques molten metals and salts are considered for cooling and heat transfer purposes.
Coal Ash / Slag
In coal-fired power plants, coal gasification plants, and waste incineration plants ash and slag must be removed from the boiler. As feedstock is continuously supplied the slag must be continuously removed from the process. The best way to achieve this is to let the molten slag flow into a quenching bath from which it can be retracted. The viscosity of the slag must be low enough to let it flow down the lining of the boiler without causing deposits. The slag viscosity can be adjusted by adding fluxing agents. For proper dosing of fluxing agents the slag viscosity of the used feedstock must be measured under boiler operation conditions.
Slag viscosity measurements must be performed under similar atmospheric conditions as in the boiler. The VIS 413 can perform measurements under controlled CO/CO2 mixture atmospheres as suggested for coal slag viscosity determination.
Salt and Metals as Heat Transfer Mediums
Molten salts or low melting temperature metals are material groups that have immense potential as thermal energy storage and heat transfer media for solar and/or nuclear energy applications. Besides other thermophysical properties a sufficiently low viscosity over the complete temperature range from 100°C to 700°C is a precondition for successful application.
Viscosity measurements on salts and metals must often be performed under dry, oxygen-free inert atmospheres. The unique vacuum and atmosphere control capabilities of the VIS 413 allows viscosity measurements on samples that are sensitive to humidity or oxygen.
Find out more about complementary TA Instruments high temperature analyzers for energy here:
- Simultaneous thermal analyzer for measuring reaction kinetics and heat flows
- High pressure TGA for measuring combustion and gasification processes under controlled atmospheres and high-pressure conditions
- Heating microscope for measurement of slag and ash fusion at high temperatures
Geological Materials
Magma
Viscosity is the most important physical property governing the production, transport and eruption of magmas. The viscosity of naturally-occurring silicate magmas can span more than 15 orders of magnitude primarily in response to variations in temperature, melt composition and the proportions of suspended solids and/or exsolved fluid phases.
Experimental investigation of magma is the base for improved modelling of geological processes. Cooling of mixed aluminosilicate liquids leads to partial crystallization which changes the composition of the residual liquid. This can lead to complex changes in magma viscosity which are only assessable by measurements.
In the diagram below, the viscosity of a basaltic andesite magma is plotted over temperature.
Find out more about complementary TA Instruments high temperature analyzers for geological research here:
- Simultaneous thermal analyzer for measuring outgassing kinetics and heat flows
- High pressure TGA for measuring outgassing and solubility under controlled atmospheres and high-pressure